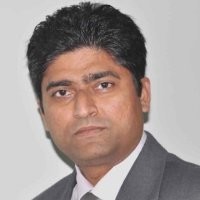
Liquid applied Polyurethane (PU) membrane is increasingly being used to replace conventional cement-based polymer coatings for waterproofing. However, the application practices have not fully evolved to harness the full benefits of PU, both in terms of effectiveness and economic efficiency. This issue is particularly pronounced in large projects such as residential apartments, commercial buildings, and infrastructure developments, where traditional methods still dominate despite the shift towards PU technology.
Differences in Properties Between PU and Cement-Based Systems
Building professionals are yet to fully understand the differences in properties of PU versus cement based systems. Many are still following the same old practices of surface preparation and testing which is usually followed in the case of cement based systems, for PU applications. This not only defeats the benefits; in most times it also works counterproductive.
Especially in the case of large projects such as residential apartments, commercial buildings, infrastructure, which involve too many stakeholders or influencers starting from the Consultant, client officials, main contractor staffs from departments such as QC, Planning, contracts, Project execution etc., application methods take a serious toll. PU has started fast replacing Cement based systems for waterproofing terraces, Podium and retaining walls etc., in the tender specifications as quality awareness is on the rise and leakages/dampness issues are still persisting in spite of huge expenditures in waterproofing. Worst affected builders apart from shifting from cement based systems to PU and other high end technologies, make the manufacturers and applicators legally responsible thro long warranties and tripartite agreements.
Surface Preparation and Application Methods
Builders and policy makers must come forward to understand that Application methods play a very important role in fetching best outcomes from their investments in waterproofing. With change in technologies, it must be understood that all associated environments and practices will also change. When we shift from Pencil to Pen writing, we must understand and accept that Erasing is not possible with Pen as we do with Pencil. We cannot enjoy the ease of writing with Pen, if we cannot compromise on the erasing advantage of pencil. In the industry, unfortunately all old practices associated with Cement based waterproofing are still grabbing PU too, not letting PU to deliver all its benefits.
Flexible Joint Treatments
With years of experience in the waterproofing industry, Waterproofing materials have to be “Flexible “and Not “Rigid”. It is necessary for the waterproofing system to accommodate movements in Construction Joints, expansion and contraction cycles of Concrete etc., Rigid systems however strong these are, tend to fail with large momentums from the concrete slabs.
Hence when the main waterproofing material chosen is flexible, even all the surface treatment materials used to treat construction joints, honey combs etc., need to be flexible too.
The best technology available as of today for treating construction joints is TPE based non-woven tapes. These tapes vary in their construction. Some are triply having a TPE tape sandwiched between two non-woven polyester fabric. Some have TPE coated on a non-woven fabric.
It is to be noted that a normal PU system alone cannot work well at construction joints as the tensile strength required is as high as 25N/MM2. Most commercially available PU have between 2 to 4 N/MM2 only. Hence a L shaped TPE tape (around 150 mm) affixed with the help of PU or any tape adhesive (epoxy or PU) will be good. Liquid Poly Urea having more than 25 N/MM2 tensile strength is even better as the application is easy (for hand applied polyurea).
Many use a v groove cut on the joint and apply Non shrink grout in horizontal to horizontal or vertical to vertical joints. This must be avoided as almost 90 percent of cases end in failure.
Primer and Main Layer Application
PU offers very good flexibility and durability in addition to many other merits. The PU membrane waterproofing system comes as a combination of Primer and the main layer.
It’s a common myth that Primer is a bonding agent. Well, yes but it does a lot more than mere bonding. While PU top membrane material is highly viscous, the primer is just the opposite.
Being low viscous, almost as low as water, it can penetrate deep into the concrete. At the same time, once fully cured, primers in the market today offer high tensile, flexural and compressive strength properties. Being also flexible, it stabilises the Concrete, prevents cracks and cavities from widening further over time. Behaviour of the mother slab has its effect on the top waterproofing membrane and hence any good membrane can fail if the concrete is not treated.
