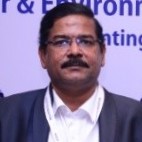
Consultant – Technical, Project Management & Business Development
Rheology is the study of flow and deformation of materials under applied forces which is routinely measured using various methods.
Rheology (Greek: rheos = flow or streaming, logos = word/science) is the study of deformation and flow of substances. Flow is the continuous deformation of a material under the influence of external forces. Various rheological measuring methods can be used to characterize coatings.
The quantities measured in rheological investigations are forces, deflections and velocities. Viscosity is the resistance of a liquid to forced, irreversible change of position of its volume elements.
Energy must be supplied continuously to maintain the flow of a liquid. Viscosity, the most frequently used rheological parameter, is calculated from the shear rate and the shear stress. Basic rheological parameters are explained in terms of the two-plate model (fig.).

The upper plate of area A is movable and the lower plate stationary. The plates are separated by a distance h which is filled with liquid. When a certain force F is applied the upper plate reaches a velocity v which is related to the shear stress.
The two characteristic values, shear stress, τ , and shear rate, Y, can be derived from the two-plate model. The shear stress has the dimensions of pressure and is defined as the shear force F [N] per shear area A [m²] where the force is parallel to the surface. The unit is the Pascal (Pa) which is the same as N/m2.

The shear rate (Y) or velocity gradient is obtained from the velocity v [m/s] and the plate separation h [m]. The units are second-1.

Although the term viscosity is often used in connection with coatings, the term flow behavior would surely be better. Usually coatings show a flow behavior in which they become thinner, that is to say, the viscosity value drops under the influence of shear forces. This phenomenon, known as pseudoplasticity, will be dealt with in more detail later.
Applicational properties of coatings are associated with different shear rates (fig). When stirring (dispersing), low viscosities are necessary but storage should preferably take place at high viscosity so that the pigments are prevented from settling out. For spray application, the paint should have as low a viscosity as possible but as soon as the paint is on the surface it should assume a high viscosity to prevent sagging on vertical substrates. The flow behavior of paints under typical processing conditions can be ordered according to shear rate.

Viscosity describes the frictional forces in a system and thus the resistance of a liquid to flow. The viscosity is a measure of the viscous flow of a liquid. The larger the viscosity, the less flowable the liquid. The (shear) viscosity (dynamic viscosity) is obtained as the ratio of shear stress (T) to shear rate (Y). The units are Pa · s-1.

If the viscosity of a substance is constant at different shear rates, it is said to exhibit ideal or Newtonian behavior. Newtonian flow is generally found only with low molecular weight liquids such as water, solvents and mineral oils. In practice, most shearable systems have flow properties which depend on the shear rate.
If the viscosity decreases with increasing shear stress, the flow behavior is said to be intrinsically viscous, shear thinning or pseudoplastic. Most coatings and polymer solutions show pseudoplastic behavior.
Bingham fluids are viscoplastic but their flow properties are linear. After a minimum shear stress, they reach the yield point, Tf, and begin to flow. Below this point they behave as an elastic body. Examples are ketchup and certain wall paints. These liquids only begin to flow when a particular stress is reached. This occurs, for example, if a loaded paint roller is pressed against a wall and rolled. At that moment, the shear force is sufficient for the paint to become liquid and wet the wall. As long as the paint is on the roller without any force applied it behaves like an elastic solid and does not drip from the roller.


