Cement in general, adhesive substances of all kinds, but in a narrower sense the binding materials used in building and civil engineering construction. Cements of this kind are finely ground powders that, when mixed with water, set to a hard mass. Setting and hardening result from hydration, which is a chemical combination of the cement compounds with water that yields sub microscopic crystals or a gel-like material with a high surface area. Because of their hydrating properties, constructional cements, which will even set and harden under water, are often called hydraulic cement. The most important of these is Portland cement.
This article surveys the historical development of cement, its manufacture from raw materials, its composition and properties, and the testing of those properties. The focus is on Portland cement, but attention is also given to other types, such as slag-containing cement and high-alumina cement. Construction cements share certain chemical constituents and processing techniques with ceramic products such as brick and tile, abrasives, and refractories.
APPLICATIONS OF CEMENT
Cements may be used alone (i.e., as grouting materials), but the normal use is in mortar and concrete in which the cement is mixed with inert material known as aggregate. Mortar is cement mixed with sand or crushed stone that must be less than approximately 5 mm (3/16 inch) in size. Concrete is a mixture of cement, sand or other fine aggregate, and a coarse aggregate that for most purposes is up to 19 to 25 mm (3/4 to 1 inch) in size, but the coarse aggregate may also be as large as 150 mm (6 inches) when concrete is placed in large masses such as dams. Mortars are used for binding bricks, blocks, and stone in walls or as surface renderings. Concrete is used for a large variety of constructional purposes. Mixtures of soil and Portland cement are used as a base for roads. Portland cement also is used in the manufacture of bricks, tiles, shingles, pipes, beams, railroad ties, and various extruded products. The products are prefabricated in factories and supplied ready for installation.
Because concrete is the most widely used of all construction materials in the world today, the manufacture of cement is widespread. Each year almost one ton of concrete is poured per capita in the developed countries.
HISTORY OF CEMENT
The origin of hydraulic cements goes back to ancient Greece and Rome. The materials used were lime and a volcanic ash that slowly reacted with it in the presence of water to form a hard mass. This formed the cementing material of the Roman mortars and concretes of 2,000 years ago and of subsequent construction work in Western Europe. Volcanic ash mined near what is now the city of Pozzuoli, Italy, was particularly rich in essential aluminosilicate minerals, giving rise to the classic pozzolanic cement of the Roman era. To this day the term pozzolanic, or pozzolan, refers either to the cement itself or to any finely divided aluminosilicate that reacts with lime in water to form cement. (The term cement, meanwhile, derives from the Latin word cementum, which meant stone chippings such as were used in Roman mortar—not the binding material itself.)
Portland cement is a successor to a hydraulic lime that was first developed by John Smeaton in 1756 when he was called in to erect the Eddy stone Lighthouse off the coast of Plymouth, Devon, England. The next development, taking place about 1800 in England and France, was a material obtained by burning nodules of clayey limestone. Soon afterward in the United States, a similar material was obtained by burning a naturally occurring substance called “cement rock.” These materials belong to a class known as natural cement, allied to Portland cement but more lightly burned and not of controlled composition.
The invention of Portland cement usually is attributed to Joseph Aspdin of Leeds, Yorkshire, England, who in 1824 took out a patent for a material that was produced from a synthetic mixture of limestone and clay. He called the product “Portland cement” because of a fancied resemblance of the material, when set, to Portland stone, a limestone used for building in England. Aspdin’s product may well have been too lightly burned to be a true Portland cement, and the real prototype was perhaps that produced by Isaac Charles Johnson in south eastern England about 1850. The manufacture of Portland cement rapidly spread to other European countries and North America. During the 20th century, cement manufacture spread worldwide. By the early 21st century, China and India had become the world leaders in cement production, followed by the United States, Brazil, Turkey, and Iran.
