‘Shotcrete’ is concrete conveyed through a hose and pneumatically projected at high velocity at the projected surface, as a construction technique. It is a sprayed concrete which is batched in a predetermined ratio of cement and aggregates and mixed with (or without) water. The shotcrete process was first used in Pennsylvania, USA in 1907 by Dr. Akeley.
Shotcrete undergoes placement and compaction at the same time due to the force with which it is projected with nozzle. It can be impacted onto any type or shape of surface, including vertical and overhead areas. This technology helps in completion of the construction task with a great economy in terms of both i.e. time and investments. Shotcrete technology is introduced to make the work immediate and easier, where any alterations may exist or any architectural effects have to be enhanced. Technical properties like compressive strength & elastic modulus of early age shotcrete shows an important influence on the safety of tunnel, lining of canals and building construction etc. during construction period.
Shotcrete is an excellent for stabilization and support of structure in a very short time and for concrete applications without using any moulds. Shotcrete or ‘Sprayed Concrete’ is the interaction of man, machine and concrete. In times of rapidly increasing mobility and limited space, the need for underground infrastructure continues to grow. In that case, shotcrete has an important role in order to get the requirements fulfilled. This article basically outlines the history of shotcrete and its basic principles, different testing methods, its advantages over ordinary concreting process and applications of shotcrete.
INTRODUCTION
The development of new technology in every field of construction engineering is increasing gradually. In the last three decades, lot of research was carried out throughout the globe in order to improve the performance of concrete in terms of strength and durability. In 1907, an American taxidermist Dr. Carl Akeley invented this technique to repair the crumbling façade of the field at Columbia museum in Chicago. He used the method of blowing dry material out of the hose with the help of compressed air and injecting water near the nozzle while the mix was released. After some experimentation, a single chamber pressure vessel developed which contains a mixture of cement and sand. The mixture pressurized with compressed air and forced through an opening along a delivery hose. At the end the hose was fitted with a nozzle and a water spray. In spite of the increasing importance of shotcrete, a complete guidance reference for the application of shotcrete, in which shotcrete is a primary support in different conditions, is not yet available. The support proposed by experiment classifications are also based on the databases in which a steel frame is dominated and suggested shotcrete thickness by them should be reconsidered. These factors made the analysis of tunnel stability in some common geotechnical conditions by numerical methods.
PRINCIPLES
The early machines placed the dry mix of coarse sand and cement into the pressurized chamber where the mix usually projected to the end nozzle where water is added just before spray of mix. Therefore this system is usually termed as “Dry process”. After some time and research, the process developed and a “true gun” method was also upgraded. This required the sand and cement mixture to be fully mixed with water before being pumped through a fundamentally different machine. Because of its different mixing the system became known as the “wet process” the wet process was not fully developed commercially until well into the 1970’s, much of its experimentation being carried out in the USA.
The two basic shotcrete processes are:
- Dry mix shotcrete
- Wet mix shotcrete
Dry Mix Shotcrete
As illustrated in fig.1, the dry shotcrete components, which conditionally are slightly pre-dampened to reduce dust, are fed into a hopper with continuous disturbance. Compressed air is introduced through a rotating barrel or feed bowl to convey the materials in a continuous stream through the hose pipe. Water is added to the mix at the end of nozzle.
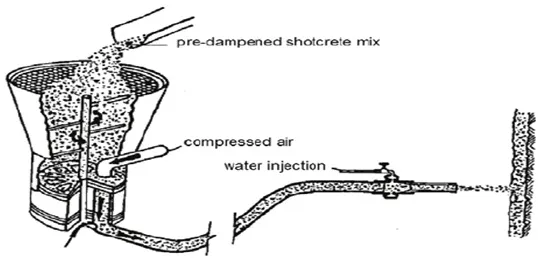
Wet Mix Shotcrete
In this case, shotcrete components and water are mixed (usually in a truck-mounted mixer) before delivery into a positive displacement pumping unit, which then delivery the mix hydraulically to the nozzle where air is added to project the material onto the rock surface (see fig. 2).
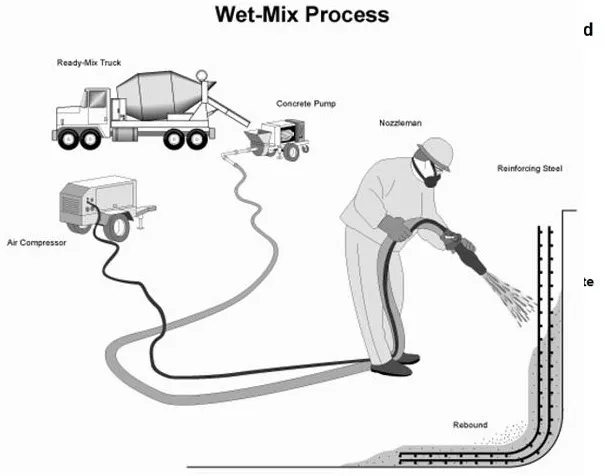
The final product of either the dry or wet shotcrete process is technically similar. The dry mix system tends to be more widely used in mining because of inaccessibility for large transit mix trucks and also because it generally uses smaller and more compacted equipment.
This can be moved around relatively through easy way in an underground mine environment. The wet mix process is ideal for high production applications in mining and civil engineering where a deep shaft or long tunnel is being driven and where access allows the application equipment and delivery trucks to operate on a quite continuous basis. Application of both is usually site dependent whether to use dry mix or wet mix shotcrete.
DIFFERENT TESTING METHODS
Tests at the execution site should be carried out on a regular basis on cores or other samples taken from sprayed concrete applied in the works. Tests may be repeated if the source or qualities of any of the materials or the mix proportions are likely to be changed during the course of the works.
