The tensile membrane structure is the term usually used to refer to the construction of roofs using a membrane held in place on steel cables. It is the form of structure that is carrying only tension, eliminating compression or bending. Most tensile structures are supported by some form of compression or bending elements. Tensile structures are the most common type of thin-shell structures.
Tensile structures have been in use since ancient times. The most rudimentary applications could be seen in the form of tents and other temporary roofing used by nomadic tribes. These structures exhibit nonlinear behavior, as opposed to linear relationships observed in conventional structures, which use steel as its primary material resource. The non-linear relationship can be observed in geometry as well as in material aspects.
A tensile membrane structure is most often used as roofs as they can economically and attractively span large distances. Tensile membrane structures may also be used as complete buildings, with a few common applications such as sports facilities, warehousing and storage buildings, and exhibition venues.
The first development of practical calculations of stresses and deformations of tensile structures, shells and membranes by a Russian engineer Vladimir Shukhov. he designed eight tensile structures and thin-shell structures exhibition pavilions for the Nizhny Novgorod Fair of 1896, covering an area of 27,000 square meters. Noways, the tensile membrane has found popularity worldwide.
Classification of tensile membranes
There are three different main classifications in the field of tensile construction systems: membrane tensioned structures, mesh tensioned, and pneumatic structures. The first relates to structures in which a membrane is held by cables, allowing the distribution of the tensile stresses through its form. The second case corresponds to structures in which a mesh of cables carries the intrinsic forces, transmitting them to separate elements, for example, sheets of glass or wood. In the third case, a protective membrane is supported through air pressure.
Tensile membrane materials
Textile membranes usually consist of proved or coated fabrics. Some types of nonwovens are in use for special applications. Today, there is a wide range of natural and synthetic fibres which could be used for the production of the membranes. However, the typical demands on structural textile membranes and the necessity of a series of detailed tests with the material itself as well as with its joints have, for common use, led to a small selection of fibres.
The fabrics themselves are not waterproof. Also, most of the fibres will be attacked by environmental effects, as e.g. sunlight radiation. Inter alia, this usually results in a reduction of strength and flexibility. The fabrics therefore must be proved or coated. Proving is the preferential treatment for cotton and cotton/synthetic fabrics. Coating with PVC is the most common solution for Polyester -and Aramid fabrics, coating with PTFE is typical for glass fibre-fabrics.
The coating system must be well suited to the fibres used for the fabric itself: on the one hand, the coatings are applied onto the fabrics at high temperatures which the fibres must be able to withstand, on the other hand, the chemical and mechanical adhesion to the fabric is of importance for the shear stiffness and with that also for the load bearing capacity of many of the structural details. The strength of a membrane depends on the type of yarn, the type of weave and the count used for the fabric. The PVC/Polyester and the PTFE/Glass materials which can be bought from stock show a strength up to 200 kN/m (short term tensile test, 230 C). On inquiry, qualities up to more than 300 leN/m can be produced. The strong qualities of PVCI Aramides can reach the order of 600 kN/m. However, because of their high price and missing translucency, the latter are chosen for special cases only.
The most popular types of tensile fibers are discussed below-
PVC Coated Polyester: PVC coated polyester can be a great material choice for both permanent and temporary tensile fabric structures. PVC coated polyester is known for its excellent strength, flexibility, translucency and affordability compared to PTFE coated glass cloth and ETFE. The PVC coating, which is applied to polyester includes UV stabilizers, fire retardant additives, and anti-fungicides. PVC coated polyester fabrics have a structural lifespan greater than 20 years.
PTFE Coated Glass Cloth: PTFE coated glass cloth was developed by DuPont in the 1960s and has been used to create tensile fabric structures since the early 1970s. Originally, the material had a lifespan of 25 years; however, this has already been exceeded, with present day expectations lying somewhere between 30 and 50 years.
ETFE: While ETFE is a film rather than a fabric, it is worth touching on because it is commonly used as an alternative to structural glass and is rapidly growing in its applications. ETFE is an excellent choice if thermal insulation is a priority of your project.

Types of Tensile Structures
There are three types of tensile structures, each of them is explained below.
1. Linear Tensile Structures
Linear tensile structures are the structure in which all the members are in linear tensile forces. These linear members are supported by the compression members, but the major loads are carried out by tensile members. A common example of this structure is cable-suspended bridges. The main pillars act as compression members, but the whole load is carried out by the cables which are in tension.
2. Three-dimensional Tensile Structures
Three-dimensional tensile structures is a compilation of elements that are primarily in tension, with the compression being transferred to a central mast and down into the ground. The most common occurrence of three-dimensional tension can be seen at sports arenas and usually serve as roofs for these structures.
3. Surface-Stressed Tensile Structures
Surface-stressed tensile structures are the same as other 2 tensile structures, but the surface members are tension bearing members. Fabric tensile structures are the great examples of Surface-stressed tensile structures, where the vertical pillars hold the specially designed fabric which is in tension.
