Pneumatic tyred rollers, also known as rubber-tired rollers or pneumatic rollers, are heavy construction machines used for road compaction. They are equipped with multiple rubber tyres on both the front and rear axles, which can be adjusted to control the level of compaction. The flexibility of the rubber tires and their ability to adjust air pressure allows these rollers to effectively compact various materials like soil, asphalt, or aggregates. These rollers are commonly used to achieve smooth and even surfaces on roads by applying pressure evenly across the surface during compaction.
Why are pneumatic tyred rollers required ?
1. Adaptability: Pneumatic tyred rollers can adjust their tire pressure to suit different types of materials, making them versatile for a wide range of compaction tasks, including soil, asphalt, and aggregates.
2. Compaction Control: The ability to fine-tune tire pressure allows for precise control over compaction density, ensuring that construction projects meet specific technical requirements and standards.
3. Even Pressure Distribution: Pneumatic tyred rollers distribute compaction pressure evenly across the surface, reducing the risk of over-compaction or under-compaction, which can be crucial for achieving uniform and durable road surfaces.
4. Speed and Efficiency: These rollers can cover a larger area in less time compared to some other compaction equipment, increasing efficiency on construction sites.
5. High Tractive Force: The rubber tires provide excellent tractive force, allowing the roller to work effectively on steep grades and challenging terrains.
6. Reduced Surface Damage: The flexible rubber tires minimize surface damage and scuffing, which is essential for achieving high-quality finishes on asphalt and other delicate materials.
7. Consistent Compaction: These rollers can maintain consistent compaction density over large areas, which is vital for the long-term durability of roads and pavements.
Different types of pneumatic tyred rollers
Pneumatic Tyred Rollers with Hydrodynamic Propulsion System:
The latest models of pneumatic tyred rollers now incorporate a hydrodynamic propulsion system. These rollers use hydro-motors to control propulsion energy, allowing for electronic adjustment of traction force, which enhances fuel efficiency. They provide a smooth start and stop, making them ideal for demanding terrain. These rollers excel in kneading and sealing on job sites, improving productivity on rough surfaces. They can work on both aggregates and asphalt, offering air pressure adjustment for flexibility. The spacious cab and user-friendly controls make them easy for operators to handle. These rollers have gained popularity for their effectiveness with stiffer mixes, as they enable better static penetration into materials. The weight and tire air pressure can be adjusted to meet specific job requirements.
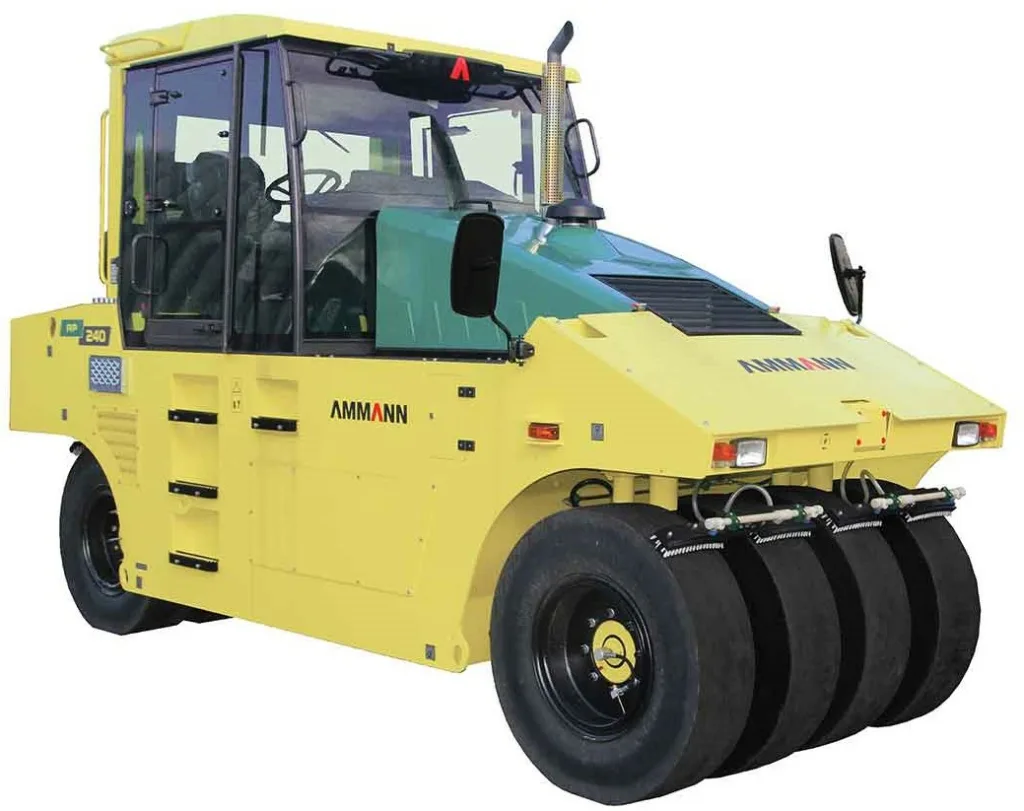
Pneumatic Tyred Rollers with Roll-Over Protective Structure:
Modern pneumatic rollers come equipped with safety features like a Roll-Over Protective Structure (ROPS). This system is designed to protect equipment operators in case of rollovers, with bars attached to the frame to create a protective space for the operator. The operator benefits from an integrated sunshade, dual seating options, and a sliding console for comfort and visibility. The newer model uses mass and manipulation forces for compaction and can adapt to various applications through ballast adjustments and tire inflation pressure changes. The positioning of four front and rear tires ensures even surface coverage, while front tire suspension maintains stability on uneven terrain and uniform tire contact pressure.
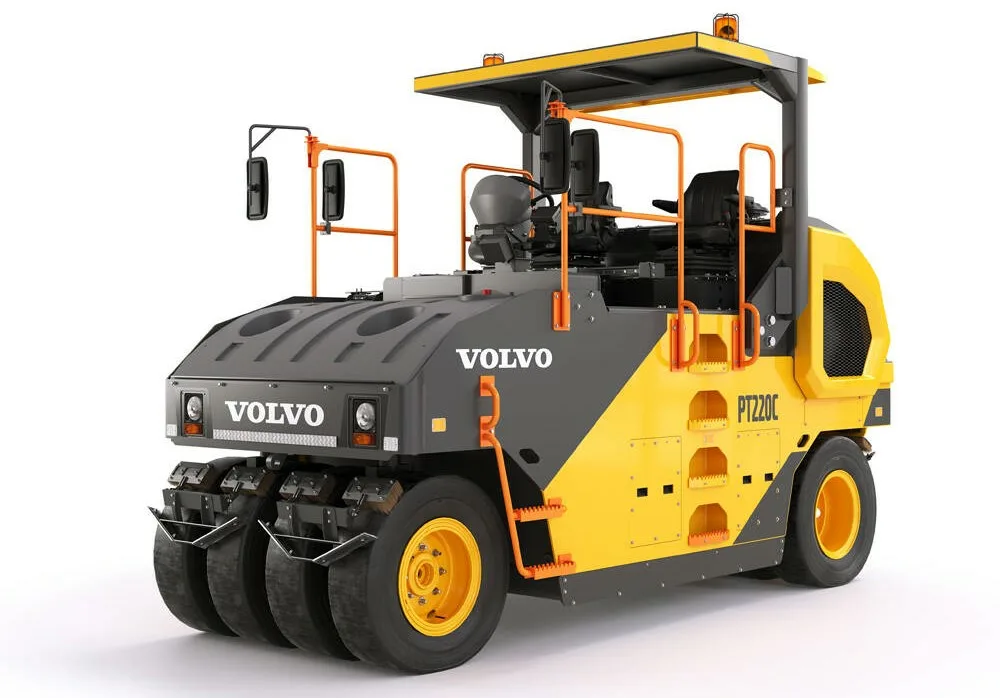
Pneumatic Tyre Roller with Optional Temperature Sensor:
Pneumatic tyred rollers come with optional temperature sensors to achieve optimal soil surface density. They can even adjust tire pressure during compaction with an air-on-the-run system. These rollers are specially designed for compacting bases, sub-bases, and asphalt mixes on various job sites. They feature an isostatic front axle that allows front tires to oscillate, ensuring constant ground contact and maximizing compaction. Additionally, a standard automatic central tire inflation system maintains consistent pressure across all tires, facilitating easy pressure adjustments to suit ground conditions and compaction needs.