a) Newtonian behavior
b) pseudoplastic (non-Newtonian) behavior
c) Bingham behavior with yield point Tf
d) Thixotropic behavior
Materials whose viscosity increases with increasing shear stress are thixotropic or dilatant. Thixotropic behavior is shown by, for example, dispersions with high solids content or high polymer concentrations. Thixotropic behavior is not usually found in paints and coatings as it can lead to problems with processes involving pumping or stirring.
Flow behavior can be shown diagrammatically in two ways: as a flow curve or a viscosity curve. A flow curve shows the dependence of shear force (T) on shear rate (Y) (fig.) and a viscosity curve shows how the viscosity depends on the shear rate (fig.).
Rheological additives can be roughly separated into inorganic and organic thickeners or thickeners for solventborne or waterborne coatings.
Examples of modified inorganic thickeners for solventborne and waterborne systems include:
- bentonite
- synthetic lattice-layer silicate
- pyrogenic silica (sometimes organically modified)
Examples of organic thickeners for solventborne or waterborne systems include:
- polyureas
- cellulose derivatives
- polyamides
Examples of organic thickeners for waterborne coatings include:
- associative thickeners
- non-associative thickeners
This list is not intended to be comprehensive.
Associative thickening involves non-specific interactions of hydrophobic end-groups of a thickener molecule both with themselves and with components of the coating. The thickener produces a reversible, dynamic network of thickener molecules and other components of the coating. The thickening effect is caused by interactions of the hydrophobic end groups of the thickener with other components of the formulation.
Non-associative thickening is thickening by an entanglement of water-soluble, high molecular weight polymer chains. The effectiveness of a thickener is mainly determined by the molecular weight of the polymer. Formulations thickened nonassociatively have pseudoplastic rheology with highly elastic properties. This produces good stabilization against settling out and low sagging even with high build coatings. Non-associatively thickened systems often have limited flowability. The high molecular weight of the thickeners can sometimes lead to compatibility problems such as depletion flocculation
Associative thickening can produce rheology ranging from Newtonian to pseudoplastic. Associative thickeners are often used to adjust application properties such as spattering or brushing resistance. Formulations with associative thickeners often exhibit high gloss and good leveling.
Associative thickeners also consist of hydrophilic water-soluble or water-emulsifiable polymer components and can simultaneously act in a non-associative manner. Both thickening modes are exhibited by associative thickeners, albeit to different extents. Table shows thickeners commonly used for waterborne coatings and the way in which the thickening is produced.

HEUR: Hydrophobically modified Ethylenoxide Urethane Rheology modifier
HASE: Hydrophobically modified Alkali Swellable Emulsion
HMPE: Hydrophobically Modified PolyEther
HMHEC: Hydrophobically Modified Hydroxy Ethyl Cellulose
Polyurethane thickeners belong to the associative category. The molecular weight of polyurethane thickeners is from one to several powers of 10 lower than that of non-associative thickeners. Nonassociative thickening can therefore be ignored.
Chemistry of polyurethane thickeners
Polyurethane thickeners are water-soluble or water-emulsifiable polymers with a segmented structure. The middle section consists of one or more hydrophilic segments while the end-groups are hydrophobic. Linking of the middle segments with each other and with the end-roups occurs mainly via free hydroxyl groups of the segments with monoor poly-isocyanates forming the urethane structures which give their name to this class of products. The molecular weights of typical polyurethane thickeners lie between 15,000 and 100,000 g/mol.
Polyurethane chemistry opens up many possibilities for synthesizing thickeners with differing property profiles.
This can be achieved by, for example, varying:
- the type of hydrophobic end group
- the molecular weight of the thickener
- the hydrophilic character of the middle section by the choice of isocyanate and the molecular weight of the polyethylene glycol
- the middle section with hydrophobic dialcohols
- the branching of the thickener molecule by reaction with polyisocyanates or polyalcohols
- the branching of the middle section by reaction with alkyl epoxides during manufacture of the polyethylene glycol
Further variations are possible during the formulation of the thickener as a waterborne preparation. Substances high in hydrophobic components require emulsifiers or solvents as formulation aids. The structure of the emulsifier co-determines the applicational properties of the thickener. A suitable choice of emulsifier allows the property profile of the thickener to be adjusted.
Mode of action of polyurethane thickeners
The associative thickening action of polyurethane thickeners can be explained as follows: interactions of the thickener molecules with each other and with the surface of dispersion and pigment particles produce a network (fig.).
Although the simplified model in fig. is helpful in explaining associative thickening clearly, the actual mechanisms of thickening by polyurethane thickeners are more complex.

Mode of action of polyurethane thickeners
Investigations on solutions of polyurethane thickeners in water show that the thickener molecules are present in mono-molecular form only in highly diluted solutions. With increasing concentration, the thickener molecules associate with each other to form loop micelles. The block-like structure of the thickener favors this phenomenon: the hydrophobic components of the molecule orient towards the interior of the micelle, the hydrophobic middle segments form the outer loop-shaped sheath.
At even higher concentrations, mutual interaction of the loop micelles results in two phase systems consisting of a freeflowing phase with low thickener content and a thickener gel. In the free flowing phase, the thickener molecules are dissolved individually or are present as loop micelles. The thickener gel consists of associates of thickener molecules. The cohesion of the gels is thought to stem from bridging and entanglement mechanisms by the micelles (figs).