Preconstruction Tests
The frequency of carrying out each test for mix control should be in accordance with the IS standards. Composition of the sprayed concrete is determined in the course of preconstruction tests in which the required properties are to be checked. Examples of properties to be checked are as follows:
- Fresh concrete:
- Water demand, workability, pump ability
- Spray ability/rebound.
- Slump, density.
- Accelerator dosage and compatibility with type.
- Hardened concrete:
- Compressive strength and density at 7 days and 28 days.
- Flexural strength.
- Residual strength.
- Bond permeability.
Compressive Strength Test
The compressive strength developed in shotcrete, i.e. up to 24- hour, is measured using the tests, namely penetrometer and Hilti stud. Both the tests are related and use the impact of the compressive strength as per the value of penetration reading of needle. Apart the recommendation as they are given by these methods statement or local regulations, one has to keep in mind that any general correlation function describing these impacts would be just an approximation. Thus, results from these methods depends on the mix design, i.e. on the used aggregates (0-8 mm), and would not necessarily result in absolute values of the compressive strength.
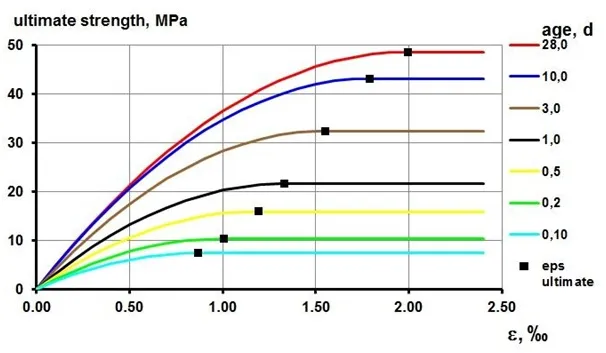
The following three tests are necessary for shotcreting process:
- Needle penetration
- Stud driving
- Coring
ADVANTAGES OF SHOTCRETE
Shotcreting process has some merits over normal concreting, which demonstrates that why this technique should be used in concrete construction which are discussed below:
- The sprayed concrete i.e. shotcreting can be applied easily in restricted areas at some distance from the access point. In this process concrete mix can be transported up to a long distance from the production site.
- The applied shotcrete is structurally strong and durable material, which is capable of getting an excellent bond with concrete, masonry, steel and other materials. The water cement ratio in shotcrete process normally varies from 0.35 to 0.5 by mass which is less than the other concrete. The reported compressive strength lies in the range of 20 to 50 N/mm2.
- Generally shotcrete has drying shrinkage value between 0.6 to 0.10%. Shotcrete has very good durability in laboratories and under field exposure.
- The most important thing is that shotcrete has advantages over other conventional concrete in a variety of new construction and in repair works.
APPLICATIONS OF SHOTCRETE
There are different fields, where shotcrete plays an important role and proves its good workability, compressive strength and bonding where ordinary concreting fails.
REPAIR
As shotcrete provides better surface finishing so it can be used for the repair of damaged concrete surface, wood, or steel. There are some examples which indicates the use of shotcrete in repair works:
- Bridges: Shotcrete is likely to be used for bridge deck rehabilitation, but it is very costly for full thickness repair. However it is useful for beam repairs of variable depths, caps, columns, abutments, wing walls, and under decks from the technical point of view.
- Buildings: Shotcrete is commonly used for the repairing of buildings for earthquake damage, fire and other deterioration, strengthening walls, and encasing structural steel for fireproofing.
- Marine: The most damages occur from deterioration of concrete and reinforcement in marine structures. The damages basically are the results of corrosion in steel, freezing and thawing action, abrasion, impact loading, structural distress, abrasion due to the action of waves, gravel, sand, and floating ice, and also from chemical attack in presence of sulphates. Shotcrete application generally used for short outage of these damages.
- Spillways: It seems likely that the surface of spillways is subjected to high velocity flows, which results in cavitation, erosion or abrasion.
UNDERGROUND EXCAVATIONS
In the most part, shotcrete process is generally used in underground excavation in rock, but occasionally, this process mostly used for the advancement of the tunnels through altered, cohesionless, and loose soils. Basically the underground shotcrete applications ranges from supplementing or replacing conventional support materials like lagging and steel sets, sealing rock surface, channelling water flows, and the installation of temporary support and lining works.
SLOPE AND SURFACE PROTECTION
Shotcrete is mostly used for temporary protection of exposed rock surfaces, which deteriorate in the exposed air location. Shotcrete may also be used for permanently covering slopes, or cuts that deteriorate in time span. Therefore shotcrete is beneficial to the surface of landfills and other waste areas to restrict the infiltration.
NEW SURFACE STRUCTURES
Shotcrete is not the fastest method for placing concrete on all jobs, but effectively it saves the time where thin sections and large areas exist.
- Pool and tanks.
- Shotcrete floors and walls.
- Shotcrete domes.
CONCLUSION
The use of Shotcrete to build new concrete structures as well as to restore and repair existing structures is well known and it is perhaps the most diverse method available for concrete construction. The use of this innovative technology is increasing day by day and procedures for its proper performance are well developed and high quality work is regularly obtained.
This technology may be expensive at some scale as compared to conventional concrete, but it is rather important to use recent technology, which is innovative in the field of engineering and proves to be efficient and quick.
About the author
The author is the Managing Director at Skanda Group of Constructions. He is an experienced Civil Engineer with a demonstrated history of working in the construction industry. He is skilled in AutoCAD, Construction, Management, Concrete, and Structural Analysis.