Prestressed concrete is substantially “prestressed” (compressed) during production, in a manner that strengthens it against tensile forces which will exist when in service. It is also known as pre tensile concrete, and is made by applying tension to the steel rebar during the curing process. Prestressed concrete is achieved by casting concrete into pre-assembled forms in combination with rebar and steel cable (strand) reinforcement. These cables are tensioned (stretched) to approximately three-quarters of their ultimate strength. Once the concrete cures to its required strength, the tensioning is released. The steel cables reacting to the release, transfers the tensile stresses into the concrete, rendering an even stronger structural component.
The main purpose of having prestressed concrete is to increase the load that the member can withstand. This is most common in long span beams found on bridges and railway viaducts, slab, and concrete piles. Prestressed concrete may be precast or cast in place, in this article we have focused on precast.
How is concrete prestressed?
To prestress a concrete member, a high-strength steel strand is laid in the form before concrete is placed. The strand is anchored and then pulled until it reaches a desired tension. The amount of tension applied can range from a few thousand to tens of thousands of psi depending on design.
After tension has been applied to the strand, concrete is poured into the form. As it cures, the concrete bonds to the strand. When it hardens to its specified strength, the strand is released and axial compression is transmitted to the cross-section of the member. The piece can then be stripped from the form and moved to storage.
Pretension prestressing can impart camber to the member that is useful in resisting service loads. This is frequently the case in double tees, which form the driving surfaces in parking structures. The cambered tee deflects slightly as cars drive over it, then returns to its original shape. The prestressed concrete doesn’t crack because the prestressing holds it in compression.
In some precast concrete members, such as walls and sandwich wall panels, no camber is desired. In these cases the strand is placed in the centroid of the wall, or of the wythes, to prevent the introduction of camber. In composite panels, stresses are adjusted so that the prestressing force coincides with the centroid of the composite section. Generally, precasters space strands uniformly across wall panels.

