Precast elements could be made of reinforced or prestressed concrete. The behaviour of these two under service loads is dependent on the properties of the material composition as well as the manufacturing process. It is important to understand the nature of the materials used in the precast concrete buildings.
Given below is an overview of different materials used in precast concrete buildings.
Cement for Precast Concrete Buildings
Cement should comply with the requirements of IS 456;2000, for gaining satisfactory performance in a structure. The standard classifies cement under two divisions;
Ordinary Portland Cements [OPC] 43 grade [IS:8112] and 53 [IS:12269] are normally used in precast concrete construction.
Portland Pozzolana Cement [IS 1481] and Portland Slag Cement [IS 455] are preferred

Supplementary Cementitious Material [SCMs] for Precast Concrete Buildings
Supplementary cementitious materials are natural materials or industrial byproducts that exhibit cementitious behaviors when combined with either water or water and other compounds. SCMs enhance the results of ordinary portland cement (OPC) hydration reactions in concrete and are either incorporated into concrete mixes as a partial replacement for portland cement or blended into the cement during manufacturing. SCMs augment cement’s actions and can improve fresh concrete characteristics, strengthen hardened concrete properties and reduce raw material costs.
Waterproofing admixture for Precast Concrete Buildings
Waterproofing admixture for precast construction should comply with the requirements of IS; 9103-1999, when compared with the manufacturers’ declared values. Where two or more admixtures are to be used in combination they should be checked for compatibility with the cement. It is also desirable to conduct trials with admixtures using the specific materials to be used in the project to ascertain the dodge for the desired performance.

Reinforcement bars for Precast Concrete Buildings
Reinforcement bars should comply with IS; 1786-2008 for high strength deformed bars for concrete reinforcement, IS; 432 for mild steel and medium tensile bars. Bars are classified by shape, ductility, class, strength grade and size. The physical properties, chemical compositions and geometry of ribs and lungs in case of steel reinforcement shall be in conformity with IS; 1786-2008.
Welded wire fabric reinforcement is widely used in developed countries and its use in India is also seeing a rise.
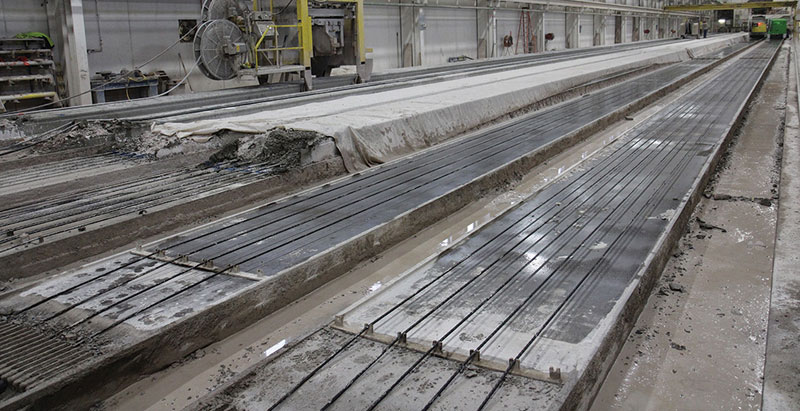
Protective coatings on reinforcement for Precast Concrete Buildings
Appropriate quality of concrete and amount of cover in combination with proper detailing is considered sufficient to protect reinforcing steel for the normal life of a structure. The most commonly used coating is zinc-based. It provides appropriate thickness in the form of hot-dip galvanization. It should not be coupled with dissimilar metals.

Fibers for Precast Concrete Buildings
Fibers can be used as reinforcement in precast concrete, either as a fiber-only solution or as a combined solution with conventional rebar reinforcement. Fiber-reinforced concrete (FRC) in precast construction increases its structural integrity. It contains short discrete fibers that are uniformly distributed and randomly oriented. Blends of both steel and polymeric fibers are often used in construction projects in order to combine the benefits of both products; structural improvements provided by steel fibers and the resistance to explosive spalling and plastic shrinkage improvements provided by polymeric fibers. In certain specific circumstances, steel fiber or macro synthetic fibers can entirely replace traditional steel reinforcement bars in reinforced concrete. This is most common in industrial flooring but also in some other precasting applications.

Epoxy grouts for Precast Concrete Buildings
Epoxy grouts are used when very high strength is desired to the concrete. Design, detailing, and proper material specification of field-cast grouts are critical for a number of reasons. They are mixtures of epoxy resins and filler material, mostly sand. The physical properties of epoxy vary widely so the user should be familiar with the compounds to be used.

Conclusion
Precast concrete materials help you maximize your project’s potential while making sure it is completed on time. They are also among the most versatile products in construction, combining a strong structure with the ability to meet compatibility requirements.
Image Source: esolution-pt.com, monocrete.com, techdry.com.au, bft-international.com, precast.org, designingbuildings.co.uk, slideserve.com, aggregate.com, trpreadymix.com, parex.co.uk