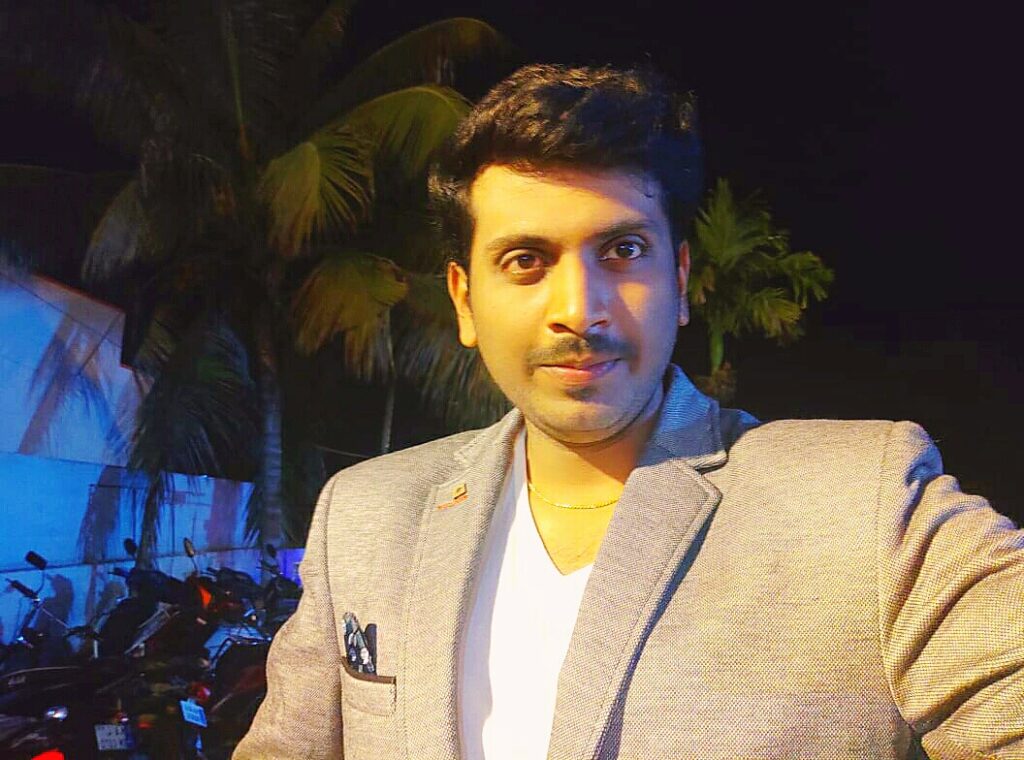
The construction industry is India’s most significant economic sector as highlighted in the 11th five-year plan. It accounts for nearly 11% of India’s GDP and plays a crucial role in the country’s development. In today’s globalized era, speed and efficiency are vital for meeting the stringent deadlines required to complete projects on schedule. This urgency is pushing various sectors, including construction and real estate, to seek competitive advantages.
Despite the rapid growth and development in India’s construction sector, many less developed countries do not place as high a value on time as Western countries do. This creates a massive opportunity within India, especially for newcomers in the prefabrication (prefab) sector. As urban areas expand, the use of prefab concrete components manufactured in factories for building houses and commercial structures is becoming increasingly appealing. Prefabricated construction offers numerous benefits, such as cost, time, material, and labor savings, in addition to ensuring consistent quality.
Prefabrication involves the manufacturing and preassembly of components, elements, or modules before their installation at the final site. This industry serves as the foundation for developing innovative construction ideas in any country. While popular in many foreign countries, India has shown some reluctance toward adopting prefabrication. However, its advantages are becoming more recognized, and many developers, builders, and contractors are gradually embracing it.
Despite its benefits, prefabrication has not yet overtaken conventional construction methods in popularity. Prefabricated materials can reduce construction time by as much as 50 percent and simplify the construction process. Although these materials are more commonly used abroad, in India, their use is primarily limited to large projects in major cities, such as elevated expressways and metro rail projects, or by major housing companies like Tata Housing and L&T in cities like Bangalore, Pune, and Mumbai. Prefabrication is still rare in rural areas, indicating significant growth potential in these regions.
This article deals with the views of the Indian construction industry on prefabrication and the barriers that are restricting it to enter the industry. It includes questionnaire survey to uncover the barriers to the development of this technology.
OBJECTIVES OF THE STUDY
- Offsite construction benefits
- Impact of Prefabrication
- Analyse prefabrication policies adopted in foreign countries.
- Address Indian construction industry on prefabrication.
- Pointing out the major barriers which hinder the progress of prefabrication technique in India.
