Building cracks are the most common problem found in any type of building. We all love to have a house which is structurally safe and beautiful but it is not so easy, one has to overcome natural calamity, soil failure, construction faults, improper design, and inadequate joints causing cracks on the building. Through the cracks in concrete cannot be prevented entirely but they can be controlled by using adequate material and technique of construction and specific design criteria. On timely identification of such cracks and adopting preventive measure are essential. Active cracks cause serious problems and they need special attention as they are structurally hazardous. So, it is important to understand the types of cracks, crack patterns and their causes and the preventive measures to be taken to control the cracks.
The article focuses on the Investigation of Cracks and Repair Methods in Buildings
INTRODUCTION
Cracks in the building are a universal problem faced throughout the world. Building components develop cracks whenever stress in the components exceeds its strength. Stress in the building components could be caused by externally applied forces such as dead, live, wind, seismic loads or foundation settlement or could it be induced internally due to temperature variations, moisture changes and chemical actions. Cracks affect the building’s artistic look and it destroys the wall integrity, affects the safety of structure and even reduces the durability of structure.
PRINCIPLES OF INVESTIGATION OF CRACKS
Step 1: Discussion with Client/Owner of the Building
One of the simplest and most important things is to discuss with a client or owner about the cracks in the building and gather information from them.
- When was the building constructed? Date and year of construction?
- Ask for building drawings? And the details of constructions if available.
- Ask them when the cracks first appeared? Or how long was the cracks seen?
- Check whether the client makes complaints about pieces of concrete falling, excessive deflections, large cracks, staining, and water leakages?
- Ask them whether any repair work was carried out if yes, what was the result?
Step 2: Visit the Site
- When you visit the site, always carry proposed building drawings. Check whether the building is constructed as per the plan.
- Check its present use of the structure or any change in the usage of the building.
- Photograph the cracks and number them.
- Mark the width of the crack.
- Check for any tilting of walls or tilting of any structural members, deflections, staining, water leakage, spalling, and corrosion.
- Collect the samples from the site.
Step 3: Understand the Cracks and Its Causes
- Find the type of crack -Is it alive or dead crack.
- Find the causes of cracks : Is it permeability of concrete, corrosion of reinforcement, moisture variation, temperature variation, poor construction practices, poor structural design and specifications, elastic deformation, creep, chemical reaction, foundation movement & settlement of soil ,growth of vegetation, additional alternation of structures.
Step 4: Monitoring and Measuring the Movements of Cracks
- Using tell-tale.
- Crack width gauge.
- Precision callipers.
Step 5: Finding the Suitable Techniques to Repair Crack
- Epoxy Injection.
- Grouting And Sealing.
- Stitching.
- Drilling And Plugging.
- Gravity Filling.
- Drying Packing.
- Polymer Impregnation And Underpinning.
Step 6: Formation of Report
UNDERSTANDING THE CRACKS
Generally cracks can be divided into two types:
- Structural cracks and
- Non-structural cracks.
- STRUCTURAL CRACKS: Structural cracks may rise due to various reasons such as incorrect design, overloading of the structural components. Structural cracks endanger the stability of the building and may be difficult to be rectified.
Table No.1 Structural Cracks Formed On Beam, Column and Slab
BEAMS | COLUMNS | SLABS |
Flexural Cracks | Horizontal Cracks | Flexural Cracks |
Shear Cracks | Diagonal Cracks | Shrinkage Cracks |
Torsional cracks | Corrosion cracks | Corrosion cracks |
Corrosion cracks | ||
Combination of above cracks |
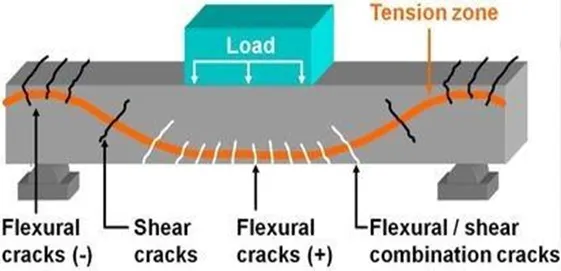
NON-STRUCTURAL CRACKS (HAIR CRACKS)
Non-structural cracks are generally due to internal forces developed in the building.
