Batch mix asphalt plants are the most widespread types of asphalt plants used to create hot mix asphalt. The compenent of a asphalt batch mix plant will include heating and weighing of aggregates, heating and weighing of bitumen, weighing of filler material and in the end mixing aggregates, bitumen and filler material to produce hot mix asphalt. The percentage of each item can vary depending on the mix material recipe set in the control panel. Working of a asphalt batch plant will include heating and weighing of aggregates, heating and weighing of bitumen, weighing of filler material and in the end mixing aggregates, bitumen and filler material to produce hot mix asphalt. The percentage of each item can vary depending on the mix material recipe set in the control panel.
The newer models comes with counter flow technology continuous drum mix plants are setting new standards for asphalt mix production. The prime benefits of the plant are fuel efficiency, low carbon footprint, environment protection and facility to add RAP. It mixes aggregates and bitumen to create the hot mix paving material. The aggregates here can be a single-sized material or can be a blend of various grades/sizes of materials. These plants are used in different applications, such as road construction, parking lots, airport construction etc. Asphalt mixing plants are a combination of electronic and mechanical machinery, where asphalt is produced as a hot mixture.
Manufacturers of asphalt batch mix plants are bringing a series of advanced features in their products that will lower their operating costs and yield higher productivity. They are incorporating newer product ranges to cater to the demand for longer stretches of road projects and making provision for the use of recycled and waste materials in their plants. The initiatives are taken for the technological modification of products based on specialised technologies. There are different types of asphalt batch mix plant models available in India.
Types of asphalt batch mix plants
Asphalt batch mix plant with geared motors that reduce fuel and minimise maintenance costs
The latest Asphalt batch mix plant provides the consistency that is crucial to your mix quality. All plant processes and components are carefully developed to ensure that feeding, heating, drying, screening and mixing seamlessly blend. The plant utilises multiple coupled geared motors that reduce fuel and minimise maintenance costs. The plant can be easily modified to use 25% recycled asphalt, enabling customers to adjust mixes to a specified RAP design. Optional insulation enhances dryer efficiency and reduces fuel consumption. Silo pockets can utilise optional temperature probes. The plant comes with multiple coupled geared motors eliminating the need for a linkage mechanism, thereby limiting parts and maintenance costs. Wear parts are durable and easy to maintain and replace. Central lubrication points simplify mixer maintenance. The distribution deck protects mesh and dispenses material to avoid screen overload and damage. The plant is also easy to pack and load. Fast setup times mean a quick return to production upon arrival.
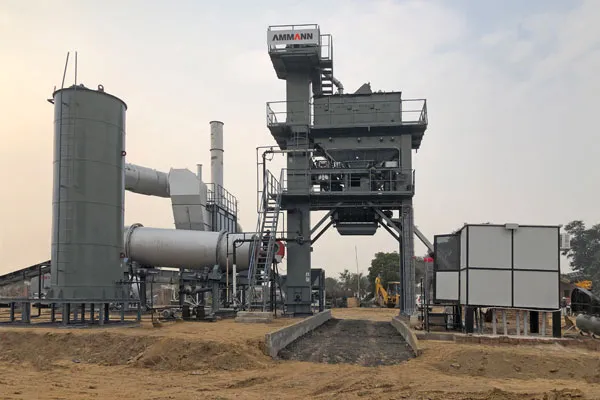
Asphalt batch mix plant with RAP system
There are now standard models with, Reclaimed Asphalt Pavement (RAP) system. Recycling asphalt pavement creates a cycle of reusing materials that optimises the use of natural resources. Reclaimed asphalt pavement (RAP) is a useful alternative to virgin materials because it reduces the need to use virgin aggregate, which is a scarce commodity in some areas of the United States. It also reduces the amount of costly new asphalt binder required in the production of asphalt paving mixtures. With increased demand and limited aggregate and binder supply, hot mix asphalt (HMA) producers discovered that reclaimed asphalt pavement (RAP) is a valuable component in HMA. As a result, there has been renewed interest in increasing the amount of RAP used in HMA. While several factors drive the use of RAP in asphalt pavements, the two primary factors are economic savings and environmental benefits. RAP is a useful alternative to virgin materials because it reduces the use of virgin aggregate and the amount of virgin asphalt binder required in the production of HMA. There are options now for cold RAP systems, for which manufacturers have added an extra bin in the hot bin system, in case the client would like to use the RAP system in the future. RAP can be added three ways – into the drier drum, into the mixer and preheated in a parallel RAP drier drum.
