Formwork is temporary or permanent molds into which concrete or similar materials are poured. In the context of concrete construction, the falsework supports the shuttering molds. A formwork system is a fast assembles and removal system that shortens the construction period and saves the administration cost. A set of formwork can build one storey in every four days under a normative construction. There are several types of formwork systems that are in practice, but in this article, we will discuss the innovative ones that are being practiced globally. Given below are few such formwork systems and their functionality is discussed below.
Fabric Formwork
The use of fabric as a concrete formwork material has been in practice for many years. As of late, geotextile fabrics are relatively readily available and cost-effective as a result of their widespread acceptance and use in traditional site backfill applications. In order to employ the durable, functional, and aesthetic qualities of a concrete structural system in locations where site logistics might be prohibitive or experienced labor less locally available, alternative lightweight fabric forming systems may prove viable. The overall economy on formwork material and construction operations are consistent with the sustainable practices of using less material and energy in construction. When compared with traditional rigid wood or steel panel formwork, less material by weight is required on-site for casting, with the possibility of less ensuing waste. The fabric formwork systems can take advantage of designing formwork ties and support systems for lessened pressures at greater heights. In practice, the height of the fluid concrete can be tactilely monitored on the forming surface, which can allow for fewer stages of concrete construction on site. Other sustainable advantages inherent in the system are increased durability and the use of less material to form out-of-plane, curved features. In this paper, two recent residential projects in rural Vermont are presented to illustrate the sustainable advantages of geotextile fabric as part of the formwork system. The fabric formwork was used for walls, columns, and elevated slab soffits, resulting in savings in formwork material weight of at least 35% compared to a standard wood panel system. This also translates to reduced energy use for material transport, less waste, fewer pour operations, and the use of so-called local labor that is not dependent on larger scale concrete operations experience. Once stripped, the fabric has the potential to be reused on-site as subgrade stabilization.

ABS plastic formwork system
A large amount of deforestation has occurred in the recent past causing environmental imbalance to our ecosystem. As a preventive measure to stop deforestation we should find alternatives to wood formwork. In this point of view ‘ABS PLASTIC FORMWORK’ is the only possible solution to this problem as it is a recyclable, reusable and eco-friendly alternative. That’s why we are introducing the plastic formwork to replace the traditional formwork. ABS Plastic formwork is a new innovation in the formwork industry, it is famous for its lightweight, speedy construction and accuracy in work . Today almost over 350000 sq m of formwork is being used for construction purposes all over the world. In our country, ABS plastic formwork has been used on many construction projects and it has been proved to be economical. ABS plastic formwork has been widely used in gulf countries, Europe, Asia as well as all other parts of the world. This technology is most suitable for huge housing projects to be completed in a short period of time, where columns, beams, slab sizes are standard. This technology gives more accurate results and good quality of construction in optimum cost and minimum time.

The panels of plastic formwork are made up of ABS (Acrylonitrile Butadiene Styrene). The panel of this formwork has thickness 80mm. These panels fit perfectly to each other.for the purpose of interlocking panels, nylon handles are used and this is the only locking assembly for this system. While for construction of slab and beams, panels are interconnected in the same manner and supported by regular props that are used in the construction industry. As the formwork material is made up of ABS plastic, they are light in weight but still possess a high load-bearing capacity. As the material is light in weight, handling and on-site transportation process become much easier. Hence, there is no need for heavy lifting equipment. The panels are in fixed sizes and when connected adjacently, they are exactly in plumb and when connected perpendicularly then they make exactly 90-degree angle giving exact dimensions of required column sizes. Hence, skilled labour is not required.
The panels are available in different sizes, that are 1200mm*600mm, 400mm*600mm, 350mm*600mm, 300mm*600mm, 250mm*600mm, 200mm*600mm. Adjustable panels are also available. With the help of adjustable panels, different sizes of columns can be achieved. All these panels are made with high accuracy which provides ease in construction work.
