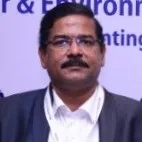
Consultant – Technical, Project Management & Business Development
The effect of water cement ratio on hardened properties of cement mortar with partial replacement of natural sand by artificial sand is investigated. Designed mortar mix having proportions as 1:2, 1:3 and 1:6 with water cement ratio of 0.5 and 0.55 respectively is used in experimental study. Mortar cube specimens are tested for evaluation of compressive strength. The mortar exhibits excellent strength with 50% replacement of natural sand by artificial sand. This paper puts forward the applications of artificial sand as an attempt towards sustainable development. It will help to find a viable solution to the declining availability of natural sand to make eco-balance.
Introduction
The global consumption of natural sand is very high, due to the extensive use of concrete or mortar. In general, the demand for natural sand is quite high in developing countries to satisfy the rapid infrastructure growth, in this situation developing countries like India are facing shortage in good quality natural sand. Particularly in India, natural sand deposits are being depleted and causing serious threat to the environment as well as the society. Increasing extraction of natural sand from river beds causing many problems, losing water retaining sand strata, deepening of the river courses and causing bank slides, loss of vegetation on the bank of rivers, exposing the intake well of water supply schemes, disturbs the aquatic life as well as affecting agriculture due to lowering the underground water table etc are few examples. Properties of aggregate affect the durability and performance of concrete, so fine aggregate is an essential component of concrete and cement mortar. The most commonly used fine aggregate is natural river or pit sand. Fine and coarse aggregate constitute about 75% of total volume. It is therefore, important to obtain right type and good quality aggregate at site, because the aggregate forms the main matrix of concrete or mortar.
Now a day’s sand is becoming a very scarce material, in this situation research began for inexpensive and easily available alternative material to natural sand. Some alternatives materials have already been used as a part of natural sand e.g. fly-ash, slag limestone and siliceous stone powder are used in concrete mixtures as a partial replacement of natural sand. However, scarcity in required quality is the major limitation in some of the above materials. Now a day’s sustainable infrastructural growth demands the alternative material that should satisfy technical requisites of fine aggregate as well as it should be available abundantly.
The effect of high levels of fines content on concrete properties. It has taken a review of the strength and behavior of concrete by using crushed rock dust as fine aggregate, they investigated the possibility of using crushed rock as 100 % replacement for sand, with varying compacting factors. The proportioning concrete mixes with rock dust as fine aggregate. It was also carried detailed investigation on utilization of quarry waste fine aggregate in concrete mixtures. The investigated experimentally the performance of concrete with quarry dust as fine aggregate. The investigated the crushed stone waste as fine aggregate for concrete. It was also carried out the tests on concrete with stone crusher dust as fine aggregate. The investigated on stone dust as fine aggregate in structural concrete. And has studied the substitution of the dune sand by the clay sand (calcined clay) influences appreciably on the water demand necessary to have acceptable workability (Fluidity or consistency) of fresh mortar. Artificial sand offers viable alternative to natural sand and it is purpose made fine aggregate produced by crushing and screening or further processing i.e. washing, grading, classifying of quarried rock, cobbles, boulders or gravels from which natural fine aggregate had been removed. Based on review work is carried out on strength properties of cement mortar with partial replacement of natural sand by manufactures sand. Also strength of cement mortar is calculated using different water cement ratios.
A. Research significance
The main objective of the present work is to systematically study the effect of water cement ratio and percentage replacement of natural sand by artificial sand as 0.5, 0.55 and 0%, 50% and 100% respectively on the strength propertied of cement mortar. The study is carried out on mortar with proportion 1:2, 1:3 and 1:6 with water cement ratio of 0.5 and 0.55 respectively. Artificial sand can be used as fine aggregate, but it has to satisfy the technical requisites. On this aspect research on cement mortar with artificial sand is scarce, so this paper investigates the cement mortar produced with artificial sand.