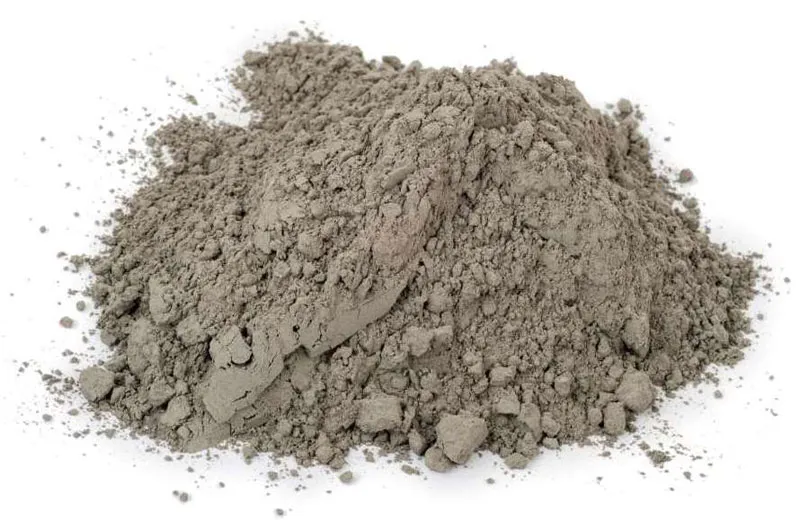
RAW MATERIALS
COMPOSITION
Portland cement consists essentially of compounds of lime (calcium oxide, CaO) mixed with silica (silicon dioxide, SiO2) and alumina (aluminium oxide, Al2O3). The lime is obtained from a calcareous (lime-containing) raw material, and the other oxides are derived from an argillaceous (clayey) material. Additional raw materials such as silica sand, iron oxide (Fe2O3), and bauxite—containing hydrated aluminium, Al (OH) 3—may be used in smaller quantities to get the desired composition.
The commonest calcareous raw materials are limestone and chalk, but others, such as coral or shell deposits, also are used. Clays, shales, slates, and estuarine muds are the common argillaceous raw materials. Marl, a compact calcareous clay, and cement rock contain both the calcareous and argillaceous components in proportions that sometimes approximate cement compositions. Another raw material is blast-furnace slag, which consists mainly of lime, silica, and alumina and is mixed with a calcareous material of high lime content. Kaolin, white clay that contains little iron oxide, is used as the argillaceous component for white Portland cement. Industrial wastes, such as fly ash and calcium carbonate from chemical manufacture, are other possible raw materials, but their use is small compared with that of the natural materials.
The magnesia (magnesium oxide, MgO) content of raw materials must be low because the permissible limit in Portland cement is 4 to 5 percent. Other impurities in raw materials that must be strictly limited are fluorine compounds, phosphates, metal oxides and sulphides, and excessive alkalies.
Another essential raw material is gypsum, some 5 percent of which is added to the burned cement clinker during grinding to control the setting time of the cement. Portland cement also can be made in a combined process with sulfuric acid using calcium sulphate or anhydrite in place of calcium carbonate. The sulphur dioxide produced in the flue gases on burning is converted to sulfuric acid by normal processes.
EXTRACTION AND PROCESSING
Raw materials employed in the manufacture of cement are extracted by quarrying in the case of hard rocks such as limestones, slates, and some shale, with the aid of blasting when necessary. Some deposits are mined by underground methods. Softer rocks such as chalk and clay can be dug directly by excavators.
The excavated materials are transported to the crushing plant by trucks, railway freight cars, conveyor belts, or ropeways. They also can be transported in a wet state or slurry by pipeline. In regions where limestones of sufficiently high lime content are not available, some process of beneficiation can be used. Froth flotation will remove excess silica or alumina and so upgrade the limestone, but it is a costly process and is used only when unavoidable.
