Automatic doors play a role in enhancing operational efficiency and safety within manufacturing facilities. By automating entry and exit points, these doors facilitate seamless movement of personnel, equipment, and materials, reducing downtime and streamlining workflows. Their ability to maintain a controlled environment by minimizing air exchange ensures adherence to specific environmental conditions critical for manufacturing processes. Equipped with sensors, automatic doors enhance safety by preventing collisions and facilitating swift evacuations during emergencies. The integration of these doors into automated systems allows for synchronized workflows, contributing to overall process efficiency.
Advantages of using automatic doors for manufacturing facilities
1. Efficient Material Flow:
– Automatic doors facilitate smooth and uninterrupted movement of materials and goods in and out of manufacturing areas. This helps optimize the overall production process by reducing bottlenecks and delays.
2. Improved Productivity:
– Quick and automated access allows employees to move freely without interruptions, saving time and increasing overall productivity. This is especially beneficial in environments where timely production is critical.
3. Controlled Environment:
– Automatic doors contribute to maintaining a controlled environment within manufacturing spaces. They minimize the exchange of air between different zones, helping to regulate temperature, humidity, and prevent dust or contaminants from entering sensitive production areas.
4. Energy Efficiency:
– These doors are designed with energy efficiency in mind. They minimize air exchange, which is crucial for facilities that require specific environmental conditions. This helps in reducing energy consumption and operational costs.
5. Safety Measures:
– Automatic doors enhance safety in manufacturing facilities. They can be equipped with sensors to detect the presence of people or objects, preventing collisions and accidents. In emergency situations, such as fires, they can facilitate swift and organized evacuations.
6. Adaptability to Workflows:
– These doors can be integrated into automated systems, allowing seamless coordination with other manufacturing processes. They can be synchronized with production cycles, ensuring that access points are open or closed as needed during different phases of manufacturing.
7. Space Optimization:
– Traditional swinging doors require additional space for clearance, which might not be practical in manufacturing layouts where space utilization is crucial. Automatic doors, with their sliding or folding designs, optimize the use of available space.
8. Enhanced Security:
– Automatic doors often come with secure locking systems, enhancing the overall security of the manufacturing facility. Access control mechanisms can be integrated, restricting entry to authorized personnel only.

Different types of automatic doors used for different manufacturing facilities
1. Sliding Doors:
Sliding doors are commonly employed in manufacturing facilities, warehouses, and production areas where large and frequent access is required. These doors operate by sliding horizontally along a track, making them space-efficient and facilitating quick and convenient entry or exit. Their suitability for wide openings and robust design makes them ideal for industrial settings where the efficient movement of materials and personnel is crucial.
2. Rolling Doors:
Rolling doors find application in areas with limited ceiling space, such as factories and storage facilities. Comprising horizontal slats that roll up into a coil, these doors are versatile and customizable for various sizes and materials. Their design allows for efficient use of space, making them practical for environments where maximizing available room height is essential. Additionally, rolling doors are known for their durability and ease of maintenance, contributing to their popularity in industrial settings.
3. High-Speed Doors:
High-speed doors are designed for specific manufacturing environments that require rapid opening and closing. Commonly used in cleanrooms, temperature-sensitive areas, and manufacturing plants, these doors minimize air exchange, contributing to energy efficiency and climate control. The quick operation of high-speed doors enhances workflow efficiency and helps maintain the desired conditions within the facility, making them a valuable asset in modern industrial settings.
4. Folding Doors:
Folding doors are a space-saving solution for manufacturing facilities with limited lateral space. These doors consist of panels that fold as the door opens, allowing for efficient use of available space. This design makes folding doors suitable for applications where swinging doors might be impractical. The versatility and customization options of folding doors make them adaptable to diverse industrial environments seeking practical and space-efficient door solutions.
5. Sectional Doors:
Sectional doors, composed of horizontal panels that slide vertically, are commonly utilized in loading docks, warehouses, and manufacturing facilities. The vertical movement of the panels allows for smooth operation even in spaces with limited headroom. Sectional doors provide a balance between insulation, security, and practicality, making them a reliable choice for various industrial applications where ease of use and functionality are paramount.
6. Air Curtains:
While not physical doors, air curtains are significant in maintaining climate control at entrances to manufacturing facilities. Acting as invisible barriers, air curtains reduce energy loss by minimizing the exchange of indoor and outdoor air. This technology is crucial in environments where maintaining a specific temperature or preventing contaminants from entering the facility is essential, contributing to energy efficiency and overall operational effectiveness.
7. Revolving Doors:
Revolving doors are commonly found at entrances to manufacturing facilities and office areas. Their rotating design minimizes the influx of outside air when people enter or exit, contributing to temperature control and energy efficiency. Apart from their practical benefits, revolving doors also have an aesthetic appeal and can enhance the overall image of a facility, making them a popular choice for entrances where a combination of functionality and visual impact is desired.