Pneumatic Tyred Rollers with Closed Hydraulic Drive System:
Pneumatic tyred rollers incorporate a closed hydraulic drive system consisting of an electro-hydraulic proportional variable displacement pump and motor. This system enhances drive performance and gradeability with two infinitely variable speed gears, ensuring optimized working speeds in various conditions. The electronic levers provide soft start and parking performance. The design with access holes and overturned cover boards facilitates maintenance and component care. These models are suitable for compacting asphalt pavement, foundation layers, secondary foundation layers, dams, and industrial construction sites. The dual-circuit brake technology offers a higher brake effect, fast response, and reliability, making them ideal for mountainous areas.
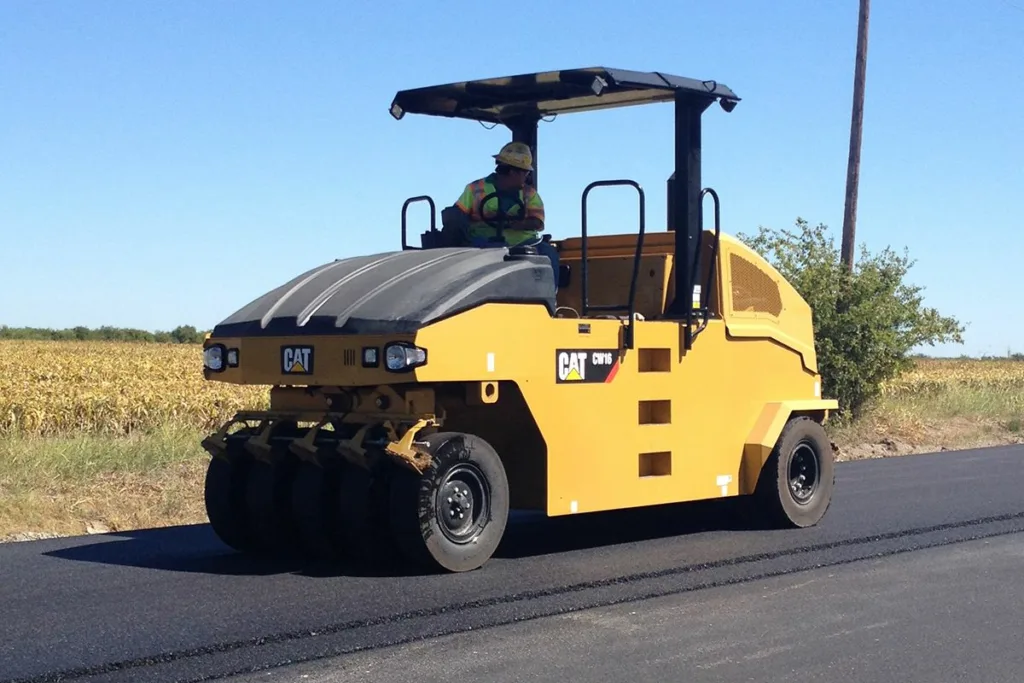
Pneumatic Tyred Rollers with Better Compaction Width:
The pneumatic tyred rollers are purpose-built for compacting bases, sub-bases, and asphalt mixes in various construction projects. They feature either seven or nine wheels, including three or five steered oscillating front wheels and four traction rear wheels, ensuring exceptional maneuverability. With an operating mass of 6000 kg, these rollers are valuable for achieving optimal compaction results. They offer wide base tires, an air-on-the-run option, and a backup sprinkler to enhance quality. The dual-circuit braking system ensures full braking capacity even if one circuit is compromised. The optional temperature sensor and unique analyzer help achieve the ideal density and surface texture while providing detailed statistics and documentation.