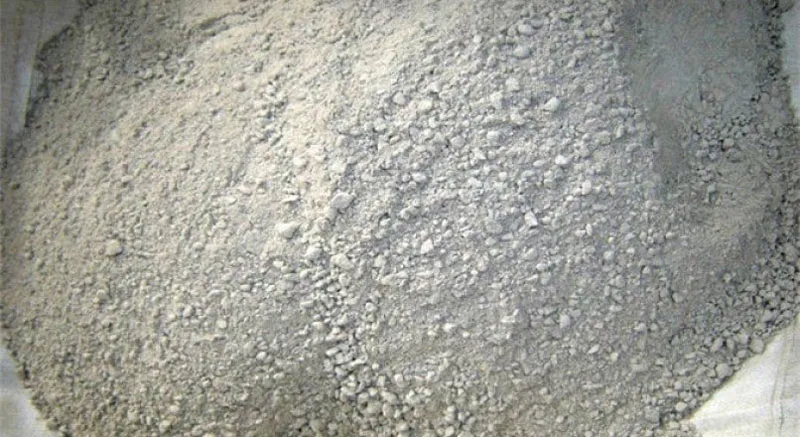
MANUFACTURE OF CEMENT
There are four stages in the manufacture of Portland cement:
- Crushing and grinding the raw materials.
- Blending the materials in the correct proportions.
- Burning the prepared mix in a kiln.
- Grinding the burned product, known as “clinker,” together with some 5 percent of gypsum (to control the time of set of the cement).
The three processes of manufacture are known as the wet, dry, and semidry processes and are so termed when the raw materials are ground wet and fed to the kiln as slurry, ground dry and fed as a dry powder, or ground dry and then moistened to form nodules that are fed to the kiln.
CRUSHING AND GRINDING
All except soft materials are first crushed, often in two stages, and then ground, usually in a rotating, cylindrical ball, or tube mills containing a charge of steel grinding balls. This grinding is done wet or dry, depending on the process in use, but for dry grinding the raw materials first may need to be dried in cylindrical, rotary dryers.
Soft materials are broken down by vigorous stirring with water in wash mills, producing a fine slurry, which is passed through screens to remove oversize particles.
BLENDING
A first approximation of the chemical composition required for a particular cement is obtained by selective quarrying and control of the raw material fed to the crushing and grinding plant. Finer control is obtained by drawing material from two or more batches containing raw mixes of slightly different composition. In the dry process these mixes are stored in silos; slurry tanks are used in the wet process. Thorough mixing of the dry materials in the silos is ensured by agitation and vigorous circulation induced by compressed air. In the wet process the slurry tanks are stirred by mechanical means or compressed air or both. The slurry, which contains 35 to 45 percent water, is sometimes filtered, reducing the water content to 20 to 30 percent, and the filter cake is then fed to the kiln. This reduces the fuel consumption for burning.
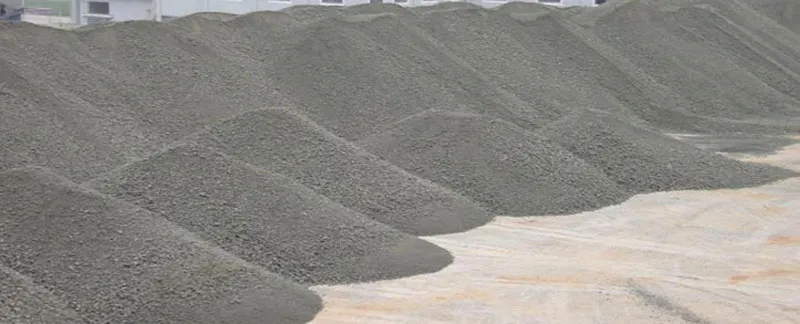
BURNING
The earliest kilns in which cement was burned in batches were bottle kilns, followed by chamber kilns and then by continuous shaft kilns. The shaft kiln in a modernized form is still used in some countries, but the dominant means of burning is the rotary kiln. These kilns—up to 200 metres (660 feet) long and six metres in diameter in wet process plants but shorter for the dry process—consist of a steel, cylindrical shell lined with refractory materials. They rotate slowly on an axis that is inclined a few degrees to the horizontal. The raw material feed, introduced at the upper end, moves slowly down the kiln to the lower, or firing, end. The fuel for firing may be pulverized coal, oil, or natural gas injected through a pipe. The temperature at the firing end ranges from about 1,350 to 1,550 °C (2,460 to 2,820 °F), depending on the raw materials being burned. Some form of heat exchanger is commonly incorporated at the back end of the kiln to increase heat transfer to the incoming raw materials and so reduce the heat lost in the waste gases. The burned product emerges from the kiln as small nodules of clinker. These pass into coolers, where the heat is transferred to incoming air and the product cooled. The clinker may be immediately ground to cement or stored in stockpiles for later use.