METHODOLOGY
A. LITERATURE REVIEW
A literature survey is done on the prefabrication technique, its impact in construction industry and barriers that restricts the entry of prefabrication technique in India. And it is being analyzed well and found out various findings that could overcome the barriers and how the construction productivity does improve. Also found out how different countries affected the impact of off-site construction.
B. CASE STUDY AND VISITS
Case studies can be produced by following a formal method. These case studies are likely to appear in formal research venues, as journals and professional conferences, rather than popular works. The resulting body of ‘case study research’ has a prominent place in many disciplines, professions in construction fieldA questionnaire survey of construction organizations including client, designers, contractors, offsite suppliers and manufacturers is prepared.
C. QUESTIONNAIRE DESIGN
The questionnaire comprises of 3 parts. The first part was designed to collect the basic information regarding the respondents company type, position, years of experience, whether they had been engaged in prefabrication projects. The second and third part consisted of list of factors of advantages and barriers for adopting prefabrication. The fourth part consisted of strategies to overcome the barriers to prefabrication and it was divided into two; 1st part consisted of list of factors of strategies and supports from Government to (benefit company’s utilization) promote prefabrication, and the 2nd part consisted of list of factors of logistical barriers to prefabrication adoption. The fifth part was designed to know the current uses of prefabrication in the respective organization such as how often they used prefabrication technology in their projects and also what forms of prefabrication were used by the company.
ANALYSIS METHOD
In this article Likert scale was used. Likert scale is used to gauge attitudes, values and opinions. It allows the individual to express how much they agree or disagree with a particular statement. The respondents were asked to evaluate the degree to which the factor using five-point Likert scale.
The multi-choice answers comprised ratings from 5 to 1 on the level of importance.
- Most important = 5
- Important = 4
- Neutral = 3
- Less important = 2
- Least important = 1
A snowball sampling technique was adopted to obtain responses. Similar technique was used in the studies by this method enables the collection of information from respondents through social networks. The questionnaire quantitative data analysis was done by using Microsoft Excel and the following statistical tool was used
A. MEAN SCORE METHOD
It was used to rank the relative importance of specific factors. In this research it is used to determine the relative ranking, as perceived by the respondents. If two or more factors happened to have the same mean score, the one with lowest standard deviation (SD) was assigned a higher rank.
B. CRONBACH’S COEFFICIENT ALPHA
It was used to measure the internal consistency among the various factors to evaluate the reliability of the fivepoint scale. The value obtained if higher than 0.5 thresholds, indicating that five-point scale measurement was reliable at 5% significance level.

RESULTS AND DISCUSSIONS
A total of 155 questionnaires were distributed. All questionnaires were sent to the respondents with a request for them to forward the questionnaire’s link to their colleagues or to other experts who are experts with basic knowledge and understanding of prefabrication technology. Valid opinions were gathered using this approach to data sample collection.
Out of the 155 questionnaires sent out, 65 were returned with valid responses, accounting of response rate 42%. Of these sample group responses were from contractors (52%), consultants (architectural and structural) (28%), client (11%), manufacture and suppliers (1%) and others include builder, real estate firm and project management consultants.






CONCLUSION
Prefabrication is a manufacturing process; generally taking place at a specialized facility, in which various materials are joined to form a component part of the final installation. This thesis presented the views of the respondents working in construction industry on prefabrication. Survey conducted for this thesis was mainly answered by respondents from Kerala and rest was from L&T, Total environment building systems, Shapoorji Pallonji Constructions etc. Majority of the respondents of this survey have experience between 2 to 5 years and also out of 65 respondents only 16 respondents said yes to the experience in prefabrication field. This indicates that there is no much significant usage of prefabrication technology in less developed areas. But from various news articles it was found that there is considerable progress in prefabrication even though the progress was very few, such as incorporation of prefabricated housing in government own buildings, hospital, school etc.
The main advantage of prefabrication is saves construction time, reduces construction waste, together with increased quality. The main barriers obtained from the survey were improper transportation facilities, logistical limitations to design and also prefabrication is more expensive than traditional construction method. This is because our society is mainly focused on cost effective construction and the fact that ‘time is money’ has little weight in less developed areas. Since the technology is not widely used we had to depend on factory sites which are far, as a result transportation cost increases, logistical limitations for design comes, and simultaneously construction cost also increases. For prefab more skill and advanced technology is required, and also proper training is to be given. The main innovative ways to improve the up taking of this technology is by creating awareness, for this Government, bureaucrats; all have to come forward. By ensuring finances and insurance, collaborating industries and academia for training, training within the industries, standardization of components which also increase the confidence about prefabricated components among Indian construction industry and public.
About the author
The author is the Managing Director at Skanda Group of Constructions. He is an experienced Civil Engineer with a demonstrated history of working in the construction industry. He is skilled in AutoCAD, Construction, Management, Concrete, and Structural Analysis.