Precast concrete is produced by casting concrete in a reusable mold or “form” which is then cured in a controlled environment, transported to the construction site and lifted into place. Precast is used within exterior and interior walls. By producing precast concrete in a controlled environment (typically referred to as a precast plant), precast concrete is afforded the opportunity to properly cure and be closely monitored by plant employees.
Using a precast concrete system offers many potential advantages over onsite casting. Precast concrete production can be performed on ground level, which helps with safety throughout a project. There is greater control over material quality and workmanship in a precast plant compared to a construction site. The forms used in a precast plant can be reused hundreds to thousands of times before they have to be replaced, often making it cheaper than onsite casting when looking at the cost per unit of formwork.
Benefits of precast concrete
It, a highly efficient, practical method of concrete construction makes beautiful buildings possible at a cost that rivals even the most utilitarian industrial building. Understanding some of the benefits of precast concrete will assist designers in evaluating the impact of precast concrete on the environment and the building operation. Some of its benefits are given below.
- It offers an efficient delivery model for your project; allowing building construction to proceed while the design is developed.
- It can take nearly any shape or size, be manufactured in virtually any color and comes in a wide variety of finishes. With precast, you are limited only by your imagination.
- Precast concrete products are manufactured off-site, under roof and are delivered ready to install when needed. This innovative process compresses project schedules, reduces safety concerns, reduces site disruption and reduces overall project costs by requiring fewer trades for construction and fewer people on site.
- Precast concrete structures provide superior resistance to fires, natural disasters, insects and mold. Like no other building material, its resistance to rain, wind damage, earthquakes, termites and decay provides lower maintenance and insurance costs. It can also withstand many winters of freeze-thaw cycles better than other building materials.
- Costs associated with heating and cooling can be greatly reduced through concrete’s thermal mass benefits. Reduced peak heating and cooling loads can be achieved because concrete reacts slowly to changes in outside temperature.
- The exterior of a precast concrete structure can be left unpainted without damage from the elements. If painting is desired, repainting is needed only every five to ten years. Precast concrete interiors are less subject to damage and easier to wash.
- Because of concrete’s density, precast buildings absorb sound making it an ideal choice for commercial and residential buildings.
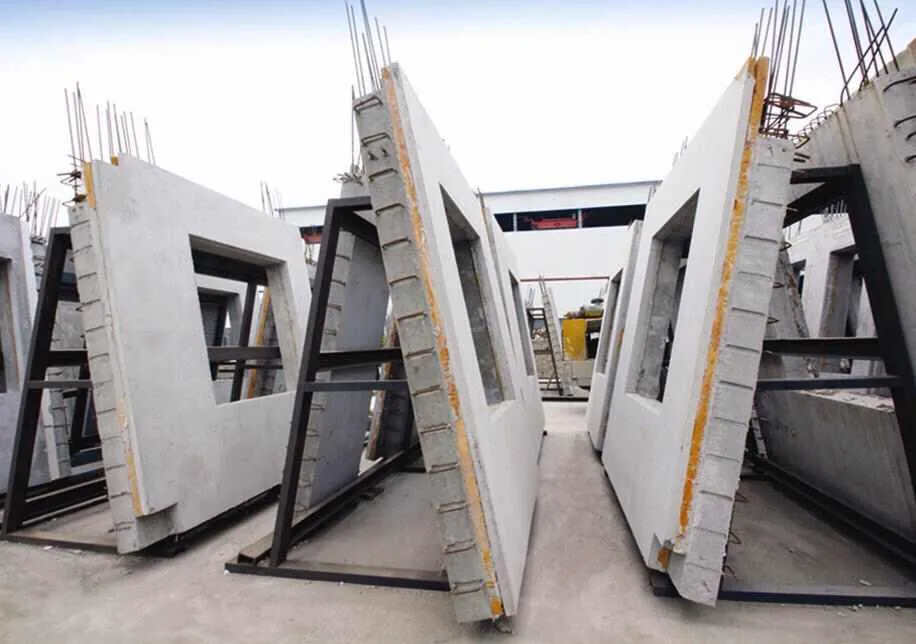
Precast concrete structural elements
A precast building is constructed by assembling and connecting various prefabricated elements required in the building structure. These elements are:
- Precast slabs
- Precast beams
- Precast columns
- Precast walls
- Precast foundation
Categories of precast building system
Depending on the load-bearing structure, precast systems can be divided into the following categories:
- Large-panel systems
- Frame systems
- Slab-column systems with walls
- Mixed system
Applications of precast concrete
Precast concrete sandwich wall panels have been used on virtually every type of building, including schools, office buildings, apartment buildings, townhouses, condominiums, hotels, motels, dormitories, and single-family homes. Although typically considered part of a building’s enclosure or “envelope,” they can be designed to also serve as part of the building’s structural system, eliminating the need for beams and columns on the building perimeter. Besides their energy efficiency and aesthetic versatility, they also provide excellent noise attenuation, outstanding durability (resistant to rot, mold, etc.), and rapid construction. In addition to the good insulation properties, sandwich panels require fewer work phases to complete. Compared to double-walls, for example, which have to be insulated and filled with concrete on site, sandwich panels require much less labor and scaffolding.
