Any negligence during the construction process may lead to distress in concrete slab pavement. This distress may appear in the form of cracks. Cracks in concrete slabs are caused by several variables including water intrusion, expansion and contraction from seasonal temperature changes, and sun exposure. It is important to understand the type of crack formed and its effects on structural stability.
Discussed below are different types of cracks that may occur in concrete slab pavement.
Uncontrolled shrinkage cracking
The time at which shrinkage cracks occur depends on the rate of drying but is usually several months to three or four years after casting. The loss of moisture from fresh concrete results in a reduction in volume. If the shrinkage movement is opposed by some external or internal restraint, stresses will develop. When the stress exceeds the tensile capacity of the concrete, cracks develop. Thin members with a large surface area such as slabs are particularly vulnerable. Drying out occurs from the surface and hence the surface layer is first affected. The surfaces of large cross-section members may crack because the movement is restrained by the inner section of concrete. Concrete near to corners and edges is particularly prone to cracking as loss of moisture takes place from the adjacent surfaces. There is no typical pattern of drying shrinkage cracking as the cracks form at any location where there is a restraint to shrinkage movement.
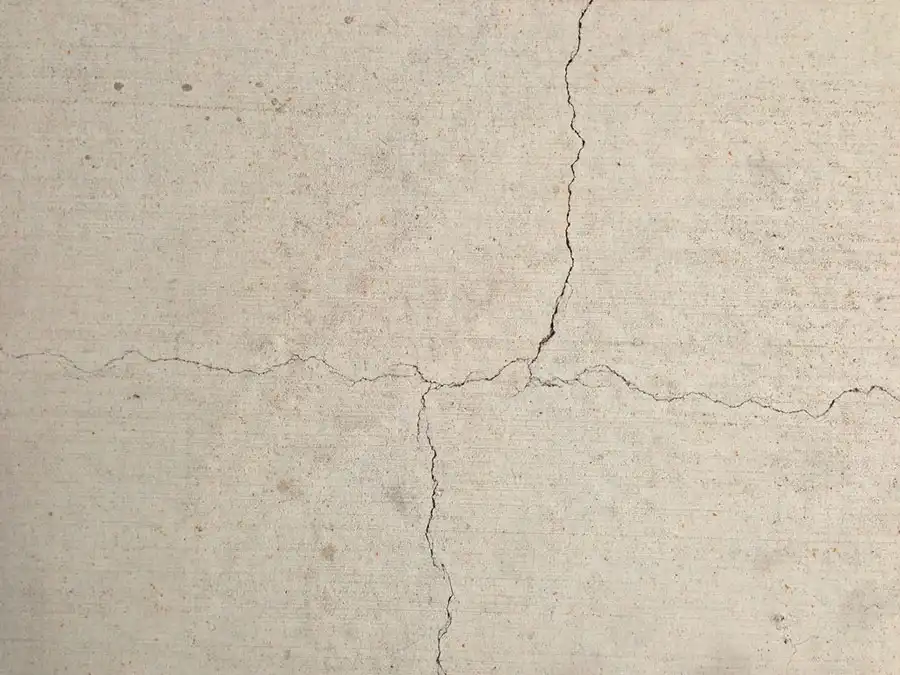
Blowups
Blowups are joint failures that are caused due to excessive expansion related to high temperatures and high moisture content. Blowups usually occur at joints or cracks in the pavement. During cold periods concrete slabs contract leaving wider joint openings. If these openings become filled with incompressible material subsequent PCC slab expansion during hot periods may cause high compressive stresses. If these stresses are great enough, the slabs may buckle and shatter to relieve the stresses. Blowup can be accelerated by joint spalling, durability cracking and freeze-thaw damage. If the pavement is susceptible to blowups, they begin to appear after 35 years of age.
