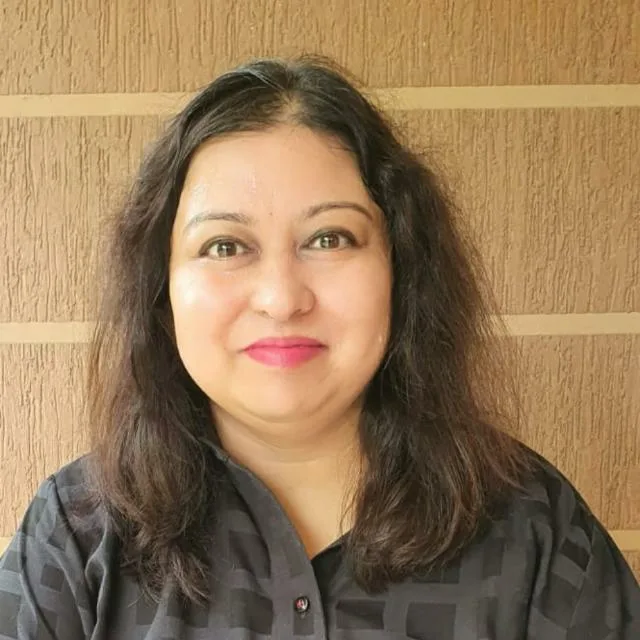
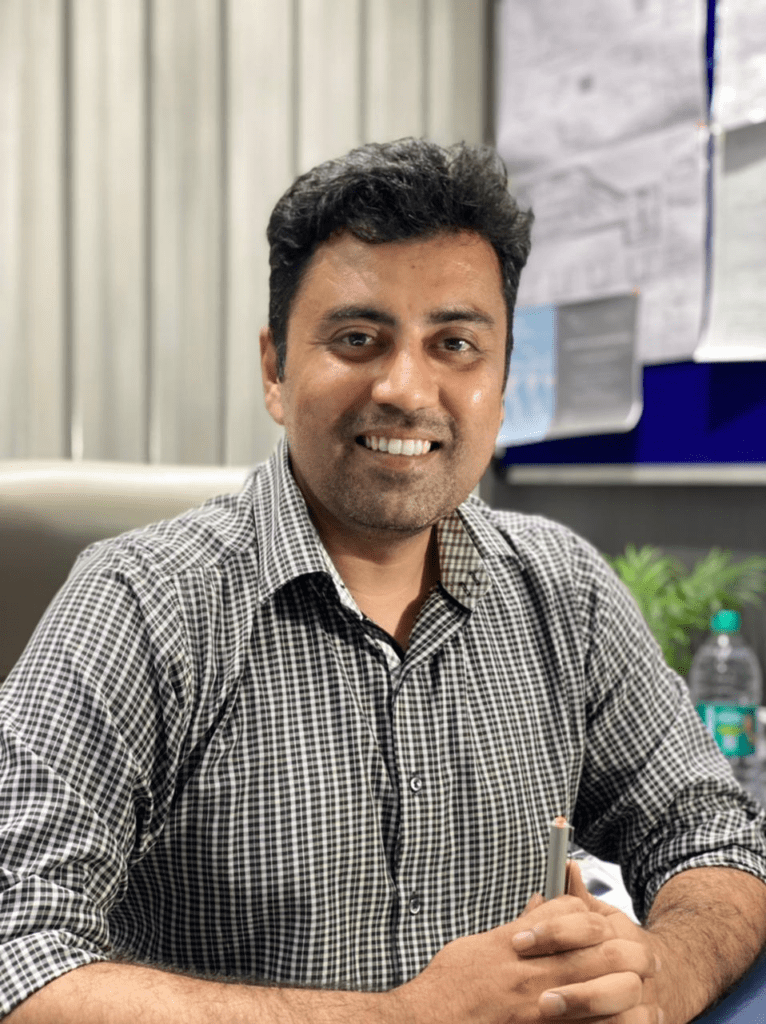
Overview:
The article emphasizes the numerous practical advantages of precast concrete box culvert technology compared to cast-in-situ methods for bridge construction, with accelerated project timelines being paramount. It analyses two challenging site projects as case studies to vividly illustrate the significant time savings achievable through precast construction methods.
Introduction:
Precast Concrete Technology that involves the manufacture of concrete components for bridges at a more favourable site or factory and transporting it to the site of construction. There are many benefits of using precast technology for bridge construction. These precast components for bridges may be box culverts, piles, piers or long span girders and decks. Be it minor bridges using box culverts or major bridges using long span girders, precast construction is known to have accelerated the construction project time greatly. This article discusses the inherent benefits of precast technology over cast in situ technology and briefly discusses two case studies that prove the acceleration of project time that can be achieved using precast box culvert bridges in challenging sites.
