In the series of these articles I am attempting to explain each significant aspect of Universal/ Unified Bridge Management System (UBMS). In this article, I explain the role of testing in UBMS. In my previous articles, I dwelled on Significance of IBMS and Migration of IBMS to UBMS. Explaining about Migration from IBMS to UBMS, I had briefly stated the reason of having testing of bridges as a part of flow of activities in the overall system to manage bridges efficiently. In this article, I shall dwell on this aspect of UBMS and explain how the definition of cause of distress in EN 1504, enabled us to use testing as a confirmation process for the prognosis established during inspection of bridges. Any test procedure enables us to determine only specific properties of the material or component that is tested. The test results cannot be generalised to apply to the whole structure unless similar distress symptoms exist on the whole structure. This is a very significant aspect that UBMS relies on.
DEFINITION OF CAUSE OF DISTRESS
UBMS has relied on the development in Europe, for the definition of the primary causes of distress. Sustainability of constructed structures has been the driving force for all research in design, construction and rehabilitation of structures. Within repairs and rehabilitation, it was more the durability of repairs to enhance the service life to the designed value that was more of a concern. European standards provide normative documents that provide guidelines for a regulated practice. EN 1504 is one such document which provides the guidelines for Products and systems for protection of repairs in Concrete structures. In my next article I shall explain more about this definition of cause of distress. For the present we shall defines three fundamental causes of distress namely
- Physical cause
- Mechanical cause
- Chemical cause
These three causes are further sub-classified as under:
Table 1: Causes of deterioration in concrete.

Detailed classification of each sub-cause shall also be defined in my subsequent article. It is important to note that each cause of distress, affects certain parameters of the material by changing the performance of that material or component under the influence of that cause. UBMS tries to focus on this change of performance to confirm or reject the cause of distress.
At the same time, it is significant to note that Bridges are at times large or mega structures with multiple units and multiple structural forms combined into one bridge which has multiple components. This can result in multiple causes affecting different components or different structural forms. Also due to its large magnitude or dimensions, a single bridge may have a primary cause supported or complimented by many secondary causes.
Another important aspect of distress in bridges is the possibility of non structural distress which also needs attention. Distress in Non-Structural members can also get manifested into distress in Structural members so it is important to arrest such distress at the nascent stage before they get manifested into Structural distress.
CORELATION BETWEEN CAUSE OF DISTRESS AND TESTING
Recent changes and additions made by Indian Road Congress (IRC) in their special publications (IRC SP) namely IRC SP 40, IRC SP 18 and IRC SP 35; IRC has defined 24 test procedures to be available for testing on bridges. Relevant available International Codes are to be followed for the procedure and reporting. The tests are now included in IRC documents are tabulated below
Table 2: Test available for concrete testing.
S.No | Test Name |
01 | Pull-out Test (Hole Drilled & insert placed in old concrete) |
02 | Penetration Resistance/ Windsor probe Test |
03 | Resistivity Measurements |
04 | Half-Cell potential Measurements |
05 | Ultrasonic Pulse Velocity |
06 | Acoustic Emission Test |
07 | Dynamic Response Technique |
08 | Ground Penetrating Radar |
09 | Radiography |
10 | Carbonation Test |
11 | Crack Measurement |
12 | Trepanning Test |
13 | Endoscopic Test |
14 | Thermography |
15 | Petrography |
16 | Impact-Echo |
17 | Schmidt/Rebound Hammer Test |
18 | Permeability |
19 | Cover Meter |
20 | Chemical Analysis (Sulphate Content, chloride Content) |
21 | Hammer Rap/Heavy Chains |
22 | Linear Polarization Resistance (LPR) |
23 | Galvano-Static Pulse Method |
This has come as a big relief to the testing and rehabilitation fraternity as previously only 4 tests were relied on (in India) for testing as they were only defined in IRC or IS codes. Now with the inclusion of other test procedures, it is possible to define the various tests that can be used for specific purpose of identification of the change in performance due to specific cause of distress. IRC outline various parameters that these tests can evaluate. The parameters that each of the tests can or cannot evaluate include cracking, Scaling, Corrosion, Wear and Abrasion and Strength. UBMS has adopted this relationship between the defined parameters that these tests can evaluate to the cause of distress. The table below illustrates the various tests that can be used to confirm the various causes of distress in structural members.
Table 3: Applicability of ND Tests to confirm cause of distress.
S.No | Test Name | Applicability as per Distress cause matrix |
01 | Pull-out Test (Hole Drilled & insert placed in old concrete) | A1, A4 & A5 |
02 | Penetration Resistance/ Windsor probe Test | A1, A4 & A5 |
03 | Resistivity Measurements | C1, C2, C3 & C4 |
04 | Half-Cell potential Measurements | C1, C2, C3 & C4 |
05 | Ultrasonic Pulse Velocity | B1, B2, A2 & A3 |
06 | Acoustic Emission Test | B1, B2, A2 & A3 |
07 | Dynamic Response Technique | B1, B2, A1, A2, A3, A4 & A5 |
08 | Ground Penetrating Radar | A2 & A3 |
09 | Radiography | A2 & A3 |
10 | Carbonation Test | C1, C2, C3 &C4 |
11 | Crack Measurement | B1, B2, A2 & A3 |
12 | Trepanning Test | B1, B2, A1, A2, A3, A4 & A5 |
13 | Endoscopic Test | B1, B2, A2 & A3 |
14 | Thermography | B1, B2, A2, A3, C1 & C3 |
15 | Petrography | C1, C2, C3 & C4 |
16 | Impact-Echo | B1, B2, A2 & A3 |
17 | Schmidt/Rebound Hammer Test | C1, C2, C3 &C4 |
18 | Permeability | A2, A3, C1 & C3 |
10 | Cover Meter | Measure cover depth and locate rebars in concrete. |
20 | Chemical Analysis (Sulphate Content, chloride Content) | C1, C2, C3 &C4 |
21 | Hammer Rap/Heavy Chains | A1, C1 & C2 |
22 | Linear Polarization Resistance (LPR) | C1, C2, C3 &C4 |
23 | Galvano-Static Pulse Method | C1, C2, C3 &C4 |
Having established the correlation between the test procedure and the cause of distress, it is essential to have a protocol in the UBMS system that will enable use of the this correlationship. UBMS flow of activities ensure that the bridges, which have distress are identified as having defects by the inspection engineer, who generates his prognosis as to the cause of distress by creation of cause matrix. This is only an assumed cause of distress which is required to be confirmed by a procedure which is mainly by one of the above tests as applicable. Engineers use testing to confirm such prognosis.

