Pipe jacking is a trenchless construction method used to install underground pipelines without the need for extensive excavation. Instead of digging open trenches, pipe jacking involves pushing or jacking prefabricated pipes through the ground from a launch shaft to a receiving shaft. This process is particularly useful in urban areas where space is limited, and disruption to surface infrastructure needs to be minimized. The importance of pipe jacking lies in its ability to reduce environmental impact, mitigate disruption to surface activities, and provide a cost-effective solution for installing underground pipelines. By avoiding the need for extensive excavation, pipe jacking helps preserve existing structures, roads, and landscapes. It also minimizes traffic disruptions and disturbance to local communities during construction.
An overview of the typical steps involved in pipe jacking:
1. Site Preparation: The construction site is prepared, including the setup of launch and receiving shafts. These shafts serve as entry and exit points for the pipe being installed underground.
2. Excavation: A small pilot tunnel is excavated from the launch shaft to the receiving shaft using specialised equipment such as a tunnel boring machine or microtunnelling machine. This creates a pathway for the pipe to be jacked through the ground.
3. Pipe Installation: Prefabricated pipe sections are assembled at the launch shaft. The first section of the pipe is then connected to the jacking equipment, which pushes or jacks the pipe through the pilot tunnel towards the receiving shaft.
4. Jacking: As the pipe advances through the ground, additional pipe sections are added at the rear. Hydraulic jacks or mechanical pushing systems are used to apply force to the pipe, driving it forward through the soil.
5. Spoil Removal: Excavated soil, known as spoil, is removed from the launch shaft using conveyor belts, slurry pumps, or other methods and transported to the surface for disposal or reuse.
6. Pipe Alignment and Grouting: Throughout the jacking process, careful monitoring ensures that the pipe remains aligned and on the correct trajectory. Grout may be injected around the pipe to stabilize the surrounding soil and prevent settlement.
7. Receiving Shaft: Once the pipe reaches the receiving shaft, it is guided into place and connected to the existing underground infrastructure. The shaft is then backfilled, and surface restoration work is carried out to restore the construction site to its original condition.
Applications of pipe jacking
1. Underground Utility Installations: Pipe jacking is extensively used for the installation of underground utilities such as water mains, sewer lines, stormwater drainage systems, and telecommunications conduits.
2. Road and Highway Crossings: Pipe jacking is employed for the construction of road and highway crossings, including culverts, underpasses, and pedestrian tunnels.
3. Bridge Foundations and Abutments: In bridge construction, pipe jacking can be utilized for the installation of pile foundations and abutments.
4. Railway and Transit Projects: Pipe jacking is applied in railway and transit projects for the installation of drainage systems, utility conduits, and culverts beneath rail lines and transit corridors.
5. Airport Infrastructure: Pipe jacking is employed in airport construction projects for the installation of drainage systems, fuel pipelines, and utility conduits beneath runways, taxiways, and terminal areas.
6. Tunnelling and Subway Construction: Pipe jacking can be used in tunnelling and subway construction projects for the installation of utility conduits, ventilation shafts, and emergency exits.
7. Building Foundations and Basements: In urban construction projects, pipe jacking can be utilized for the installation of building foundations, basement walls, and underground parking structures.
Advantages of pipe jacking
- Minimal surface disruption
- Environmental preservation
- Versatility in soil conditions
- Accommodation of existing infrastructure
- Enhanced safety
- Faster project completion
- Precision and accuracy
- Sustainable construction practices
- Reduced risk of utility strikes
- Minimized disturbance to wildlife
- Flexibility in project design
- Reduced noise and vibration during construction
- Enhanced public perception of projects
- Lower risk of soil contamination
- Opportunity for phased construction
- Potential for future expansion or rehabilitation without major disruptions
Different methods used for pipe jacking
Several methods are used for pipe jacking, each tailored to specific soil conditions, project requirements, and site constraints. Some of the commonly used methods include:
1. Microtunnelling: Microtunnelling involves the use of a microtunnel boring machine (MTBM) to excavate a small diameter tunnel ahead of the pipe. The pipe is then pushed or jacked into place behind the machine. This method is suitable for compact soils, rocky terrain, and urban areas with limited space.