In the semidry process the raw materials, in the form of nodules containing 10 to 15 percent water, are fed onto a traveling chain grate before passing to the shorter rotary kiln. Hot gases coming from the kiln are sucked through the raw nodules on the grate, preheating the nodules.
Dust emission from cement kilns can be a serious nuisance. In populated areas it is usual and often compulsory to fit cyclone arrestors, bag-filter systems, or electrostatic dust precipitators between the kiln exit and the chimney stack.
Modern cement plants are equipped with elaborate instrumentation for control of the burning process. Raw materials in some plants are sampled automatically, and a computer calculates and controls the raw mix composition. The largest rotary kilns have outputs exceeding 5,000 tons per day.
GRINDING
The clinker and the required amount of gypsum are ground to a fine powder in horizontal mills similar to those used for grinding the raw materials. The material may pass straight through the mill (open-circuit grinding), or coarser material may be separated from the ground product and returned to the mill for further grinding (closed-circuit grinding). Sometimes a small amount of a grinding aid is added to the feed material. For air-entraining cements (discussed in the following section) the addition of an air-entraining agent is similarly made.
Finished cement is pumped pneumatically to storage silos from which it is drawn for packing in paper bags or for dispatch in bulk containers.
THE MAJOR CEMENTS: COMPOSITION AND PROPERTIES
PORTLAND CEMENT
Chemical Composition
Portland cement is made up of four main compounds: tricalcium silicate (3CaO · SiO2), dicalcium silicate (2CaO · SiO2), tricalcium aluminate (3CaO · Al2O3), and a tetra-calcium aluminoferrite (4CaO · Al2O3Fe2O3). In an abbreviated notation differing from the normal atomic symbols, these compounds are designated as C3S, C2S, C3A, and C4AF, where C stands for calcium oxide (lime), S for silica, A for alumina, and F for iron oxide. Small amounts of uncombed lime and magnesia also are present, along with alkalies and minor amounts of other elements.
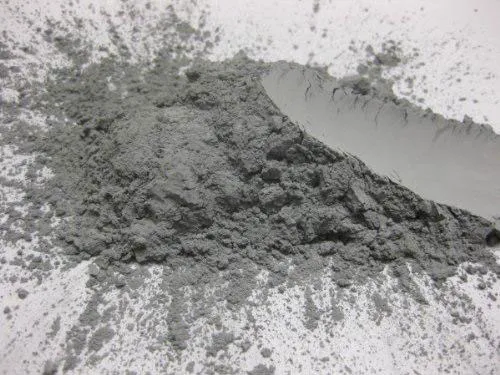
Hydration
The most important hydraulic constituents are the calcium silicates, C2S and C3S. Upon mixing with water, the calcium silicates react with water molecules to form calcium silicate hydrate (3CaO · 2SiO2 · 3H2O) and calcium hydroxide (Ca [OH] 2). These compounds are given the shorthand notations C–S–H (represented by the average formula C3S2H3) and CH, and the hydration reaction can be crudely represented by the following reactions:2C3S + 6H = C3S2H3 + 3CH2C2S + 4H = C3S2H3 + CH During the initial stage of hydration, the parent compounds dissolve, and the dissolution of their chemical bonds generates a significant amount of heat. Then, for reasons that are not fully understood, hydration comes to a stop. This quiescent, or dormant, period is extremely important in the placement of concrete. Without a dormant period there would be no cement trucks; pouring would have to be done immediately upon mixing.
Following the dormant period (which can last several hours), the cement begins to harden, as CH and C–S–H are produced. This is the cementitious material that binds cement and concrete together. As hydration proceeds, water and cement are continuously consumed. Fortunately, the C–S–H and CH products occupy almost the same volume as the original cement and water; volume is approximately conserved, and shrinkage is manageable.
