Digital twin technology is a virtual model of a real-world object, process, or system that updates in real time using data from sensors and other sources. It helps in tracking progress, predicting problems, and improving decision-making. In construction, digital twins allow teams to monitor sites, plan better, reduce risks, and manage buildings efficiently even after completion.
How Digital Twin Technology Works in Construction?
Digital twin technology creates a virtual replica of a construction project that updates in real time using data from various sources. This helps teams track progress, identify issues early, and improve decision-making. The process involves the following steps:
- Data Collection and Integration – IoT sensors, drones, and monitoring tools gather real-time data on site conditions, material usage, equipment performance, and environmental factors.
- Digital Model Creation – A virtual model is built using BIM (Building Information Modeling) and other software to represent the structure and construction processes.
- Real-Time Data Processing – The collected data is continuously fed into the digital model, updating it with current site conditions and project status.
- AI and Analytics – Advanced algorithms analyze the data to detect issues, predict potential failures, and suggest improvements for efficiency and safety.
- User Interaction and Control – Construction teams use dashboards, mobile apps, and simulation tools to monitor progress, optimize workflows, and make informed decisions.
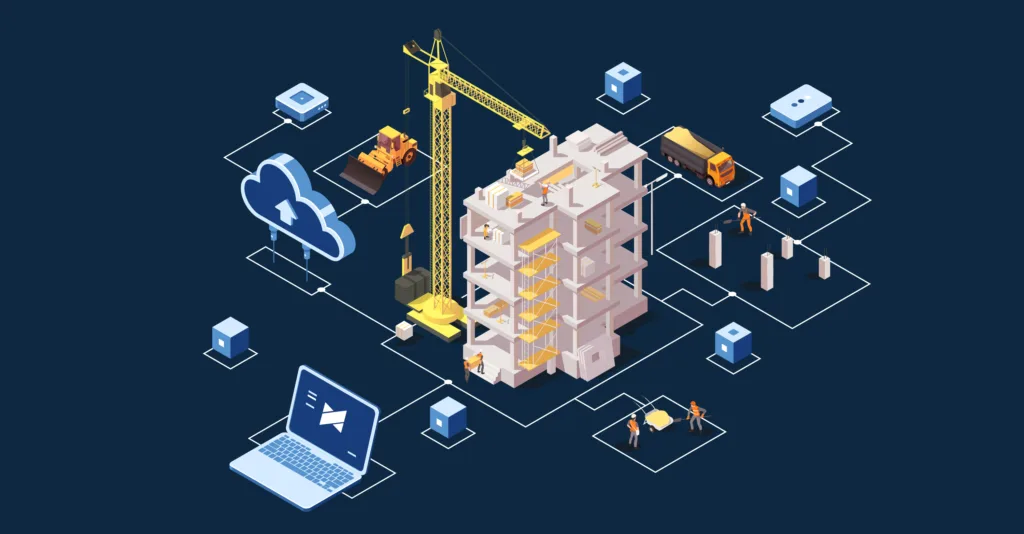
How Digital Twin Technology Enhances Construction Project Execution
1. Better Planning and Design
Digital twins integrate with BIM to provide a comprehensive visualization of construction projects. This allows architects and engineers to identify design flaws, simulate different scenarios, and optimize layouts before actual construction begins.
2. Real-Time Monitoring and Control
By continuously collecting data from construction sites, digital twins provide real-time updates on project status. Project managers can track progress, identify deviations, and make data-driven decisions to keep the project on schedule.
3. Predictive Maintenance and Risk Mitigation
Digital twins use AI and machine learning to analyze structural integrity and predict potential failures. This proactive approach helps in preventing costly rework and enhances safety by identifying risks early.
4. Enhanced Collaboration Among Stakeholders
Digital twin platforms allow project stakeholders, including architects, contractors, and investors, to access real-time project data. This transparency improves communication and decision-making throughout the project lifecycle.
5. Optimized Resource Utilization
With accurate data insights, digital twins help in optimizing the use of materials, equipment, and labor. This reduces waste and enhances efficiency in construction projects.
6. Improved Quality
By comparing real-world construction with digital models, digital twins help in maintaining quality standards. Any discrepancies between the planned and actual construction can be detected early and corrected.
7. Post-Construction Management
After project completion, digital twins continue to play a role in asset management. They help in monitoring building performance, scheduling maintenance, and ensuring the longevity of structures.