Now we need to understand how cementitious systems work. Manufacturers recommend “Semi saturated Dry” condition of the mother slab before membrane coatings are done. Without saturating the mother slab cavities with water, if membrane coating is applied, it will lead to two major issues.
One – the water component in the membrane will be sucked into cavities leaving the cement content of the top material not having sufficient water to react and hence a weak membrane is formed.
Two – The entrapped air in the cavities leaves a pinhole when it escapes from the cavities.
Hence it is obvious that any crack on the mother slab will also suck water from the main membrane leaving the membrane portion above the crack weak. This calls for treatment of cracks and porosity before application of the coating. Hence this also calls for testing for cracks and porosity using a hydro pond test. After the pond test, cracks and porous areas are identified and these are to be treated with various methods such as injection grouting, grooving of cracks and packing the same with polymer mortar. In spite of all these time and labour intensive repairs works and application of cement based coats, experience has proven that repair methods are not long lasting.
Injection grouting using cement slurry mixed with non-shrink grouting additives does mere filling of cavities and voids but does not offer strength to the mix. These grouts cannot withstand expansion and contraction of concrete and give up over time. The added grouting additive offers thixotropic and swelling properties only to the cement slurry, but not any strength.
Similarly, cracks treated with polymer modified grout or non-shrink concrete can give up when the stresses on the cracks are strong enough to break the grout. Flexible materials handle these far better.
Now let us come back to our PU. While the primer takes care of the concrete with its own flexible strengths, the top PU membrane being highly viscous and dense, remains firmly on top unlike the cement based where the water component is sucked into cavities and cracks. PU sits on top of the primer material which is also having its spread deep into concrete with all its strengths.
This eliminates the need for any crack or porosity treatment. Hence PU does not need a hydro test to identify cracks. Cracks up to 0.3 mm are well handled by primer and top PU combination. Cracks above 0.3 mm are unusual and hence needs to be considered as a structural issue.
Avoiding Moisture and Enhancing Wettability
There are two other concerns associated with PU.
Moisture Averse- Unlike cementitious materials, which demand the surface to be in SSD condition which is nothing but a moist surface, PU demands a moisture free surface. Ideally it is great if the entire concrete slab is dry. For practical purposes, most manufacturers recommend a moisture level of less than 4% at the surface level. It is better to use Meters which use electromagnetic waves to determine the moisture. These can detect moisture up to 25 MM depth.
Meters which use terminal pins which pass current and determine the moisture are not very accurate.
Having very less vapour transmission properties, membranes form bubbles and pin holes if applied on moist surfaces. This is another strong reason why hydro tests are to be avoided for PU.
Wettability – Being extremely viscous and dense material, when applied with a brush or a roller, the material does not reach the entire contours of the surface, it forms like a film over small cavities rather than getting into the cavities.
Brush or roller applied PU
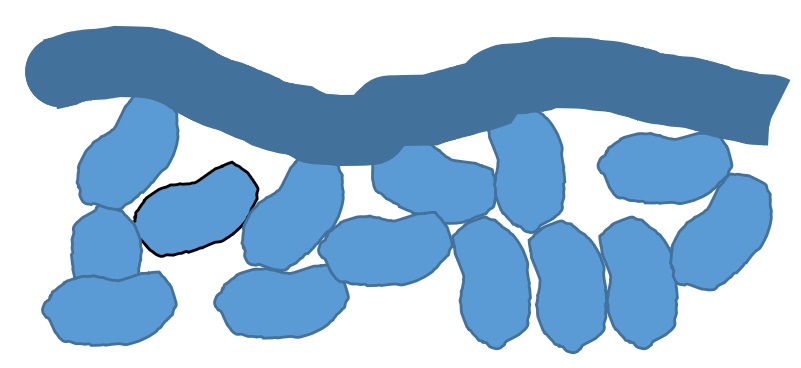
This demands for the usage of Airless spray machines.
