Grouting is very essential for post-tensioned elements for the protection of high tensile steel elements as well as for better behavior at the ultimate stage of bonded cables. Cement grout surrounding the steel element provides an alkaline environment which protects the steel from corrosion. Hence it shall be ensured that grout is present in the entire duct without any hollow pockets and that a good bond exists between the steel and the duct. Grouting shall be carried out preferably within 3 days or a maximum of 7 days of final stressing.
Corrosion behavior of grout/prestressing strand system should be tested to verify that grout will resist aggressive substances and protect prestressing steel from corrosion. To evaluate the corrosion protection capability of different grout mixtures samples with embedded prestressing steel were prepared and potentiodynamic anodic polarization was performed. From corrosion testing, it was concluded that grout with low chloride diffusion coefficient, good homogeneity, and volume persistence could assure longer durability of prestressed structures.
The currently applicable European Standard EN 447 “Grout for prestressing tendons – basic requirements” provides general guidance and defines test procedures for quality control of grouts, but there is no guidance for grout formulation.
Grouting procedures for post-tensioning system
Grouting requirements
The requirements of the grout are fluidity and low sedimentation in the plastic state. In the hardened state, it shall be dense, have low shrinkage, and be durable. The grouting technique adopted should be such that it can be carried out easily and effectively. The grout shall be made from the cement specified section and water conformation. Fine sand passing 150 mm IS Sieve may be added only for ducts of very large size. If permitted by the engineer-in charge, admixtures may be added to improve the performance of the grout. The water-cement ratio for neat cement grouts should be generally 0.40 by mass or less. To ensure that grout of low-water cement ratio does not set too early a stage, the grout shall be maintained at a low temperature, generally not exceeding 18 degrees celsius, while being pumped. The compressive strength of 100 mm cubes of the grout shall not be less than 17N/mm2 for 7 days. Test cubes shall be cured in a moist atmosphere for the first 24 hours and subsequently in water.
Grouting equipment
The grouting equipment shall consist of a –
- A mixer
- A holding tank for the grout and
- A pump
The mixer shall be of a high-speed colloidal mixing type capable of mixing with high local turbulence while imparting only a slow-motion to the body of the grout. A grout screen should be fitted to remove the clots from the grout, which can block the pump or the duct. The pump and the injection equipment shall be capable of continuous operation with little, if any, pressure variation and shall have a system for recirculating the grout while actual grouting is not in process. Compressed air systems must not be used for grouting work. The pumping equipment shall be able to deliver the grout at a nozzle pressure of at least 0.7N/mm2.
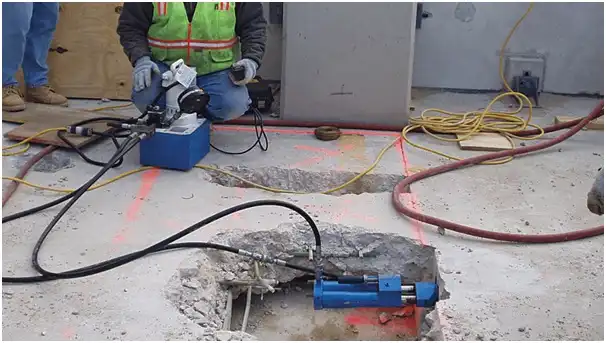
All piping to and from the grout pump shall have a minimum of bends, valves, and changes in diameter and the delivery hose shall be as short as practicable. All piping, pumping, and mixing equipment should be thoroughly washed with clean water after each series of operations or more frequently if necessary. In any case, the intervals between the washings shall not exceed 3 hours.
Grouting Mixing
Water shall be measured and added to the mixer first, followed by cement. When these are thoroughly mixed, any additives and sand if any shall be added. When all the ingredients have been added, mixing shall continue for at least two minutes. The mixing time shall be following the results of the stability test and should not exceed four minutes.
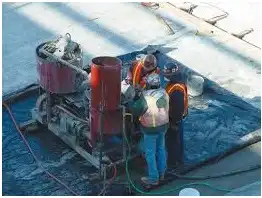
Duct preparation for grouting
Ducts shall be kept clean at all times. Unwanted opening at anchorages and in any other locations shall be sealed before grouting starts. In all long duts, or in any duct where considerable changes of level occur and in any large diameter ducts, rout vents shall be provided at all crests and intervals of 20 m to 30 m so that grout can be injected successively through vents as the grout flows along the ducts. When water is likely to enter ducts, valley vents shall also be provided for drainage.
Grouting Injection
Grouts should be injected from the lowest to the uphill point, wherever practicable so that air and water in the duct, being less dense than the grout, will be pushed ahead of the grout mix and be less liable to become entrapped in the grout mix. Before starting the injection grouting ensure that in which place you have to do grout, Suppose it may be a basement crack, void, and any Honeycomb. That is most important to know about the place where the grouting is going to be done. It may be on height or base if on the height you require a high-pressure injection grout machine it may be manual or automatic.
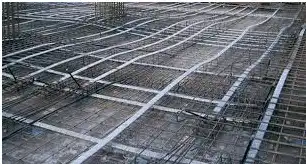
Regrouting
Grouting may be complemented by subsequent regrouting in certain cases wherein the entrapment of water is suspected or anticipated.
Grouting blockages
If a blockage is encountered in a cable, it should be ascertained whether the blockage is in the grout hose or the duct. A blocked hose can be uncoupled and cleaned by pumping water through it, or it can be replaced by a new hose. A blocked duct can generally be cleaned by blowing water or compressed air through it and special actions will have to be taken.
Image Source- Youtube, structural.net, noorps.com, dsi usa