Materials due to moisture variation, temperature changes and suitable remedial measures can be taken to control it. Cracks may appreciably vary in width from very thin hair crack barely visible to naked eye to gaping crack. Depending upon the crack width, the cracks are classified as:
- Thin Crack -less than 1 mm in width
- Medium Crack -1 to 2 mm in width.
- Wide Crack -more than 2 mm in width.
- Crazing -Occurrence of closely spaced fine cracks at the surface of a material is called crazing. Crazing is the development of a network of fine random cracks on the surface of concrete or mortar caused by shrinkage of the surface layer.
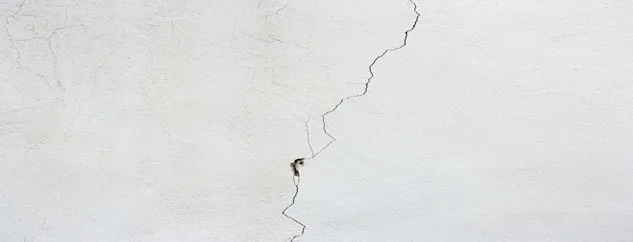
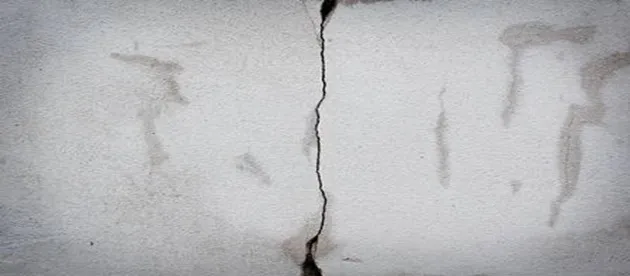
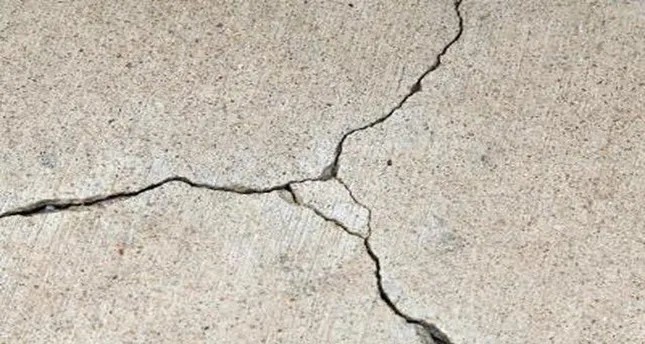
DIFFERENT CASES OF CRACKS IN BUILDINGS
- Cracks on walls
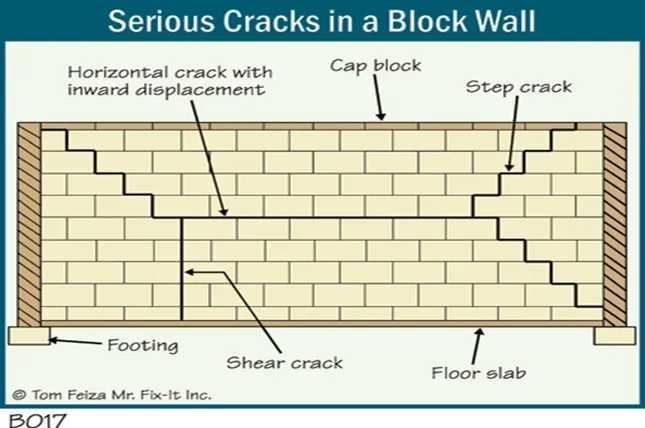
Step cracks, stair step cracks or stepping cracks all refer to cracks that follow the mortar joints in a block wall. The cracks step up or down along the mortar. In many cases, this type of crack is caused by minor movement of the footing, shrinkage or wall movement, and by itself is not a major cause for concern; however, wide cracks or step cracks combined with other cracks and movement indicate a problem.
