
Technical Manager – Dextra
Reinforced concrete design and construction practice has historically focused on the use of lap splicing as a method of transferring load between reinforcement bars. This relies on the load being transferred from one rebar, through the surrounding concrete and into the adjacent lapped rebar. However, the lapping of reinforcement is not always the most appropriate splicing method and there are many situations where the use of mechanical rebar couplers is more desirable from a design perspective, more convenient from a construction perspective, or both.
1. Principle and uses
Rebar coupler systems, sometimes also known as mechanical splices, are used as an alternative to traditional lap splices in concrete. They transmit the rebar load directly from one rebar to another without relying on concrete bond, concrete strength, or the condition of the concrete surrounding the rebar and coupler.

2. Advantages of sing rebar coupler systems
There are many well documented advantages to using rebar coupler systems. These include:
2.1 Rebar Continuity
Reinforced concrete design codes of practice, including IS 456, assume that the detailing, quality of materials and workmanship is such that the transmission of forces in a lap splice from one rebar to the other is assured. However, if the bond between the concrete and the rebar is lost, possibly because of concrete cracking, deterioration, poor on site workmanship, rebar corrosion and subsequent spalling etc. then the rebar lap splice may fail. Rebar couplers do not rely on concrete bonds and therefore they create more reliable rebar continuity.
2.2 Avoidance of Transverse Splitting Forces
Many structural concrete codes of practice recommend the use of rebar couplers as an alternative to lapping, particularly for large rebar diameters where splitting and dowel action forces can be significant. IS 456 states “lap splices shall not be used for bars larger than 36mm” and goes on to say that if there is no alternative, then lapping of large diameter bars should be accompanied by additional spirals along the lap length to act as confinement reinforcement.
2.3 Reduction of Rebar Congestion
Lapping rebar in heavily reinforced sections can cause significant congestion, resulting in problems fixing the steel and insufficient room for the proper placement and compaction of the concrete. The use of rebar couplers can significantly reduce congestion making the placement and compaction of the concrete easier, leading to less risk of concrete segregation due to over vibration and as a result an increase in the concrete quality.

2.4 Safety
On site safety during construction is paramount and the use of rebar couplers can contribute to enhancing site safety.
- Rebar protruding through shuttering, which can be hazardous, can be eliminated by using couplers butted up against the shuttering or formwork, allowing the connection of the adjoining rebar after the shuttering or formwork is removed.
- On site welding of rebar can be eliminated by joining prefabricated cages with rebar couplers.
As well as construction site safety, rebar couplers are often seen as a safer alternative to lapping as they do not rely on concrete bonds and therefore they create more reliable rebar continuity – see Section 2.1.
2.5 Ease of Construction
The safety advantages of rebar couplers do not come at the expense of constructability. In fact, the use of rebar couplers can make on or off-site construction easier and faster as well as safer.
- Prefabricated rebar cages can be easily connected on site making on-site welding of rebar unnecessary.
- Individual concrete elements and construction joints can be joined without the need to drill through shuttering.
- The use of couplers allows for the face of concrete elements to remain smooth during construction, making construction easier and faster.

(i) The use of couplers at concrete faces means that concrete elements can be joined without the need to drill through formwork.
(ii) Couplers can be used to join prefabricated cages on site, making on-site welding unnecessary.
2.6 Reduction in Steel Use
The use of rebar couplers reduces steel consumption and can therefore be an environmentally friendly and more sustainable option than lapping. The rebar steel saving being equivalent to the lap length.

