The alkali-aggregate reaction (AAR) occurs when alkalis, typically sodium and potassium ions from cement, reacts with minerals present in aggregates within concrete.This reaction can lead to the formation of a gel, which can induce swelling and exert pressure on the concrete, ultimately resulting in the expansion and, in severe cases, the cracking of the structure. The detrimental consequences of this reaction become more pronounced over time, potentially compromising the structural integrity of the concrete.
Types of alkali-aggregate reaction in concrete
Alkali-Silica Reaction (ASR):
Alkali-Silica Reaction (ASR) is a prevalent form of alkali-aggregate that occurs when certain reactive forms of silica minerals present in aggregates, such as opal, chert, and strained quartz, react with the alkalis, namely sodium and potassium, in the cement. This chemical reaction leads to the formation of a gel-like substance within the concrete. As the gel absorbs water, it causes the concrete to expand, resulting in distinctive cracks and map-like patterns on the surface. ASR is particularly associated with fine aggregates and can pose a significant durability concern for concrete structures.
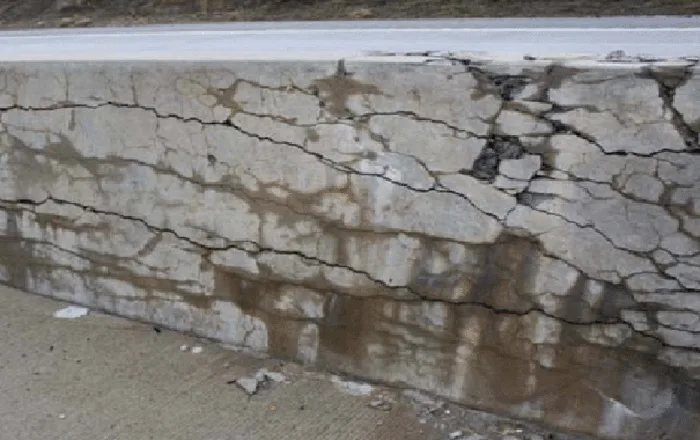
Alkali-Carbonate Reaction (ACR):
Alkali-Carbonate Reaction (ACR) is a type of alkali-aggregate reaction that occurs between alkalis present in the cement and carbonate minerals found in specific aggregates. Common reactive carbonate minerals include dolomite and certain types of limestone. Unlike ASR, ACR typically does not produce a gel; instead, the reaction products lead to the expansion of the concrete. Over time, this expansion can result in cracking and structural damage. Although ACR is less common than ASR, it remains a consideration in regions where reactive carbonate aggregates are used in concrete construction.
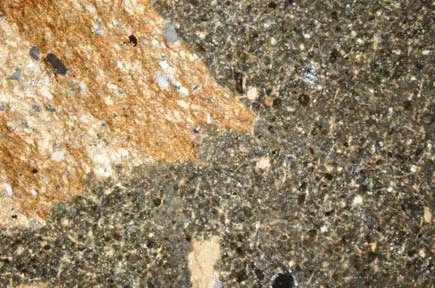
Where does alkali-aggregate reaction occur?
- Buildings
- Bridges
- Dams and Water Retaining Structures
- Highway Pavements
- Tunnels
- Hydropower Plants
- Ports and Harbors etc.
Causes of alkali-aggregate reaction in concrete
High Alkali Content in Cement: Excessive alkali levels, particularly sodium and potassium, increase the likelihood of alkali-aggregate reaction (AAR) in concrete.
Reactive Minerals in Aggregates: Aggregates containing reactive minerals, such as certain forms of silica or carbonate, can undergo chemical reactions with alkalis, contributing to AAR.
Moisture Availability: Moisture enables the chemical reactions between alkalis in cement and reactive minerals in aggregates, causing expansive gel formation.
Elevated Temperatures: Higher temperatures can accelerate AAR, potentially intensifying the expansion and deterioration of the concrete over time.
Inadequate Concrete Mix Design: Poorly designed concrete mixes, lacking consideration for aggregate reactivity and other mitigating factors, can contribute to the development of alkali-aggregate reactions in the structure.
Impacts of alkali-aggregate reaction in concrete
The impact of alkali-aggregate reaction (AAR) on concrete can be detrimental to the durability and structural integrity of the affected structures. Some key effects include:
1. Cracking: AAR induces the formation of cracks in the concrete, compromising its structural integrity. These cracks can vary in size and pattern, such as map cracking, and may lead to water infiltration and further deterioration.
