ABSTRACT
The construction industry has advanced leaps and bounds during the last 6 decades but for a few haunting challenges like:
1. Almost all round failing waterproofing systems and has become a major challenge for the construction industry.
SIGNIFICANCE: The rejection/falling concrete cover of top floor RCC.
2. Damp walls due to RISING DAMPNESS due to
i)DPC FAILURE &
ii)Wet Sunken slabs
LATEST TECHNOLOGY using AQUAVENT® – PATENTED PRODUCTS & A COPYRIGHTED TECHNOLOGY with respect to:
- The 1st Roof crack (Over deck) management tool.
- The 1st Rising Dampness & DPC failure management tool.
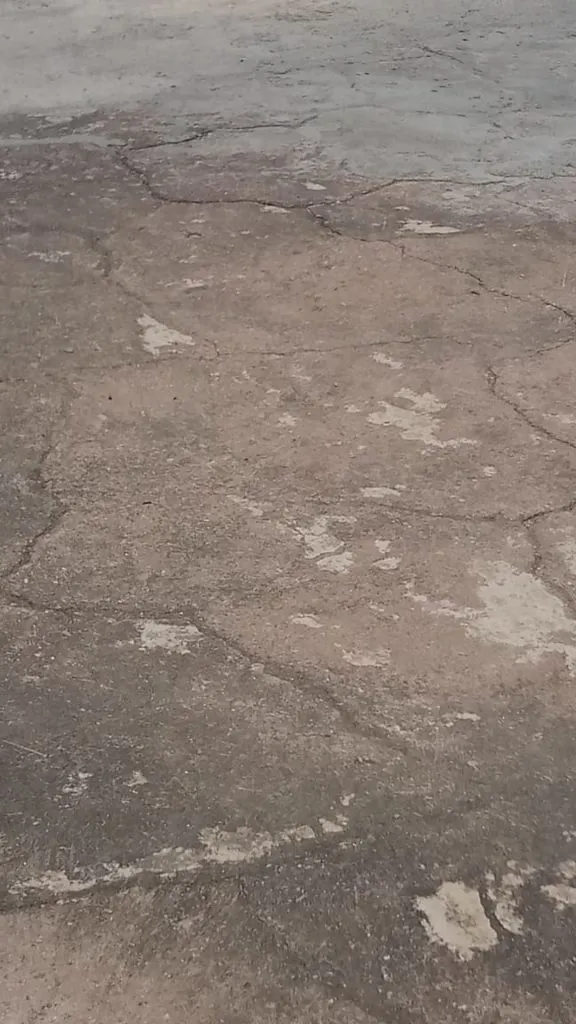

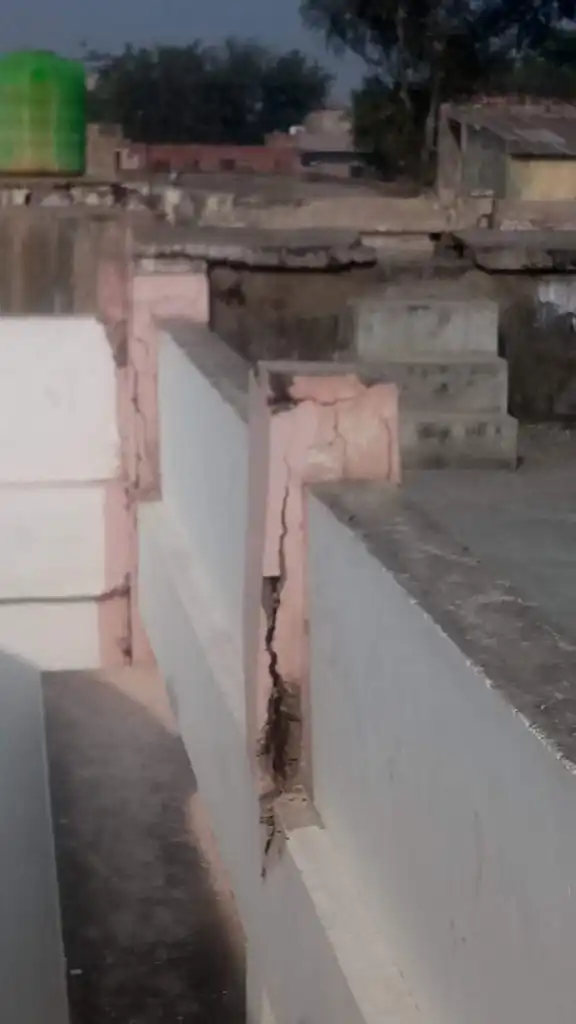
Main Article
We have witnessed the waterproofing industry struggling for long term solutions since its inception.