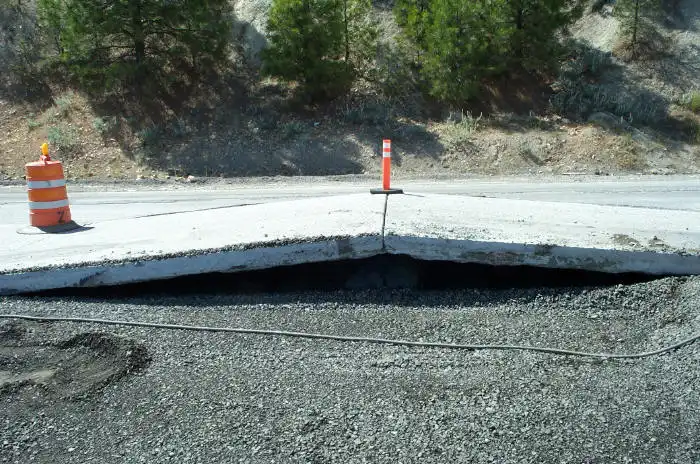
Pop-outs
A small piece of concrete that breaks loose from the surface of pavement concrete, either due to the expansive nature of aggregate or due to the low quality of material and workmanship, is known as pop-out. 25 to 100 mm in diameter and 13 to 50 mm in depth are the usual sizes of pop-outs. Pop-outs caused by alkali-silica reactions may occur as early as a few hours to weeks and sometimes even within a year of concrete placement.
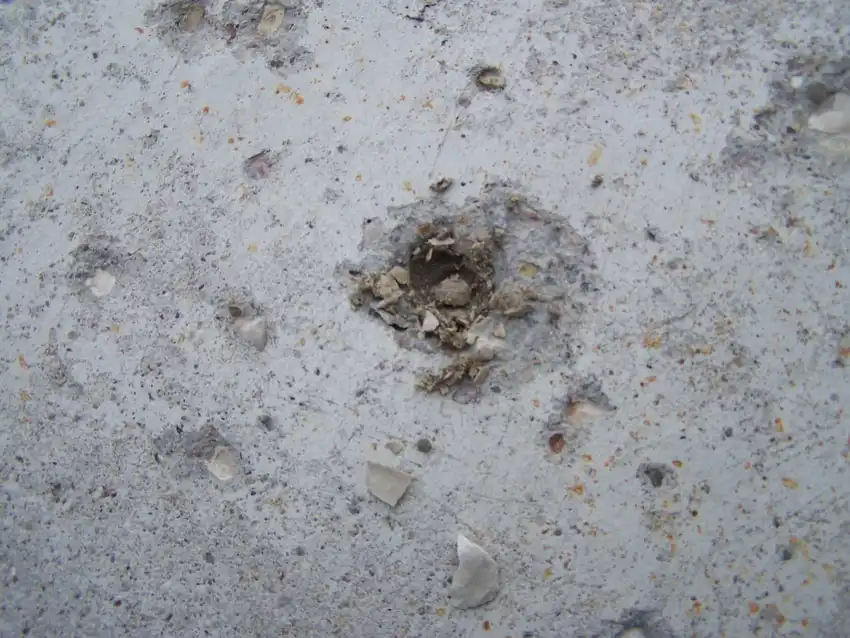
Expansion Cracks
In very hot weather a concrete slab, like anything else, will expand as it gets hotter. This can cause great stress on a slab. As the concrete expands, it pushes against any object in its path, such as a brick wall or an adjacent slab of concrete. If neither has the ability to flex, the resulting force will cause something to crack. Expansion joints are used as a point of separation (or isolation), between other static surfaces to prevent this type of cracking.
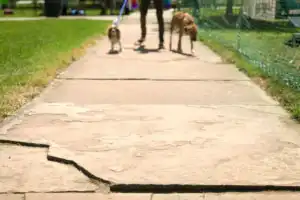
Corner break
A crack that intersects the joint of the pavement near the corner of the slab (within 200 mm) is called corner break or corner crack. It can extend through the entire slab. The causes that are responsible for corner break are high corner stresses, loss of soil support, curling and warping stresses and ineffective load transfer at the joints. Corner break leads to infiltration of moisture, faulting, spalling and disintegration in the pavement slab. Full-depth repair is the solution to refurbish the pavement that suffers a corner break.

Settlement cracks
Settlement cracks in a slab indicate inadequate site preparation, such as failure to compact fill on which a slab was poured. Settlement cracks appear on subbase and subgrade. Locations of an underlying pipe culvert and slab culvert are more prone to settlement cracking. Settlement of subgrade and other pavement layers over pipe culverts and in the vicinity of slab culverts mainly during and after the rainy season can cause full depth cracking of overlying concrete slabs.
