The hydraulic bridge also known as “moving bridge” is a bridge that is used to allow seaside traffic through a body of water. In short, it can be moved to allow the passage for boats or ships. The bridge design incorporates an integrated hydraulic system into the bridge in order to carry more weight. The system is most suitable for arch-based bridges in which the main forces are directed in a horizontal sideways direction. The hydraulic system is integrated into the main load bearing members of the bridge can be minimally controlled by computers; however, if calibrated and constructed accurately, the system has the possibility for non-electronic autonomic self-adjustment which entails low maintenance cost and a reduced safety risk in an event of an electrical malfunction.
The integration of hydraulic gears with the existing hydraulic bridge models was introduced from the beginning of 20th century onwards. Smooth and accurate acceleration and deceleration, positive locking in any conditions, driving end locks, safe and easy operations, and ability to carry varying loads are some advantages of the hydraulic bridge.
Working mechanism of hydraulic bridge
Pascal’s law is the principle behind hydraulic bridge working. The hydraulic bridge uses petroleum-based hydraulic fluids for operations. Hydraulic motors and hydraulic cylinders are two important components used for powering the bridge with hydraulics. For a bridge operation, the amount of gearing required is dependent on the type of hydraulic motor. The hydraulic cylinders can be divided into tie rod and welded depending on the construction. The welded hydraulic cylinder is suitable for providing longevity for the bridge.
The bridge inherently distributes their forces in a lateral/horizontal direction at the supports at the reactions. This includes bridges based on the arch, such as bowstring arch bridges. At the midpoint of the arch there is a pinned connection, essentially making it a three hinged arch (two at the supports). This implies any loading will cause the arch to spread out and this is taken advantage by the hydraulic system.
Why are we need hydraulic bridges?
Generally bridges that rise and fall are on main waterways used by shipping and the clearance under the bridge is insufficient to allow safe passage underneath it and often affected by rise and fall tide levels. Often the raising of roadway levels to give height on a bridge is not practical and of course over time shipping is getting larger and larger to reduce emissions and cut transport costs, which would require greater clearance on bridges, and on fixed bridges could be no longer able to go under.
Advantages of hydraulic bridge
If accurately calibrated, there is no need for computers to control the hydraulic actuators. The hydraulic rams can be in motion only by the loading applied to it. That is to say, if a certain load is applied on the bridge, the hydraulic ram applies an appropriate force upwards to counteract any deflections. This implies that there is very little maintenance concerning automated systems and in situations such as blackouts or malfunctions, the bridge will not be in any immediate concern for failure. As a result of applying a force upwards that is dependent on the load and displacement of the bridge, the quantity of material required to construct the bridge is reduced. The material alone does not have to handle all imposed loading; the load is distributed onto the hydraulic rams. Its advantages includes;
- Ease and accuracy of control; By using simple levers and push buttons the operator of a hydraulic system can easily start, stop speed up and slow down
- Multiplication of force; Fluid power system without using, cumbersome gears pulleys and levers can multiply forces simply and efficiently from a fraction of a Pound to several hundred tons of output
- Constant force and torque; Only Fluid Power Systems are capable of supplying constant force and torque regardless of the speed changes
- Simple safe and economical; In general hydraulic systems use fewer moving parts as compared to purely mechanical and electrical systems thus they become simpler and easier to maintain
Types of hydraulic bridge
There are three main types of the hydraulic bridge as given below;
Bascule Bridge
The Bascule bridge is a subcategory of drawbridge. These bridge can be a single leaf or double leaf. s fixed and supported on an axis that is perpendicular to the longitudinal axis of the bridge and the horizontal axis is located at the centre of gravity. Single leaf bascule bridges are similar to draw bridges. Whereas, the double leaf bascule bridges will split in the middle. These bridges are structurally sound, reliable, and economical.