TESTING PROTOCOL TO CONFIRM THE CAUSE OF DISTRESS
UBMS mandate that on all such bridges; which have been identified to have a distress, tests be performed as per the correlation to confirm the prognosis. Unless the prognosis is confirmed by positive results of the tests, the same cannot be accepted as the correct cause of distress. In case the test results turn out to be negative, the bridge is reassigned to the inspection engineers to determine the diagnosis / prognosis again as to why the distress is occurring in the bridge. The Inspection engineers relies on the visual signs of distress to define his prognosis. To this extend the inspection engineers needs to be trained. (Training is a topic of one of the subsequent articles in this series).

The Testing agency, within the UBMS flow of activities, needs to confirm the prognosis and confirm the primary causes and the secondary causes. They also need to quantify the amount of distress and its severity. This part of work is shifted from Inspection engineer to Testing agency in UBMS, since the testing agency are more equipped to confirm the prognosis and define the cause and severity of distress in the structure. Once the tests confirm the prognosis and the cause of distress, the flow of UBMS moves ahead to define the principle of rehabilitation. The quantity of repairs and the detailed scheme of repairs/ rehabilitation/ strengthening is compiled. Testing forms an important link between prognosis and definition of remedial intervention. It is critical for the full exploitation of UBMS.

CONCLUSIONS
UBMS activity flow has ensured that one of the most important steps of management of bridges, namely the definition of the cause of distress in the bridge is identified. This distress is confirmed by a procedure, that ensures that the hypothesis formed during inspection as to the reason of distress is checked by testing of the structure. The tests to be performed, are one that are best suited to evaluate the performance of the structure under distress. Since, many test procedures are available it is important to choose the correct test procedure. Every distress causes a particular parameter of the structure to modify its response. It is this fact that is used to decide the test best suited to evaluate that changes in response. Such a confirmation by testing, ensures the most important step in management of bridges (Decision on the primary cause of distress in the bridge) on a network is a validated process. This makes UBMS a better system to handle distress in bridges.
About the author:
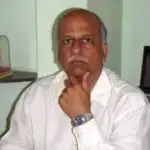
The article is authored by SACHIDANAND JOSHI, Emeritus Chair—IBMS @ IDDC Engineers Pvt. Ltd.
All of the author’s career has been devoted to the Rehabilitation of structures. He has been a team leader to over 2000 inspection, repair and rehabilitation projects. Having seen the various causes of distress so closely and the extent of damage and loss that is caused by ZERO maintenance of various structures, he decided to devote his energy to conceptualize a system that can avoid this scenario. From that urge to minimize distress, came his focus on Asset Management Program.
SACHIDANAND JOSHI is presently working passionately to implement Asset Management Programs in various facades of the Civil Engineering industry in India. The author has ha flair to conceptualize projects and get the team to complete the micro-planning.