PU must be sprayed with airless spray machines. When sprayed with very high pressure such as 7500 psi thro very small nozzles, the PU material is broken down into millions of droplets and each having a diameter of less nanometres. These droplets can easily enter any small cavity or a dent.
Spray applied PU
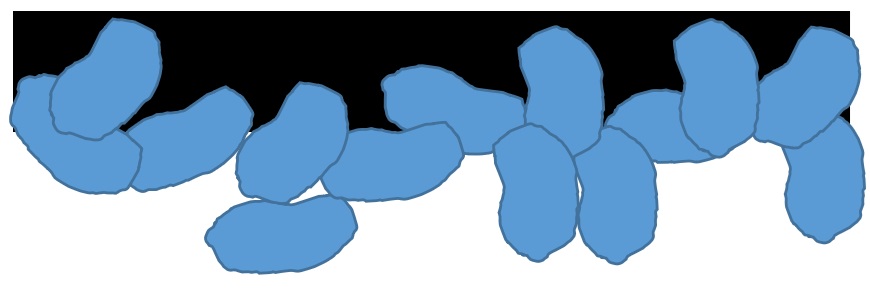
Prior to the application of PU, even the primer must be applied using the same sprayer. This facilitates the low viscous primer entering deep into the porous concrete and cracks and releasing any entrapped air.
Subsequent application of PU will create an excellent bond between the molecules of the Primer and the PU. Brush applied PU can be peeled with fingers. But spray applied PU forms a homogenous surface over the concrete surface. Once cured after seven days, it is impossible to separate Membrane alone from Concrete.
The manufacturer must be able to recommend the right capacity of the airless spray machine and its back up air compressor.
The next is, productivity advantage of using spray equipment.
In a day, 600 to 800 SQM single coats can be applied with the help of two spray men, one helper and a supervisor. Each coat including primer takes about minimum 24 hours to become fit enough to receive the next coat.
Hence PU application must be done in a minimum batch size of 800 SQM and above. the 800 sqm area can be completed in three working days without any wait time. Also the next batch must be ready to receive applications. Hence planning must be done to have a much larger area ready before we engage the spray application.
Scheduling and Planning
In many projects even today, planners tend to keep waterproofing applicators on standby while they take their cool time in preparing the work front. This increases the cost.
Many projects take almost one to even two months to complete 800 sqm of work.
A very effective schedule planning is required and this should be done jointly by all stakeholders such as client, main contractor, waterproofing applicator, other related contractors. For example, painting work may affect waterproofing works and vice versa.
The best time to do waterproofing of terrace or podium is the final stages of the construction when there is least dust, least worker footfall, no wet works, the place is completely dry and clean , free from stored construction materials, equipment etc.,
Let us see how many days it should take to complete 800 sqm of area having around 100 running metres of Construction Joints.
Day One: Three workers (One skilled and two unskilled)
Grind Construction joint undulations and chip out any loose mortar or concrete.
Day Two: Start with tape application
Day three and four: Complete joint treatment. (Surface grinding is required only to eliminate sharp projections. Natural surface undulation of concrete is fine.)
Day Five: Use compressed air to clean dust. Start primer application using airless spray and complete on the same day
Day six: Do First coat PU and complete
Day Seven: Do second coat PU and complete.
Day Eight to Day Fourteen: Air curing
Day Fifteen: After seven days of air curing, hydro test can be done. Even if leakage is noticed, it is easier to repair after PU is applied. A few overcoats should rectify the leakage.
The above procedure has clearly eliminated Pre ponding and testing, conventional crack repairs etc.,
The larger the area, the faster the work is. For example, surface preparation works can go in multiple areas (such as terrace, podium, swimming pool et,) simultaneously and spray application can be done in series one by one covering all areas.
But the conventional way of work execution still believes preparing smaller areas and completing and moving forward rather than preparing the entire area and spray apply the entire in one stretch.
