Crushing equipment is used to reduce the size of material into much smaller pieces. The equipment is designed with heavy plates or jaws used to apply pressure to whatever material has been fed into the chamber. The crusher equipment is predominantly used by the mining industry to carry out operations like the crushing of rocks, building materials, solid waste, etc. Modern crusher models adopt self-drive mode, possess advanced technology, and complete function. The newer models use a direct drive system for optimum fuel efficiency and low operating costs and include several user-friendly features. This ensures that they’re both simple to operate, and easy to maintain. Mobility and versatility have been key factors in the development of new models, with many companies also offering new options of hybrid drive systems.
The static plants, which take days to set up and dismantle, have slowly become redundant with the advent of portable devices with higher capacity. There is a growing requirement of aggregated equipment in the coming years to meet the demand from the construction and infrastructure sector. This anticipates an increased demand for crushers. In the construction sector, growth in roads, railways, irrigation, and other infra projects will drive the material processing equipment industry. The rising use of artificial sand for construction work after the ban on river sand mining is expected to have a positive impact on the growth of the crushing equipment market. The coal sector is set to grow rapidly for the next few years. Different types of crusher models are available for different applications, each of them is discussed below.
Different types of crusher equipments
Hybrid crusher with advanced roll-crushing technology
The latest hybrid crushers are designed for the primary, secondary and tertiary crushing of soft to medium-hard materials that also tend to be wet and sticky. This versatile machine combines advanced roll-crushing technology, overload protection and a compact frame to optimize your productivity. Depending on the application and model, it can achieve capacities of up to 12,000 metric tons per hour. Hybrid crusher models have a compact design and take up minimal space, thanks to a small roll diameter made possible by the aggressive tooth geometry. The crushing rolls are equipped either with crushing rings, segments or crushing picks, depending on the application and feed material. The drive system for the rolls consists of individual electric motors for each roll, as well as couplings and gears. The newer models have a compact design and take up minimal space. The crushing rolls are equipped either with crushing rings, segments, or crushing picks, depending on the application and feed material.

Jaw crusher featuring hydraulic discharge setting adjustment
Modern jaw crushers feature hydraulic discharge setting adjustment, adjust-on-the-fly chamber clearing in the event the site loses power (once power is restored) and hydraulic relief for overload events with auto-reset. Machines have an aggressive nip angle that provides consistent crushing throughout the entire crushing chamber, which leads to increased production and less downtime on maintenance. Hydraulic separation and individual lifting of shells are a trend that creates a better environment for any workers on-site working with the equipment. The size of a jaw crusher is designated by the rectangular or square opening at the top of the jaws. Primary jaw crushers are typical of the square opening design, and secondary jaw crushers are of the rectangular opening design. Jaw Crushers can be used in stationary, wheeled portable and track-mounted locations. The Jaw Crusher is well suited for a variety of applications, including rock quarries, sand and gravel, mining, construction and demolition recycling, construction aggregates, road and railway construction.
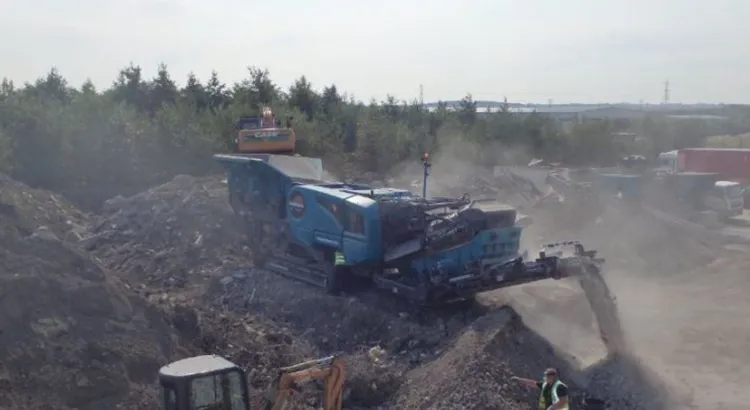
Gyratory crusher lined with wear-resisting plate
The gyratory crusher consists of a heavy cast-iron, or steel, frame which includes in its lower part an actuating mechanism and in its upper part a cone-shaped crushing chamber, lined with the wear-resisting plate. Spanning the crushing chamber across its top is a steady-rest (spider), containing a machined journal that fixes the position of the upper end of the main shaft. In the newer models, the active crushing member consists of the main shaft and its crushing head, or head center and mantle. This assembly is suspended in the spider journal utilizing a heavy nut which, in all but the very large machines, is arranged for a certain amount of vertical adjustment of the shaft and head.

Cone crusher designed for the hardest material types
The new models of cone crushers come with multi-cylinder hydraulic cone systems suited for the secondary or tertiary stages of crushing plants by changing body liners and adaptors. It comes with an automatic control and fingertip manipulation system and two hydraulic cylinders that have a protective effect that if one overloads, then another one can fast react to clear choke merely by remote control. They are widely employed for crushing hard and abrasive materials in both the aggregate and mining industries. Designed especially for the hardest material types, cone crushers are one of the best choices for crushing river gravel, basalt and granite, along with abrasive materials in the mining industry like iron, chrome, magnesite and copper ores. The robust design and high-grade cast steel body of our cone crushers provide the strength and stability necessary for crushing extra-hard materials while ensuring low maintenance costs.