If the concentration of thickener in aqueous solution is raised still further, the two phase system changes into a single phase thickener gel.
In paints, polyurethane thickeners are usually used at concentrations at which two-phase systems have been observed in aqueous solutions. It is therefore probable that the polyurethane thickener is also present in paints as a two-phase system. The thickener gel interacts via the hydrophobic groups with the surfaces of the pigments and binders. A refined model of the mechanism of associative thickening by polyurethane thickeners is shown in fig.
Polyurethane thickeners form a temporary network. The linkage points of the network consist of thickener molecules and thickener micelles adsorbed on the pigment or binder surfaces. It is characteristic that the linkage points of the network are constantly breaking and reforming. The system is thus highly fluid which explains the good flow and leveling characteristics of associatively-thickened paints.

The strength of the network and the resultant rheological properties of the system can be controlled via the hydrophobicity of the end groups. Long hydrophobic end groups exert strong interactions and ensure efficient thickening. To achieve comparable thickening with shorter end groups, significantly higher concentrations are required.
The length of the hydrophobic group influences not only the strength of the associative effect but also the kinetics of exchange and thus the rate at which the associative linkage points break and reform. When shear stress is applied to paints, the associative linkage points are broken. If the thickener is unable to reestablish the disrupted linkage points immediately, the associative network is weakened. There is then a shear-ratedependent loss in viscosity.
Long hydrophobic end groups possess a slow rate of exchange; i.e. the viscosity of thickeners with long hydrophobic end groups diminishes slowly under shear stress. The formulation becomes pseudoplastic. Short hydrophobic end groups exhibit a fast rate of exchange so that thickeners with such groups are effective even at high shear rates and result in formulations with Newtonian rheology.
Measuring viscosity with the relative viscometer
The volume of the sample is unknown; shear rate and shear stress cannot be quantified. Relative viscometers are suitable for comparative measurements of systems with similar rheology. In the coatings industry, relative viscometers of the Brookfield or Stormer spindle type are commonly used, usually at constant shear force.
Leveling
Leveling, the flow behavior in a horizontal position, is determined with a leveling doctor blade. In this method, the coating is applied as five double lines with increasing film thickness from 100 to 1000 μm on a Leneta sheet. The proportion of lines which have coalesced is quoted according to a scale of 0 (no leveling) to 10 (very good leveling). It is also common practice to visually compare a dried paint film with a standard (fig.). The paint is usually applied in a manner resembling subsequent application conditions.

Test methods
Measuring viscosity with the absolute viscometer
In absolute viscometers, the geometry of the measuring cell is known and the shear surface and plate separation are therefore also known. The shear stress, shear rate, and thus the viscosity can be calculated from the shear force and speed. The absolute viscometer is usually used to take measurements over a range of shear rates. The results are presented in flow curves or viscosity curves. Typical absolute viscometers are cone and plate or two-plate rotational viscometers (fig).

Sagging
Sagging, the flow behavior in a vertical position, is determined with a sagging doctor blade. Ten stripes of the paint are applied using the doctor blade in thicknesses of 75 to 300 μm on a Leneta sheet. Immediately after application, the card is lifted into a vertical position so that the stripes lie parallel to the horizontal. The stripes with the lowest film thickness are at the top. After drying, the stripe at which the paint starts to sag is given on a scale of 0 to 10: 0 meaning that all stripes sagged and 10 meaning that no stripes sagged (fig).

Alternatively, it is possible to determine at which film thickness sagging starts to occur by applying the paint, in various thicknesses or as a wedge, to a vertical surface.
Brushing resistance
Brushing resistance is determined by applying a specified amount of paint to a test surface and assessing the resistance felt on distributing the paint with a brush.
Spattering characteristics
The spattering characteristics can be determined by applying a specified amount of paint uniformly on a previously conditioned roller and rolled several times over a grid. The paint spray thrown from the roller is collected on a black card under the grid. The test card is compared with a standard tested at the same time.
These test methods are shown in a video on our Homepage entitled “Various methods for measuring viscosity”.
Selection methods
At this point, to select what type of thickener need to use. Start to see which type of thickener and the different shear level required. These methods of incorporation are extremely important as the higher the shear, the more potential foaming issues may have to be addressed. Figure below illustrates four specific attributes that the viscosity of the product addresses.
In the above example, the direct relationship that paint rheology has on specific attributes. The thickener selection and chemistry type determine the shear rate needed to incorporate into the paint.
After choosing the ingredient for viscosity build, levelling and sagging directly affect the final paint’s performance.
With the newest paint and coating formulations reducing volatile organic compounds (VOC), waterborne paint formulations have become extremely complex. Older versions of many coatings contained a mere five to seven ingredients and were loaded with glycol ethers. That is no longer the case, with zero-VOC paints flooding the market. Chemists must ensure that EVERY ingredient is VOC-free. So today, the chemical manufacturers have modernized additives to meet these requirements.