Although the formulas above treat C–S–H as a specific stoichiometry, with the formula C3S2H3, it does not at all form an ordered structure of uniform composition. C–S–H is actually an amorphous gel with a highly variable stoichiometry. The ratio of C to S, for example, can range from 1:1 to 2:1, depending on mix design and curing conditions.
Structural Properties
The strength developed by Portland cement depends on its composition and the fineness to which it is ground. The C3S is mainly responsible for the strength developed in the first week of hardening and the C2S for the subsequent increase in strength. The alumina and iron compounds that are present only in lesser amounts make little direct contribution to strength.
Set cement and concrete can suffer deterioration from attack by some natural or artificial chemical agents. The alumina compound is the most vulnerable to chemical attack in soils containing sulphate salts or in seawater, while the iron compound and the two calcium silicates are more resistant. Calcium hydroxide released during the hydration of the calcium silicates is also vulnerable to attack. Because cement liberates heat when it hydrates, concrete placed in large masses, as in dams, can cause the temperature inside the mass to rise as much as 40 °C (70 °F) above the outside temperature. Subsequent cooling can be a cause of cracking. The highest heat of hydration is shown by C3A, followed in descending order by C3S, C4AF, and C2S.
TYPES OF PORTLAND CEMENT
Five types of Portland cement are standardized in the United States by the American Society for Testing and Materials (ASTM): ordinary (Type I), modified (Type II), high-early-strength (Type III), low-heat (Type IV), and sulphate-resistant (Type V). In other countries Type II is omitted, and Type III is called rapid-hardening. Type V is known in some European countries as Ferrari cement.
There also are various other special types of Portland cement. Coloured cements are made by grinding 5 to 10 percent of suitable pigments with white or ordinary gravy Portland cement. Air-entraining cements are made by the addition on grinding of a small amount, about 0.05 percent, of an organic agent that causes the entrainment of very fine air bubbles in a concrete. This increases the resistance of the concrete to freeze-thaw damage in cold climates. The air-entraining agent can alternatively be added as a separate ingredient to the mix when making the concrete.
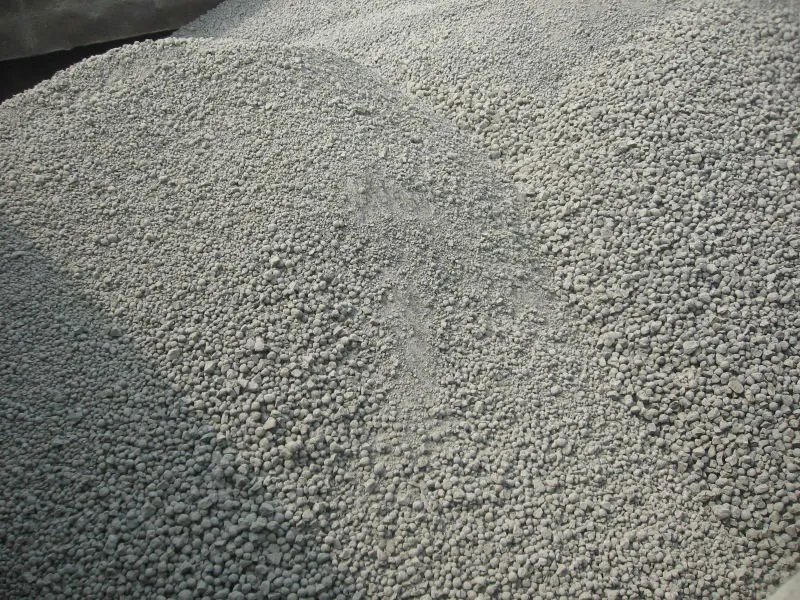
Low-alkali cements are Portland cements with a total content of alkalies not above 0.6 percent. These are used in concrete made with certain types of aggregates that contain a form of silica that reacts with alkalies to cause an expansion that can disrupt a concrete.