A lot of products have been developed and modified during the last 3/4 decades and a big advancement has been witnessed…..but still, we are struggling for some long term solution in waterproofing. The eventuality is that almost every structure is witnessing Damp walls, Roofs, sunken slabs, etc and resulting into distressed RCC. –particularly the rejection of PCC cover of the ceiling of top floor IMPLYING almost alround failure of waterproofing systems.
The irony is that even the heritage structures like Rashtrapati Bhawan and other buildings are being maintained back to back waterproofing guarantees but still leakages are persistent.
The damp –colour variation at the junction of top floor RCC. roof slab and parapet say it all.
The basic reason for this is GROSS NEGLECT on account of the engineering assets …in the country or possibly they were CLUELESS of the possible solutions. A lack of motivation to invest one’s time and energy could also be a reason.
EFFECT:
1.ROOFs /Terraces
The prolonged entrapped moisture between the RCC. slab and top finishing tiles/PCC. on roof & terraces sets in a phenomenon – ‘HARITON’ effect-explained later.



The alternate DRY-WET cycles lead to cracks development and transmission of leakages through these results into the oxidation process of steel, thereby increasing its volume This increase in volume creates stress on concrete cover over steel leading to de-bonding which ultimately leads to spalling-rejection of concrete cover.
This has led to a very grim and scary situation where we feel limited to:
- All round distress of RCC. structures eventually in 10-15 years of construction.
- IRONICALLY the nodal agencies have LOWERED THE AGE OF RCC. from at least 200 years to less than 50years to rationalize the limitation.
- Health hazard due to dampness
- No long term SOLUTION insight
- Over burdening of government & others non-plan expenditure
2. WALLS
The basic issue with respect to the walls is capillary action. This is activated by:
i) DPC failure:
The basic reason for this is neglecting/lack of understanding of the DPC layer/Plinth Beam ie. Plastering across the Plinth Beam/foundation up to the brick wall neglecting the basics of DPC. [Damp proofing course].
This connects the wet soil to the brick wall. The logical capillary action is activated – ‘HARIWON’ effect -explained later, leading to wet walls.
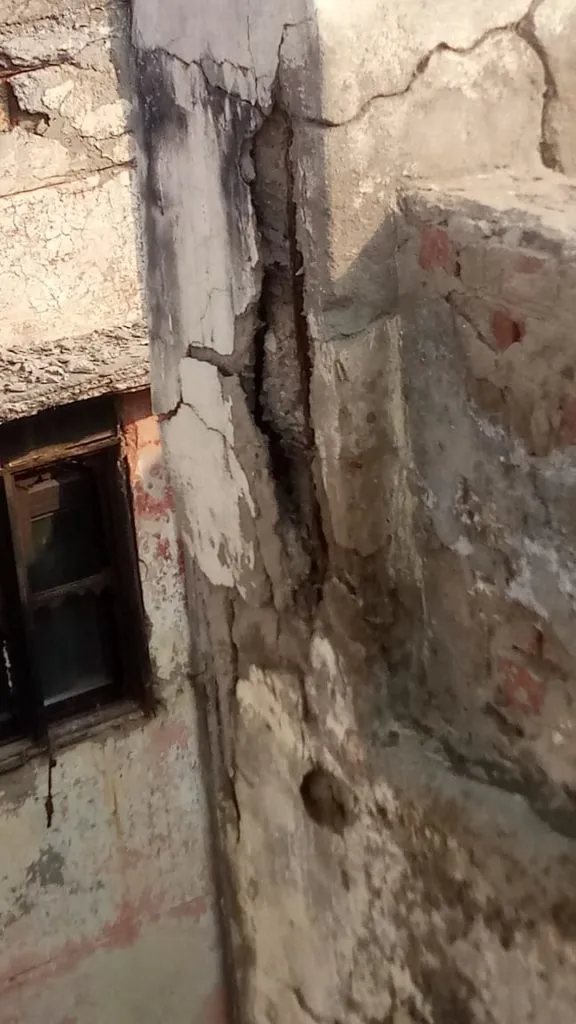

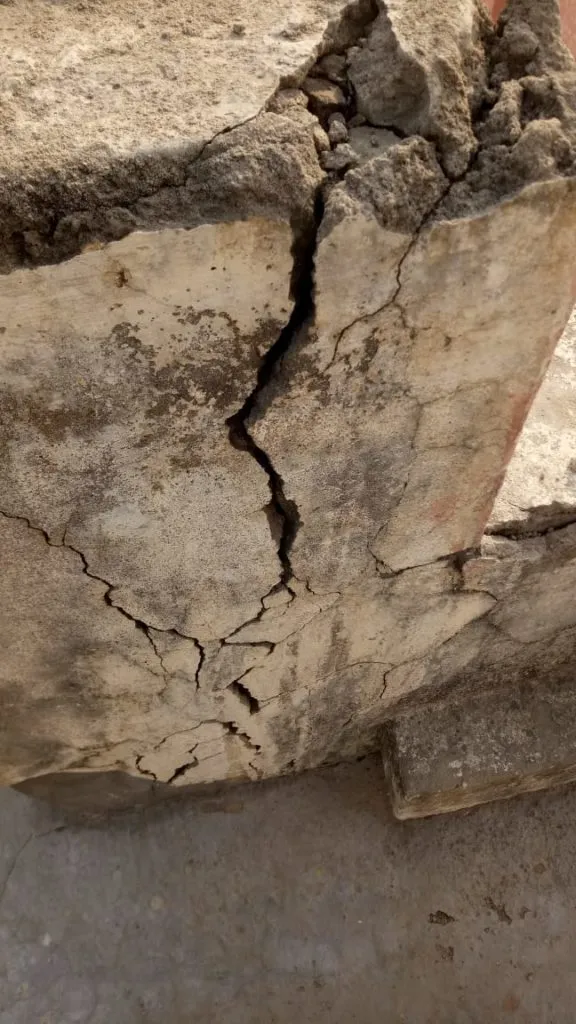
Many unsuccessful attempts have been made like coatings, masking reinforcements, tiles, PVC paneling etc. The dampness is seen to cross over even up to Roof ceiling across the tiles etc. [Provided to cover the damp areas]
ii) WET SUNKEN SLABS:
Here the foam concrete/filling of sunken slab once saturated by leakages from sewerage or water pipes and fittings transmits capillary action as in DPC leading to wet patches outside bathrooms, urinals etc. The wet walls are a very common sight and the industry had somewhat accepted it as a NOT–DOABLE proposition. THIS DAMPNESS IS TRANSMITTED TO ADJACENT RCC. BEAMS, COLUMNS AND SLAB and is the biggest reason for EARLY ONSET OF DISTRESS and therefore, should not be neglected.
To answer this, the author took the challenge and went to the ground to study the 5 burning issues:
- The non structural-crack development
- The DPC. failure
- RISING DAMPNESS
- Reduce the financial burden to an average householder and government, industry due to recurring expense on account of repainting
- Augmentation strength of DISTRESSED RCC. structures without dismantling.
And after 23 years of various studies has come up with practical solutions.
The NEED for the STUDY became more important, as, our premier institutions IIT’s, BIS and all institutions were clueless.
THE STUDY
A phenomenon ‘HARITON‘ effect discovered in the year 1996-97, as an answer to the development of the repeated crack in the roof tiles, finishing top layer or waterproofing done, etc.
