The first boring machine reported to have been built was Henri-Joseph Maus’s Mountain Slicer. Commissioned by the King of Sardinia in 1845 to dig the Fréjus Rail Tunnel between France and Italy through the Alps, Maus had it built-in 1846 in an arms factory near Turin. It consisted of more than 100 percussion drills mounted in the front of a locomotive-sized machine, mechanically power-driven from the entrance of the tunnel. During the late 19th and early 20th century, inventors continued to design, build, and test TBMs in response to the need for tunnels for railroads, subways, sewers, water supplies, etc. TBMs employing rotating arrays of drills or hammers were patented. TBMs that resembled giant hole saws were proposed. Other TBMs consisted of a rotating drum with metal tines on its outer surface or a rotating circular plate covered with teeth, or revolving belts covered with metal teeth. However, all of these TBMs proved expensive, cumbersome, and unable to excavate hard rock; interest in TBMs therefore declined. Nevertheless, TBM development continued in potash and coal mines, where the rock was softer.
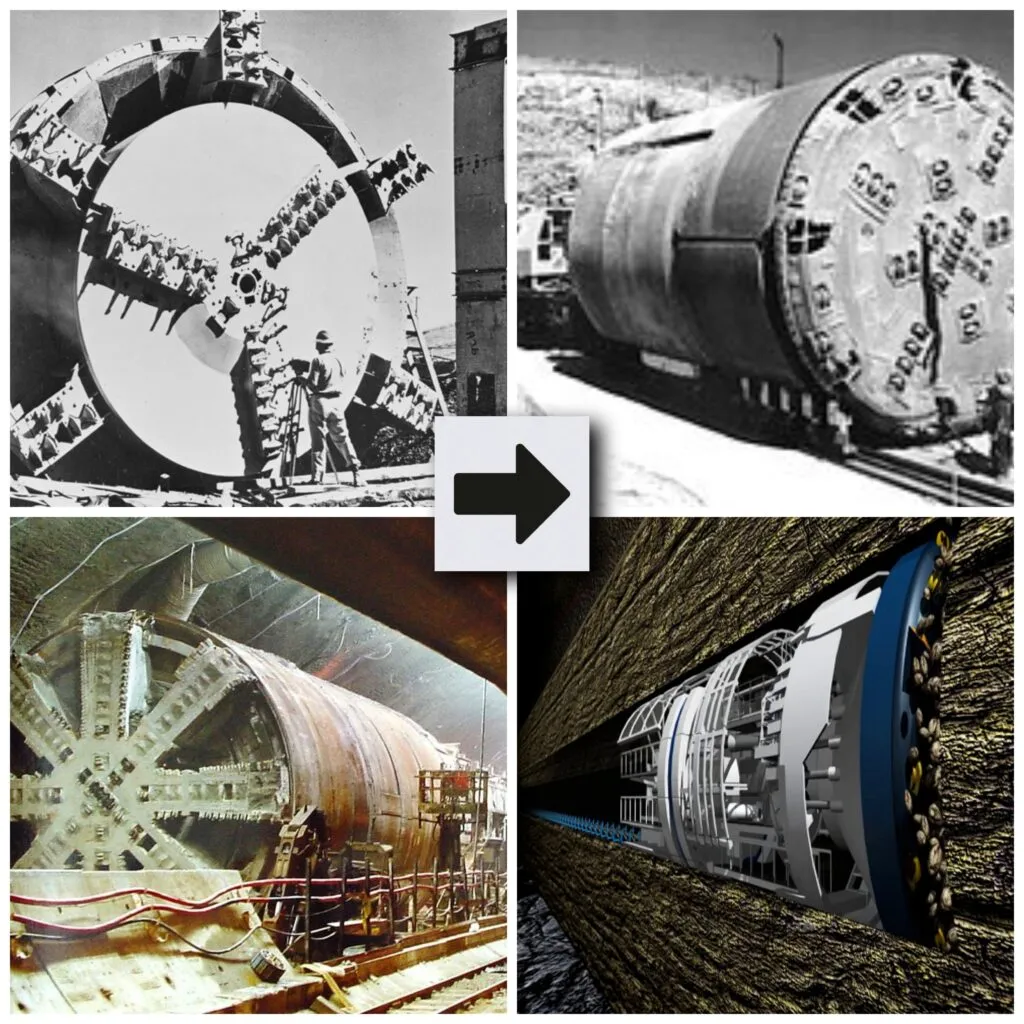
Tunnel boring machines have gone through an evolution, the modern TBMs typically consist of the rotating cutting wheel, called a cutter head, followed by the main bearing, a thrust system and trailing support mechanisms.
