Cold Central Plant Recycling (CCPR) is a pavement repair technique where old asphalt is milled, recycled in a central plant, and then mixed with additives like emulsions or foamed asphalt. The recycled material is then returned to the site and reused, reducing the need for new materials and lowering costs. This technique is environmentally friendly, energy-efficient, and helps extend the life of the road.
Cold Central Plant Recycling (CCPR) uses:
- Urban Roads: Ideal for maintaining and upgrading roads in cities and towns, where traffic congestion and limited space make full road reconstruction difficult.
- Highways and Rural Roads: CCPR is effective in both high-traffic highways and rural roadways, providing an efficient solution for rehabilitating large road sections.
- Airports: It is used in the resurfacing of airport runways and taxiways, where quick turnaround and cost-effectiveness are important.
- Industrial Roads: Ideal for roads in industrial areas that face heavy loads and wear, extending their lifespan while reducing downtime.
- Residential Areas: CCPR can also be used in residential neighborhoods to repair and improve local streets, offering an environmentally friendly alternative to traditional methods.
- Bridges and Overpasses: It is sometimes used in rehabilitating bridge approaches and overpasses, where pavement condition affects the overall structure’s longevity.
- Parking Lots: CCPR is effective in resurfacing and strengthening parking lots, ensuring long-term durability at a lower cost.
Process of Cold Central Plant Recycling (CCPR)
The Cold Central Plant Recycling (CCPR) technique works through a systematic process that involves several steps:
- Milling: Existing asphalt is removed from the road surface.
- Transport: The milled material is taken to a central plant.
- Processing: In the plant, the material is mixed with additives like emulsions or foamed asphalt.
- Recycling and Mixing: The material is blended to restore its quality and strength.
- Reapplication: The recycled mixture is laid back on the road.
- Compaction: The surface is compacted to ensure durability and stability.
Advantages of the Cold Central Plant Recycling (CCPR) technique:
- Reduces the need for new materials, lowering overall project costs.
- Minimizes waste by reusing existing asphalt and reducing the need for new raw materials.
- Offers faster project completion by reusing and recycling existing materials on-site.
- Less new material is required, lowering transportation expenses.
- Improves the strength and durability of the recycled pavement, extending its lifespan.
- The process can be done with minimal disruption to traffic and surrounding areas.
- Reduces emissions associated with new material production and transportation.
- Suitable for a wide range of pavements, including urban streets, highways, and rural roads.
- The recycled mix can be engineered for better performance, enhancing road quality.
- Keeps old pavement material out of landfills by recycling it for new use.
- Decreases the consumption of natural resources such as aggregates and bitumen.
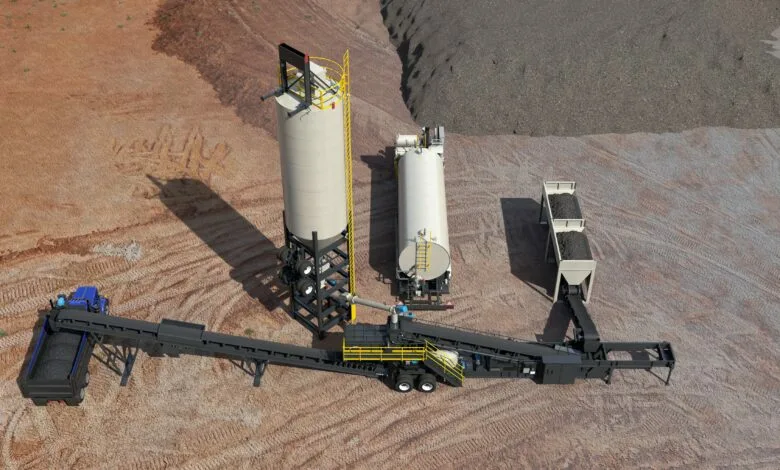
Types of Cold Central Plant Recycling (CCPR) Techniques
- Full-depth Reclamation (FDR) with Cold In-Place Recycling (CIR): This method involves milling the entire thickness of the existing pavement, recycling it at a central plant with additives like emulsions or foamed asphalt, and reusing the material as a new surface layer. It’s ideal for heavily deteriorated roads requiring full rehabilitation. The process not only saves on material costs but also reduces the need for hauling new aggregates, making it an environmentally-friendly option. The rehabilitated pavement is immediately ready for use, minimizing disruption to traffic.
