Chloride-induced corrosion occurs when chloride ions, often from de-icing salts, seawater, or polluted environments, penetrate concrete and reach the steel reinforcement. These chlorides break down the passive oxide layer that protects the steel, allowing it to rust. The expansion of the rust causes the concrete to crack, spall, and deteriorate, compromising the structural integrity of the building. This corrosion is especially problematic in coastal areas and environments exposed to high levels of chloride.
Chloride-induced corrosion typically occurs in :
- Roadways and Bridges: In regions that use de-icing salts during winter, which can infiltrate concrete structures like bridges, overpasses, and roadways.
- Marine Structures: Such as docks, piers, and seawalls, where constant exposure to seawater accelerates chloride penetration.
- Industrial Facilities: Where chemicals or pollutants containing chloride are used or stored, leading to corrosion in nearby concrete structures.
- Underground Structures: Including parking garages or basements, where high humidity levels combined with external chloride sources can lead to corrosion.
- Water Treatment Plants and Sewer Systems: In areas exposed to chloride-containing wastewater or other industrial discharges.
Causes of Chloride-Induced Corrosion:
- Penetration of chloride ions from deicing agents.
- Exposure to seawater, which contains high levels of chloride.
- Industrial pollutants that contain chloride compounds.
- Poor concrete mix or insufficient cover over steel reinforcement.
- High moisture content in concrete, which accelerates chloride diffusion.
- Inadequate curing or aging of concrete, making it more permeable to chlorides.
- Use of recycled aggregates containing chloride traces in concrete mixes.
- Inadequate sealing of concrete surfaces, allowing chloride ions to enter.
- Water leakage from nearby sources, bringing chloride ions into the concrete structure.
- Insufficient thickness of concrete cover over the reinforcement.
- Aging of protective coatings or corrosion inhibitors.
Signs of Chloride-Induced Corrosion:
- Cracks in concrete near reinforcement.
- Spalling or flaking of concrete.
- Rust stains on concrete surfaces.
- Exposed or corroded reinforcement.
- Hollow sound when tapping concrete.
- Efflorescence on concrete surfaces.
- Moisture accumulation or wet spots.
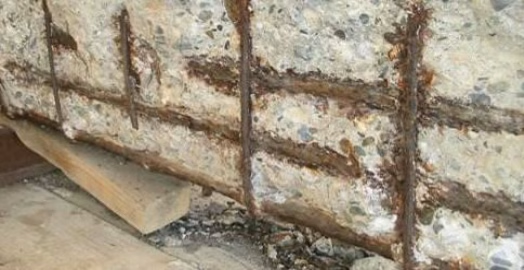
Types of Chloride-Induced Corrosion:
1. Uniform Corrosion
Uniform corrosion occurs when chloride ions penetrate the concrete evenly, leading to consistent rust formation along the surface of the steel reinforcement. This type of corrosion generally progresses at a steady rate, causing a gradual reduction in the cross-sectional area of the steel. While less severe than localized corrosion, uniform corrosion can still weaken the structure over time if left unaddressed. It is commonly seen in environments where chloride exposure is widespread and evenly distributed, such as marine atmospheres.
2. Pitting Corrosion
Pitting corrosion is a localized form of damage where small pits or cavities form on the steel surface due to concentrated chloride ions in specific areas. This type of corrosion is particularly dangerous as it can lead to rapid deterioration of the steel reinforcement while leaving the rest of the surface relatively unaffected. The pits act as stress concentrators, increasing the likelihood of structural failure. Pitting is difficult to detect in its early stages and often progresses unnoticed until significant damage has occurred.
3. Crevice Corrosion
Crevice corrosion develops in narrow gaps or crevices between the steel reinforcement and the surrounding concrete, where chloride ions can accumulate. These confined spaces create an oxygen-depleted environment, which, combined with high chloride concentrations, accelerates the corrosion process. Common areas for crevice corrosion include construction joints, interfaces between dissimilar materials, and locations with poor compaction of concrete. It can severely affect the structural integrity of the component if not addressed.
4. Galvanic Corrosion
Galvanic corrosion occurs when dissimilar metals, such as steel and aluminum, are in contact within a chloride-rich environment. The presence of an electrolyte, such as water containing chloride ions, creates an electrochemical reaction, leading to the accelerated corrosion of the less noble metal. In reinforced concrete structures, this type of corrosion is typically seen in cases where different types of embedded metals are used, and it can significantly shorten the lifespan of the structure if preventative measures are not implemented.