Through the below illustration, let us understand how the effectively we can utilise our resources over a shorter time
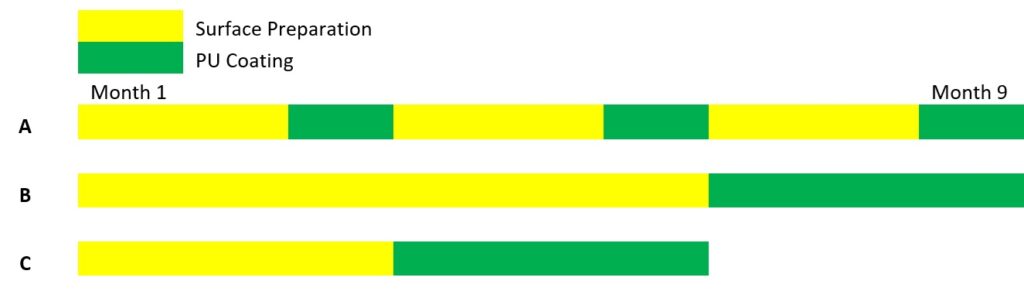
A is the current practice at most places. No professional schedule planning. Bring all material machines and contractors in advance. Make all work simultaneously. Show the client that the works have started early. But the truth is, work is going to get completed on the same day as the work if we had planned the schedule in a professional way. Material and machines are brought in advance and kept in standby. This increases the cost of idle resources.
B shows better planning. Material and the machine are brought in much later, on the 7th month and the work is complete by the 9th month i.e., Just In Time when the entire work front is ready
C is even better. Unnecessary and rudimentary practices in surface preparation are eliminated.
Apart from increasing coat, A leads to more quality issues. PU material must be stored under 25 deg cent. Most construction sites do not have such a facility. Hence it is important to bring the material just in time when the site is ready to apply. At higher temperatures and humidity, the material under property changes and hence results in poor cured properties. Sometimes the material solidifies choking the spray equipment. Special care must be taken when joints are made due to intervals between coatings. In case of rains, water seeps below the applied coat in the concrete from the un applied area, thus causing bubbles, de bonding etc.,
Dosage and Application Guidelines
Typically, 100 grams per square meter of Primer and 1.5 to 2 kgs per square meter of PU (depending upon manufacturer’s recommendations) in two coats will form approximately 1 mm dry film thickness. However, the primer dose may be increased to up to 250 grams in order to stabilise weaker concrete in old buildings. Minimum of 1 mm thickness is required. However, it is always advisable to have thickness around 1.3 to 1.5 mm to ensure waterproofing effectiveness.
Skill requirements:
The skill requirements for PU application is certainly much more than conventional cementitious waterproofing. The spray equipment demands a lot of care and daily cleaning of the fluid lines is mandatory. The operator of the machine must have special training to handle the equipment while the sprayers must have professional painting experience with exposure to spray equipment. Yet the machine, being subjected to very high pressure, breaks down often due to wear and tear, leading to failure of mechanical parts. A very good service support backup and spares logistics is essential.
Any process involves these five Ms. Material, Machine, Man, Method and Management.
Material – there are more than twenty-five players operating in India with a wide range of products and specifications.
Machine – The best of the spray equipment and associated tools are available. These are not Plug and Play. Requires expertise and a lot of maintenance. Machine needs to match the material.
Manpower – Skilled manpower are very few.
Method – Needs a relook. A lot of improvement is required
Management – Execution Management must engage professional task scheduling techniques. Old school firefighting techniques must be shelved.
Conclusion
To fully leverage the benefits of Polyurethane waterproofing, the industry must adopt new methods and practices tailored to PU’s unique properties. This involves updating surface preparation techniques, employing the right materials and machinery, and ensuring skilled application and effective management. Only through such comprehensive changes can the full economic and functional advantages of PU waterproofing be realised, ensuring long-term durability and effectiveness in large-scale construction projects.
About Author
The author is a seasoned consultant and contractor specializing in waterproofing and insulation works. With over 30 years of experience in multidisciplinary project management, the author combines engineering expertise with practical know-how to deliver effective solutions in the construction industry.
Email Id: uranuschemicals@gmail.com