Precast vs cast in situ construction
Precast concrete or site cast concrete? This is a crucial question for anyone moving forward with a commercial building project. Depending on your particular needs, you may choose to go with one over the other. Because on site concrete pouring is custom to the build, it is incredibly versatile. However, it is also far more costly, labor intensive and time intensive. While precast concrete does have to be hauled to location, its unparalleled quality, affordability, and longevity make it stand out against its on-site competitors. Given below is a comparison of precast and cast – in- situ construction.
- It is poured and molded over rebar or wire and then cured offsite. This involves pouring concrete into pre-made molds and then cured under ideal conditions within the manufacturing plant itself. Once hardened and ready for use, those preformed concrete products are shipped to the job site where they are assembled into the desired structure. As opposed to precast, site cast, sometimes known as in-situ concrete, is poured, molded and cured on site. Like precast concrete, on site concrete is formed in a mold and then lifted in place.
- Precast & cast-in-situ concrete are the product produced by casting concrete in a mould or formwork cured to get the strength of RCC elements. The precast concrete is transported to the construction site, lifted and positioned at the predetermined place. The cast-in-situ concrete is a standard concrete which is poured into the specific formwork on the site and cured to get the strength of RCC elements.
- In the precast concrete elements are manufactured in a controlled casting environment and hence it is easier to control mix, placement and curing. Elements can be cast in advance and held until the hour you need them, thereby saves time. Weather condition has no effect on casting work. In the cast-in-situ concrete, column, slab etc. elements are cast on site in the open environment and hence it is difficult to control mix, placement and curing. Elements cannot be casted in advance. Weather conditions can delay the casting work.
- It is a cheaper form of construction if large structures are to be constructed. In situ concrete is cheaper form of construction for small structures.
- Precast concrete requires heavy machinery and cranes for handling i.e. lifting and installation of heavy elements. Skilled and technical contractor is required for construction of the precast concrete structure. Cast-in-situ concrete does not require such handling equipment, More labours are required for this at the construction site.
- Precast concrete construction is quick as it can be installed immediately and there is no waiting for it to gain strength. Increase in strength can be achieved by accelerated curing. In situ concrete construction is slow as gaining of strength requires time. Increase in strength at situ by accelerated curing is a difficult task.
- In Precast Concrete total construction time is less as compared to cast-in-situ.
- Precast concrete gives smooth interior finish hence they need minimum preparation before paint, wallpaper etc. or the other wall coverings can be applied directly. In the cast-in-situ concrete construction, you have to do plaster for the smooth finish and also requires pre-preparation for a paint like wall putty etc.
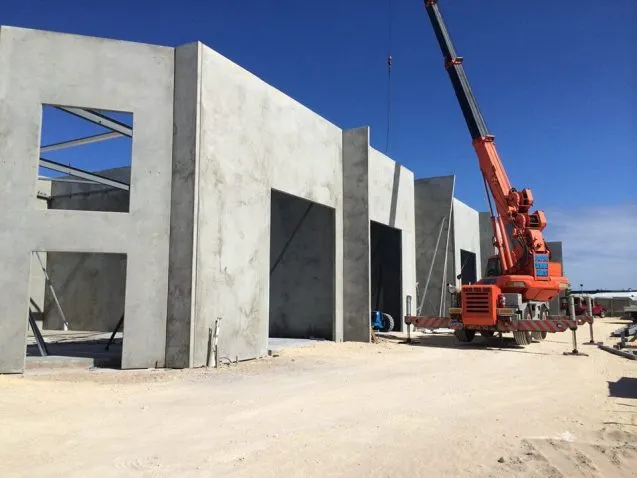
Conclusion
Precast construction requires a restructuring of the entire conventional construction process to enable interaction between the design phase and production planning in order to improve and speed up the construction. One of the key premises for achieving that objective is to design buildings with a regular configuration in plan and elevation.Ifyou choose precast concrete, you’re going to need to hire a precast concrete manufacturer. To maximize the benefits of precast concrete, you need a manufacturer that will have the capacity to produce the materials you need to get the job done and meet your specifications. Without a reputable manufacturer, some of the benefits of precast concrete construction are lost.