The choice of additives, such as wetting aids, dispersing aids, and the products that address sagging and viscosity consistency, will affect that overall formulation.
Now, let’s discuss what additives are available and how they affect these flows. Most people refer to these as associative thickeners.
Rheology modifiers
Rheology modifiers that thicken by volume exclusion include cellulosic ethers and alkali soluble (or swellable) emulsions (ASE). Cellulosic ethers are nonionic, water soluble polymers derived from natural fibers. They thicken by absorbing water and creating chain entanglement and flocculation.
There are basically three types that are commonly used in waterborne paints to control overall viscosity and flow. They are:
- ASE = Alkali swellable emulsions
- HASE = Hydrophobically modified ASE
- HEUR = Hydrophobically modified ethoxylated urethane resins
Thickener selection affects many things with the paint, such as adequate covering power, good film build, brush-ability and viscosity. Then flow, sag and leveling are also affected. Even paint splatter resistance can be controlled with the correct thickener!
As an example, in medium and high PVC paints, the HEUR thickeners also improve water resistance and even wet scrub resistance in the final paint.
Associative and non-associative thickeners
The viscosity stability during colorant addition, there are some cases where the use of a combination of both associative and non-associative thickeners help tailor the needs of the rheological profile for the best performance.
The “associative thickening involves non-specific interactions of hydrophobic end groups of a thickener molecule both with themselves and with components of the coating. The thickener produces a reversible, dynamic network of thickener molecules and other components of the coating. The thickening effect is caused by interactions of the hydrophobic end groups of the thickener with other components of the formulation.”3
The non-associative thickening as “thickening by an entanglement of water-soluble, high molecular weight polymer chains. The effectiveness of a thickener is mainly determined by the molecular weight of the polymer. Formulations thickened non-associatively have pseudo-plastic rheology with highly elastic properties. This produces good stabilization against settling out and low sagging even with high build coatings.”3
Surfactants are normally used in waterborne paints for different effects to the coating. These can affect the efficiency of thickeners as well, look at this possibility.
Adding universal colorants to paint can also disrupt and contribute to a lower viscosity due to the normal glycol ethers that are used in these products.
Recent Advances in Waterborne Coatings Technology
An overview of technological advances enabling superior performance in the architectural segment versus historical technologies. In subsequent articles, we’ll expand on these topics, as well as provide an overview and details of emergent waterborne coatings technologies that are closing the gap in the high performance industrial coatings market versus solvent-borne and solvent-less systems.
Many of the technological advances that exist today are the result of increasingly stringent regulations. Volatile Organic Compound (VOC) regulations automatically come to mind first, but there are several others. The elimination of the use of alkylphenol ethoxylates (APE’s) led to new classes of surfactants developed by many.
With the emergence of nanomaterials for applications spanning abrasion resistance, UV-protection, antimicrobial protection and thermal and electrical conductivity, there is a cautious concern that we may not have enough information to deem all of these materials as “safe.” Bioaccumulation and non-degradability add to this concern.