- Cold In-Place Recycling with New Material Addition: Reclaimed asphalt pavement (RAP) is processed at a central plant, where new materials like aggregates or binders are added to enhance the recycled material’s properties, improving strength and durability for reuse in pavement construction. This method ensures the recycled material meets the necessary specifications for structural performance. It’s particularly useful when the existing RAP is too weathered or degraded to meet the desired standards for resurfacing.
- Cold Central Plant Recycling with Emulsion: Bitumen emulsion is mixed with the RAP in a central plant to act as a binder, rejuvenating the asphalt. This process provides flexibility and stability while reducing energy consumption due to lower temperature requirements. The use of emulsion also enhances the recycled material’s ability to resist cracking and rutting, ensuring a longer-lasting pavement. It is a cost-effective solution, particularly for roads with moderate distress where a complete replacement is unnecessary.
- Cold Central Plant Recycling with Foamed Asphalt: Foamed asphalt is injected into RAP at the central plant, creating a stable, binder-rich mixture. The foam enhances workability and bonding, reducing the need for additional additives and offering a durable, sustainable solution. This technique also reduces the carbon footprint by allowing recycling at lower temperatures compared to traditional hot-mix asphalt. The result is a flexible, resilient pavement structure that can handle varying traffic loads and environmental conditions.
- Cold Central Plant Recycling with Lime or Cement Stabilization: Lime or cement is added to the RAP in a central plant to improve its moisture resistance and strength. This technique enhances the recycled material’s durability and performance, especially when the RAP quality is low. It also helps to prevent cracking and improves the overall longevity of the pavement. Lime or cement stabilization is particularly beneficial in areas with poor-quality RAP or where high structural integrity is required for the new surface.
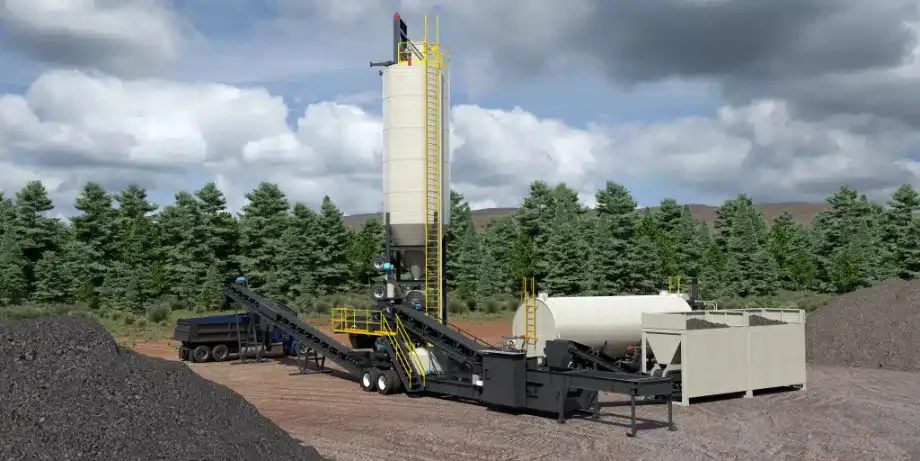
Different types of equipment used in Cold Central Plant Recycling (CCPR):
- Milling Machines (Cold Planers): These are used for removing the existing pavement layers, grinding them into smaller particles (Reclaimed Asphalt Pavement or RAP) for recycling. The quality of milling directly affects the quality of the recycled material.
- Recycling Plant (Central Mixing Plant): This equipment is responsible for processing the RAP by adding stabilizers or binders such as bitumen emulsion, foamed asphalt, or lime/cement. It mixes the RAP and additives thoroughly to produce a high-quality recycled mix.
- Paving Machines (Pavers): Once the recycled material is processed, pavers are used to lay the new recycled surface. These machines ensure that the recycled material is spread evenly across the roadway and compacted effectively for a smooth, durable surface.
- Compactors (Rollers): Rollers are used to compact the newly laid recycled asphalt material. Proper compaction is important to ensure that the recycled mix has the necessary strength and stability for long-term performance.
- Bitumen Sprayers: In techniques where bitumen emulsion or foamed asphalt is used, bitumen sprayers distribute the binder evenly over the RAP to create the desired mixture. They ensure uniform coverage for better bonding and performance.
- Material Feeders: These machines are used to feed raw materials such as aggregates, stabilizers, or binders into the recycling plant. Accurate material feeding is essential for achieving the desired mix proportions and ensuring consistent quality.
Conclusion
Cold Central Plant Recycling (CCPR) stands as a sustainable and cost-effective solution for road rehabilitation, offering significant environmental and economic benefits. By reusing existing materials and incorporating advanced techniques, it not only extends the lifespan of roads but also contributes to a greener future.