Cast in place permanent form for concrete beams and columns
The new system consists of four phases; the preliminary phase where a modified reinforcement design of beam and column is processed, the design phase where design parameters are set, the construction phase and the application phase where possible loads are determined and then materials used are tested. A 0.485 water-cement and 1:2.75 cement-sand ratios respectively are used for the mortar mix and a ½” x ½” gauge 23 galvanized welded wire mesh for reinforcement. The construction phase includes the load testing of the fabricated 200mm x 300mm x 10mm prototype ferrocement plates using a Universal Testing Machine (UTM) and 100mm x 200mm x 2400m beam samples using Reaction Frame Test (RFT). Ferrocement form prototype has a nominal capacity of 0.015kN-m creating 0.02mm deformation while achieved during the actual test which has an impressive average capacity of 0.267kN-m for a deflection of 0.02mm, thus makes the design form applicable. A modified beam with 4-1” x 1” x ⅛” angle bars and has a capacity of 20.23kN-m and is comparable to a conventional beam with 4-12mmØ deformed rebars that have a capacity of 14.32kN-m. The comparative analysis shows a 31% cheaper cost in materials compared to conventional formwork without reusing materials and 9% cheaper costs when materials are used twice. The labor needed for the new system is almost equal to that estimated for conventional systems when materials are used twice with only 4 to 5 percent savings. The new system is time-efficient with 11 to 17percent savings in the number of days as compared to using conventional formwork systems. The analyzed data shows that ferrocement as formwork is viable and has achieved the necessary requirements a good formwork must-have. Furthermore, the economic efficiency of this study goes beyond what is expected; granted that the new system is done in considering the project in its entirety.
Automated Layout Climbing Formwork System
Layout planning of climbing formwork systems is a prerequisite for executing efficient and cost-effective structural framework in a high-rise building construction. However, most of the formwork system layout is operated manually under the heuristic approach of the supervisor and thus is prone to errors that affect the constructability of the entire construction. Furthermore, the inflexibility of the current method to changes in building design also results in unexpected variability during system utilization. Automated formwork layout method that considers essential factors such as configurations on the unit module of the form as an input data, information on building parameters for specifying possible areas of system installation and configurations on the working platform for the optimal arrangement of unit systems can be suggested as an alternative to the current manual execution of formwork layout. Therefore, this study proposes an automated layout planning method of climbing formwork systems by using genetic algorithms. The method developed in this study is to be utilized for reasonable decision making of the construction worker in control of the automated layout planning.
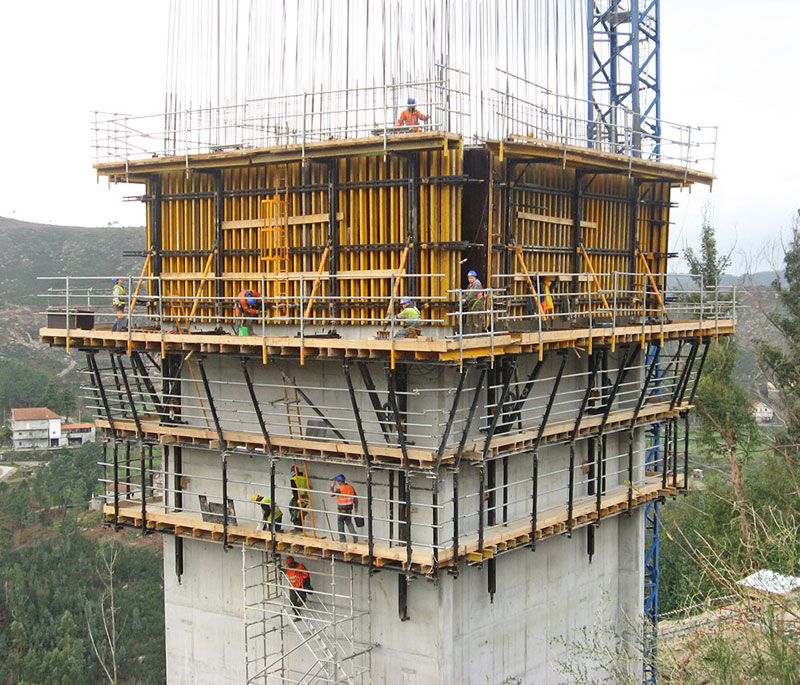
Cellform Permanent Formwork System
Cellform is similar to Groundform but combines with Cellcore & Claymaster to create a permanent shuttering system with all the benefits of ground heave solutions in one. The Cellcore element comes already fitted to the bottom of the Groundform whilst the Claymaster is attached to the vertical side of the Cellform on site. The system reduces the width of the dig and therefore the amount of muck away. It also eliminates the additional labour required to strike and remove shuttering.
