Epoxy Coated Rebar acts as a barrier system intended to prevent moisture and chlorides from eroding the surface of the reinforcing bar. It rebars corrosion performance. Epoxy Coated Rebar is used to provide additional protection in environments where reinforcements are subjected to accelerated corrosion. The use of these bars is significantly increasing as the concrete use is becoming more diverse in corrosion-prone areas. Epoxy coatings provide optimum protection against abrasion, turbulence, corrosive fluids and extreme temperatures. Epoxy coated rebar is not only durable but also resistant to many corrosive substances. It offers corrosion resistance especially for marine structures.
These types of bars are coated with Fusion Bond. These coatings are in the form of dry powder at normal atmospheric temperature. The powder is applied electrostatically to the surface of cleaned hot steel bars and cured to form a protective film after undergoing various chemical processes. The epoxy-coated rebars last longer due to the protective film and thereby contribute to the quality of construction. A good quality Epoxy Coated TMT Bar must have a uniform coating, Chemically stable and adhere to a high pH environment.

Manufacturing of Epoxy Coated Rebar
The manufacturing process of Epoxy Coated Rebars involves 4 important steps, surface preparation, induction preheating, fusion with epoxy powder application and curing. Coating operation involves moving the straight length of steel through the application process on a rapidly moving conveyor. Specialized coating operation units may use a special hanger system. The steps are as followed;
- The process starts with rebars positioned into shakeout table or fluidization bed where it is spread out to a conveyor system
- The steel is visually inspected for oil, grease and other contaminants
- The steel is then moved towards a blast cleaner wherein the contaminants are removed
- The steel is now ready for proper coating
- Bars them pass through a powder spray booth where spray nozzles embed a dry epoxy powder
- Electrostatic charges are then pushed into the powder particles resulting incomplete and even coating
- As dry powder heats the hot steel it melts and flows into the peaks and valleys of the steel covering and conforming to the bars
- Following the powder application, the coating is allowed to cool for 30- 40 seconds
- The coating cures to a hardened state and develops most of its beneficial properties
- Air or water quench often follows the curing period to cool off the bar and facilitate handling
- The coated bars are passed through a cooling tunnel after curing, where water is sprayed on the bars to cool them
- The bars are then transferred to the final inspection rack for testing and inspection.
Different test methods for checking the quality of Epoxy Coated Rebar
Apart from the manufacturing process, there are several test methods to confirm the quality of the Epoxy Coated TMT Bar, which are given below.
- Test Method for holiday detection
- Test Method for coating thickness
- Test Method for impact strength
- Test Method for bendability
- Test Method for bond strength
- Test Method for alkali resistance
- Test Method for corrosion resistance
Advantages of Epoxy Coated Rebar
Plain steel often falls prey to corrosive forces over time. As rust forms on the outside of the embedded rebar, it exerts an increasing amount of pressure on the surrounding concrete. This can cause the concrete slab to spontaneously crack, while also making the concrete more vulnerable to damage caused by blows and compressive forces. The surface of the concrete may develop patches of spalling, creating rough and unattractive areas. Epoxy-coated rebar prevents corrosion and the problems that it causes and offers a multitude of advantages.
- The coating layer is firm and stable which offers good tenacity and high insulation
- The coating layer is corrosion-resistant
- Lower maintenance cost
- Lower lifecycle costs over time
- Uniform thickness of coating which adds to the quality of production
- Acts as an insulator for electrochemical cells and offers barrier protection to steel which prevents the entry of chloride ions
- Excellent adhesion and it forms a lasting bond with the surface of the steel rebars
- High mechanical impact strength.
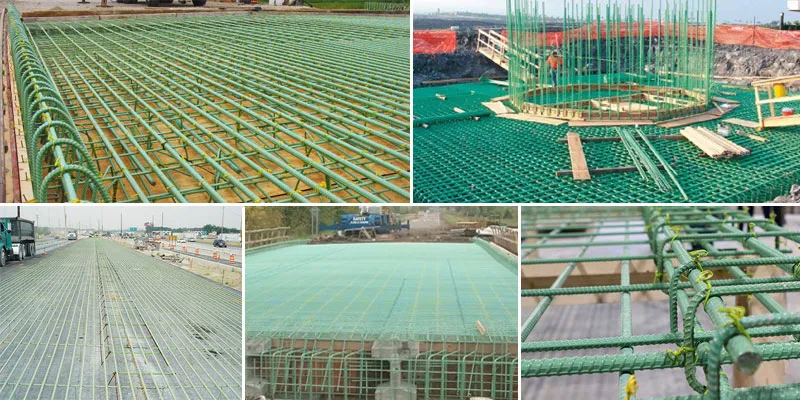
Applications of Epoxy Coated Rebar
Epoxy Coated TMT Rebars are used in concrete subjected to corrosive conditions. These may include exposure to deicing salts or marine environments.
- Underground buildings
- Bridges
- Pavements
- Offshore structures.
- Parking structures.
- Marine structures
Conclusion
The Epoxy Coated Rebar comes with an array of advantages and applications which has been discussed. We will keep you updated on the latest trends related to TMT bars in upcoming articles.
Image Source: dimensionfabricators.com, blackswampsteel.com