Steel bar is a non-ferrous metal that can be further exposed and subjected to different elements in the environment. Through galvanization and application of a protective coating of zinc on steel, it would be able to better withstand corrosion. Galvanized steel reinforcement bars serve as a barrier to the corrosive environment to which the bars are exposed when embedded in concrete. It creates a protective coating that shields the metal from the surrounding environment. The layer of zinc prevents water and moisture and other elements in the air from corroding the steel underneath. It can also protect the metal from galvanic corrosion. It occurs when two metals of a different electrochemical makeup are placed into contact with one another with an electrolyte present, such as salty water. Depending on the atomic structure of the two metals, one metal is the anode and the other is the cathode. The anode corrodes more rapidly than it would by itself and the cathode corrodes at a slower pace than it would by itself. The reason zinc is used for galvanizing is that it has an affinity towards being the anode when in contact with many different types of metals.
Different methods of Galvanization of Steel Reinforcement Bars
There are different methods of galvanization which differ from one another in terms of the material used, the thickness, as well as the type of processes that are included.
Hot-Dip Galvanizing
The hot-Dip Galvanizing method involves dipping the base metal into a molten pool of zinc. The three main steps in the hot-dip galvanizing process are surface preparation, galvanizing, and post-treatment. First, the base metal must be cleaned either mechanically, chemically, or both to assure a quality bond can be made between the base metal and the zinc coating. Once cleaned, the base metal is then fluxed to rid it of any residual oxides that might remain after the cleaning process. The base metal is then dipped into a liquid bath of heated zinc and a metallurgical bond is formed. This molten bath begins a metallurgical bond between the zinc and the receiving metal. After the metal is pulled from the bath, it reacts to being exposed to the atmosphere, and the pure zinc mixes with oxygen to form zinc oxide. A reaction then transpires between zinc and oxide particles in the air, making the final zinc-oxide protective layer. The benefit derived from this specific method is considered to be economical and can be quickly performed to complex shapes. Hot-dip galvanizing process continues to evolve with new technologies.

Electro galvanizing
Electro galvanizing method utilizes an electrical current in an electrolyte solution to transfer zinc ions onto the base metal. This involves electrically reducing positively charged zinc ions to zinc metal which are then deposited on the positively charged material. Grain refiners can also be added which helps to ensure a smooth zinc coating on the steel. Electro galvanizing is typically applied continuously to a roll of sheet metal. The most common zinc electrolyte-anode arrangement uses lead-silver or other insoluble anodes and electrolytes of zinc sulfates. Soluble anodes of pure zinc are also used. The coating develops as positively charged zinc ions are electrically reduced to zinc metal and deposited on the positively charged cathode. The method provides a uniform coating and precise coating thickness.

Pre-galvanizing
Pre-galvanizing is used for the steel mill, usually on materials that already have a specific shape. This method involves metal sheets being rolled through a cleaning process, which is similar to the hot-dip galvanizing procedure. Then, this metal is passed through a pool of liquid hot zinc to recoil. A major benefit derived from this particular method is that steel sheets in large coils could be galvanized within a short period having a more uniform coating. An advantage of this method is that large coils of steel sheets can be rapidly galvanized with a more uniform coating compared to hot-dip galvanizing.