2. Slurry Shield tunnelling: Slurry shield tunnelling utilizes a tunnel boring machine equipped with a slurry system to stabilize the tunnel face. The slurry acts as both a lubricant and a support medium, allowing for excavation in soft soils and preventing ground collapse. The pipe is installed behind the tunnel boring machine as it progresses.
3. Earth Pressure Balance tunnelling: Earth pressure balance tunnelling also employs a tunnel boring machine but utilizes excavated soil to balance the pressure exerted by the surrounding ground. This method is suitable for cohesive soils and minimizes settlement and ground disturbance during excavation.
4. Auger Boring: Auger boring involves the use of a rotating cutting head to excavate a pilot bore, followed by the installation of steel casing or pipe segments behind the auger. This method is suitable for stable soils and can accommodate larger diameter pipes and longer distances.
5. Guided Boring: Guided boring utilizes a guided boring machine (GBM) to create a pilot bore while maintaining alignment and grade accuracy. The machine is guided by a laser or optical system, allowing for precise installation of pipes beneath existing infrastructure such as roads, railways, and buildings.
6. Horizontal Directional Drilling (HDD): Horizontal directional drilling involves the use of a drilling rig to bore a pilot hole underground, followed by the installation of the pipe using a combination of drilling fluid and thrust force. This method is suitable for crossing obstacles such as rivers, highways, and environmentally sensitive areas.
Different equipments used for pipe jacking
1. Tunnel Boring Machines (TBMs):
Tunnel Boring Machines (TBMs) are sophisticated pieces of equipment designed to excavate tunnels for underground infrastructure projects, including pipe jacking. TBMs consist of a rotating cutting head that bores through various soil and rock types, along with a trailing support system for removing excavated material. They offer several advantages, including high excavation rates, reduced manual labor, and enhanced safety for workers. TBMs are particularly well-suited for large-diameter pipe jacking projects in challenging