This is the basic reason for the failure of almost all waterproofing products till date. The significance of failure is all round distress of almost all buildings RCC. The ceiling of which the concrete cover is falling.
It has been found that the grading course of almost all roofs ie. Between the RCC. slab and top finishing tiles/PCC etc is wet. The moisture/water from this substrate is evaporated in warm weather. This creates an air pressure-an up thrust causing the weakest section of the top layer, to develop crack/s to facilitate the release the hot compressed air.
The crack so formed is created by the lifting of the lower end (towards the slope). The lower section being lesser in thickness lifts, creating a type of funnel for rainwater to get absorbed into the substrate, a SIPHON action sets in during continuous drizzling, thus rewetting it, acting, as, a CATCHMENT.
This phenomenon is named “ The HARITON effect”.
Now that we had discovered the basic reason of NON-STRUCTURAL CRACKS development, we now needed the CRACK MANAGEMENT TOOL. This has been discussed in detail in solutions subhead.Waterproofing /coating is provided over the tiles etc periodically. This again cracks up, as explained above, leading to failure of the waterproofing system.
Similarly ‘HARIWON’ effect discovered in 1998 while solving the matrix of DPC failure and RISING DAMPNESS. The basic issue with respect to the walls is capillary action.
This is activated by :
i) DPC failure: The basic reason for this is neglecting the DPC layer/Plinth Beam ie. Plastering across the Plinth Beam/foundation up to the brick wall.
This connects the wet soil to the brick wall. The logical capillary action is activated. The wet walls resulted into peeling of painting, effervescence, saltpeter and even wearing up of plaster. Interestingly, the SALTPETRE is precipitated only on damp walls.
During the study, it was observed that the saltpetre effect is aggravated when the walls get wet. The above has to be painted with waterproofing products, reinforcements, tiles, wooden, plastic paneling and re-plastering etc. All these products and practice have also failed to deliver, as, the dampness travels beyond the tiled area and even rises to the roof.
The phenomenon is the transmission of moisture by capillary action from a highly saturated area to a lesser saturated area. This is termed “HARIWON effect”
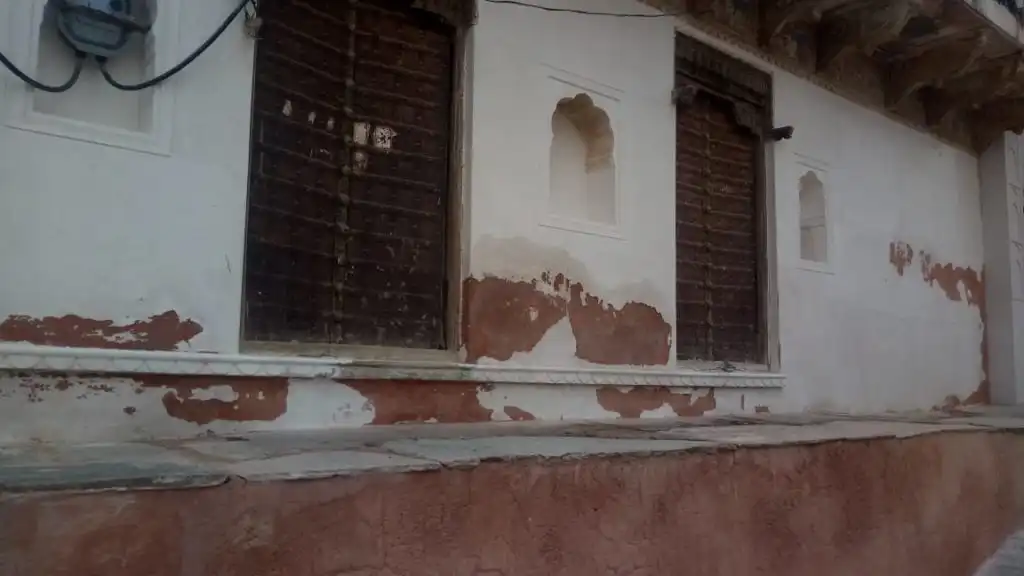


SOLUTIONS
1. ROOF/TERRACES:
The biggest challenge was the roof cracks development.