B. Materials
Aggregate: – Locally available river sand as fine aggregate (4.75mm to 75 micron (0.2 to 0.003 in)) is used. Artificial sand (4.75mm to 75 micron (0.2 to 0.003 in)) is used for partial replacement to natural sand. Natural and artificial sand are from zone II (IS 383). Sieve analysis and material properties are presented in Table 1 and 2 (IS 383 and IS 2386). Cement: – The cement used is 53 grade (Ordinary Portland Cement) (IS 12269).
Table 1: Physical properties of materials
Property | Fine Aggregate (IS 383) | Coarse Aggregate (IS 383) | |
Natural Sand | Artificial Sand | ||
Specific Gravity | 2.6 | 2.84 | 2.75 |
Fineness Modulus | 2.89 | 2.84 | – |
Water Absorption | 6.5% | 5.6% | 2.5% |
C. Experimental Program
The main objective of this experimentation is to find out the effect of replacement of natural sand by artificial sand with 0%, 50% and 100% on hardened properties of cement mortar. The experimental work includes the casting, curing and testing of specimens. Material properties are shown in Table 1.Mortar mix is prepared with proportions of 1:2, 1:3 and 1:6 with water cement ratio of 0.5 and 0.55 respectively. Three trials are carried out for each water cement ratio and mortar mix proportion, where Mix 1 is the reference mix with 0% artificial sand, Mix 2 is with 50% replacement of natural sand by artificial sand and Mix 3 is with 100% artificial sand. All of the experiments are performed in normal room temperature. The mortar ingredients, namely cement and fine aggregate first mixed in dry state. Artificial sand is used as a partial replacement to the natural sand then calculated amount of water is added and mix it thoroughly to get a homogeneous mix. Mortar is poured in the moulds layer by layer and compact thoroughly. Cubes are used for compressive strength test having size 7.06 mm (0.3 in) x7.06 mm (0.3 in) x 7.06 mm (0.3 in) that are cured in water for 28 days and tested at 28 day’s on Universal testing Machine (UTM).
D. Results and Discussion
Table 3, table 4 and table 5 gives the test results of cement mortar with proportion of 1:2, 1:3 and 1:6 having water cement ratio as 0.5 and 0.55. Mortar mixes revealed an increase of compressive strength up to 14.53%, 46.95% and 60.62% for proportion of 1:2, 1:3 and 1:6 with water cement ration as 0.5 as result of replacement of artificial sand up to 50% respectively as shown in table 3, table 4, table 5 and figures 1, 2 and 3 respectively. This may be due to the fact that 50% replacement of natural sand by artificial sand may show the optimum reaction with optimum filler capacity. It can be concluded that 50% replacement of natural sand by artificial sand will yield the maximum strengths for cement mortar. In this study we observe that the overall strength of mortar is higher are compared with reference mix.
