Soil compaction is necessary to increase the bearing capacity and stiffness of soil. The method increases the shear strength of soils by adding friction from the interlocking of particles. With the method the future settlement of soils is also reduced by increasing the stiffness and eliminating voids. Soil compaction equipment is used in soil to compact varying soils, reduce the void ratio and increase soil density.
Features of soil compaction equipments
Newer compaction equipment combines existing features with intelligent compaction technology. It has great compaction output while offering improved efficiencies and cost savings as well. These are suitable for compaction of a wide range of soils, from silt to crushed stones.
Different types of soil compaction equipment are being used to compact varying soils and aggregates in applications such as highways, utilities, water retention structures, as well as in large residential, commercial and industrial site preparation. The latest soil compactor delivers all your compaction needs and includes features that help you tackle even the most demanding jobs.
There is demand for compaction models that can deliver higher productivity, quicker compaction, better paving quality and surface finish, along with faster project completion. Discussed below are different types of compaction equipments.
The newest soil compactors come with drum drive-type propulsion for use on steep job sites, such as building levees or dykes, and slippery or poor under-wheel site conditions. Newer models can ride on steep inclines and slippery surfaces. The traction system delivers optimum gradeability and prevents tire spin.
The controls are easy to reach and include a propulsion control lever for enhanced precision and control. A heavy-duty steel sunshade protects operators against the elements and in the unlikely event of a machine roll-over.

Soil compaction equipment types
Pneumatic tyred rollers
Pneumatic tyred rollers now come with optional traction control that boosts productivity on tough terrain. The proven hydrodynamic propulsion system ensures productivity. Traction force can be adjusted electronically, which leads to fuel efficiency. The hydrostatic models enable particularly smooth starts and stops. These rollers provide a kneading and sealing effect for job sites, increasing productivity on tough terrain. The rollers provide the kneading and sealing effect for job sites increasing productivity on tough terrain.
The pneumatic tyred rollers perform on both aggregates and asphalt, offering flexibility with air pressure adjustment features. Ballast packages can easily be added or removed to ensure the most efficient machine and process are provided. can be used on several different projects, such as subdivision streets, large parking lots, and driveways. Operators would find the machine easy to control as it is very user-friendly and easy to operate, it comes with a spacious cab. Everything can be easily managed by the operator through a control operation station.
The pneumatic tyred rollers perform on both aggregates and asphalt, offering flexibility with air pressure adjustment features. The newer pneumatic roller models are built on a hydraulic transmission system, which simplifies steering and on-off operations. A single pump, single motor transmission system with steady speed adjustment poses no impact on road material.The latest models can be used on several different projects, such as subdivision streets, large parking lots, and driveways.
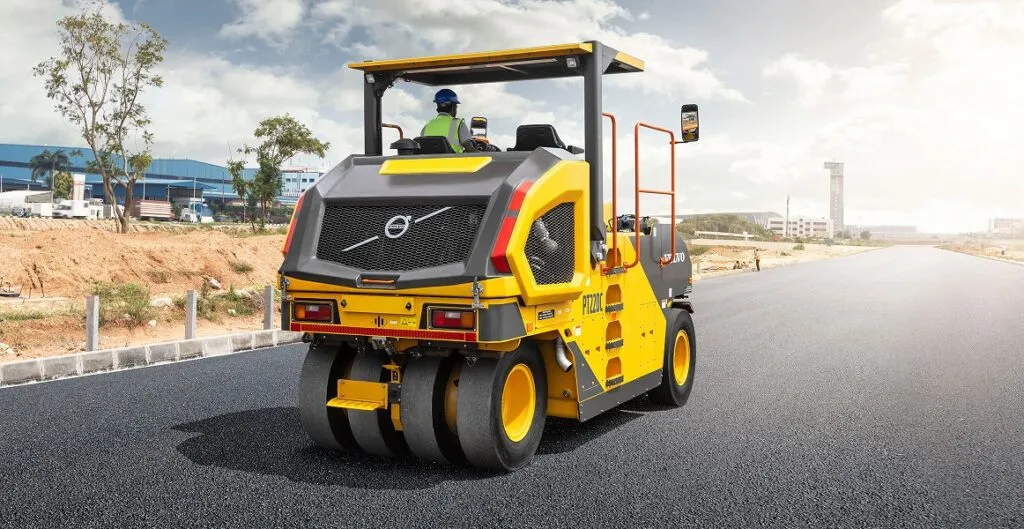
Tandem vibratory roller
Latest range of tandem rollers comes with an automatic compaction assistant. Smart compact technology actively supports the operator by combining the simple operation with handling via smartphones, computers, and other digitally controlled devices. The automatic mechanism sets compaction parameters for each drum, then the operator enters whether a base, binder, or asphalt surface course is to be compacted.
Smart Compact decides automatically whether to compact with vibration and big or small amplitude, with oscillation, or statically. The oscillatory movement of the drum in the newer models can also improve surface smoothness, by re-aligning the material. There is also a Self-regulating system embedded in the machines for automatic adjustment of amplitude based on stiffness.
It is best suited for applications such as highway road shoulders, retaining the walls of flyovers, footpaths, trenches, service roads, industrial and residential columns, rural roads.