2.7 Seismic Use
For major earthquakes, the design approach of IS 1893-1 is to prevent the collapse of structures. Severe cracking and the degradation of concrete elements is therefore possible. In such cases, the bond between the rebar and the concrete may be compromised and this in turn will compromise the ability of a lap splice to transfer load from one bar to another, and thus compromise the ability of the element to carry load. Mechanical rebar couplers do not rely on rebar bond with the concrete to transfer the load from one bar to the other and are therefore often seen as a safer option to lap splicing for seismically designed structures.
If conventional lap splicing is employed, the seismic design of reinforced concrete structures will often exacerbate reinforcement congestion problems. In addition, the significant increase in lap lengths and other codified detailing requirements can lead to over-reinforced concrete and a potential for non-ductile, brittle behaviour at the lap splice region due to the concentration of stresses at both ends of the lap, inadvertently altering the elements deformation capacity. In such cases the use of mechanical rebar couplers is therefore seen as a distinct advantage.
The ductility of reinforcement is of significant importance in seismic design, and the principal measurement of rebar ductility is the percentage elongation at maximum force, as defined in IS 1786. For rebar coupler systems conforming to IS 16172 there is a ductility requirement for the adjoining rebar. However, this requirement is less that that given in IS 1786, principle because IS 16172 does not require a “bar break” level of rebar coupler performance, which would force the rebar to be loaded to it’s maximum force. Thus, for a rebar coupler system, the only way to retain the full rebar ductility, is to ensure that it is not reduced in capacity as a result of a stress raiser or loss of rebar cross section at the mechanical rebar coupler. In other words, the coupler needs to be what is commonly known as a “bar break” system. That is, a system which exceeds the ultimate tensile strength of the actual rebar it is connected to, ultimately forcing a tensile failure to occur in the rebar away from the influence of the coupler splice.
Full capacity “bar break” rebar coupler systems therefore provide both a strength and a ductility advantage over systems with a lower level of strength and are the only types of systems whereby the ductility of the connecting rebar is not compromised.
2.8 Advantages Summary
Mechanical rebar couplers create a continuity of reinforcement which is not reliant on the quality or integrity of the concrete. Their use creates less rebar congestion, more convenient and often safer site practice as well as reducing the amount of steel used. While different performance levels exist for rebar couplers, a guaranteed “bar break” coupler means that there will ultimately be no brittle failure in a ‘beyond design” event and the full ductility of the rebar will be maintained, a feature which is recommended in safety critical applications or if the structure could be subject to impact damage or a seismic event.
3. Types of Coupler System
SP 34 and IS 16172 Annex A both describe some of the rebar coupler technologies available. In broad terms they can be broken down into:
- Couplers requiring rebar end preparation such as threading or the extrusion of sleeves onto the end of the rebar.
- Repair couplers requiring no rebar end preparation.
- Grouted couplers, requiring one or both adjoining rebars to be grouted into the coupler.
In addition, some coupler systems have in-build quality control features whereby each and every connection is automatically and systematically proof loaded by the processing machinery as part of a quality control procedure.

The ends of the rebar are cold forged to increase their diameter, prior to threading

Male and female sleeves are swaged/extruded onto the rebar ends
The coupler types shown in Figure 5 and 6 are both simple to install and can be verified to be installed correctly by visual inspection, as it is clear to see when the appropriate level of male, female, thread engagement is achieved. Other types of couplers are more difficult and often impossible to visually verify that they are installed correctly.
Some types of coupler systems require to be torqued to a specific minimum value in order to achieve the correct level of performance. It is advisable that these types of couplers are marked in some way after the torquing operation has been completed, in order to give a visual indication that the correct procedures have been followed.
3.1 Couplers Requiring Rebar End Preparation
Coupler systems requiring rebar end preparation are usually the most cost effective, but their use needs to be pre-planned as the bar end processing usually occurs at the rebar cut and bend depot and supplied to site with the appropriate rebar. These cut and bend fabricators would usually hold a stock of couplers and have the machinery to process the bar ends to suit the coupler system.
Each system is typically available in a number of different configurations. These are:
- Standard.
Standard couplers require the adjoining rebar to be rotated to form the connection.
- Positional.
Positional coupler systems do not require the rotation of the adjoining rebar.
- Bridging.
Bridging coupler systems will allow the adjoining rebar to be connected without rotation while also bridging a gap.
- Transition.
Transition couplers allow connection between different rebar diameters.
3.1.1 Standard Couplers
A standard coupler configuration required the rotation of the adjoining rebar to make the connection.

3.1.2 Positional Couplers
A typical positional coupler configuration has an extended length of thread onto the ribs of one rebar allowing the coupler unit to be fully screwed onto one bar, before being screwed back onto the adjoining rebar. This type of system is often supplied with a locknut in order to lock the assembly into position without rotating the rebars.

3.1.3 Bridging Couplers
Where the ends of the connecting rebar cannot be brought together, a bridging coupler system can be used in order to bridge a small gap between the ends of the rebar.

3.1.4 Transitional Couplers
Transition coupler systems are designed to connect rebar of two different diameters. Sometimes this can be done by applying a smaller thread on the larger diameter bar, and other times by using a transitional coupler, as shown in Figure 8. If couplers are used to connect rebar of different diameters, it is usual for the performance requirements are based on the smaller of the two rebar diameters used.