Advantages of prestressed precast concrete
Some of the common advantages of prestressing for precast concrete elements are-
- Prestressing helps in reducing the sizes of the sections and hence self weight or dead load component of applicable cable loads decreases, leading to a lighter weight structures and supporting elements including foundation elements
- The reduction in dead load also helps in reducing the seismic effects correspondingly and elements required to resist the imposed loads, such as- frames, columns, beams, shear walls etc, also become lighter in design
- The probability of large spans results in larger column-free internal spaces for the various floors
- For high-rise buildings, a reduction in member sizes will also result in shallower concrete deck framing depths, which in turn will reduce the floor to floor height requirements and the overall height of the building structure.
- The high tensile steel used in prestressing has higher strength than the ordinary reinforcing steel, with lesser sectional area. Typically high tensile steel is approximately 4.5 times stronger than ordinary steel, but costs only about twice as much per unit strength. This has an overall cost-reducing effect.
- Prestressing of beams and slabs is very economically applied in long-line precasting beds in mass-production mode in factories. Because of the inherent efficiencies of such mass production, methodologies with attendant reduction in labor costs, reduction in cost of formwork, with large number of reuses etc., additional saving result.
- Apart from the above, the common advantages of precasting are also available to prestressed elements , such as speed of construction due to parallel production. Further since prestressing enables longer spans, fewer number of elements are required overall and this significantly improves construction/erection speed.
- Prestressing at an appropriate age prevents shrinkage cracks from developing and hence the element is free of any cracks. Crack-free structures have better quality, water-tightness and better durability.
Difference between prestressed and non-prestressed precast concrete elements
Prestressing can be utilized to achieve higher span- to-depth ratios and provide increased resistance to cracking. It can be applied to precast as well as cast-in-situ concrete elements. Prestressing is generally incorporated into a member using pre-tensioning and post-tensioning processes. Reinforcing bars or welded wire reinforcement serve as secondary reinforcement, whereas in non-prestressed elements untensioned steel is used as the primary and the only reinforcement. For partially prestressed concrete, the resisting section comprises both prestressed and non-tensioned or passive reinforcement. Prestressing affects the state of stresses in a concrete member as well as the state of deflections or deformations.
Prestressing incorporation method using Pretensioned and Post tensioned elements
In pretensioned elements, the prestressing steel is tensioned initially between rigid abutments, often covering a number of precast elements located in between the two abutments. Then formwork is fixed in position in between the two abutments around the tensioned wire for the various elements. Secondary reinforcement and other items to be embedded in the concrete member are then placed in position and concrete is thereafter placed into the formwork. After the concrete has achieved the required strength and bond between the prestressing steel and concrete has developed, the long pretensioned steel is cut between the various precast elements and the prestressing force is transferred from steel to the concrete through bond. Development of good bonds is vital for successful performance of pretensioned elements. After this stage the elements are removed from the formwork and sent to stacking before usage. Since the prestressing steel is placed in the empty formwork , there are no restraints for the steel and hence the steel wire is straight/ horizontal between end anchorages. If a curved or trapezoidal or any other profile is desired for the steel then deviators have to be positioned at the locations of the geometry. These deviators have to be smooth to minimize friction while stressing and strong enough to resist the unbalanced forces which arise at the locations of geometry changes. While such deviated profiles may be useful from a design point of view, they would considerably add to the costs on account of the deviators and also may be more cumbersome. Self-stressing formworks can also be used where the anchorages are directly located on formwork instead of independent abutments.
When post tensioning is adopted, the prestressing steel elements are enclosed within a conduit or sheathing or duct or greased sleeve with the assembly being referred to as ‘tendon’. This tendon is typically tied to a cage or mat of reinforcement, placed within the formwork. Mechanical anchorage elements are placed at each of the two ends of the tendon and secured to the formwork. After concrete has been placed and cured within the form, prestressing force is applied to the high tensile steel and force held by the mechanical anchorages. At this point, the prestressing force has been transferred through the anchorages to the concrete member, which can then be taken out of the mould and sent for stacking before usage.
Under certain circumstances a combination of pretensioning and post tensioning may be used.This approach may be used where the self-stressing forms or tensioning abutments cannot sustain the full required design prestressing force for prestensioning. In such a case, the majority of the force is applied through post tensioned steel and post tensioned tendons are used later to introduce the remainder of the design prestressing force after the member is removed from the form. This approach may also be used in prestressed precast panels that are poured in a flat position but which need to stand in an upright position in service.
Applications of Prestressed Precast Concrete
Prestressed concrete is a highly versatile construction material as a result of it being an almost ideal combination of its two main constituents: high-strength steel, pre-stretched to allow its full strength to be easily realised; and modern concrete, pre-compressed to minimise cracking under tensile forces. Its wide range of application is reflected in its incorporation into the major design codes covering most areas of structural and civil engineering, including buildings, bridges, dams, foundations, pavements, piles, stadiums, silos, and tanks.
Building structures
The prestressing of concrete allows “load-balancing” forces to be introduced into the structure to counter in-service loadings. This provides many benefits to building structures:
- Longer spans for the same structural depth – Load balancing results in lower in-service deflections, which allows spans to be increased (and the number of supports reduced) without adding to structural depth.
- Reduced structural thickness – For a given span, lower in-service deflections allows thinner structural sections to be used, in turn resulting in lower floor-to-floor heights, or more room for building services.
- Faster stripping time – Typically, prestressed concrete building elements are fully stressed and self-supporting within five days. At this point they can have their formwork stripped and re-deployed to the next section of the building, accelerating construction “cycle-times”.
- Reduced material costs – The combination of reduced structural thickness, reduced conventional reinforcement quantities, and fast construction often results in prestressed concrete showing significant cost benefits in building structures compared to alternative structural materials.