A tunnel boring machine (TBM) is a machine used to excavate tunnels with a circular cross-section for tunnels and metros. It offers the advantages of limiting the disturbance to the surrounding ground and producing a smooth tunnel wall. This significantly reduces the cost of lining the tunnel and makes them suitable to use in heavily urbanized areas. TBM applications can be segmented into traffic tunneling and utility tunneling. The traffic tunneling segment is divided into road tunneling and railway/metro tunneling, while the utility tunneling segment can be classified into water and sewage, hydropower, and pipelines.
Advantages of TBM
- Faster excavation
- Continuous operations
- Less rock damage
- Lesser support requirement
- Uniform muck
- Greater safety
Elements of TBM
- The boring system- an essential element as it determines the efficiency of a TBM. It consists of a cutter head with disc cutters mounted over it. When the cutter head rotates, the setup of the discs should be such that the entire cutting face should come in concentric tracks. The selection of cutter head and discs depends upon the rock type and the ease of cutting.
- The thrust and clamping system- it is responsible for the advanced push and the boring process. The thrust system provides the push to the cutter head through hydraulic cylinders. Thus, this system controls the movement of the cutter head.
- Muck-Removal System- it is connected to the conveyor belts and collects the muck generated near the cutterhead, which ultimately is disposed of outside the tunnel.
- Support System- supports are provided to avoid the sinking of TBM.For smaller diameter tunnels, the supports are provided around the rear carriage behind the TBM. While, in the case of bigger diameter tunnels, in addition to supports around the rear carriage, advancement supports such as rock bolts and umbrella reinforcement are provided.
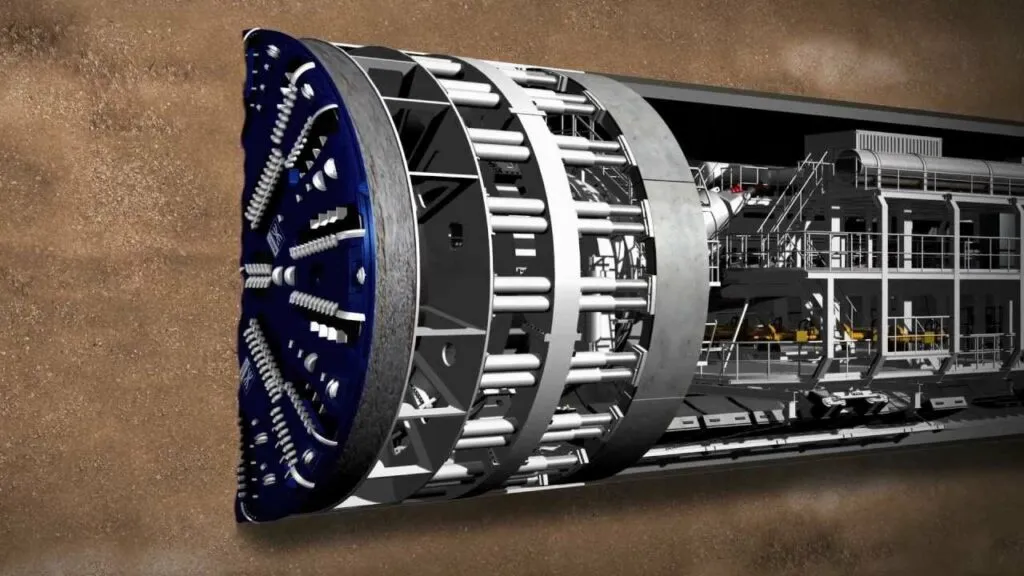
Parts of TBM
- Cutter head – comes with cutting discs and tools.
- Muck buckets- for carrying and disposing of excavated muck.
- Power supply System- equipped with cutter head rotation, and thrust.
- Bracing system -used during mining.
- Equipment – for ground support installation.
- Shielding – for workers and steering system.
Method of TBM
The cutter head on the TBM rotates and thrusts into the rock surface that lies ahead of it. This thrust causes the cutting disc tools to break the rocks.The grippers/braces develop the reaction to applied thrust and torque forces with the help of anchoring. The comes the following steps;
- Excavate the launching and retrieve shaft
- Assemble the TBM at the launching shaft
- Cut and excavate the tunnel
- The TBM then arrives in the retrieval shaft and gets dismantled for transportation.