Mechanical plating
The mechanical plating process imparts coating by cold welding fine metal particles to a workpiece. It is done by tumbling small parts in a drum with zinc and proprietary chemicals. Small iron and steel parts usually limited in size to about 8-9 inches and weighing less than one pound are cleaned and flash copper-coated before loading into a plating barrel. The barrel is then loaded with proprietary chemicals, glass beads and zinc powder and tumbled. During tumbling, the glass beads peen zinc powder onto the part. Once finished, the parts are post-treated with a passivation film, dried, and packaged.
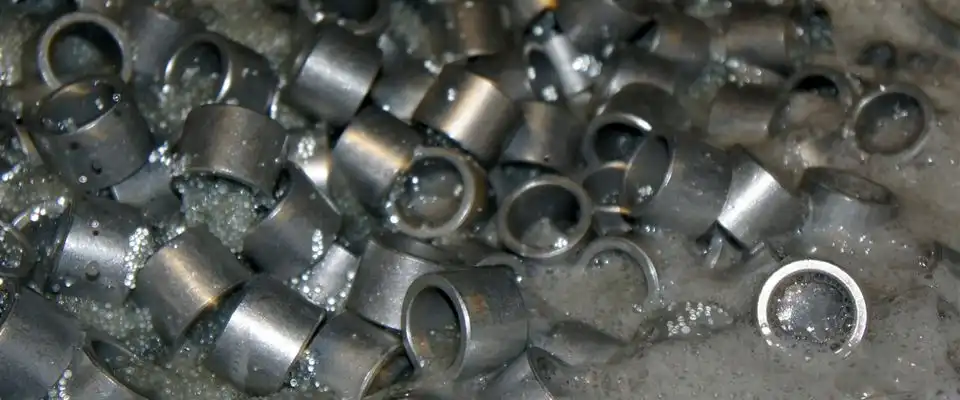
Inline galvanizing
The inline galvanizing method involves feeding the tubing through a bath of molten zinc and then applying a conversion coating to prevent the formation of naturally occurring zinc oxide and hydroxide. A clear, inorganic, topcoat usually is applied over the conversion coating. Only the outside of the tubing goes through this process; the tubing’s inside surface receives only a coating of zinc-rich paint. This method allows accurate control of coating thickness, ductility and other characteristics of the zinc coating. In-line galvanized methods help to produce thinner coatings than batch hot-dip galvanizing for the same steel thickness. They can usually be further processed by bending or roll forming, for example as purlins and girts, without damaging the coating. In addition, welded hollow sections formed from pre-galvanized strips are in wide use.
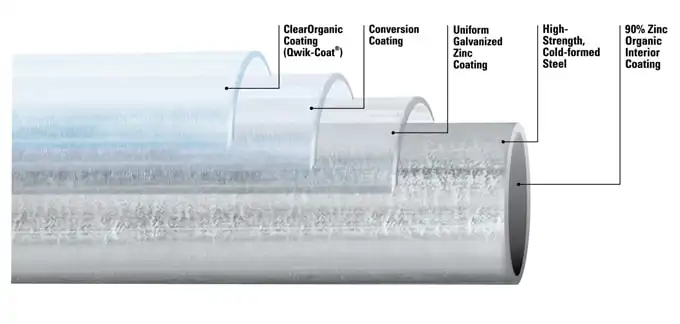
Sheet galvanizing
Sheet galvanizing is also a hot-dip process applied to steel sheets, strips, and wire. Preparing the steel for the continuous galvanized coating begins with cleaning in an alkaline liquid combined with brushing, rinsing, and drying. Then the steel passes into the heating or annealing furnace to soften it and impart the desired strength and formability. In this annealing furnace, the steel is maintained under a reducing gas atmosphere, composed of hydrogen and nitrogen, to remove any oxide that may be on the surface. The steel then exits the furnace, entering into a vacuum chamber, or snout, before entering the molten zinc bath to prevent air from reoxidizing the heated steel product. The steel is then sent around a submerged roll in the molten bath to create the bonded coating and removed in a vertical direction. As the product is withdrawn from the bath, precisely regulated, high-pressure air (air knife) is used to remove any excess zinc to create a closely controlled coating thickness. The steel is then allowed to cool and solidify before application.

Applications of Galvanized Steel Reinforcement Bars
Galvanized steel is widely used in applications where corrosion resistance is needed without the cost of stainless steel and can be identified by the crystallized pattern on the surface. Galvanized steel is widely used in the construction industry, wind & solar industries, automotive industry, telecommunication industry to name a few.
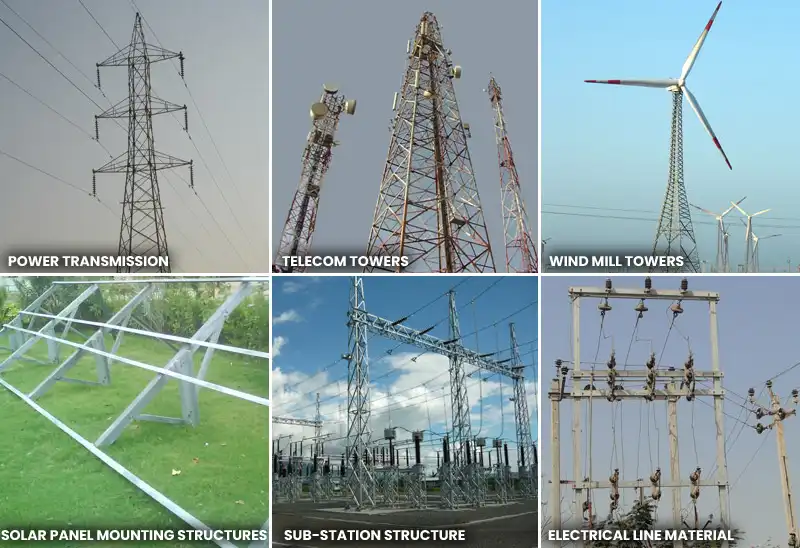
Conclusion
Discussed above are the different methods of steel galvanization. Each method comes with different mixes and attributes. In an upcoming article series, we will discuss in brief each method’s advantages and applications.
Project Image courtesy: Vishal Engineers & Galvanizers Pvt. Ltd.