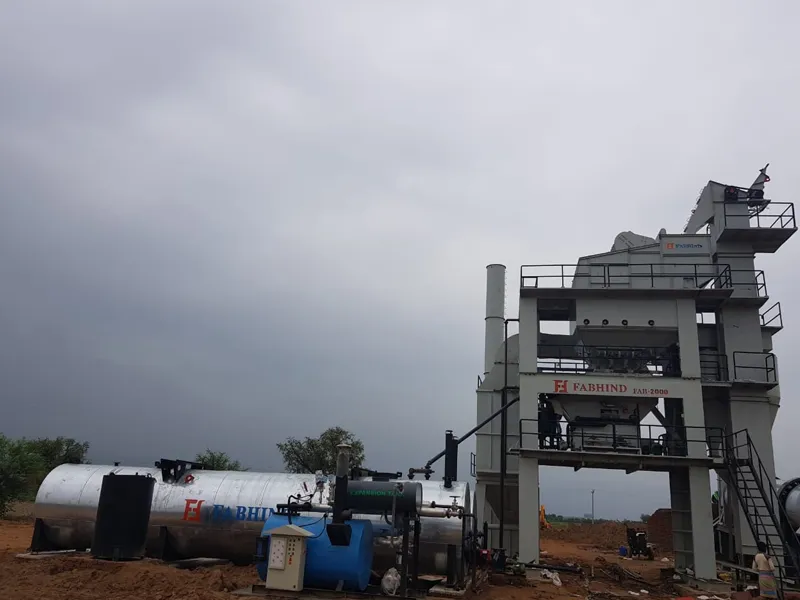
Asphalt batch mix plant with Cold aggregates bin feeders
Latest Asphalt batch mix plant bins are all-welded and modular in construction, permitting easy addition of bins to meet growing needs. Steep bin walls and valley angels allow free flow of aggregate from the feeders minimising hold up of materials in the corner and bridging with sticky aggregates. The bins are supplied with adjustable calibrated gate openings and variable speed feeders drive, together offering total proportional control, greater flexibility and accuracy of operations. The high-pressure atomized, fully automatic remotely controlled burner unit has a very good reputation for its fuel efficiency, ease of operation and high uptime. Completely automatic process control with systems interlocks ensures conformance to high safety standards. The thermodrum unit follows a triple heat transfer system that ensures a total transfer of heat to the aggregates, translating into higher productivity and lower fuel consumption. The heat is transferred to the aggregates using conductive, convective and radiation techniques. The unique flight design ensures total heat transfer, thorough mixing & coating, lower emissions and prevention of bitumen oxidation.

Asphalt batch mix plant for small to medium-sized projects
The latest asphalt mix plants are available in a modular and containerized design with no external ducting, requiring minimal transport vehicles and allowing for the quickest erection and fastest setup time. The plant units need minimal inputs for setting up and assembly at the site. Each module has been intuitively designed with unique assembly systems which help set up the plant with greater ease. Cumbersome ducts and time-consuming complex assemblies have been all done away to give way for quick setting-up. The smart’s modular and standardised transport dimensions allow the use of standard trucks or trailers for transportation. Without any over-dimensioned unit nor heavy transportation costs, the plant allows contractors to utilise the equipment in different terrains. The components are robust and designed to perform in harsh environments. There are also 5+1 aggregate grades for precise tuning of sizes, rust-arrestor technology and accurate weighing systems. Plants are designed specifically with recycling in mind, so prevention of oxidation, protection of virgin bitumen, rejuvenation of old asphalt, and class mix gradation. AP rejuvenation system allows easy rejuvenation of old asphalt and ensures optimal workability and savings in RAP. The plants has integrated new technologies like Fibre Dosing System to produce SMA; and Coal Fire Burner to save fuel cost.
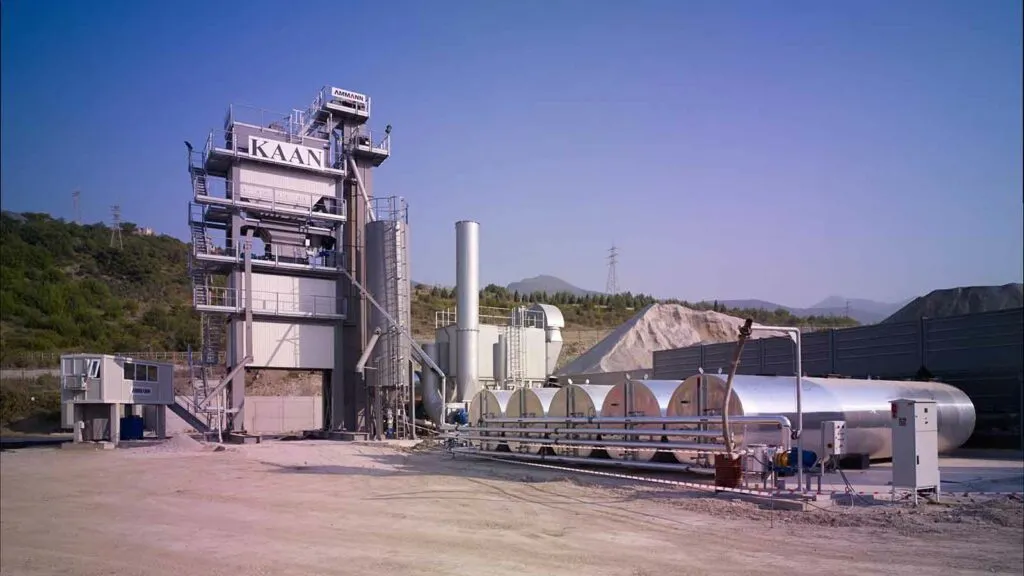
Asphalt batch mix plant with a control cabin and automation system
Asphalt Plant can be controlled continuously through the computer monitor on the operator table manually and automatically. Control system is done by customised software that works on the Windows operating systems. Main program is very easy to understand and functional. It is used easily with one button click. The peripheral information is collected from 3 stations and stored in the computer and processed. It can be controlled directly or from distance by modem/internet. Plant operations and production reports are stored in a database. Aggregate bitumen temperature, flame amount percentage, damper opening percentage, dosing velocities, mixing time, weighing of bitumen, filler and aggregate, etc. are observed and controlled from the control cabin instantly. The control cabin of the plant is made of sheet iron and its door can be locked. The field of view for the operator is designed as the operator will be able to see and follow all the plants. The cabin is insulated against heat and cold. An air conditioner with sufficient capacity is provided inside the control cabin to perform heating and ventilation.
Conclusion
Asphalt batch mix plants are being subjected to technological development as per customers’ requirements. This type offers maximum flexibility and great versatility and is ideal for applications where it is necessary to satisfy a range of different product specifications and to promptly respond to the various needs of the projects.
Image sources- Ammann India, Marini India, Fab India