FOUNDATION MOVEMENT AND SETTLEMENT OF SOIL
Shear cracks in buildings occur when there is large differential settlement of foundation and it may be either due to the following reasons:
- Unequal bearing pressure under different parts of the structure.
- Bearing pressure on soil being in excess of safe bearing strength of the soil.
- Low factor of safety in the design of foundation.
- Local variation in the nature of supporting soil.
PREVENTATIVE MEASURE
The design of foundation should be based on sound engineering principles and good practice.
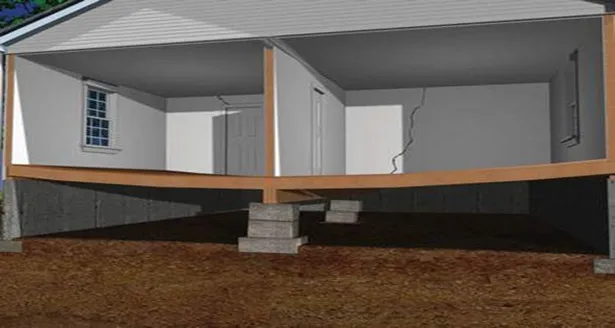
Cracks On Beams And Columns
This type of failure occurs when a material strains under stress. When two materials (having different elastic properties) built together under the effect of load then different shear stresses in these materials create cracks at the junction. Dead and live loads are the main cause of elastic deformation in any structural components of a building.
Preventive Measures: Create slip joints under the support of concrete slab on walls. Provide horizontal movement joints between the top of brick panel and reinforced cement concrete beam/slab.
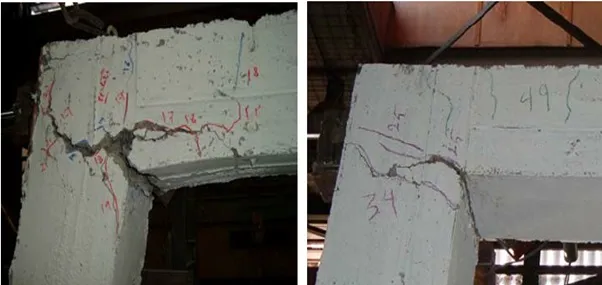
CAUSES AND ITS PREVENTIVE MEASURES
- Thermal Movement
Most materials expand when they are heated, and contract when they are cooled. The
Expansion and contraction with changes in temperature occur regardless of the structure’s cross-sectional area. It is one of the most potent causes of cracking in buildings which need attention.
Preventive Measures: Joints should be constructed like construction joints, expansion joints, control joints and slip joints. The joints should be planned at the time of design and be constructed carefully.
- Chemical Reaction
Chemical reactions may occur due to the materials used to make the concrete or materials
That comes into contact with the concrete after it has hardened. Concrete may crack with time as the result of slowly developing expansive reactions between aggregate containing active silica and alkalis derived from cement hydration, admixtures or external sources.
Preventive Measures: If sulphate content in soil exceeds 0.2 percent or in ground water exceed 300 ppm, use very dense concrete and either increase richness of mix to 1:1/5:3 and to prevent cracking due to corrosion in reinforcement it is desirable to specify concrete of
Richer mix for thin sections in exposed locations.
- Shrinkage
Most of the building materials expand when they absorb moisture from the atmosphere andshrink when they are dry. Shrinkage can be of plastic or dry. The factors causing shrinkage in cement concrete and cement mortar and their preventions are as follows.
- Excessive Water: The quantity of water used in the mortar mix can cause shrinkage. Vibrated concrete has less quantity of water and less shrinkage than manually compacted concrete.
Preventive Measures: Use minimum quantity of water required for mixing cement concrete or cement mortar according to water cement ratio. Cement concrete is never allowed to work without mechanical mix and vibrator.
- Quantity of Cement
As a general rule, the richer the mix is, the greater the shrinkage/drying will be.