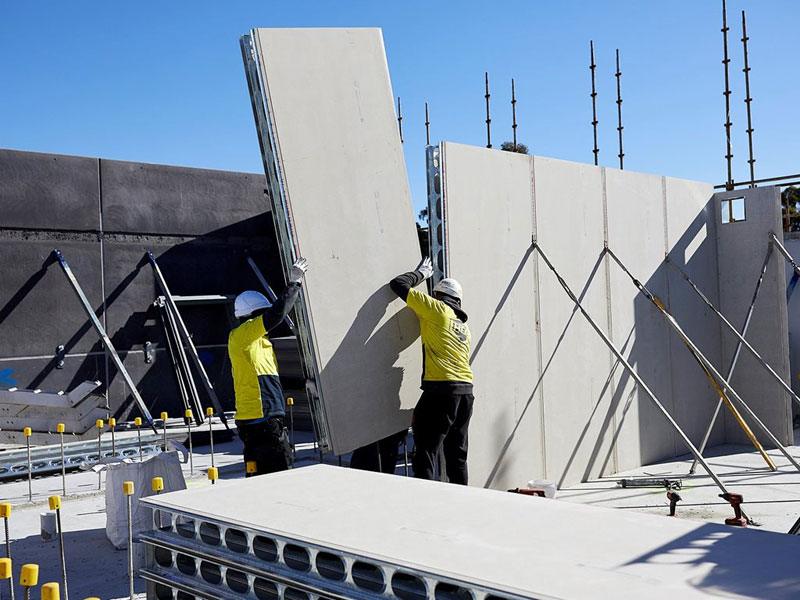
Insulated Concrete Formwork
Insulated concrete formwork (ICF) is an in-situ concrete system of building that is quick to construct and offers superior levels of performance over alternative methods of building envelope construction.
ICF has been growing in the UK self-build sector for some years and provides design professionals, architects, homeowners and contractors with a more efficient way to build concrete homes and commercial ICF structures. It is also one of just four approved walling systems for domestic basements ICF is based on hollow lightweight block components that lock together without intermediate bedding materials, such as mortar, to provide a formwork system into which concrete is poured. The blocks are formed of panels of insulation material, usually expanded polystyrene, tied together with plastic or steel ties. Once the concrete has cured, it becomes a high strength concrete frame structure with the formwork remaining in place.

This monolithic, insulated concrete formwork system of the building is quick to construct yet offers levels of performance significantly better than available from slower, more traditional approaches to building. Once set, the concrete becomes a high strength structure and the formwork remains in place as thermal insulation, with U-values down to 0.11 W/m²k – ideal for zero energy buildings.
The building process is quick, tidy and precise, with lower labour and equipment requirements than alternative methods. Originally developed and patented by isorast in the 1970s, this insulated concrete formwork system has been progressively improved and developed to satisfy the very best worldwide standards of energy efficiency and the recognized need for improved building techniques. Isorast constructions (aka Wallform) in the United Kingdom have an established track record of over thirty years’ performance and have a long life expectancy. As a highly insulated structure.
Info and image – Ascelibrary.org,ijret.org, iraj.in/journal, iaarc.org, becowallform.co.uk, concrete.org.uk, materialdistrict.com, liveprojectsnetwork.org, tss-me.com, architectureanddesign.com.au, ulmaconstruction.com