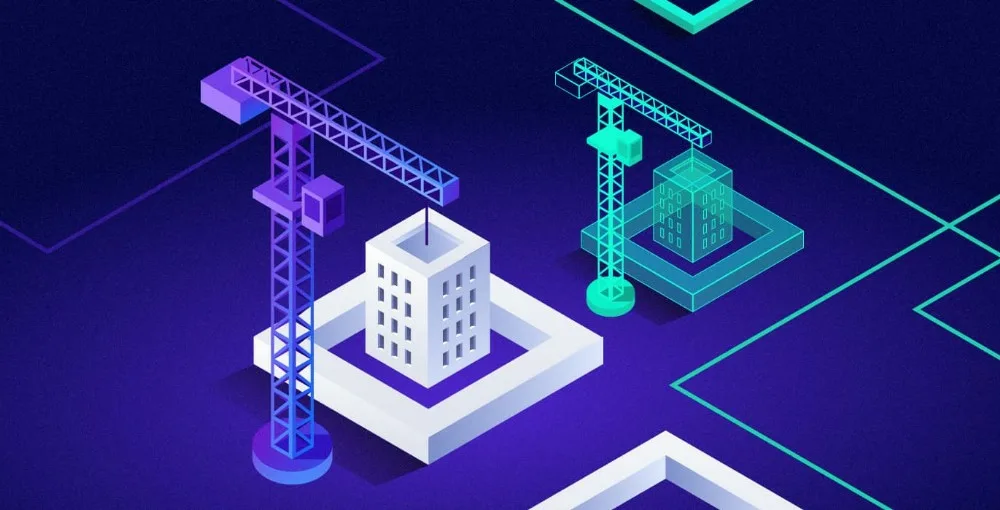
Types of Digital Twins used in Construction
Project Twin
A project twin provides a comprehensive digital representation of the entire construction project. It integrates design data, site conditions, scheduling, and resource management into a single model. By continuously updating with real-time data, project twins help teams track progress, identify deviations from the plan, and detect potential delays early. These models improve collaboration among stakeholders by providing a shared digital workspace where project managers, engineers, and contractors can monitor construction in real time.
Process Twin
Process twins focus on optimizing construction workflows and execution strategies. These models simulate different construction methods, enabling teams to identify bottlenecks and improve efficiency before actual work begins. By analyzing data on labor productivity, material usage, and equipment operation, process twins help ensure smoother project execution. They also assist in reducing downtime and minimizing costly delays by predicting potential obstacles in the construction timeline.
Product Twin
A product twin represents individual components of a construction project, such as beams, columns, HVAC systems, or prefabricated elements. These twins help in quality control by tracking the manufacturing and installation of each component. Engineers can use product twins to monitor structural performance, detect defects, and ensure compliance with safety standards. In modular and prefabricated construction, product twins play a important role in optimizing component assembly and minimizing material wastage.
Asset Twin
An asset twin is created once a construction project is completed and is primarily used for maintenance and lifecycle management. These models provide a detailed digital replica of the built structure, continuously updated with data from sensors that track performance, energy consumption, and environmental impact. Facility managers use asset twins to plan maintenance schedules, predict potential failures, and ensure the long-term sustainability of buildings and infrastructure. Asset twins are particularly valuable in smart buildings and infrastructure projects where long-term monitoring is essential for operational efficiency.
System Twin
A system twin focuses on interconnected building systems such as electrical networks, HVAC, plumbing, and safety systems. These models provide insights into how different systems interact within a structure, allowing engineers to optimize energy efficiency and detect faults before they cause failures. System twins are particularly useful in large-scale commercial buildings, industrial facilities, and smart cities, where efficient system operation is important for sustainability and cost management.
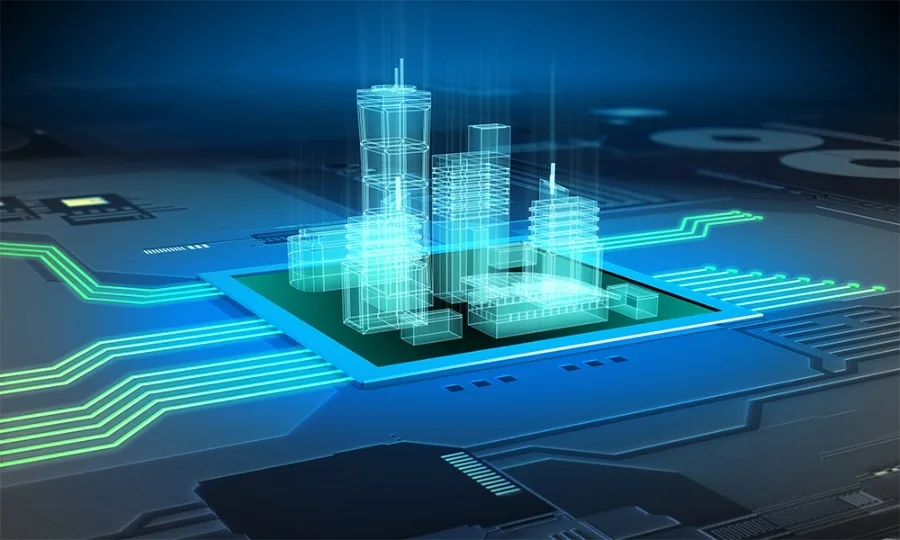
Applications of Digital Twin Technology in Construction
1. Site Planning and Optimization
Digital twins help in planning site layouts, determining optimal equipment placement, and ensuring efficient use of space. This reduces conflicts and improves workflow.