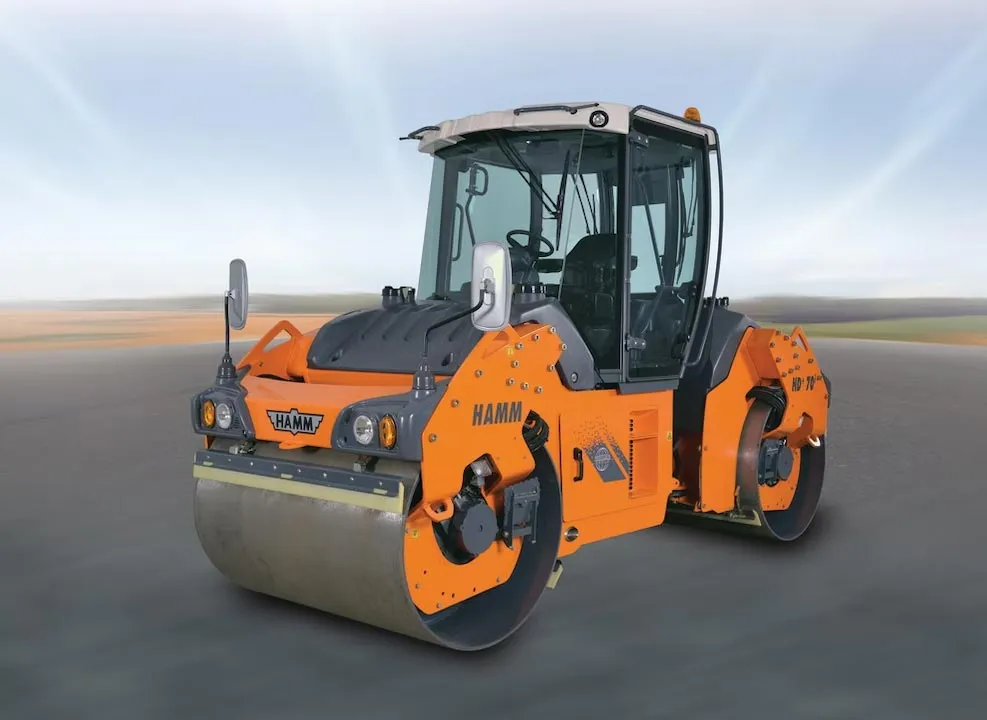
Drum vibratory rollers
Modern drum vibratory rollers enable superior operation around corners, over bumps or dips, and in confined areas. The front drums of the small rollers are positioned about two inches off-center from the back drum, allowing for a tighter turning radius, while both drums have a balanced design and a tapered edge to reduce tearing around curves and during transitions.
The latest models drive the propulsion system. The compaction performance is further enhanced with an oscillating articulated roller joint that maintains consistent drum-to-ground contact, and an updated drum design that reduces drift and maintains constant compaction throughout each rotation.
Standard dual frequencies and amplitudes, along with standard auto vibration control, let the operator set compaction performance based on the type of material and the depth of lift, reaching desired compaction in fewer passes, and ultimately improving productivity and reducing wear and tear on the equipment.
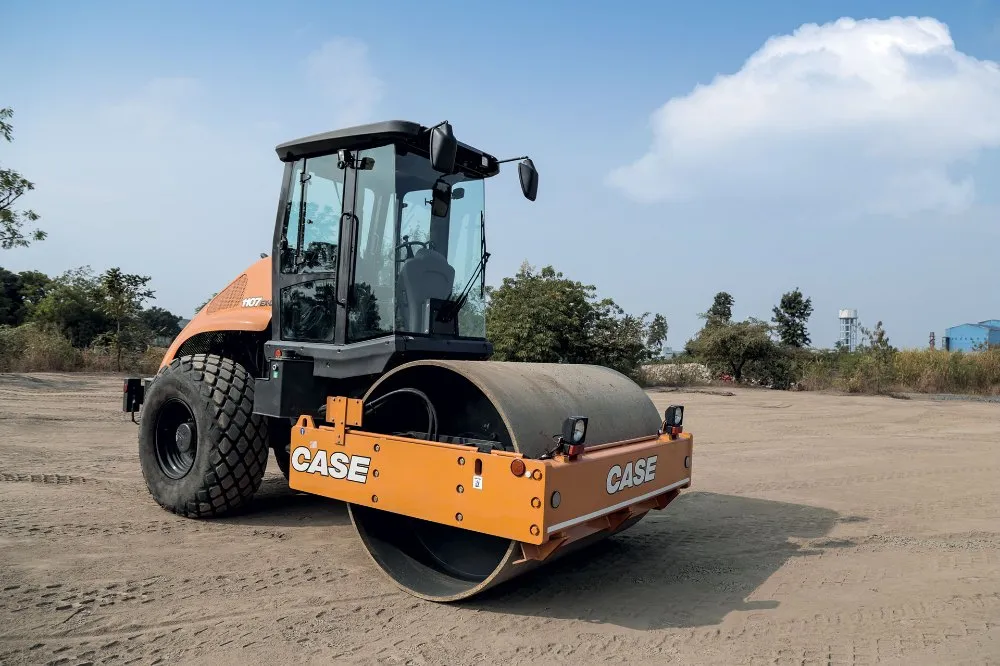
Conclusion
India’s compaction equipment market is expected to witness significant growth over the coming years on account of several upcoming projects, such as the expansion of public infrastructure. The rise in construction in smart cities is a major driver for the market. The massive investments made by governments to improve infrastructure are driving the demand for compaction equipment. There are numerous ongoing and upcoming projects for roads and dams which will further spur the demand for compaction equipment.