The study of the phenomenon was done at Dehradun, Uttrakhand. Dehradun is a typical area which receives rainfall at least once in a week. The biggest crack development is observed with a sudden cloud formation in a hot afternoon and a sudden downpour (called 4 o’clock rain by localities). This causes a type of THERMAL SHOCK-complimented by “HARITON effect”. A thermal shock is due to abrupt cooling of a hot substrate.
It took a while to understand that the thermal shock and HARITON effect are two separate phenomena.
A crack redevelopment of a polymer coating on roof in a single day, made it clear that there is some other aspect. A hole was drilled, a pipe and a balloon over it, fixed to make sure water from rainfall doesn’t go in. The balloon was seen to inflate a bit next afternoon. We now inflated a balloon and deflated it and fixed it again. EUREKA –it inflated a bit more. Now we knew that moist hot air is being released continuously.
To facilitate the hot air release/counter the cracks, initially, we created a chimney sort of arrangement at highest locations-central ridge lines in the roof. This was a cumbersome process and backfired at some locations on account of maintenance issues. A more user- friendly product/procedure was the necessity.
A product AQUAVENT [R] for roofs conceived in 1996-97 and AQUAVENT [W/M] for WALLS in 1998 and finally submitted for © COPYRIGHT and PATENT in 2016, when Prof.SK Agarwal, Ex-Head, Structural Civl Engineering, IIT-Roorkee University, suggested it to be shared with the fraternity at large.
The roof model was initially made of UPVC pipes, later in MS and finally in Aluminum, because of its good conductivity, paintability and durability.
Finally the SOP[Standard operating procedure] adopted is:
Step 1: Installation of AQUAVENT (Moisture release system) 1 per 40 Sqm.
Step 2: Injection grouting of cracks @ 1 -2 kg/Sq.cm pressure using grouts with bonding aids. A special grouts mix prepared for HERITAGE STRUCTURES.
Step 3: Gravity Grouting in substrate with anti corrosive grouts to inhibit corrosion process of the RCC. Slab and initiate rapid drying to distress the RCC slab.
2. WALLS:
The wall model was initially developed in an earthen model with various versions in 1998, Upvc in1999 and finally in Aluminum in 2016.
Finally the SOP[Standard operating procedure] is:
DPC failure:
Step 1: Installation of AV (Moisture release system) <1 per Rmt along scirting.
Step 2: Injection grouting for creating a chemical DPC @ 1 -2 kg/Sq.cm pressure using grouts and Soil stabilizers at ground level in specific cases.
SUNKEN SLABS:
Step 1: Installation of AV (Moisture release system) 1 per Rmt along skirting/outerface.
Step 2: Injection grouting for creating a chemical DPC @ 1 -2 kg/Sqcm pressure using grouts
Step 3: Pressure Grouting of traps, chowkhats / doorframes, corners and hollow with anti corrosive waterproofing grouts to inhibit corrosion process.
AQUAVENT has been successfully used in INDIA at :
- 1996: VSNL[Ahmed Satellite Station, Lachhiwala, Dehradun, Uttrakhand]
- 1998:1KN MARG, NDC Tees January Marg, BASE HOSPITAL, New Delhi,
- 2016: GPO.[A heritage building] Fort Mumbai.2018-19:
- BIRLA HOUSE, NEW DELHI
- BIRLA HOUSE JAIPUR
- MUNJAL FARMS, DELHI
- RAINBOW MESS, TRIVENI MESS
- 510-AD missile UNIT [CE -DZ, Delhi Cantt.]
- Itrana Cantt- Alwar
- KV-OLF, Raipur Dehradun, Uttrakhand.
- Gurudwara Sahib: New Rajendra Nagar.