Benefits of Precast Technology in Bridges over Cast in situ Technology:
Precast Concrete Technology often uses high performance concrete where the concrete microstructure is refined to a nano level leading to higher strength, durability and crack resistance. When made in factory-controlled environment, the precast components can have better quality and durability characters as indicated by testing and inspection parameters.
The construction benefits are clearly seen in terms of less space requirement at site. This is because the main space requiring operation is unloading of precast component and the requirements of space for raw material storage, plant machinery storage, stockyard and labour colony are eliminated. The manpower requirement is also considerably reduced at site as the only manpower required is for the installation purpose. The nature of construction activities (mainly installation) is much easier, smarter and less laborious as compared to cast in situ operations. This also leads to safer operations as human labour activities like carrying of raw material are not required at bridge sites that are typically having work requirement at high heights, across water bodies and limited space for movement. On the same lines, quality checks and laboratory set ups required at such sites can be reduced/eliminated as these can be done majorly at factory where the precast components are manufactured in a safer and convenient workplace environment. Since the finished component is brought to site, the threat of moisture, water, winds etc on raw material mixing are eliminated and better weather resistance is ensured.
With advances in joinery technology, segmental bridge construction is made possible which was earlier monolithic concrete requirement for huge volumes in case of cast in situ. Earlier reinforcement spans were also very long for concrete pour for single span, which is difficult to handle. This also increased the need for repair and maintenance.
There are other sustainability benefits of precast construction in terms of life cycle perspectives, but all in all, the major benefits of this technology can be reaped where construction project time is critical or construction project site is critical.
Case Study 1: Installation of Box Culvert Bridges at Lakhpat, India-Pakistan Border
Site of bridge construction
FUJI Silvertech was assigned the task of providing the bridge solution for a site at Lakhpat, near Bhuj in Gujarat at the India-Pakistan Border.
This site is characterized by very poor soil bearing capacity (less than 1 T/m2), lack of accessibility, high water tables, highly saline and corrosive environment. For construction, there was no existing infrastructure for power supply, housing or sanitation and there was difficulty in transportation of material, manpower and equipment. This was a challenge for using cast in situ technology construction. Further, the construction project time had to be short because of local disputes coming from across the border and construction labour not willing to stay or work at this particular site. This bridge was achieved very fast with use of precast technology.
Efforts had been done by the client (CPWD) for ground improvement to raise the SBC to a higher value. FUJI Silvertech planned the precast infrastructure requirement by developing conceptual drawings and details drawings. The drawings and design were validated by the National Institute of Technology at Surat, Gujarat. Modeling and Analysis of the precast bridge was done using Finite element method. Thus, design precast components that consisted of walls and box culverts were manufactured at FUJI Silvertech’s precast factory at Bagodara, Ahmedabad and transported to site by truck. After this point the bridge infrastructure was installed in 10 days.
Precast Bridge Solution Construction Sequence
Figure 6: Complete precast bridge solution on Day 10
Achievement
Precast Technology enabled accelerated bridge construction at a strategic political site in 10 days’ time using precast box culverts, precast wing walls and precast parapet walls.
Case Study 2: Installation of Box Culvert Bridges at Himank, Leh-Ladakh region
Site of bridge construction
FUJI Silvertech was faced with another challenge when couple of bridges were to be constructed using precast box culverts segments at Leh-Ladakh region. The site was challenged with very cold temperatures, high terrain. The cold air made it impossible to pursue construction work before 12 noon and after 4 pm. Due to this achieving project times with cast in situ construction could not have possible. Further, due to the hilly terrain, raw material storage, movement of plant equipment to the high altitude etc and manpower availability was a huge challenge.
An enormous feat of providing and installing precast box culverts for 68 bridges was achieved in only 4 months’ time. This was a definite acceleration in construction that could be achieved due to the precast technology.
Figure 8: Construction of precast box culvert bridge
Achievement
A remarkable achievement of construction of 68 bridges in 4 months was achieved at a site of high altitude using Precast Technology.
Conclusion
There are many applications and benefits of precast technology in Bridge Construction. The acceleration in construction project duration is the biggest benefit achieved by this technology. At sites that offer challenges in terms of geographical, strategic or socio-environmental features, the precast technology can help achieve some remarkable construction timelines.
About authors:
Dr. Anal Sheth, is the Research and Development Head at FUJI Silvertech Concrete Pvt. Ltd. and is involved in development and maintenance of new age precast solutions and international accreditation. She is a structural engineering graduate from University of Illinois, Urbana Champaign with over 20 years of combined experience in academia and corporate sector.
Dr. Parth Thaker, is the Design Head at FUJI Silvertech Concrete Pvt. Ltd. and is involved in structural design and development of precast infrastructure solutions. He has to his credit, designed more than 300 precast box culvert bridges in a short duration of 4 years in his current profile. He is a structural engineering graduate of CEPT University, Ahmedabad and has over 17 years of combined experience in academia and practice.