2. Reduced Durability: The expansive nature of AAR can result in surface scaling, spalling, and loss of bond between the cement paste and aggregates. This diminishes the durability of the concrete and accelerates its deterioration over time.
3. Loss of Load-Bearing Capacity: The formation of cracks and weakening of the concrete can reduce its load-bearing capacity, potentially jeopardizing the structural stability of the affected elements.
4. Surface Disintegration: AAR can cause the concrete surface to disintegrate, leading to a loss of the protective cover and exposing the reinforcing steel to potential corrosion.
5. Efflorescence: The reaction products from AAR can lead to the formation of efflorescence on the concrete surface, affecting its aesthetic appearance and indicating ongoing internal damage.
6. Structural Distress: Over time, the cumulative effects of AAR can result in significant structural distress, requiring costly repairs or, in extreme cases, the replacement of affected concrete elements.
7. Crushed or Fractured Aggregates: The aggregates within the concrete may show signs of crushing or fracturing due to the expansion and pressure generated by the AAR.
8. Map Cracking on Exposed Surfaces: AAR-induced map cracking might be particularly visible on exposed surfaces, such as bridges or pavements, where the concrete is subjected to environmental conditions that facilitate the reaction.
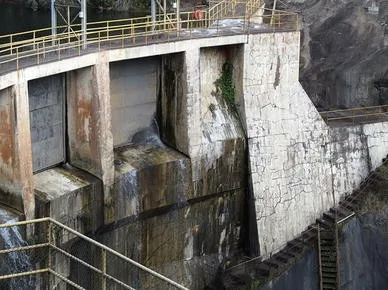
How to avoid an alkali-aggregate reaction in concrete?
To avoid alkali-aggregate reaction in concrete certain prevention steps can be taken which construction buildings and structures
- Use low-alkali cement.
- Test aggregates for reactive minerals.
- Consider blended cements (fly ash, slag).
- Control water-cement ratio.
- Utilize chemical admixtures for AAR control.
- Incorporate air-entraining agents.
- Avoid reactive aggregates.
- Use pozzolanic materials in the mix.
- Opt for lithium-based admixtures for AAR prevention.
- Consider using high-performance concrete with low permeability.
- Ensure proper curing practices to reduce susceptibility to AAR.
- Implement preventive measures during construction to minimize exposure to moisture.
- Choose aggregates with known performance history in AAR-prone environments.
- Incorporate supplementary cementitious materials like silica fume.
- Consider the use of corrosion-inhibiting admixtures to protect reinforcing steel from potential damage.
How to repair alkali-aggregate reactions in concrete?
If any of the prevention step is not mentioned above is not maintained and alkali-aggregate reactions occurs, you can repair it by following the steps mentioned below;
1. Assessment: Conduct a thorough assessment to identify the extent of the AAR damage. Determine the affected areas and the severity of deterioration.
2. Remove Damaged Concrete: Excavate and remove the damaged concrete, ensuring that all affected portions are eliminated. This may involve cutting and breaking out the deteriorated material.
3. Clean the Surface: Clean the exposed surface to remove any loose particles, contaminants, or residues that could hinder the bond between the existing concrete and the repair material.
4. Apply Bonding Agent: Apply a bonding agent to the prepared surface. This helps enhance the adhesion between the existing concrete and the repair material.
5. Mix Repair Material: Prepare the repair material according to the manufacturer’s instructions. This may involve mixing specific proportions of cement, aggregates, and any additional additives or admixtures recommended for AAR repair.
6. Place Repair Material: Carefully place the repair material into the excavated area, ensuring good compaction and a smooth finish. Follow the specified thickness and application guidelines.
7. Cure the Repair: Properly cure the repair material to promote hydration and achieve optimal strength. This may involve applying curing compounds, wet curing, or covering the repaired area with wet burlap and plastic sheets.
8. Apply Protective Coating (Optional): Depending on the severity and exposure conditions, consider applying a protective coating to the repaired surface to enhance durability and resist further alkali ingress.
9. Documentation: Keep detailed records of the repair process and maintain a record of ongoing inspections and maintenance activities to ensure the long-term integrity of the structure.
Always follow industry standards, guidelines, and the recommendations of material manufacturers for the specific repair products used. Consulting with structural engineers and professionals experienced in AAR repair is advisable for complex cases.
Conclusion
Alkali-Aggregate Reaction (AAR) poses a significant challenge to the durability of concrete structures. Early detection, proper mix design, and use of mitigating measures are crucial in preventing AAR-induced damage. Continued research and industry awareness are essential for developing effective strategies to mitigate the impact of AAR on concrete structures and ensure the long-term sustainability of construction projects.