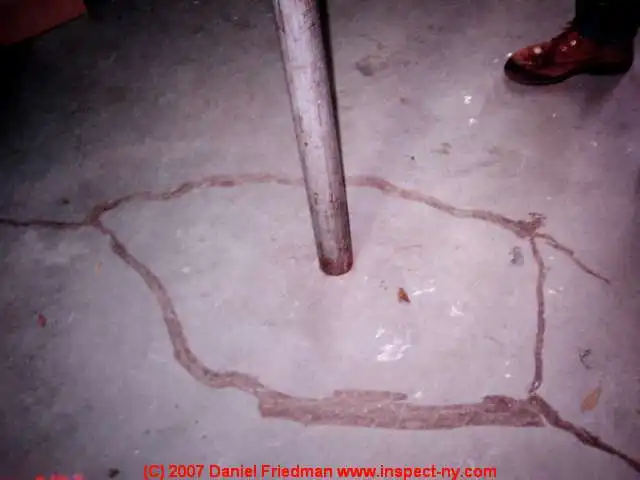
Cracks over dowel bars
Dowel bars are typically placed at the mid-depth of the slab and should be parallel to the pavement surface and parallel to the direction of travel. The center of the dowel bar should be below the joint. If dowel placement deviates from the desired position, it is said to be misaligned. Cracks over dowel bars appear at 25- 40 mm depth. These are surface cracks. The reason for these types of cracks could be, too much vibration of dowel bar inserter, stiff concrete mix, shallow depth of trowel bars and the natural phenomenon of settling heavy solids in the liquid medium around dowels. Inadequate vibration of the DBI unit and stiff concrete mix may leave a dowel trail in which concrete is not compacted properly. Sometimes, surface concrete over dowel locations also becomes weak due to the high water-cement ratio leading to the abrasion of mortar from the surface.

Cracks Caused by Overloading the Slab
Another factor which contributes to cracking is placing excessive weight atop the slab. Although it is a very strong material, concrete still has load limits. When you hear someone speak of 4,000 psi concrete, they are referring to the fact that it would take 4,000 pounds per square inch of pressure to crush it. When groundwater migrates under the concrete it causes the underlying soil to become soft or spongy. Excessive weight on the slab at this point can press the concrete down. Since the flexural strength of concrete is less than its compressive strength, the concrete bends to its breaking point. Homeowners who place large recreational vehicles or dumpsters on their driveways are more likely to see this type of cracking. Driving heavy vehicles off the edge of a slab creates a similar type of crack.

Punch-out
Punch-out is nothing but breaking a small portion of the concrete slab into several pieces. It is localized behaviour in the concrete slab. Punch-out causes roughness of the pavement surface and creates ingress to moisture into the pavement and later in base and subgrade, leading to erosion of base or subgrade. Punching makes cracks to spall and disintegrates them.

Cracks due to saw cut misplacement at transverse joint
While determining the location of the saw cutting, the distance where the shrinkage and expansion are still within the limits of the ability of concrete pavement must be considered. The depth of the saw cutting must make this place the weakest location. Saw cutting must also consider the maturity of the concrete to be able to withstand micro pre-stress at that age. Without those three things, we just move the location of the transverse crack. Late or shallow saw cutting of longitudinal joints causes longitudinal cracking]. The crack will shift from the saw cutting line, hereinafter referred to as misalignment crack. Initial crack is not caused by misalignment of concrete pavement Vibration in the construction of concrete pavement in open traffic conditions makes the concrete pavement surface more at risk for the onset of cracks.
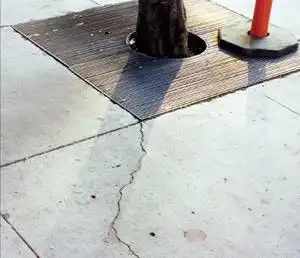
Crazing cracks
Crazing cracks are very fine surface cracks that resemble spider webs or shattered glass. They can happen on any concrete slab when the top loses moisture too quickly. Crazing cracks can be unsightly, but are not a structural problem. They are so fine that there is no way to repair them.