5. Stress Corrosion Cracking (SCC)
Stress corrosion cracking occurs when tensile stress in the steel reinforcement combines with chloride-induced corrosion, resulting in cracks along the steel. This type of corrosion is particularly concerning as the cracks can propagate rapidly, compromising the structural integrity of the reinforcement and, ultimately, the entire structure. SCC is more common in prestressed and post-tensioned concrete structures, where the reinforcement is under constant tensile stress.
6. Microbially Influenced Corrosion (MIC)
Microbially influenced corrosion is a type of chloride-induced corrosion accelerated by microbial activity, often in environments like marine or industrial structures. Certain microorganisms produce aggressive byproducts, such as acids or sulfides, that increase the corrosion rate of steel. In chloride-rich environments, these microorganisms thrive, leading to faster deterioration of the reinforcement. MIC is challenging to address because it involves both chemical and biological factors, requiring specialized treatment and monitoring.
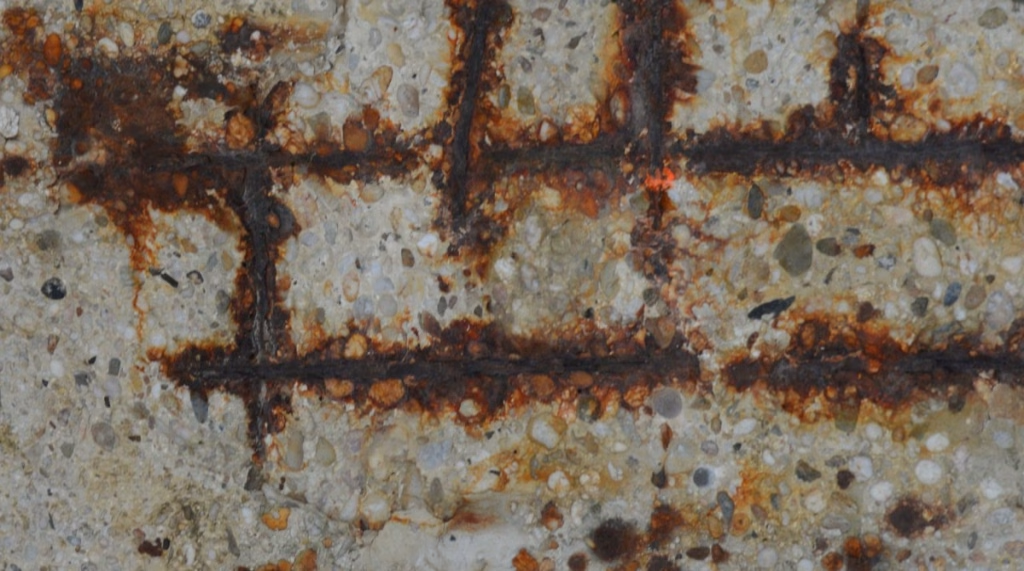
Ways to Address Chloride-Induced Corrosion:
- Use materials such as stainless steel or epoxy-coated reinforcement bars that resist chloride penetration and corrosion.
- Utilize alternative reinforcement materials like glass fiber-reinforced polymer (GFRP) bars, which are non-corrosive.
- Provide adequate concrete cover over the reinforcement to reduce the ingress of chloride ions.
- Ensure high-quality compaction and curing for better concrete density and reduced permeability.
- Add chemical admixtures, such as calcium nitrite, to the concrete mix to prevent or delay the onset of corrosion.
- Use advanced inhibitors that neutralize chloride ions or enhance the protective oxide layer on the steel.
- Apply surface sealers or coatings, such as silane or siloxane-based sealers, to prevent chloride ingress.
- Coat reinforcement bars with epoxy, zinc, or other protective materials before embedding them in concrete.
- Opt for concrete with a low water-to-cement ratio to reduce porosity and permeability.
- Include supplementary cementitious materials like fly ash, slag, or silica fume in the mix for enhanced durability.
- Install cathodic protection systems that prevent the steel from corroding by supplying a protective electric current.
- Use sacrificial anodes or impressed current systems depending on the structure’s requirements.
Conclusion
Chloride-induced corrosion is a major issue for concrete structures exposed to salts, seawater, and industrial pollutants. By identifying the signs early and using protective measures, the impact of this corrosion can be minimized, ensuring the longevity and safety of the building and structure.