Technological advances have been made in the development of coalescing solvents for waterborne resins that meet the new regulations. Some of these have boiling points that exceed the test protocol and, therefore, are not volatile. Some approaches include the use of reactive diluents or materials made from plant products (“green chemistry”). Plasticizers, such as most phthalates and n-methyl pyrollidone (NMP), have been replaced with much less toxic materials.
In the preceding years, there has been a preponderance of advancements in waterborne resin technologies. In the past few years, they have been very large. Examples of large advancements include core-shell technology, latent crosslinking, 1K technologies that perform similar to 2K, resins with easy-clean properties, resins based on green chemistries, as well as many others. Fluoropolymers, which were once used only in OEM coil coatings, have made their way into other segments of the industrial market, and have some uses in architectural exterior coatings that can tolerate cost weatherability. Fluoroadditives for slip and block resistance, as well as mar reduction, have been in production for years. The resins will be discussed in more detail in future articles.
Although not as many advances have been made in pigment technology for the architectural coatings market, there still have been some significant ones. Infrared (IR) reflective pigments mitigate heat, providing as much as 25-30°F reduction in heat vs. conventional pigments in similarly painted structures.
There are new colored pigments that are more colorfast not only in masstones but in pastels. Surface chemistry has improved the weatherability characteristics of TiO2 and inorganic nanomaterials are highly synergistic to organic UV-absorbers and hindered amine light stabilizers (HALS) in exterior semi-transparent stains and varnishes.
In this general category are colorants. Many paint companies have eliminated ready-mix colors in favor of all colors prepared via custom mixing in the store. Therefore colorants had to be reformulated to be VOC-free, in addition to being compatible in both waterborne and solventborne paints and in all types of finishes. This was a particularly difficult challenge due to the high levels of glycols, among other things.
There are a multitude of new additives, including the UVA/HALS mentioned previously. Due to the changing waterborne resin chemistries as well as VOC regulations, additive suppliers have been busy creating chemistries that work as universally as possible.
Defoamers are a good example of a real challenge. Traditional defoamers might include mineral oil or a hydrocarbon carrier with hydrophobic silica and perhaps a fatty amide. They worked well for flat paints, but negatively affected gloss levels in semito high-gloss paints and could have a significant impact on the overall VOC level of a finished paint. All things have to be considered in the formulation of a zero-VOC paint.
At about the same time new defoamers were introduced to the waterborne flexographic ink market, there was a need for similar chemistry for different reasons in coatings. Analogs of the flexo defoamers are found in the waterborne architectural market, along with others.
Formulating Waterborne Coatings: a Checklist
This technology has soared for virtually every surface imaginable. Most people think of house types of latex paint when one thinks of water-based products. And although that is still a very large market, other resin technology has allowed for water products to be applied to things like baseball bats, automobiles, trains, planes and most places in between.
The initial concern when products started going to water formulations: is this as durable as the solvent counterpart? The adage was that when adhesion was questionable, use solvent. We threw that one out the window! With the new polymer developments, newer additives development, and regulations that favor the water product over solvent, welcome to the world of waterborne/water-based products.
This list is always dependent on several factors, so let’s walk through the necessary steps to properly formulate these products. To use a checklist and find out:
- what exactly the product will be
- how it will be used
- what inherent traits it needs to have
This may sound basic, but to those who are just starting out, or even seasoned professional formulators, it is a very necessary step.
What are formulating?
Product | Example |
Paint | simple interior wall paint |
Coating | industrial application |
Ink | printing ink |
Adhesive | floor tile adhesive |
Floor polish | high volume discount store vinyl tile |
Carpet backing | OEM application |
Fabric application | silk screen pretreatment |
What technology?
Material | Example |
Solvent | Clear lacquer |
Water | Clear waterborne lacquer |
100% solids | UV curable for hardwood floors |
What surface(s)?
Surface | Examples |
Wood | cabinets, furniture, house trim, moldings |
Metal | shelving, water towers, railcars, pipe fittings |
Concrete | flooring, highways, bridges, oil rigs, buildings |
Plastic | cell phones, cars, boats |
Fabric | clothing, signs, trade show booths |
Paper | self-adhesives, sheen control, wrapping |
What traits?
Once these determined, some simple but necessary questions to start to round out the first series of items.
Traits | Considerations |
Interior or exterior | Huge factor in resin selection |
VOC targets | Environmental concerns or regulations |
Film forming or non-film forming | Secondary concern for most formulators |
Clear or colors | normally medium factor for resin selection |
High gloss or different sheens | types of matting agents’ clarity |
Thermoplastic or thermoset | large factor for overall finished product |
What properties?
Next comes the starting qualities of the products are formulating. Again simple, but necessary. if the product should incorporate:
- Adhesion qualities
- Chemical resistance
- UV resistance
- Elongation factors
What application methods?
If the method of end user application will have any bearing on product development. They may use:
- Brush
- Rollers
- Airless Sprayers
- Conventional Spray
- Curtain Coating
- Roll Coating
- Automatic Spray
- Dipping
- Robotics
About the author;
The author has more than three decades of experience in multi-disciplinary transactions ranging from industrial projects to real estate development projects. Expertise in planning, undertaking demand assessment studies, transaction services, project execution, business development, etc. including marketing strategies based on technical market analysis, feasibility studies, program requirement derivation and fund and investor sourcing.
Almost 7 years experienced senior professional with project & construction management expertise in large projects for IT, Commercial, Industrial, residential sectors, etc. and more than 18 years of heavy engineering industrial projects like Fertilizers, Oil & Gas, Petrochemicals, etc.