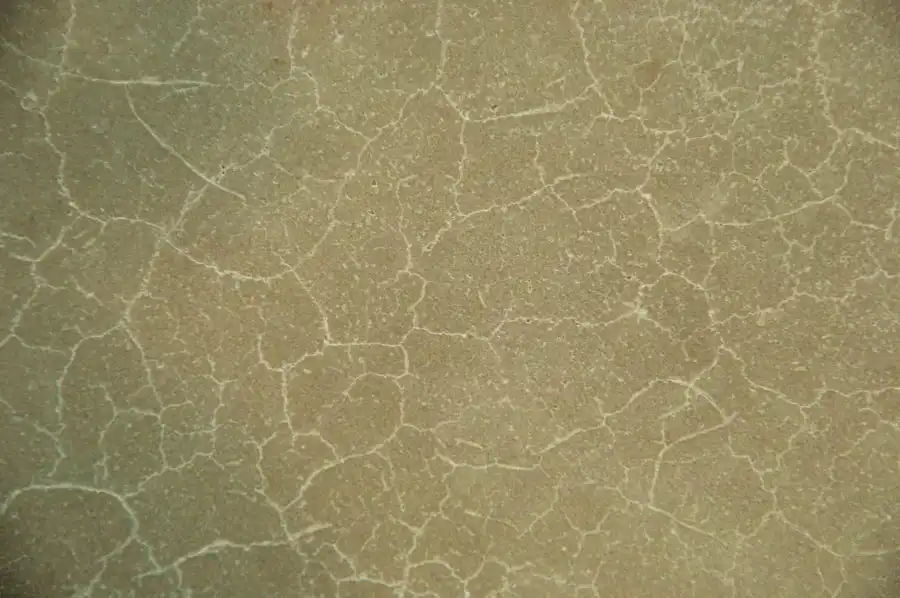
Crusting cracks
Crusting cracks often happen during the concrete stamping process. They usually occur on sunny or windy days when the top of the slab dries out sooner than the bottom. The top becomes crusty so when the stamp is embedded, it pulls the surface apart near the stamped joints causing small cracks around the outside edges of the “stones”. Although they are cosmetically unappealing, crusting cracks present no structural problem but may be patched if desired.
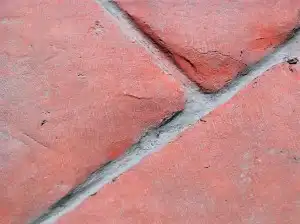
Cracks over slab and box culverts
When a concrete pavement is constructed over a box culvert, it is important to match the location of transverse joints with the boundary of the box culvert. Otherwise, full-depth transverse cracks would likely develop on the pavement slabs just above the location of the boundary of the box culvert. This might lead to the possibility of the development of transverse cracks in concrete pavement. The occurrence of these types of cracks is more wherein pavement quality concrete and dry lean concrete layers are laid directly over the culvert slab without any intermediate layer of granular sub-base.

Plastic shrinkage cracks
The primary cause of plastic shrinkage cracks is the rapid evaporation of water from the surface of the concrete. Immediately after the concrete has been placed, the particles within the concrete begin to settle. When the particles settle, the water within the concrete displaces and rises to the top. This process is better known as “bleeding.” Not all of the water within the concrete displaces. Under most weather conditions, some of the water on the surface of the concrete evaporates. The rate of evaporation depends on factors such as the temperature of the concrete, temperature of the air, relative humidity, and wind velocity surrounding the concrete. Plastic shrinkage cracks typically occur on horizontal surfaces exposed to the atmosphere. These cracks are different from other early cracks because they are deeper and wider. Plastic shrinkage cracks are typically two to four inches deep and approximately one-eighth inch wide. They may also extend several feet in length adopting a crow’s-foot pattern. These cracks form before any bond has developed between the aggregate particles and mortar. Therefore, the cracks tend to follow the edges of large aggregate particles or reinforcing bars and never break through the aggregate particles.