Masonry cements are used primarily for mortar. They consist of a mixture of Portland cement and ground limestone or other filler together with an air-entraining agent or a water-repellent additive. Waterproof cement is the name given to a Portland cement to which a water-repellent agent has been added. Hydrophobic cement is obtained by grinding Portland cement clinker with a film-forming substance such as oleic acid in order to reduce the rate of deterioration when the cement is stored under unfavourable conditions.
Oil-well cements are used for cementing work in the drilling of oil wells where they are subject to high temperatures and pressures. They usually consist of Portland or pozzolanic cement (see below) with special organic retarders to prevent the cement from setting too quickly.
SLAG CEMENTS
The granulated slag made by the rapid chilling of suitable molten slags from blast furnaces forms the basis of another group of constructional cements. A mixture of Portland cement and granulated slag, containing up to 65 percent slag, is known in the English-speaking countries as Portland blast-furnace (slag) cement. The German Eisenportlandzement and Hochofenzement contain up to 40 and 85 percent slag, respectively. Mixtures in other proportions are found in French-speaking countries under such names as cement Portland de far, cement metallurgies mixte, cement de haut Tourneau, and cement de lintier au clinker. Properties of these slag cements are broadly similar to those of Portland cement, but they have a lower lime content and a higher silica and alumina content. Those with the higher slag content have an increased resistance to chemical attack.
Another type of slag-containing cement is a supersulfated cement consisting of granulated slag mixed with 10 to 15 percent hard-burned gypsum or anhydrite (natural anhydrous calcium sulphate) and a few percent of Portland cement. The strength properties of supersulfated cement are similar to those of Portland cement, but it has an increased resistance to many forms of chemical attack. Pozzolanic cements are mixtures of Portland cement and a pozzolanic material that may be either natural or artificial. The natural pozzolanic are mainly materials of volcanic origin but include some diatomaceous earths. Artificial materials include fly ash, burned clays, and shales. Pozzolanic are materials that, though not cementitious in them, contain silica (and alumina) in a reactive form able to combine with lime in the presence of water to form compounds with cementitious properties. Mixtures of lime and pozzolanic still find some application but largely have been superseded by the modern pozzolanic cement. Hydration of the Portland cement fraction releases the lime required to combine with the pozzolanic.
HIGH-ALUMINA CEMENT
High-alumina cement is a rapid-hardening cement made by fusing at 1,500 to 1,600 °C (2,730 to 2,910 °F) a mixture of bauxite and limestone in a reverberator or electric furnace or in a rotary kiln. It also can be made by sintering at about 1,250 °C (2,280 °F). Suitable bauxites contain 50 to 60 percent alumina, up to 25 percent iron oxide, not more than 5 percent silica, and 10 to 30 percent water of hydration. The limestone must contain only small amounts of silica and magnesia. The cement contains 35 to 40 percent lime, 40 to 50 percent alumina, up to 15 percent iron oxides, and preferably not more than about 6 percent silica. The principal cementing compound is calcium aluminate (CaO · Al2O3).
High-alumina cement gains a high proportion of its ultimate strength within 24 hours and has a high resistance to chemical attack. It also can be used in refractory linings for furnaces. A white form of the cement, containing minimal proportions of iron oxide and silica, has outstanding refractory properties.
EXPANDING AND NO SHRINKING CEMENTS
Expanding and no shrinking cements expand slightly on hydration, thus offsetting the small contraction that occurs when fresh concrete dries for the first time. Expanding cements were first produced in France about 1945. The American type is a mixture of Portland cement and an expansive agent made by clinkering a mix of chalk, bauxite, and gypsum.
Gypsum Plasters
Gypsum plasters are used for plastering, the manufacture of plaster boards and slabs, and in one form of floor-surfacing material. These gypsum cements are mainly produced by heating natural gypsum (calcium sulphate dehydrate, CaSO4 · 2H2O) and dehydrating it to give calcium sulphate hemihydrate (CaSO4 · 1/2H2O) or anhydrous (water-free) calcium sulphate. Gypsum and anhydrite obtained as by-products in chemical manufacture also are used as raw materials.