4. Rebar Coupler Requirements for use in India
IS 16172 covers the performance requirements for rebar couplers. The standard also describes the testing methods, rebar coupler classification, workmanship, sampling and criteria for conformity, identification and marking. In addition, Annex A describes some of the different types of rebar coupler technologies available.
4.1 Performance Requirements
All rebar couplers are required to comply with the Indian rebar coupler standard IS 16172. This details the following performance requirements:
- Static tensile load
- Ductility
- Slip (residual elongation)
- Cyclic tensile loading
- Low Cycle fatigue loading
In addition, there is an optional high cyclic fatigue loading requirement.
All testing should be conducted in accordance with Annexes B, C, D and E of IS 16172.
4.1.1 Tensile Strength
The tensile strength of the rebar coupler assembly shall be greater than that of the minimum specified tensile strength of the adjoining rebar. For example, when used with Fe 550D rebar to IS 1786, which has a minimum tensile strength of 600 Mpa, the tensile strength of the rebar coupler assembly shall not be less than the load equating to 600 Mpa stress in the adjoining rebar.
However, it should be noted that a footnote also exists in IS 16172 stating “For important structures, the user may specify stringent requirement of bar break to avoid splice failure and to develop full tensile strength of the bar.”
4.1.2 Ductility
Ductility is expressed in terms of the percentage elongation at maximum force measured on the adjoining rebar when the assembly is loaded to destruction. A minimum of 3% should be achieved before the failure of the test assembly.
4.1.3 Slip (residual elongation)
Slip or residual elongation is a measure of how much permanent movement there is across the coupler assembly after unloading from sixty percent of the specified yield strength of the rebar. The recorded value must not be greater than 0.10mm.
4.1.4 Cyclic Tension Loading
To simulate loading which could be attributed to an earthquake, 100 load cycles between loads equating to 5% to 90 % of the specified yield strength of the rebar are applied. After cyclic loading the assembly is loaded to destruction and should exhibit no loss of static tension strength. This tension strength can be assessed statistically.
4.1.5 Fatigue Loading
Low cycle fatigue testing is mandatory. 10000 cycles at a stress range of +173 Mpa to -173 Mpa are applied at a constant frequency. Couplers complying only with the low cyclic fatigue criteria are classified as Class L
High cycle fatigue testing is optional. 2M cycles at a stress range 2σa, of 60 Mpa and with an upper stress of 60% of the specified rebar yield stress are required without failure. Couplers complying with the high cyclic fatigue criteria are classified as Class H
4.2 Testing and Quality Control Requirements
As well as type testing, intended to prove the suitability and performance of a new type of coupler or a new manufacturing process, there are also acceptance tests to perform based on the quantity and number of types, or coupler produced in a single lot.
4.3 Strength and Ductility Discussion
IS 16172 gives no strength performance categories. Given that the actual ultimate tensile strength of IS 1786 rebar can vary dramatically, for example Fe 550D rebar has a minimum ultimate tensile strength of 600 Mpa, but the actual ultimate tensile strength can be considerably higher. This means that there can be a variety of tensile strength performance characteristics of rebar couplers approved for use, as the tensile requirement is that the coupler assembly only exceeds the minimum ultimate tensile rebar stress. If a higher tensile performance level/greater factor of safety is required, then a “bar break” coupler system should be specified, which requires a tensile failure to occur in the rebar away from the influence of connection or bar end processing. This failure mode and the importance of a higher performance coupler in “important structures” is recognised in IS 16172 clause 9.2.1 (2).
The percentage elongation at maximum force is the principal measure of ductility for IS 1786 compliant rebar, and it should be noted that if the rebar coupler system fails before the rebar, the rebar will not reach its maximum force and will therefore exhibit a reduction in ductility. The only way to maintain the full uniform plastic elongation of the whole rebar “system” is to have a “bar break” level of rebar coupler system performance.
About Author
Based in the UK and with a degree in Civil Engineering, the author has worked for Civil Engineering contractors, steel mills and manufacturers of construction products. With over 25 years of experience in the design of steel products for construction, Richard is a specialist in their design, manufacture, and use. Richard is currently the Technical Manager for Dextra having held the position for the past 7 years.
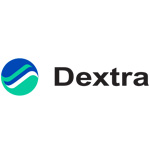
Dextra India
215 Atrium 2, Tower 2, Ground Floor, Unit no. 001, Andheri – Kurla Road, Hanuman Nagar, Andheri East 400059, Mumbai, India.
Phone: +91 22 2838 6294 ext 217 / +91 80 9746 1155
Email: bjog@dextragroup.com
Website: https://www.dextragroup.com/