Heavy machinery and rotary equipment cannot simply be installed on a concrete foundation since irregularities in both the machine base and concrete surface will create load-bearing issues and alignment difficulties. Additionally, a concrete foundation is not tough enough to withstand the compressive and dynamic loading needed to support the heavy machinery. For this reason, machinery bases are aligned and leveled by shims or jack bolts above the mechanically prepared concrete foundation and the resulting space between the machine base is filled with Engineering Grout (Industrial Grout) for load and energy transfer from the equipment into the foundation. The primary purpose of grout under machine base plates is to maintain structural integrity with the foundation for as long as the machine is operable.
The grout must be fluid enough to be poured or pumped under the baseplate to fill this space and must also maintain its volume throughout the service life of the equipment to ensure intimate contact between these surfaces for maximum load-bearing capability. Additionally, the grout must exhibit the necessary mechanical properties such as high ultimate compressive strengths over a variety of applications and service temperatures. One of the challenges of quality machinery grouting is a proper material selection for lasting security, stability and alignment of the critical equipment it supports.
Selecting the right grout material and using the correct placement technique is critical to machine alignment, integrity, and longevity.
Types of Machine Base Plate Grouting
Understanding the type of compressive load, uplift, shear, and vibration between the machine and its foundation will determine the type of grout needed under a machine’s baseplate based upon performance characteristics. Dynamic loads are associated with reciprocating equipment, motors, generators, turbines etc. Static loads are associated with columns or non-moving equipment.
A precision non-shrink grout does not exhibit any plastic or hardened shrinkage at any time. Precision non-shrink cementitious grouts are designed for static or light dynamic loading, or for high temperature exposure. Precision non-shrink epoxy grouts are designed for heavy dynamic loading from vibration or impact or for applications requiring good chemical resistance and high compressive strength, like large and heavy rotating machines.
Selection of the correct grout for the base plate grouting operations can be based on the below mentioned factors:
- Cement grout is not designed to resist continuous impact loading and the vibrations of heavy machinery. When exposed to these stresses, the material cracks or otherwise experiences damage, which can have severe ramifications for both the machine and the concrete beneath it. Epoxy grout, on the other hand, has incredible bond strength and natural resistance to vibration.
- Cement grouts are vulnerable to chemical attack which can degrade the grout over time. Epoxy grouts are both water- and chemical-resistant, making them ideal for heavy machinery, especially in facilities exposed to chemicals or wet processing.
- Cement Grout has higher temperature resistant than Epoxy based grouts and hence are ideal for high temperature susceptible areas.
Thickness of Grout
The thickness of the grout layer that is used in the constructions depends on the gap between base plate and footing and commonly is not less than 25mm. Also, ACI 351.1R-99 recommends the minimum mentioned thickness for hydraulic cement grouts in similar values.
The minimum grout thickness depends significantly on the practicality of pouring concrete under the base plate. Therefore, the minimum thickness must be sufficient to place the grout in a realistic manner. In engineering practice, and also, ACI 351.1R-99 recommends the minimum preferred grout thickness is 25 mm. When the flow length is larger than 300 mm, the thickness should be increased by 13 mm for each additional 300 mm to a maximum of 100 mm.
Cementitious non-shrink grout for for the base plate grouting
ARDEX ENDURA offers B 30, a cementitious non-shrink grout and B 50, high strength epoxy grout for grouting all kinds of machine base plates. Following is the brief table explaining the properties of the grout which helps to select the grout quickly.
B 30 | B 50 |
Cementitious non shrink, expansive grout. | High strength, free flowing epoxy grout |
Compressive strength : > 65 N/Sqmm | Compressive strength: > 90 N/Sqmm |
Flexural strength : 10 N/Sqmm | Flexural strength: 30 N/Sqmm |
Tensile strength : 3.7 N/Sqmm | Tensile strength: 15 N/Sqmm |
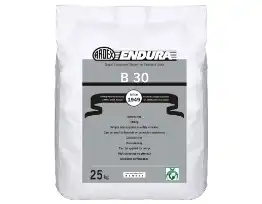

They also provide high early strength gaining grouts:
- B 31 – cementitious grout attains 10N/Sqmm in 10 Hrs.
- B 51 – epoxy resin grout attains 90N/Sqmm in 24 Hrs.
For all Contractors and Applicators committed to providing a high level of workmanship, ARDEX ENDURA helps them to increase both their professionalism and productivity.
For more details, visit- https://www.ardexendura.com/