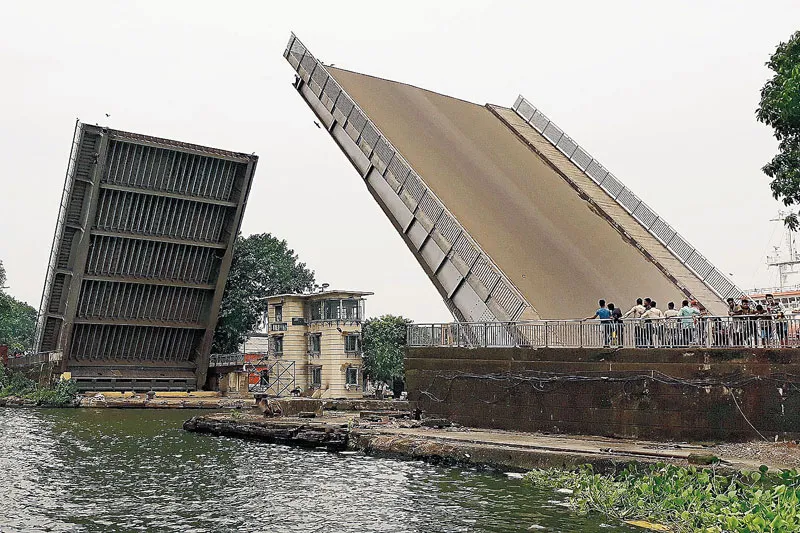
Swing Bridge
The swing bridge uses a rotating design. It will rotate at an angle of 90° in most cases. The rotating structure will be present at the centre or at both ends of the bridge. It’s fixed on the horizontal plane that turns around the vertical axis to give way for the water traffic and the bearing is installed on a pivotal pier.
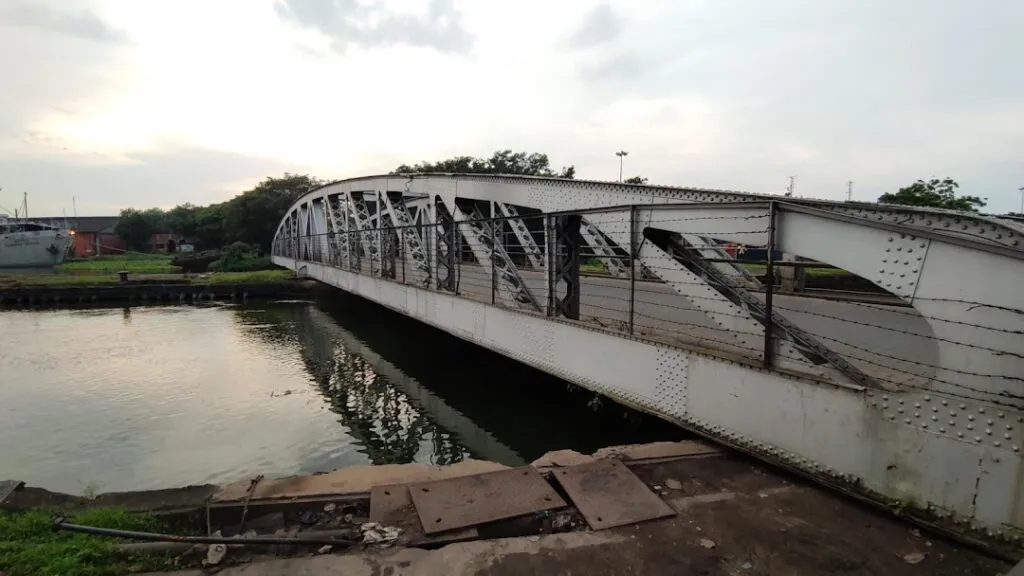
Lifting Bridge
Lifting bridges will move the bridge surface in vertical direction for opening water transportation. It is constructed and consists of a span of a common type of truss and at the end of the span, supported by towers.Another type of lifting bridge is double vertical lifting bridge, which is divided into two parts and balanced by a central tower.
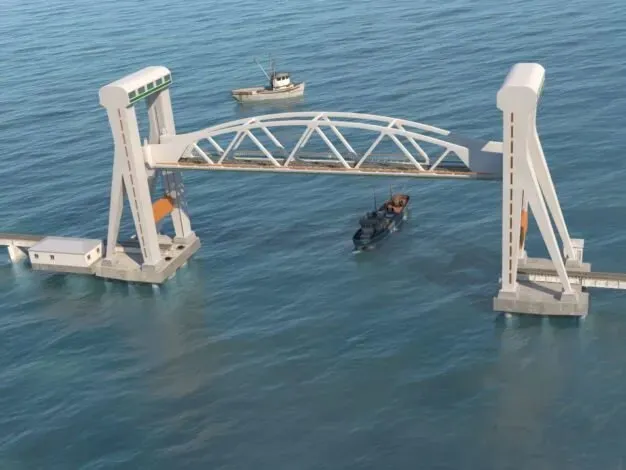
Conclusion
The purpose of hydraulic engineering is to design a structure with the proper capacity to divert or remove water from the roadway and pass collected water under the roadway. The design of a hydraulic structure requires knowing how much water is associated with the design storm and calculating the velocity, depth, and type of flow that must be accounted for in the design. In an upcoming article, we will discuss in detail the different types of hydraulic bridges, as well as the importance of effective water flow management in various engineering systems—much like the precision needed in the design of Slot Online No. 1 Indonesia, where smooth operation and efficient user flow are paramount for success.