soil and geological conditions. Their ability to bore through hard rock formations makes them indispensable for tunnelling in urban areas and mountainous terrain. Additionally, TBMs can operate continuously, allowing for rapid progress and efficient project completion. Overall, TBMs offer a reliable and efficient solution for excavating tunnels and installing pipelines with minimal surface disruption.
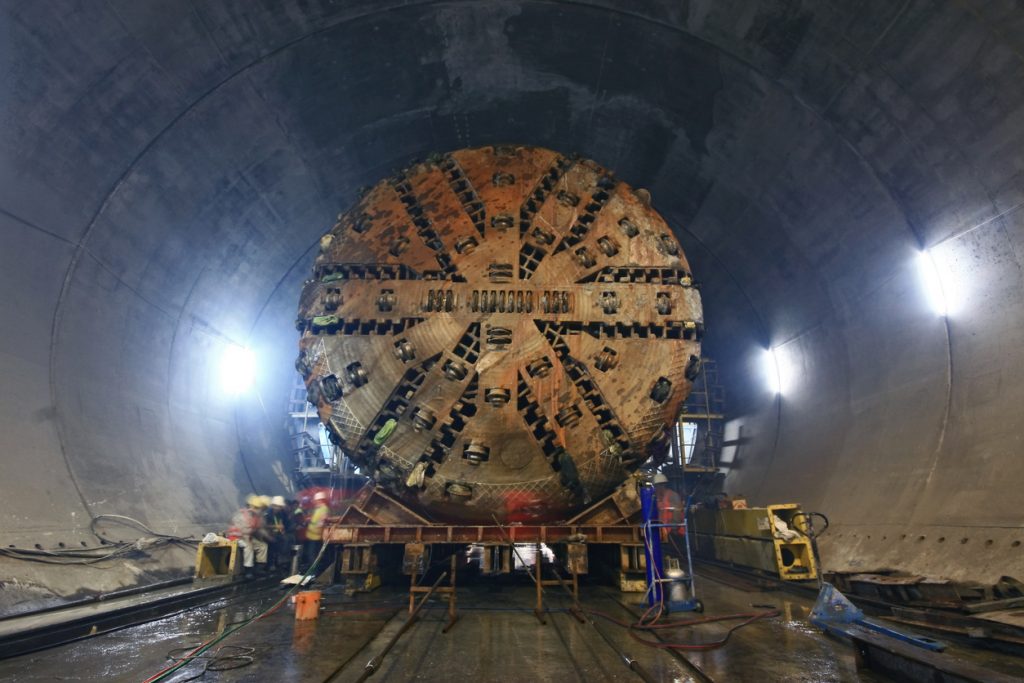
2. Microtunnel Boring Machines (MTBMs):
Microtunnel Boring Machines (MTBMs) are specialized equipment used for microtunneling projects where space is limited or smaller diameter pipes are being installed. MTBMs are similar to TBMs but are smaller in size and designed for precise excavation in confined spaces. They offer several advantages, including compact footprint, precise control, and minimal surface disruption. MTBMs are particularly useful for urban infrastructure projects, such as sewer and water main installations, where traditional open-cut methods are impractical. Their ability to operate in densely populated areas while minimizing disturbance to surface activities makes them highly desirable for sensitive environments. Additionally, MTBMs can be customised to accommodate various soil conditions and project requirements, making them versatile and adaptable for a wide range of applications.
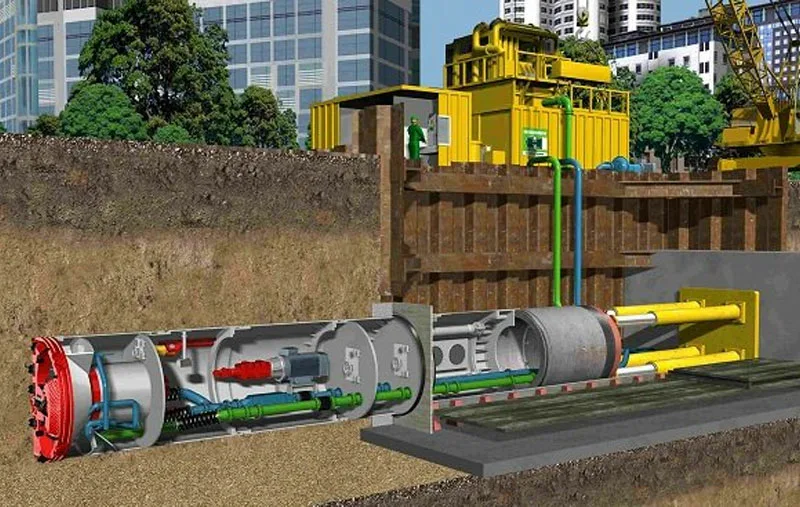
3. Auger Boring Machines:
Auger Boring Machines are heavy equipment used to excavate pilot bores for pipe installation in stable soil conditions. They consist of a rotating auger that drills into the ground and removes soil, along with a jacking system for advancing the pipe behind the auger. Auger Boring Machines offer several advantages, including simplicity, efficiency, and cost-effectiveness. They are well-suited for installing larger diameter pipes and longer distances compared to other trenchless methods. Auger Boring Machines are commonly used for utility installations beneath roads, railways, and other obstacles where surface disruption must be minimized. Their ability to operate in cohesive soils and granular materials makes them versatile and adaptable for various construction projects.