- BHARTIA HOUSE, DELHI
- Other residential projects
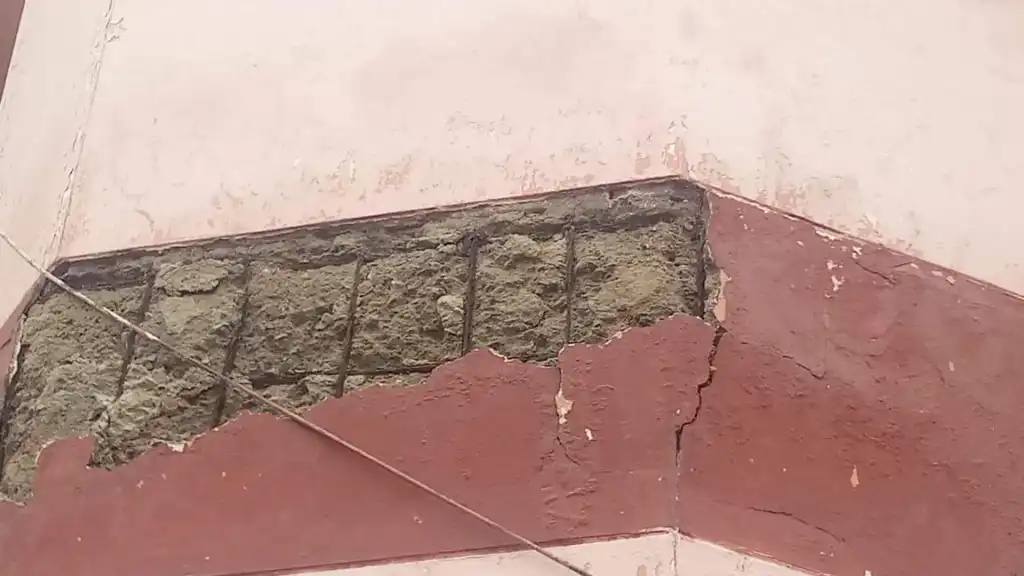

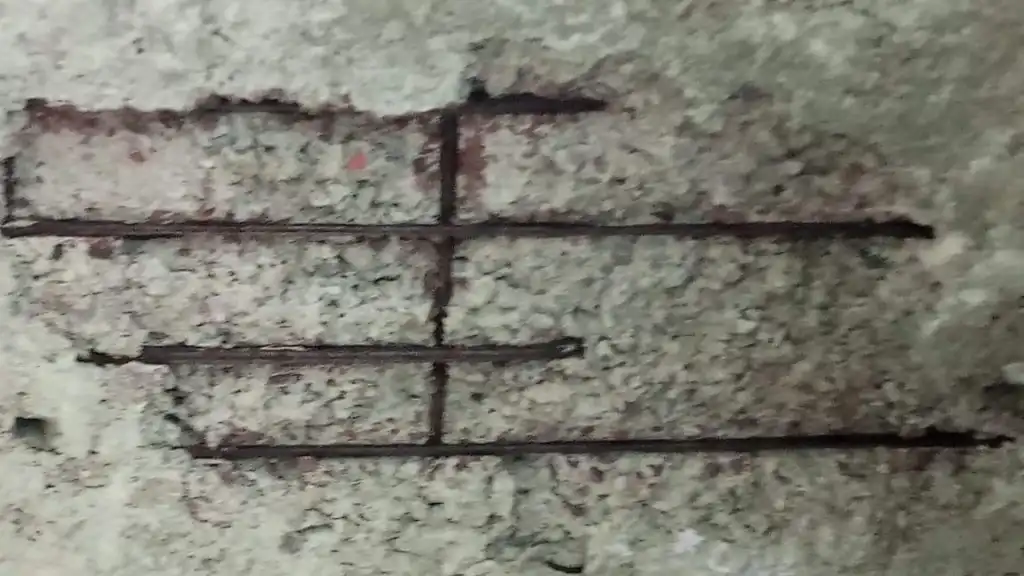

The biggest challenge attended:
A normal tendering process timing in government departments in INDIA is-
i) Tendering in April
ii) Work order by 3rd week of May
iii) Start of monsoon by 1st /2nd week of June. In fact many a contractors dismantled the roof tiles and created a virtual crisis, as, the leakage increased due to ponding of water on roof.