Table 2: Details of sieve analysis of natural sand and artificial sand
Sieve Designation | Percentage Passing of Zone II sand | Grading Limits for Zone II Sand (IS 383) | |
Natural Sand | Artificial Sand | ||
4.75 mm (No.4) | 94.75 | 100 | 90-100 |
2.36 mm (No. 8) | 88.5 | 88.1 | 75-100 |
1.18 mm (No.16) | 71.25 | 68.8 | 55-90 |
600 micron (No.30) | 42.5 | 37.3 | 35-59 |
300 micron (No.50) | 11.5 | 15 | 8-30 |
150 micron (No.100) | 1.75 | 6 | 0-10 |
Table 3: Test results of cement mortar of proportion 1:2 (1 Mpa= 0.1450 ksi)
Percentage replacement of natural sand by artificial sand | Mortar mix proportion 1:2, | Mortar mix proportion 1:2,w/c=0.55 | ||
Compressive strength MPa (ksi) | Percentage increase of compressive strength with respect to reference mix | Compressive strength MPa (ksi) | Percentage increase of compressive strength with reference to reference mix | |
Mix 1(Reference Mix) (0% Artificial Sand) | 42.26(6.13) | – | 40.55(5.88) | – |
Mix2 (50% Artificial Sand) | 48.40(7.02) | 14.53 | 44.31(6.43) | 9.27 |
Mix 3 (100% Artificial Sand) | 42.51(6.17) | 0.59 | 41.36(5.99) | 2.00 |
Table 4: Test results of cement mortar of proportion 1:3
Percentage replacement of natural sand by artificial sand | Mortar mix proportion 1:3, w/c=0.5 | Mortar mix proportion /c=0.55 | ||
Compressive strength MPa (ksi) | Percentage increase of compressive strength with respect to reference mix | Compressive strength MPa (ksi) | Percentage increase of compressive strength with respect to reference mix | |
Mix 1(Reference Mix) (0% Artificial Sand) | 28.26(4.09) | – | 27.63(4.00) | – |
Mix2 (50% Artificial Sand) | 41.53(6.02) | 46.95 | 40.05(5.81) | 44.95 |
Mix 3 (100% Artificial Sand) | 35.81(5.19) | 26.71 | 35.15(5.09) | 27.22 |
Table 5: Test results of cement mortar of proportion 1:6
Percentage replacement of natural sand by artificial sand | Mortar mix proportion 1:6, w/c=0.5 | Mortar mix proportion 1:6,w/c=0.55 | ||
Compressive strength MPa (ksi) | Percentage increase of compressive strength with respect to reference mix | Compressive strength MPa (ksi) | Percentage increase of compressive strength with respect to reference mix | |
