Stress cracking corrosion occurs when metals or concrete develop cracks due to the combined effects of tensile stress and a corrosive environment. This process involves the gradual formation of cracks under sustained tensile stress combined with exposure to corrosive substances like chlorides or sulfates. These cracks propagate over time, weakening the material and potentially leading to structural failure.
Where does stress corrosion cracking (SCC) occur?
- Concrete Reinforced Structures
- Steel Reinforced Structures
- Pipelines
- Storage Tanks
- High-Rise Buildings
- Foundations
The causes of stress corrosion cracking (SCC) include:
- Sustained tensile or compressive forces
- Exposure to corrosive substances
- High or fluctuating temperatures
- Material susceptibility
- Direct contact with aggressive chemicals
- Excessive operational or environmental stress
- Deficiencies in design or material selection
- Surface imperfections
- Inadequate maintenance
- Persistent moisture or water ingress
Signs of stress corrosion cracking (SCC):
- Visible cracks
- Surface discoloration
- Surface blisters
- Deformation
- Fragmentation
- Corrosion pitting
- Increased leakage
Types of stress cracking corrosion
There are two main types of stress cracking corrosion, namely Metal Stress Corrosion Cracking and Concrete Stress Corrosion Cracking. Under these two types various types of corrosion can occur as discussed below.
Metal Stress Corrosion Cracking
Chloride Stress Corrosion Cracking (CSCC)
Chloride Stress Corrosion Cracking (CSCC) occurs when metals, particularly stainless steels and aluminum alloys, are exposed to chloride ions. These ions are commonly found in environments with deicing salts or seawater. The presence of chloride ions exacerbates the susceptibility of these metals to cracking under tensile stress. Over time, the combination of stress and chlorides initiates and propagates cracks on the metal surface. The cracks often develop in the form of branching or intergranular patterns and can progress rapidly, compromising the structura safety of the affected metal components. This type of cracking is particularly concerning in marine structures, bridges, and other infrastructure exposed to saline conditions.
Caustic Embrittlement
Caustic Embrittlement occurs when metals, particularly carbon steels and certain stainless steels, are exposed to caustic soda (sodium hydroxide) solutions. The caustic environment causes a chemical reaction with the metal, leading to the formation of cracks and a general degradation of mechanical properties. This type of corrosion is commonly encountered in industrial settings where caustic solutions are used, such as in chemical processing plants and paper mills. The cracks caused by caustic embrittlement can spread quickly, leading to structural failures if not addressed promptly. The embrittlement effect significantly impacts the performance and longevity of metal components subjected to caustic conditions.

Concrete Stress Corrosion Cracking
Alkali-Silica Reaction (ASR)
Alkali-Silica Reaction (ASR) is a chemical reaction that takes place between the alkalis present in cement and the silica in certain types of aggregates used in concrete. When moisture is available, this reaction forms a gel that expands over time, causing the concrete to swell and crack. The expansion of the concrete matrix due to ASR can lead to significant structural issues, such as compromised load-bearing capacity and reduced durability. This type of reaction is particularly concerning in structures where large volumes of concrete are used, such as dams, bridges, and highways. The cracking patterns can be widespread, and the structure may be severely affected if the reaction is not managed.
Alkali-Carbonate Reaction (ACR)
Alkali-Carbonate Reaction (ACR) involves a reaction between alkalis in cement and certain carbonate aggregates used in concrete. Unlike ASR, ACR primarily affects carbonate-based aggregates and results in the formation of expansive products that cause concrete to crack and deteriorate. The reaction typically occurs in the presence of moisture and can lead to significant structural problems, including reduced strength and durability. ACR can be challenging to detect early, and the damage often manifests as widespread cracking that can compromise the stability of concrete structures such as pavements, retaining walls, and foundations.
Corrosion of Reinforcing Steel
Corrosion of reinforcing steel in concrete is a common issue, primarily driven by the ingress of chlorides or carbonation of the concrete. Chloride ions, often from deicing salts or marine environments, penetrate the concrete and reach the embedded steel reinforcement. Similarly, carbonation of concrete reduces its pH level, which diminishes the protective layer around the steel. As the steel corrodes, it expands, exerting internal pressure on the surrounding concrete and causing it to crack and spall. This process can severely impact the load-bearing capacity and longevity of concrete structures such as bridges and buildings.
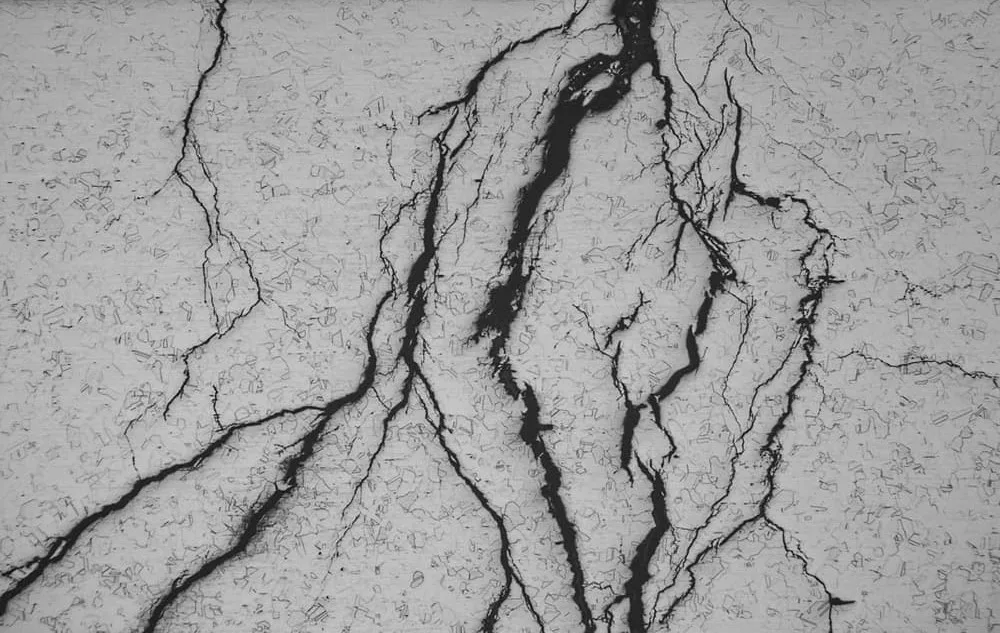
How to avoid stress cracking corrosion?
- Select materials with high resistance to stress corrosion cracking.
- Design structures to minimize stress concentrations and avoid sharp corners.
- Control environmental exposure to corrosive agents.
- Apply protective coatings or linings to shield metal surfaces.
- Implement a regular maintenance and inspection schedule.
- Ensure high-quality construction practices and materials.
- Use corrosion inhibitors to reduce corrosion rates.
- Ensure proper curing of concrete.
- Use low-alkali cements and non-reactive aggregates.
- Use corrosion-resistant fasteners in metal structures.
- Apply sacrificial anodes for cathodic protection systems.
Conclusion
Stress cracking corrosion poses a serious risk to both metal and concrete surfaces, caused by the combined effects of tensile stress and corrosive environments. Prevention involves careful material selection, stress control, environmental management, and regular maintenance. By addressing these factors, engineers can improve the durability and safety of structures, extending their lifespan and minimising repair costs.