We solved the issue by introducing the AQUAVENT and can save the civil construction/ maintenance industry billions and embarrassment of leaking roofs and damp /peeling walls.
The advantages of using AQUAVENT® -roof model are:
AQUAVENT® will revolutionize the retrofitting and waterproofing worldwide. The game changer is:
- COST: Saves approximately 50-70% cost. Approximately Rs. 2500-3000 crores to India annually & Billions of dollars/annum internationally. The savings from this can be used to protect the other roofs which have to be excluded for want of funds.
- TIME: Saves upto 90% time as compared to the conventional way of removing everything upto RCC. slab and redoing.
- GUARANTEE: Up to 20 years already delivered in INDIA.[spotless].In fact the guarantee word has become useless here, as, NO RESPITE using conventional products and methodology.
- Relief to USER: MINIMUM DISTURBANCE
- GREEN aspect
- No pollution: otherwise created by dismantling/redoing.
- Saving trees, as, less mining for raw materials-Natural resources on account of sand, cement, stone grit, manpower. You save natural resources needed for re-grading etc.
- No debris
- Ease of working during the rains, as, dismantling not done.
- The increase of AUL[Actual usable life] of structures on account of being free of leakage/seepage. We can logically extend the AUL[Actual usable life ] of structures by 20-30 years, thus, saving the immediate stress of redevelopment of additional/untimely –expensive rehabilitation /reconstruction.
- A boon for restoration of HERITAGE STRUCTURES, as, no dismantling needed. Infact special grouts formulated for these.
Implications:
- Will save approximately billions per annum to our national/international wealth.
- Alternatively, we can do more roofs per annum in same budget.
- Extend life of structures, as, in combination with Dr.MIRACLE waterproofing/retrofitting aids, the structures will be gradually de-saturated/free of corrosion.
- Already test marketed for 22 years and started using successfully in India since March 1996.
- Saving of vast natural resources, as, the need to replace grading course (wet Mud-phuska, LCC., Brick-coba, foam concrete not needed.
- Reduction of idling time of asset under repair. A great relief to user. USER: MINIMUM Disturbance.
- GREEN IMPACT: Saving Debris generation and subsequent grading course which needs the sand, grit etc
- WORKING during RAINS: Waterproofing can be done even during rains as, virtually no dismantling needed.
IMPACT/EFFECT: on Health
… Moulds produce allergens (substances that can cause an allergic reaction), irritants and, sometimes, toxic substances. Inhaling or touching mould spores may cause an allergic reaction, such as sneezing, a runny nose, red eyes and skin rash. Moulds can also cause asthma attacks.
… Exposure to damp and moldy environments may cause a variety of health effects, or none at all. Some people are sensitive to molds. For these people, molds can cause nasal stuffiness, throat irritation, coughing or wheezing, eye irritation, or, in some cases, skin irritation. Toxic black mould. Stachybotrys, or toxic black mould, is harmful in the home because it produces mycotoxins.
… These mycotoxins are very dangerous and can cause problems with the reproductive system, vision, skin, circulatory and respiratory systems and can even have psychological and neurological effects.
… The majority of moulds found in the home are caused by excess moisture, usually this is due to high humidity levels in the property but it could also be caused by leaking pipes, rising damp, rain seeping in due to a damaged roof or window frame. In new build properties you may start to notice excess moisture and even mould due to the property not drying out yet. It is important to remove the mould problems in your home as soon as possible as left untreated it can soon become a health risks to those living in the property.
About the author:
Ajaya Kumar Harit is a waterproofing -retrofitting inventor/scientist and has to his credit solving most complicated/extreme engineering waterproofing/retrofitting solutions using his SIGNATURE-without DISMANTLING techniques and solutions.
AQUAVENT®, is © copyright, ® a registered trademark & PATENT of Ajaya Kumar Harit.
(This is Constrofacilitator exclusive content….for using..of collage images and content…source to be given is mandatory…for any medium of content publishing)