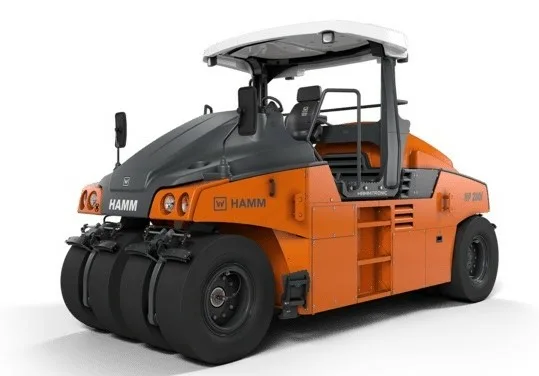
Pneumatic Tyred Rollers with Three-Point Articulation System:
The new generation of pneumatic-tyre rollers features a three-point articulation system that enhances driving and steering characteristics, making them well-suited for various construction sites, especially in earthworks and asphalt sectors. This articulation system ensures comfortable driving, safe steering, and high directional stability, even at high speeds. It optimizes traction when navigating curves, reduces impact loads on the driver, offers a wide steering angle, and prevents imprints on asphalt, ensuring even weight distribution across the rear axle. These models offer impressive compaction performance, intuitive language-neutral operation, and easy maintenance and servicing. Their powerful hydrostatic rear-axle drive and intelligent control system allow for precise speed adjustment, even on slopes. Various options, including thermal aprons and an innovative additive-sprinkling system.
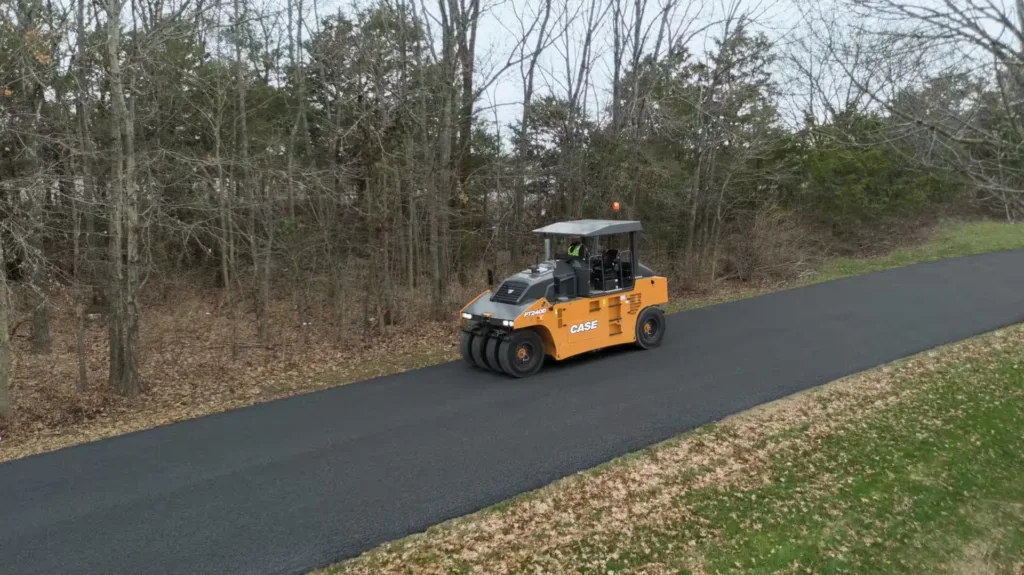
Conclusion
Pneumatic tyred rollers have undergone significant evolution, resulting in a diverse array of features and capabilities that effectively address the requirements of road construction. Their ability to adjust tire pressure, provide uniform compaction, and minimize surface damage makes them a preferred choice for achieving high-quality road construction. With ongoing technological and design advancements, these rollers persist in playing a vital role in improving the efficiency and longevity of road construction projects.
Image Source: ammann.com/cn-en/, volvoce.com/india/en-in/, lntcmb.com, cat.com, wirtgen-group.com/en-in/, casece.com