Preventive Measures: Do not use excessive cement in the mortar mix.
- Earthquake
Cracks may occur due to sudden shifts in the lower layer of the earth. The voids in the earth might have suddenly collapsed and be filled with soil from the above. Many geological events can trigger earth movements but are continuous movement.
Preventive Measures: Construct the foundation of buildings on firm ground while doing construction. Tie up the building with connecting beams at foundation level, door level and roof level.
- Vegetation
Fast growing trees in the area around the walls can sometimes cause cracks in walls due to expansive action of roots growing under the foundation. The cracks occur in clay soil due to moisture contained by roots.
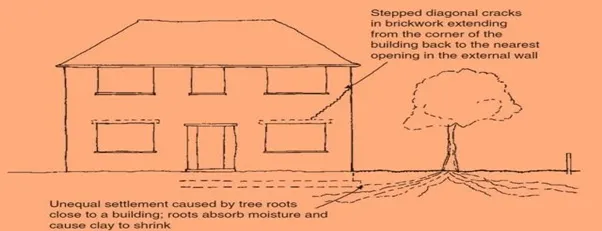
Preventive Measure: Do not grow trees too close to the building. Remove any saplings of trees as soon aspossible if they start growing in or near of walls.
- Poor Construction practices
There is a general lack of good construction practices either due to ignorance, carelessness, greed or negligence. For a healthy building it is absolutely necessary for the construction agency and the owner to ensure good quality materials selection and good construction practices.
Preventive Measure: Proper monitoring and use of good quality of materials is required at the time of construction.
- Corrosion Cracks
Under normal conditions, the pH level of concrete is high (above 12.5). The high pH of concrete allows an inactive layer of ferric oxide to form around the reinforcement, preventing rust. There are two major causes of corrosion in the reinforcing steel: chloride penetration and carbonation. Chloride penetration reduces the pH level of the concrete when oxygen, chlorides, and moisture all penetrate the concrete. Chlorides can be found in potable water, which should never be used to mix concrete. Carbonation occurs when carbon dioxide and moisture infiltrate the concrete, reducing the pH level of the concrete. Both causes of corrosion end similarly. The pH level is the concrete’s last barrier against corrosion, so the reinforcement begins to rust. Rust expands the steel to 10 times the volume, which can cause major problems in the structure.
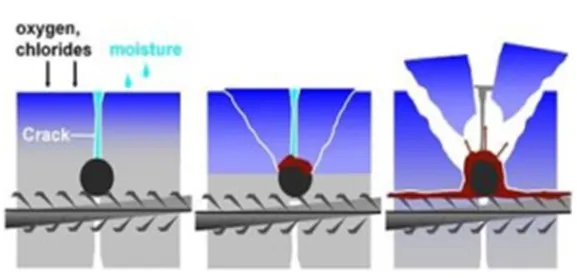
Preventive measure: Use adequate covers as per IS 456-2000. Don’t use salt water in mixing concrete.
MONITORING AND MEASURING THE MOVEMENTS OF CRACKS
At any stage, crack width can be measured, sometimes it is necessary to find out whether cracks live or dead , whether they increase with respect to time or not.
Glass Tell-Tales: A commonly used method of doing so is to fix tell-tales consisting of strips of glass about 2 to 3 cm in width an 10 to 12cm in length across a crack with some quick setting, mortar or adhesive.
If the crack widens, the tell-tale will crack. In case the crack closes instead of widening out, the glass strip will either get disjointed at one end or will crack by buckling. When it is thought necessary to observe the rate of widening of a crack and to measure the extent of widening in relation to time, instead of one glass strip, two glass strips are used side by side fixing them to the background only on one side at opposite ends. A line is drawn across the two glass strips after fixing, and as and when any widening or narrowing of the crack takes place, lines on the two strips move relatively to each other and distance between them at any time could be which would indicate the extent of movement up to the time of making the observation.