Bridges
Concrete is the most popular structural material for bridges, and prestressed concrete is frequently adopted. In short-span bridges of around 10 to 40 metres (30 to 130 ft), prestressing is commonly employed in the form of precast pretensioned girders or planks.Medium-length structures of around 40 to 200 metres (150 to 650 ft), typically use precast-segmental, in-situ balanced-cantilever and incrementally-launched designs.For the longest bridges, prestressed concrete deck structures often form an integral part of cable-stayed designs.
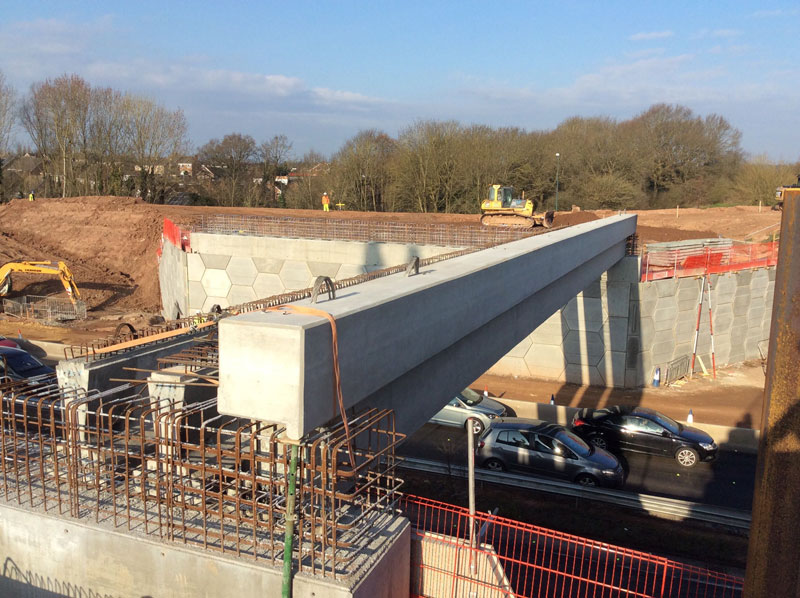
Dams
Concrete dams have used prestressing to counter uplift and increase their overall stability since the mid-1930s.Prestressing is also frequently retro-fitted as part of dam remediation works, such as for structural strengthening, or when raising crest or spillway heights. Most commonly, dam prestressing takes the form of post-tensioned anchors drilled into the dam’s concrete structure and/or the underlying rock strata. Such anchors typically comprise tendons of high-tensile bundled steel strands or individual threaded bars. Tendons are grouted to the concrete or rock at their far (internal) end, and have a significant “de-bonded” free-length at their external end which allows the tendon to stretch during tensioning. Tendons may be full-length bonded to the surrounding concrete or rock once tensioned, or (more commonly) have strands permanently encapsulated in corrosion-inhibiting grease over the free-length to permit long-term load monitoring and re-stressability.

Silos and tanks
Circular storage structures such as silos and tanks can use prestressing forces to directly resist the outward pressures generated by stored liquids or bulk-solids. Horizontally curved tendons are installed within the concrete wall to form a series of hoops, spaced vertically up the structure. When tensioned, these tendons exert both axial (compressive) and radial (inward) forces onto the structure, which can directly oppose the subsequent storage loadings. If the magnitude of the prestress is designed to always exceed the tensile stresses produced by the loadings, a permanent residual compression will exist in the wall concrete, assisting in maintaining a watertight crack-free structure

Nuclear and blast-containment structures
Prestressed concrete has been established as a reliable construction material for high-pressure containment structures such as nuclear reactor vessels and containment buildings, and petrochemical tank blast-containment walls. Using prestressing to place such structures into an initial state of bi-axial or triaxial compression increases their resistance to concrete cracking and leakage, while providing a proof-loaded, redundant and monitorable pressure-containment system.

Hardstands and pavements
Heavily loaded concrete ground-slabs and pavements can be sensitive to cracking and subsequent traffic-driven deterioration. As a result, prestressed concrete is regularly used in such structures as its pre-compression provides the concrete with the ability to resist the crack-inducing tensile stresses generated by in-service loading. This crack-resistance also allows individual slab sections to be constructed in larger pores than for conventionally reinforced concrete, resulting in wider joint spacings, reduced jointing costs and less long-term joint maintenance issues. Initial works have also been successfully conducted on the use of precast prestressed concrete for road pavements, where the speed and quality of the construction has been noted as being beneficial for this technique.

Conclusion
Prestressed concrete is the most durable, reliable and strongest concrete that is widely used for the construction of buildings and bridges. Longevity of prestressed structure is greater because the reinforcement stays unaffected. In addition to general advantages, such as excellent fire resistance, low maintenance costs, elegance, high corrosion-resistance, adaptability etc, the prestressed concrete is found to sustain the effec
Image Source:
www.oreillyconcrete.com, www.worldhighways.com, www.eliteprecast.co.uk, www.wolfsystem.at, tindallcorp.com, www.brickworks.com.au, www.prilhofer.com, precastbloks.com