Different types of TBM
Hard Rock TBM
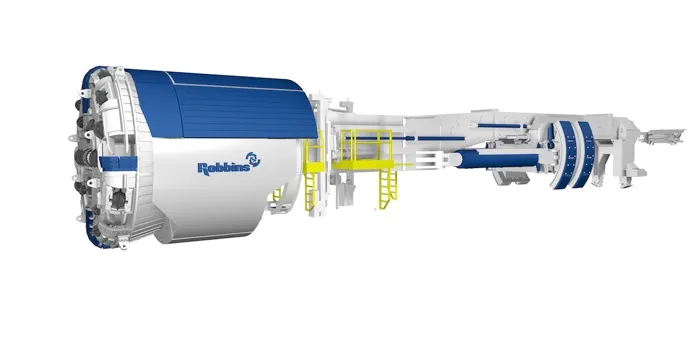
Hard rock, either shielded or open-type TBMs are used to excavate rocks with the help of disc cutters which are mounted on the cutter head. The rocks (muck) get chipped away as the disc cutter compresses stress fractures on it. Through the cutter head openings, the excavated rocks are transferred to the belt conveyor, and then to get them removed from the tunnel, these rocks are run through multiple conveyors. Now the excavated rocks are transferred to the belt conveyor through the cutter head openings.
Open-type TBMs have no shield, leaving the area behind the cutter head open for rock support. To advance, the machine uses a gripper system that pushes against the tunnel walls. Not all machines can be continuously steered while gripper shoes push on the walls, as with a Wirth machine, which steers only while ungripped. The machine will then push forward off the grippers gaining thrust. At the end of a stroke, the rear legs of the machine are lowered, the grippers and propel cylinders are retracted.
Shielded hard rock TBMs can be used in the fractured rock which erects concrete segments to support unstable tunnel walls and Double Shield TBMs have two modes such as they grip the tunnel walls to advance in the stable ground
Soft Ground TBM
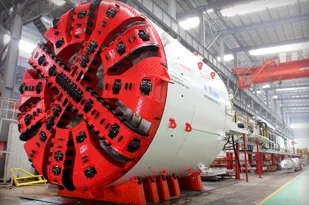
There are three types of soft ground TBMs as given below;
- Slurry Shield
- Earth Pressure Balance
- Open Face Type
Slurry Shield
It is used when the ground conditions are granular with very high water pressure. Hydrostatic pressure is applied on the excavation by filling the cutter head with pressurized slurry, which is also used as a transporting medium when mixed with the excavated material before it is pumped to the cutter head back and, then to a separation plant outside the tunnel. In soft ground with very high water pressure and large amounts of groundwater, Slurry Shield TBMs are needed. These machines offer a completely enclosed working environment. Soils are mixed with bentonite slurry, which must be removed from the tunnel through a system of slurry tubes that exit the tunnel. Large slurry separation plants are needed on the surface for this process, which separates the dirt from the slurry so it can be recycled back into the tunnel.
Earth Pressure Balance
Earth Pressure Balance machines are used in soft ground with less than 7 bar of pressure. The cutter head does not use disc cutters only, but instead, a combination of tungsten carbide cutting bits, carbide disc cutters, drag picks and/or hard rock disc cutters. The EPB gets its name because it uses the excavated material to balance the pressure at the tunnel face. It is a method of excavating, where the excavated material supports the tunnel face. It later gets plasticized with the help of slurry such that it is transportable.
Open Face Type
It is a method of excavating with no frontal support, relying on the fact that the ground being excavated will stand up with no support for a brief period, making it suitable to be used with rock types having strength up to 10MPa.The cutter head excavates the face within 150mm of the edge of the shield. Now, the shield is put forward with the cutter getting rid of the remaining ground in sync to the circular shape. Precast concrete is used to provide the ground support.
Microtunnel boring machine
It is fitted with small tunnels and diminishes in size of the general tunneling shield, the micro tunnel shield method is a digging technique that is used and the micro tunnel boring machine is quite similar to the general tunneling shield.It is a digging technique used to construct small tunnels, and diminish in size of a general tunneling shield. A micro tunnel boring machine is quite similar to a general tunneling shield but on a smaller scale.
Conclusion
Modern TBMs typically consist of the rotating cutting wheel, called a cutter head, followed by the main bearing, a thrust system and trailing support mechanisms. The type of machine used depends on the particular geology of the project, the amount of groundwater present and other factors. Though tunnels are becoming more common in transportation, most of us undermine the engineering behind them and the difficulty of planning and digging them. Thanks to advances in tunneling technology, tunneling has evolved quite a bit in the last century, with the technology being improved every day.
Image- resource-erectors.com, northeastmaglev.com, terratec.co, robbinstbm.com