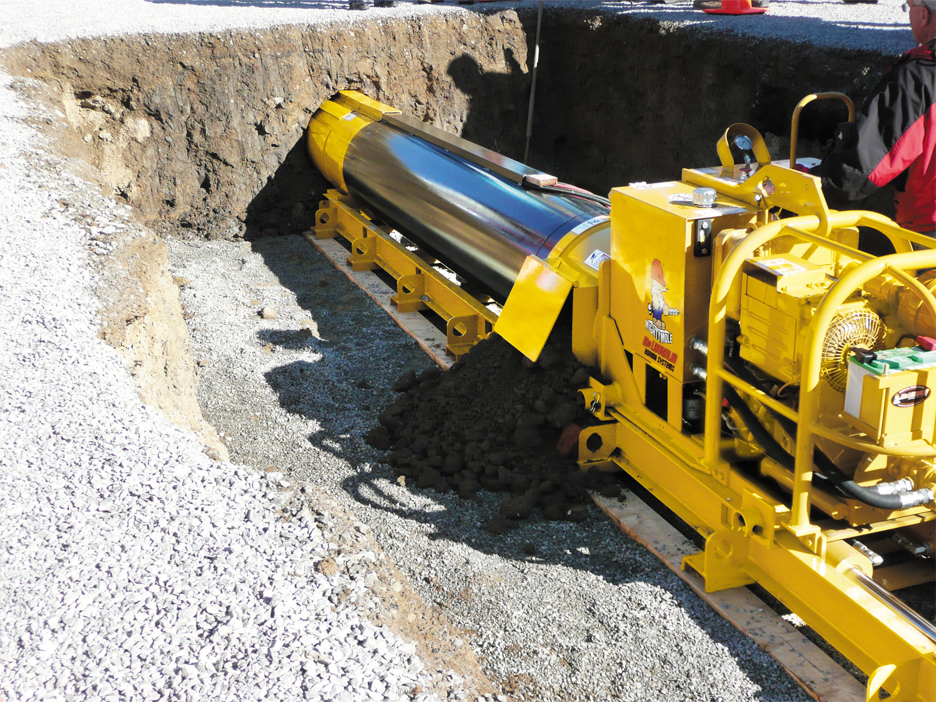
4. Guided Boring Machines (GBMs):
Guided Boring Machines (GBMs) are specialized equipment used for accurately steering and controlling the direction of pipe installations. GBMs utilize guidance systems such as lasers or optical instruments to maintain alignment and grade during the jacking process. They offer several advantages, including precision, accuracy, and versatility. GBMs are particularly useful for projects requiring high alignment tolerances, such as river crossings, highway crossings, and installations beneath buildings or utilities. Their ability to navigate complex underground environments while minimizing deviation from design specifications makes them invaluable for critical infrastructure projects. Additionally, GBMs can be customized to accommodate various pipe sizes and soil conditions, making them adaptable for a wide range of applications in the pipe jacking industry.
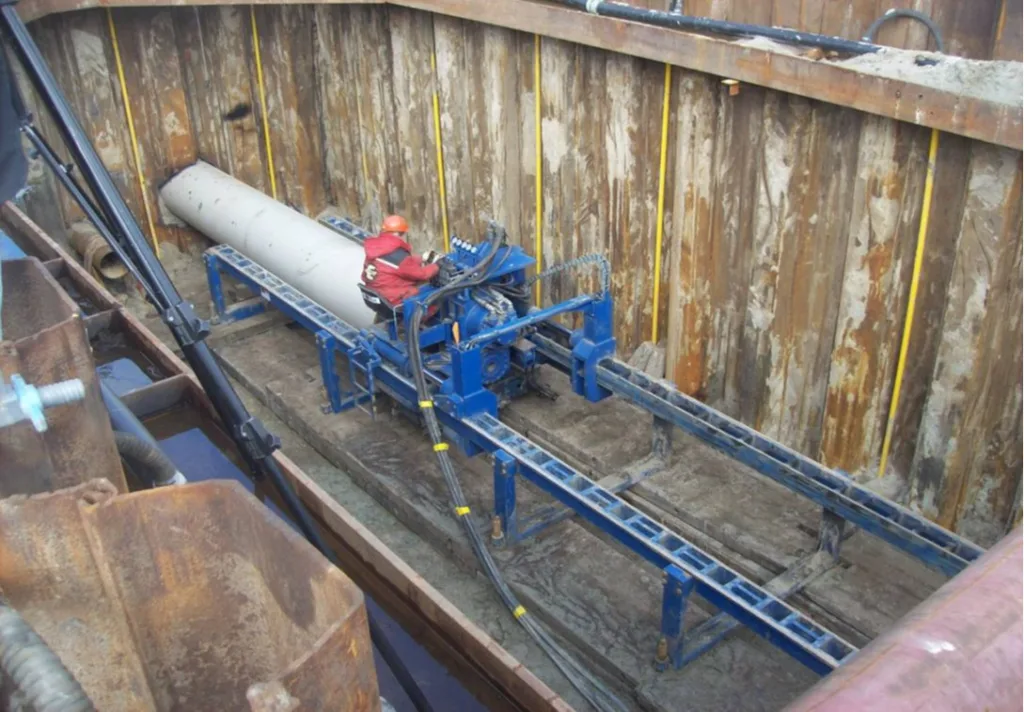
5. Hydraulic Jacking Systems:
Hydraulic Jacking Systems are essential for providing the force required to push or jack the pipe through the ground during pipe jacking operations. These systems typically consist of hydraulic cylinders, pumps, and control mechanisms. Hydraulic jacking systems offer several advantages, including high pushing force, precise control, and ease of operation. They are capable of exerting significant pressure to advance the pipe through various soil conditions while maintaining alignment and grade. Hydraulic jacking systems can be tailored to accommodate different pipe sizes and project requirements, making them versatile and adaptable for a wide range of applications. They are commonly used in conjunction with other heavy equipment, such as TBMs or auger boring machines, to facilitate efficient and controlled pipe installation.
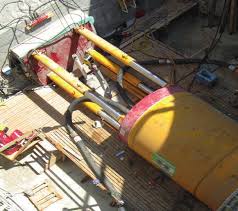
6. Pipe Handling Equipment:
Pipe Handling Equipment encompasses a range of machinery and tools used to handle and position pipe segments during pipe jacking operations. This equipment includes cranes, winches, hoists, and pipe slings designed to lift, manoeuvre, and place pipe sections into position. Pipe handling equipment offers several advantages, including increased efficiency, improved safety, and reduced manual labour. It allows for the safe and precise placement of pipe segments in the launch and receiving shafts, minimising the risk of damage or injury during installation. Additionally, pipe handling equipment can be customised to accommodate different pipe sizes, weights, and lengths, making it adaptable for various pipe jacking projects. By streamlining the pipe handling process, this equipment helps optimise workflow and ensure smooth project execution.

7. Spoil Removal Equipment:
Spoil Removal Equipment is essential for removing excavated soil, or spoils, from the excavation site during pipe jacking operations. This equipment includes conveyor belts, slurry pumps, muck cars, and vacuum trucks designed to transport spoils from the launch shaft to the surface for disposal or reuse. Spoil removal equipment offers several advantages, including increased efficiency, reduced manual labour, and improved safety. It allows for the continuous removal of spoils from the excavation site, preventing accumulation and congestion in the tunnel. Additionally, spoil removal equipment can be customised to accommodate different soil conditions and project requirements, making it adaptable for various pipe jacking projects. By ensuring the timely and efficient removal of spoils, this equipment helps maintain productivity and minimise downtime during construction.

Conclusion
PIpe jacking stands as a versatile and innovative trenchless construction method that streamlines the way underground infrastructure is installed. As technology continues to advance and infrastructure demands grow, pipe jacking is poised to play an increasingly vital role in shaping the future of construction and infrastructure development worldwide. With its ability to overcome challenges and deliver superior results, pipe jacking exemplifies the ingenuity and innovation driving the construction industry towards a brighter and more sustainable future.