8. Bi-Fold Doors:
Bi-fold doors, with two panels that fold in the center as the door opens, are well-suited for applications requiring wide openings. This design allows for efficient use of space and makes bi-fold doors practical for hangars, large storage areas, and manufacturing plants. The versatility and adaptability of bi-fold doors make them a valuable asset in industrial settings where accommodating large machinery or materials is a regular requirement.
9. Sensor-Activated Doors:
Sensor-activated doors are equipped with sensors to detect movement or approach, providing a hands-free solution for manufacturing facilities, particularly those with hygiene concerns. Commonly used in cleanrooms and areas where minimizing physical contact is crucial, these doors enhance convenience and reduce the risk of contamination. The seamless and automated operation of sensor-activated doors aligns with modern industrial practices focused on efficiency and hygiene.
10. Hermetic Sealing Doors:
Hermetic sealing doors play a critical role in environments where maintaining an airtight seal is paramount, such as cleanroom environments and pharmaceutical manufacturing facilities. These doors prevent the infiltration of contaminants and maintain controlled conditions within the enclosed space. The hermetic sealing capability ensures the integrity of the controlled environment, making these doors essential for industries where even minimal contamination can have significant consequences.
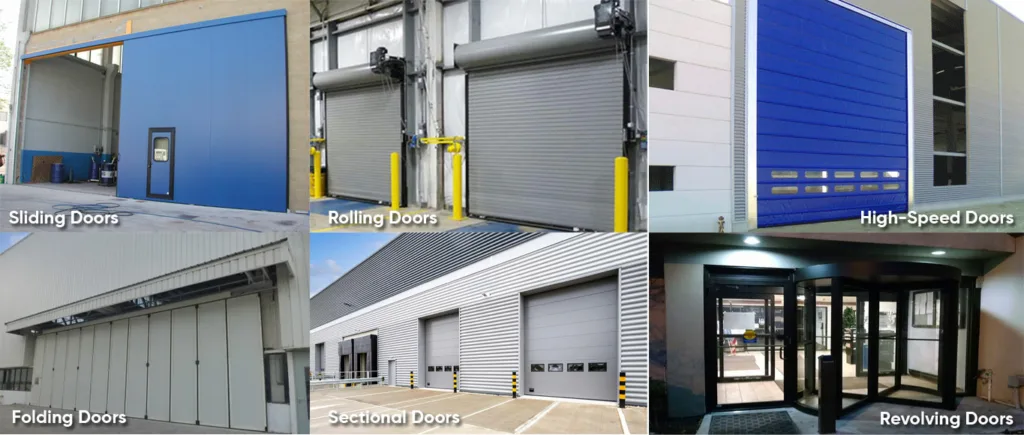
Factors to consider when selecting automatic doors for manufacturing facilities
When selecting automatic doors for manufacturing facilities, consider the following key requirements:
1. Traffic Flow Analysis: Assess the volume and patterns of foot and equipment traffic to determine the appropriate door type and size. High-traffic areas may benefit from rapid-opening doors.
2. Safety Features: Prioritize doors with advanced safety features, such as motion sensors, obstacle detection, and emergency stop functionalities. These features enhance worker safety and prevent accidents.
3. Durability and Build Quality: Manufacturing environments can be harsh. Choose doors constructed from robust materials capable of withstanding the conditions of your facility, including temperature variations, dust, and potential impacts.
4. Speed and Efficiency: Opt for doors that open and close quickly to minimize downtime. High-speed doors can improve overall operational efficiency in busy manufacturing settings.
5. Environmental Control: Consider the need for temperature or environmental control within your facility. Some automatic doors offer better insulation, helping to maintain specific conditions in different areas.
6. Integration with Existing Systems: Ensure compatibility with other systems in your facility, such as access control, security, or automation systems. Integration can enhance overall operational efficiency.
7. Compliance with Regulations: Verify that the selected doors comply with relevant safety and industry regulations. This is crucial for avoiding legal issues and ensuring a safe working environment.
8. Maintenance Requirements: Assess the maintenance needs of the automatic doors. Choose doors that are easy to maintain, and consider the availability of local service and support.
9. Customization Options: Select doors that can be customized to fit the specific requirements of your manufacturing facility. This includes size, design, and additional features.
10. Cost Considerations: Evaluate the initial costs as well as long-term operational costs. While investing in quality doors may have a higher upfront cost, it can lead to cost savings over time through increased efficiency and reduced maintenance needs.
By carefully considering these requirements, you can choose automatic doors that align with the unique needs and conditions of your manufacturing facility.
Conclusion
The adoption of automatic doors in manufacturing facilities represents a pivotal step towards efficiency, safety, and compliance. The seamless integration of these intelligent entry and exit points not only streamlines operations but also fosters a secure and controlled environment. As technology continues to evolve, the role of automatic doors becomes increasingly vital in meeting the demands of modern manufacturing. From optimizing workflow to enhancing safety protocols, the investment in these automated solutions is a strategic move that pays dividends in productivity, employee well-being, and overall operational excellence. As manufacturing processes advance, the ubiquitous presence of automatic doors stands as a testament to the industry’s commitment to innovation and the pursuit of optimal working environments.