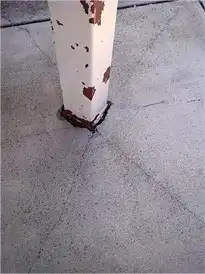
Heaving cracks
One important factor which contributes to cracking is ground movement brought on by freeze/thaw cycles. During such cycles, the frozen ground can lift as much as several inches, and then settle again when the ground thaws. If the slab is not free to move with the soil, the slab will crack. The presence of large tree roots can also cause concrete to heave. If a tree is located too close to a concrete slab, the growing roots can lift and crack the concrete
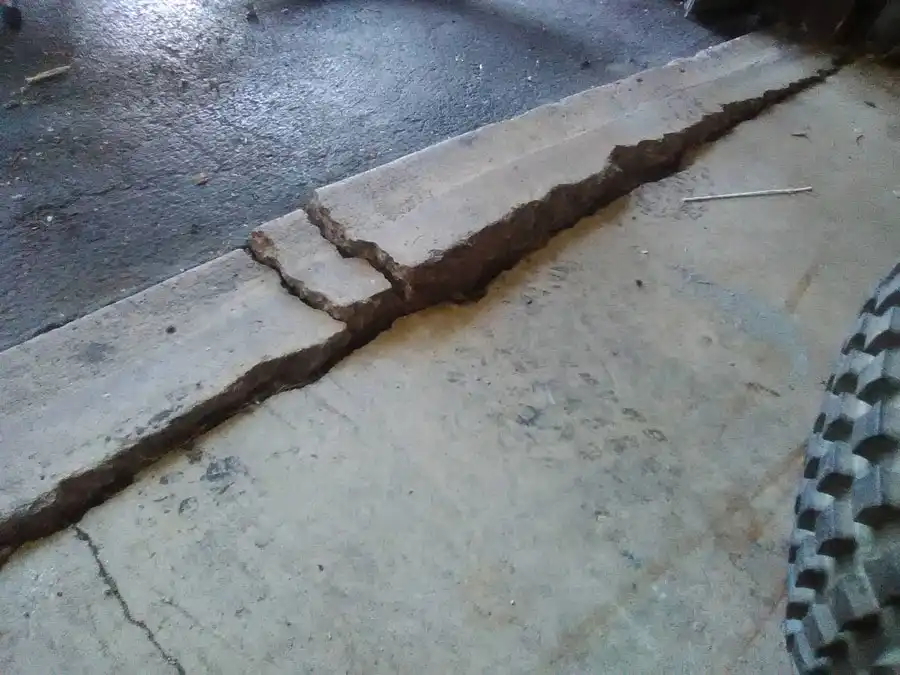
Alkali-Silica Reaction Cracks
The chemical reaction between the alkali hydroxide in the concrete and reactive aggregates produces an expansive gel, causing map cracking or directional cracking (prestressed members) in the structure. The main components of concrete are sand and gravel, which in turn contain silicates such as quartz or feldspar. The alkaline water reacts with these silicates and forms a so-called alkali calcium silicate hydrate. This mineral accumulates moisture in its structure, which causes it to expand and gradually crack the concrete from within.
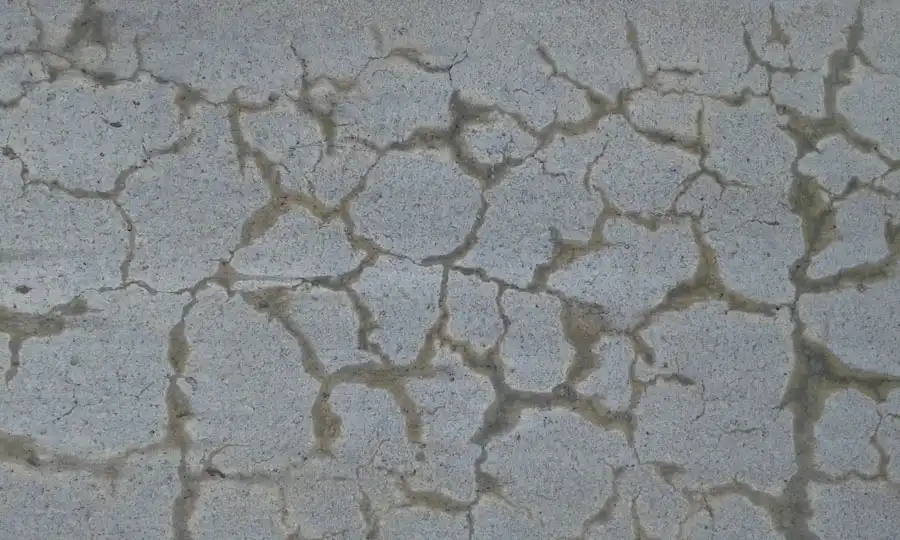
Curb cracking
Whenever the curbs are not cast monolithically with concrete pavement slabs, curb cracking could appear. It may also be observed, though not so predominantly, on the curbs laid cast-in-situ with curb casting machines but not cast monolithically with the slabs. If the transverse joint of these curbs is blocked by soil, stone grits and other material then the expansion of curbs along with concrete slabs becomes difficult and due to excessive compressive stresses curbs may crack.