2. Structural Health Monitoring
By integrating sensor data, digital twins monitor the condition of structures in real-time, detecting issues like material degradation, cracks, or stress points before they lead to failures.
3. Safety Management
Digital twins assist in improving safety by simulating emergency scenarios, optimizing evacuation plans, and monitoring compliance with safety regulations.
4. Construction Process Automation
They enable automation of construction tasks by integrating robotics and AI, improving accuracy and reducing reliance on manual labor.
5. Energy Efficiency and Sustainability
Digital twins can analyze energy consumption patterns in buildings, enabling better design choices for energy-efficient structures and optimizing HVAC systems.
6. Cost Estimation and Budget Control
By simulating different construction scenarios, digital twins help in predicting costs, avoiding budget overruns, and optimizing financial planning.
7. Logistics and Supply Chain Management
Construction materials and equipment tracking become more efficient with digital twins, reducing wastage and ensuring timely deliveries.
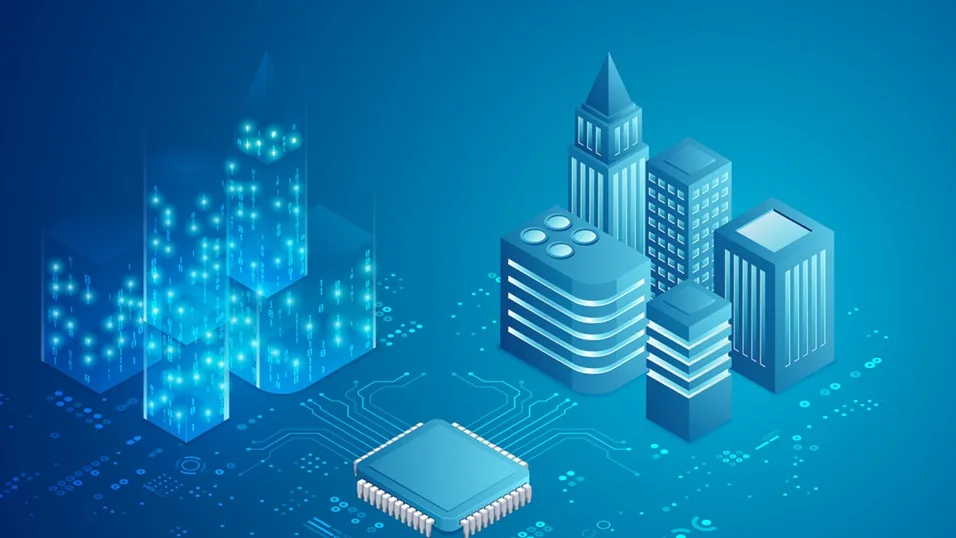
Challenges and Considerations in Implementing Digital Twin Technology
While digital twin technology offers numerous benefits, its adoption in construction comes with challenges:
- High Implementation Costs: Setting up digital twins requires investment in IoT devices, cloud computing, and AI-based analytics.
- Data Security Concerns: Protecting sensitive project data from cyber threats is important.
- Integration with Existing Systems: Ensuring compatibility with legacy construction management software is necessary for seamless implementation.
- Skilled Workforce Requirement: The adoption of digital twins requires training personnel in data analytics, AI, and digital modeling.
Future of Digital Twins in Construction
As technology evolves, digital twins will become an integral part of smart construction. The integration of AI, augmented reality (AR), and 5G connectivity will further enhance their capabilities. Governments and private sector players are increasingly adopting digital twins to improve infrastructure planning and execution.
Conclusion
Digital twin technology is transforming construction project execution by improving efficiency, reducing risks, and enabling data-driven decision-making. From planning and monitoring to post-construction management, digital twins offer a comprehensive approach to optimizing construction processes. As the industry continues to embrace digital transformation, the role of digital twins will expand, leading to more efficient and technologically advanced construction practices.