Impact crusher enabled with the maximum feed size
The latest impact crushers have been designed to offer both excellent reduction and high consistency of product yield. With its compact design and ease of mobility, the impact crusher is primarily suited to recycling, demolition and mining applications. The crusher is capable of processing a wide range of material at a high output, these plants are versatile, easy to operate and fuel efficient due to their direct drive system. They are available in stationary, track, and portable configurations meeting any demand for any of these industries. The new hybrid models of impact crushers are engineered for maximum feed size, target output size, and total capacity. The newer models are capable of producing construction-grade aggregate, artificial sand and stone materials, run of mine material, especially for the secondary and tertiary crushing stages.
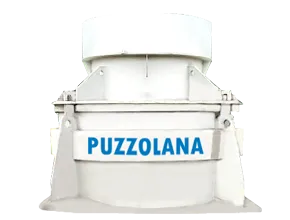
Ball mill crusher for multiple industry applications
A ball milling crusher uses a powder grinding mill used to grind ores and other materials mainly used in the mineral processing industry, both in open or closed circuits. Ball milling is a grinding method that reduces the product into a controlled final grind and a uniform size, usually, manganese, iron, steel balls or ceramic are used in the collision container. The ball milling process is prepared by rod mill, sag mill, jaw crusher, cone crusher, and other single or multistage crushing. The newer models of this machine are widely used in cement, silicate products, new building materials, refractory materials, fertiliser, black and non-ferrous metals and glass ceramics and other production industries of all kinds of ores and other grind-able materials can be dry or wet grinding.
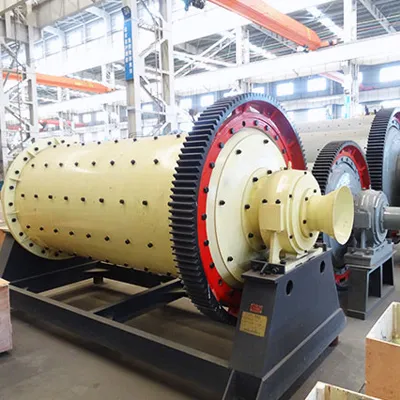
Roller crusher with replaceable abrasion-resistant steel liners
Roll crusher that has features like a high-efficiency gear drive and hydraulic gap management to ensure the lowest possible operation cost and ease of use. It can be used even for larger feed sizes. The newer models offer belt-driven Roll Crushers in four designs: Single Roll, Double Roll, Triple Roll and Quad Roll Crushers, which provide a substantial return on investment by operating at low cost and maximizing yield by generating minimal fines. The rugged design, which incorporates a fabricated steel base frame lined with replaceable abrasion-resistant steel liners, stands up to the toughest mineral processing applications while providing safe and simple operation, including an automatic tramp relief system to allow uncrushable objects to pass while the crusher remains in operation.

Hammer Mill crusher to generate high-quality aggregate
The hammermill is distinguished by its rotor which features a series of hammers, instead of blow bars, that hang loosely, ready to be spun. Once the rotor is in operation, the resulting centrifugal force sends the hammers outward, spinning rapidly in order to crush the material being processed. The newer models of this machine generate high-quality aggregates, cubical in shape, with superior soundness. it is expected that they strike and contact against each other, resulting in even further reduction
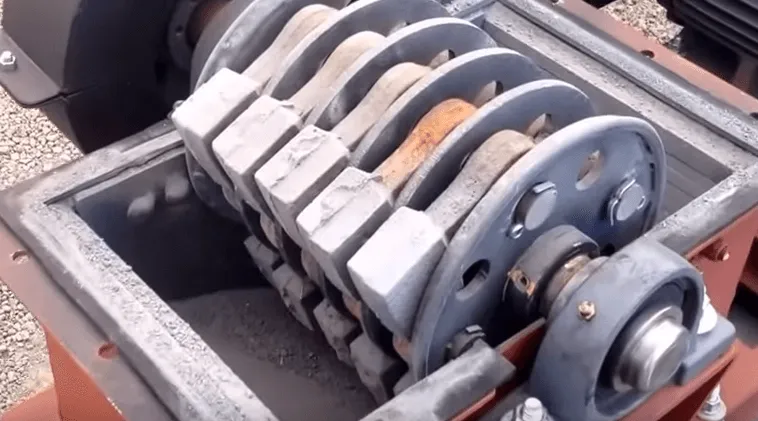
Rod Mill crusher with output material board
Latest road mil crushers employ high carbon steel or special steel rods of nearly the same length as that of the drum, in place of steel balls in ball mills. Grinding Rod Mill is mainly used for feldspar, quartz, minerals and other raw materials, processing, and crushing. When the frame rotates, centrifugal force is produced. At the same time, the steel rods are carried to some height and then fall to grind and strike the material. After grinding in the crushing chamber, the powder is discharged by an output material board. The newer models of this machine are driven by a motor with a speed reducer and peripheral large gear, or a low-speed synchronous motor with a peripheral large gear.

Conclusion
The mining and quarrying industry is one of the largest users of crushing equipment. Buyers are interested in equipment features that bring efficiency in costs and quality. Keeping the demand in mind the manufacturers are working on various new features that would be apt for the Indian and regional markets. There is a zeal among manufacturers considering the Government’s National Infrastructure Pipeline plan, policy reforms in mining, Recycling of C&D Waste and Biomining under the Swachh Bharat Mission.
Image Source: rockprocessing.sandvik, powerscreen.com/en/, puzzolana.com, promaninfi.com, propelind.com