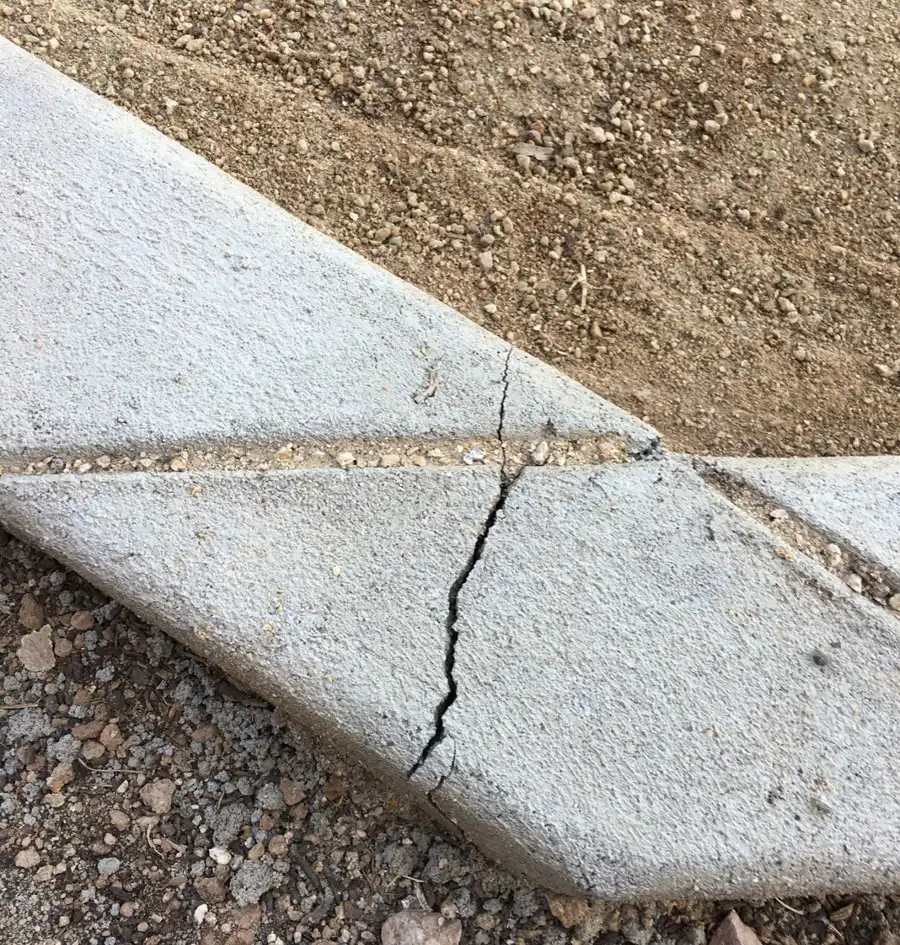
Conclusion
In general, cracking can be minimised by taking various types of appropriate measures. These measures include structural assessment and the selection of appropriate repair methods and products requires expert technical advice. In the upcoming article, we will analyse different repair methods for these crack prevention in concrete pavement slabs
Image Source: concretesupplyco.com, constructionmentor.net, pavementinteractive.org, researchgate.net, wwwapps.dotd.la.gov, concreteconstruction.net, indecorativeconcrete.com, loyalisttownship.ca, diy.stackexchange.com, cshub.mit.edu, cuttingedgecurbing.com