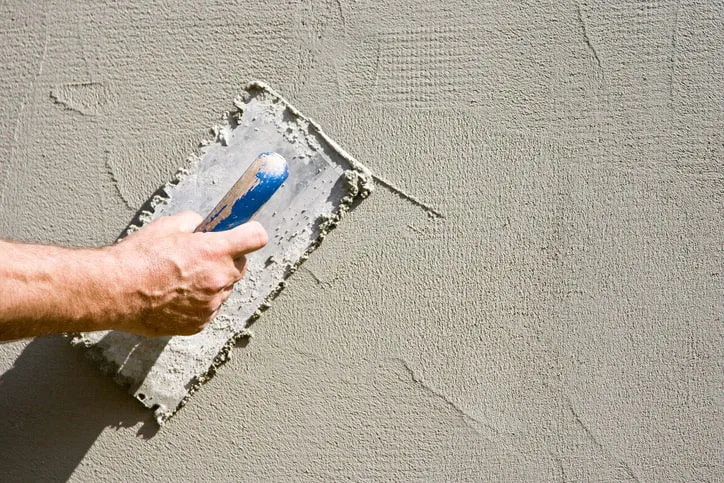
The hemihydrate, known as plaster of Paris, sets within a few minutes on mixing with water; for building purposes a retarding agent, normally keratin, a protein, is added. The anhydrous calcium sulphate plasters are slower-setting, and often another sulphate salt is added in small amounts as an accelerator. Flooring plaster, originally known by its German title of Estrich Gips, is of the anhydrous type.
CEMENT TESTING
Various tests to which cements must conform are laid down in national cement specifications to control the fineness, soundness, setting time, and strength of the cement. These tests are described in turn below.
Fineness
Fineness was long controlled by sieve tests, but more sophisticated methods are now largely used. The most common method used both for control of the grinding process and for testing the finished cement, measures the surface area per unit weight of the cement by a determination of the rate of passage of air through a bed of the cement. Other methods depend on measuring the particle size distribution by the rate of sedimentation of the cement in kerosene or by elutriation (separation) in an airstream.
SOUNDNESS
After it has set, a cement must not undergo any appreciable expansion, which could disrupt a mortar or concrete. This property of soundness is tested by subjecting the set cement to boiling in water or to high-pressure steam. Unsoundness can arise from the presence in the cement of too much free magnesia or hard-burned free lime.
SETTING TIME
The setting and hardening of a cement is a continuous process, but two points are distinguished for test purposes. The initial setting time is the interval between the mixing of the cement with water and the time when the mix has lost plasticity, stiffening to a certain degree. It marks roughly the end of the period when the wet mix can be moulded into shape. The final setting time is the point at which the set cement has acquired a sufficient firmness to resist a certain defined pressure. Most specifications require an initial minimum setting time at ordinary temperatures of about 45 minutes and a final setting time no more than 10 to 12 hours.
STRENGTH
The tests that measure the rate at which a cement develops strength are usually made on a mortar commonly composed of one part cement to three parts sand, by weight, mixed with a defined quantity of water. Tensile tests on briquettes, shaped like a figure eight thickened at the centre, were formerly used but have been replaced or supplemented by compressive tests on cubical specimens or transverse tests on prisms. The American Society for Testing and Materials (ASTM) specification requires tensile tests on a 1:3 cement-sand mortar and compressive tests on a 1:2.75 mortar. The British Standards Institution (BSI) gives as alternatives a compressive test on a 1:3 mortar or on a concrete specimen. An international method issued by the International Organization for Standardization (ISO) requires a transverse test on a 1:3 cement-sand mortar prism, followed by a compressive test on the two halves of the prism that remain after it has been broken in bending. Many European countries have adopted this method. In all these tests the size grading of the sand, and usually its source, is specified.