Advantages of Tensile Structures
Owners and developers across the globe have discovered the advantages of building with tensile fabric building structures as opposed to traditional building products. Whether you are looking for an entertainment venue such as an amphitheater, walkway coverage for travelers at transit stations, or a structure to make your athletic fields suitable for year-round competition, a tensile fabric building structure may be the ideal solution. Some of the advantages of tensile membrane structures are given below-
- With proper construction methodologies in place by design-build specialty contractors for tensile architecture, the installation of tension membrane structures is often faster and more cost-effective in comparison to traditional construction projects.
- Because of the translucency associated with nearly all of the fabric options, tensile fabric building structures provide an abundance of daytime light underneath, making it an inviting and comfortable space below.
- In addition to being more weather-proof and lighter in weight than sticks and animal skins, modern fabrics offer advantages such as protection from ultraviolet (UV) radiation and greater wind resistance. They are also coated with materials that resist UV degradation.
- Due to the unique flexible characteristics of the fabric membrane, tensioned membrane structures allow architects, designers, and engineers the opportunity to experiment with form and create visually exciting and iconic structures.
- When looking to cover large areas of space, the light weight nature of membrane is a cost-effective solution for long span applications while allowing for the possibility of column-free space. As a result, tensile membrane requires less structural steel supports compared to traditional building products, ultimately reducing project costs for building owners.
- The weight of the membrane in tensile structures is very less and consequently, the quantity of structural steel utilized to support the membrane is also minimal. Thus, the weight, as well as the overall cost of tensile structures is much less as compared to conventional roofing systems. As stainless steel is utilized, more useful space free of columns becomes available. As the weight of the structure is so little, it will not experience much acceleration forces under seismic action.
- The membrane material itself can withstand within the range of -40 o C to +70 o C. Companies of warranty for their fabrics and usually the minimum life span of these structures is about 25 years.
- The erection of the tensile structures takes less than a week to complete as all the patterning & fabrication works are mostly carried out in warehouses and the structure is erected on site. The construction period is only the time required for its erection, which can be reduced to a minimum by using advanced construction equipment and techniques.
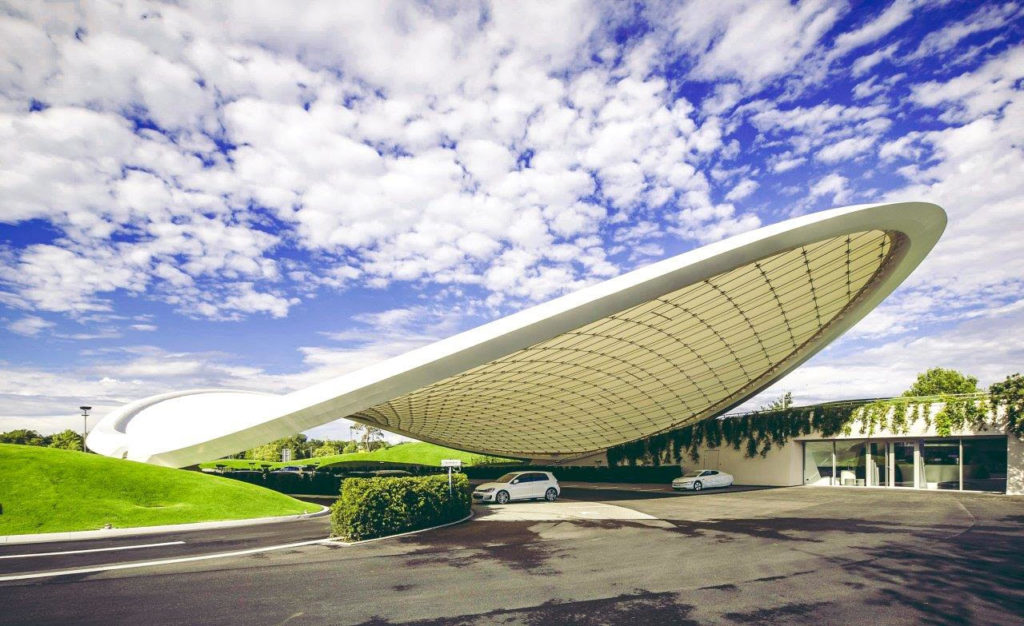
Conclusion
Membrane structures can be designed, analysed and erected in any shape or form we require. It provides extra space for the designer to experiment with different shapes. The membrane fabric can even incorporate in artificial lighting, which can add another aesthetic dimension to them. It is not only a cost-effective solution but also an aesthetically pleasing one too. The tensile structures are a relatively newer concept which is just entering the Indian construction scenario and quickly gaining popularity. The following are the areas where the tensile structure outclasses the conventional forms of structures.
Image Source- makmax.com, alibaba.com, birdair.inc