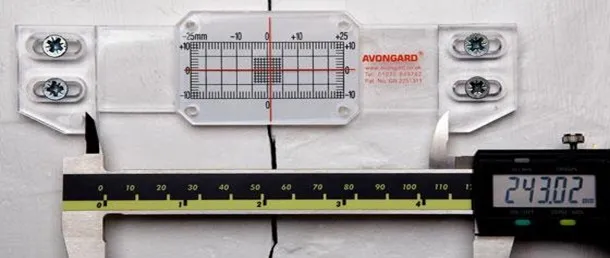
Cracks commonly occur in corners at the junction of walls. Use the type of gauge that is hinged. Most corners are not built precisely to 90 degrees and this type will fit snugly into a corner of any angle, even a bay window corner of 45 degrees. If the gauges are used in pairs and “handed” movement in three dimensions can be monitored.
CRACKS PLOTTING
The characteristics of each crack are plotted onto a drawing or sketch of the building. The characteristics to be recorded are width, direction, taper, frequency and location. If it is possible it will be useful to differentiate between cracks caused by tension, compression and shear stress. A crack on the opposite side of the wall can be shown as a broken line. Standing back from the building and plotting the cracks can help with identifying the overall pattern of movement. The arrows indicate increase in widths of cracks.
METHODS TO REPAIR CRACK
- EPOXY INJECTION
Epoxy injection is an economical method of repairing non-moving cracks in concrete walls, slabs, columns and piers a sit is capable of restoring the concrete to its pre-cracked strength. The technique generally consists of establishing entry and venting ports at close intervals along the cracks, sealing the crack on exposed surfaces, and injecting the epoxy under pressure.
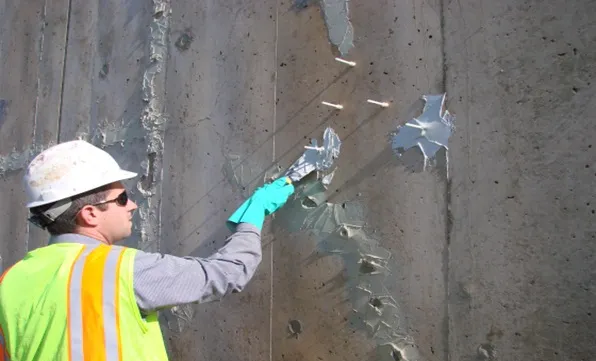
GRAVITY FILLING
Low viscosity monomers and resins can be used to seal cracks with surface widths of 0.001 to 0.08 in.by gravity filling. High molecular weight methacrylates, urethanes, and some low viscosity epoxies have been used successfully.
- GROUTING AND SEALING
In this method, the crack is made wider at the surface with a saw or grinder, and then the groove is filled with a flexible sealant. This is a common technique for crack treatment and it is relatively simple in comparison to the procedures and the training required for epoxy injection. Initially clean the surface; the surface should be free from paint, dirt, oil, efflorescence or any bond inhibiting agents. Then apply epoxy. To prevent epoxy flowing out insert a foam breaker or rod of suitable diameter and sealant is applied to it.
- STITCHING
This method is done to provide a permanent structural repairs solution for masonry repairs and cracked wall reinforcement. It is done by drilling holes on both sides of the crack, cleaning the holes and anchoring the legs of the staples in the holes with a non-shrink grout.
- DRY PACKING
It is the hand placement of a low water content mortar followed by tamping or ramming of the mortar into place and also helps in producing intimate contact between the mortar and the existing concrete.
- POLYMER IMPREGNATION
Monomer systems can be used for effective repair of some cracks. A monomer system is a liquid consisting of monomers which will polymerize into a solid. The most common monomer used for this purpose is methyl methacrylate.
- UNDERPINNING
This is the best solution whereby the footings of the building are underpinned with either concrete, masonry or piles to carry the load of the building down to a more stable stratum (e.g. rock or soils below the reactive zone).This solution is usually the most costly, particularly if there are access difficulties or if internal walls require underpinning, which may require lifting internal floors.
CONCLUSION
The cracks can be controlled if proper consideration is given to construction material and method to be used for its repairing.