In the testing of most cements, a minimum strength at 3 and 7 days and sometimes 28 days is specified, but for rapid-hardening Portland cement a test at 1 day also is sometimes required. For high-alumina cement, tests are required at 1 and 3 days. Strength requirements laid down in different countries are not directly comparable because of the differences in test methods. In actual construction, to check the strength of a concrete, compressive tests is made on cylinders or cubes made from the concrete being placed.
CONCLUSION
Basically, different types of cements and their chemical composition and applications in the current engineering and chemical world have been discussed in detail. Different type of enhancing materials and fillers are developed using Nano-technology for the productive and effective cement manufacturing has been mentioned with the chemical background. Mechanical defects when concrete are concerned and possible solutions that can be given through chemistry and nanotechnology have been deliberated in detail. In addition, CO2-entrapping chemical compounds such as zeolites and metal organic framework and their contribution in making durability of the cement manufacturing have been illustrated with their chemistry. Environment effects of cement manufacturing and how to control the pollution of the environment when manufacturing processes that are being executed have been discussed using several standard processes, including the Calera process, oxy-combustion process, and monoethanolamide (MEA) process. Currently, the applications of nanoscience and nanotechnology have been gaining pop-clarity in different fields of science and technology. Potential of nanotechnology to progress the performance of concrete and to lead to the development of novel, sustainable, advanced cement-based composites, and smart materials with unique mechanical, thermal, and electrical properties is promising, and many novel opportunities are expected to arise the future. So finally, the newest trend of making Nano-cement and its development towards current developing and updating world is described in advance.
Authored by;
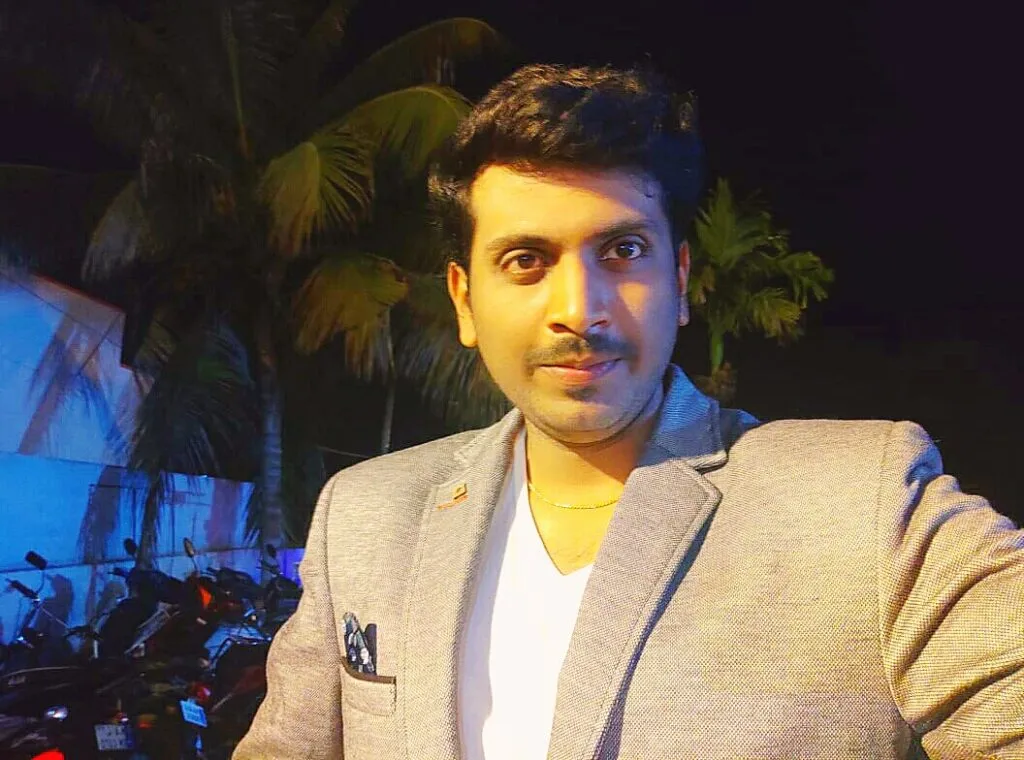