Mix 1(Reference Mix) (0% Artificial Sand) | 12.42(1.80) | – | 10.62(1.54) | – |
Mix2 (50% Artificial Sand) | 19.95(2.89) | 60.62 | 17.00(2.47) | 55.25 |
Mix 3 (100% Artificial Sand) | 16.19(2.35) | 30.35 | 14.55(2.11) | 37.01 |
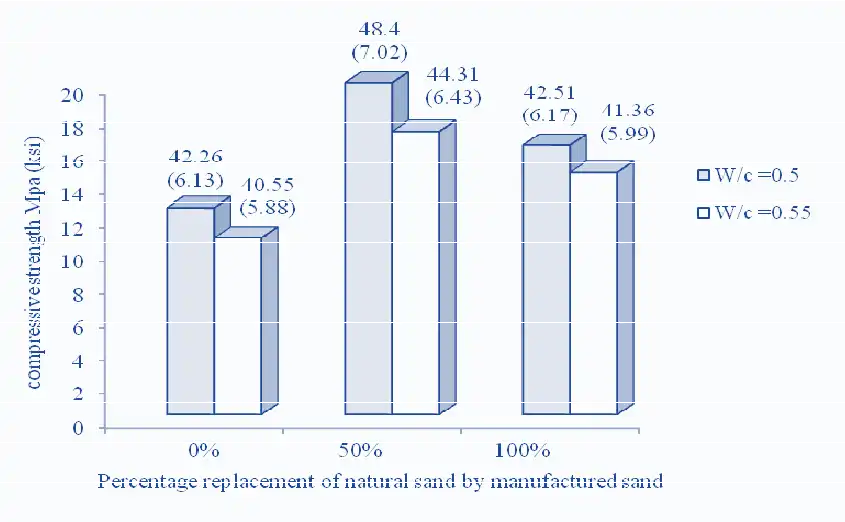
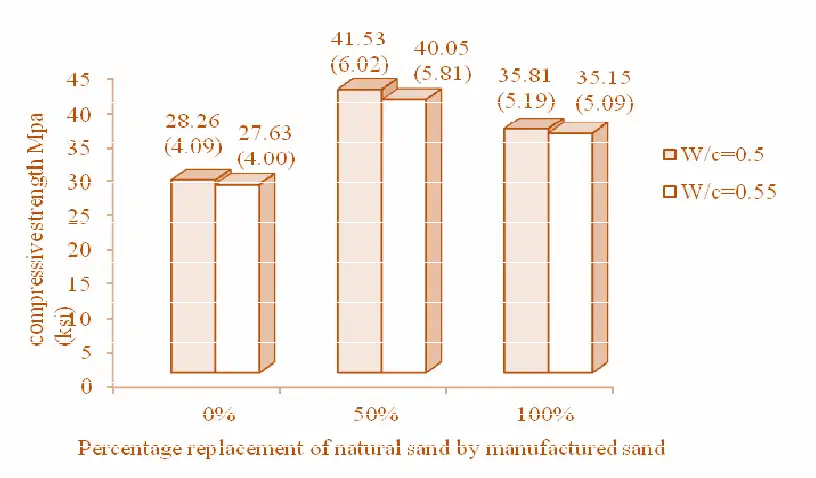
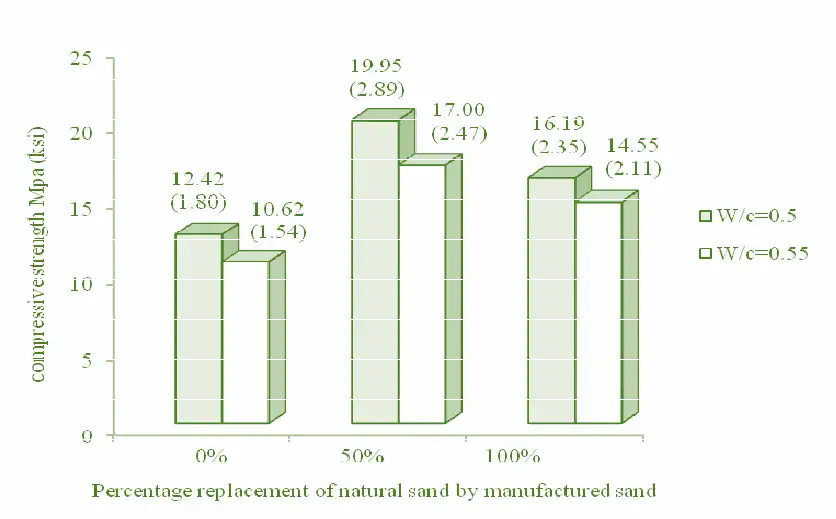
E. Conclusions
The effect of partial replacement of natural sand by artificial sand on the compressive strength of cement mortar of proportion 1:2, 1:3 and 1:6 with water cement ration as 0.5 and 0.55 are studied. Results are compared with a reference mix of 0% replacement of natural sand by artificial sand. The compressive strength of cement mortar with 50% replacement of natural sand by artificial sand reveals higher strength as compared to reference mix. The overall strength of mortar linearly increases for 0%, 50% replacement of natural sand by artificial sand as compared with reference mix (Mix 1). Artificial sand has a potential to provide alternatives to natural sand and helps in maintaining the environment as well as economical balance. Non-availability of natural sand at reasonable cost, forces us to search for alternative material. Artificial sand qualifies itself as a suitable substitute for river sand at reasonable cost. The artificial sand was found to have good gradation and nice finish which is lacking in natural sand and this has resulted in good cohesive cement mortar.
About the author;
The author has more than three decades of experience in multi-disciplinary transactions ranging from industrial projects to real estate development projects. Expertise in planning, undertaking demand assessment studies, transaction services, project execution, business development, etc. including marketing strategies based on technical market analysis, feasibility studies, program requirement derivation and fund and investor sourcing.
Almost 7 years experienced senior professional with project & construction management expertise in large projects for IT, Commercial, Industrial, residential sectors, etc. and more than 18 years of heavy engineering industrial projects like Fertilizers, Oil & Gas, Petrochemicals, etc.