Due to the soil and groundwater condition, it is critical that the structure is protected from groundwater infiltration and a suitable site-specific waterproofing system be selected for the structure. Tunnel waterproofing is one of the most demanding and challenging sectors of the tunneling industry. Waterproofing systems are faced with very strict requirements regarding durability, exposure, sustainability, and stress conditions, which demands well thought out construction methods and sequences for ease of application and total cost management. Poor waterproofing fails to protect the tunnel against damage from moisture and can result in the unintentional entry of water, soils, or chemicals.
Problem with tunnel water ingress
With respect to the durability of underground structures, the ingress of water is usually the most important factor to be considered. The International Tunnelling Association (ITA) Working Group on Maintenance and Repair of Underground Structures prepared a report on the damaging effects of water on tunnels during their service life, based on case histories collected from many countries, reflecting the worldwide practices as well as different lining methods. Seventeen types of defects have been identified and specific remedial measures have been indicated. Some of the defects are intrinsic to specific lining types but it can be stated that deficient waterproofing is at the origin of most problems. A problem that has increased in urban tunnels is related to chemically aggressive groundwater. For such cases, considerations of chemical interactions of pollutants with the waterproofing system are of major importance.
Different types of tunnel waterproofing system
There are numerous waterproofing systems available, some of the important ones are discussed below.
Liquid waterproofing system
Liquid systems have the longest track record and generally comprise the hot-applied rubber, tar, polymers and asphalt emulsions. These systems are applied hot and require electric or propane fired kettles to raise the temperature of the material to approximately 100 degrees. The necessity for a kettle requires additional manpower and the materials are placed by hand with either mops or squeegees.
Panel waterproofing System
Panel systems are those systems that use swelling Bentonite encapsulated either in a fabric roll or cardboard. The Bentonite must swell to create an effective waterproof barrier. This swelling occurs generally within 4 hours of contact with water. This system requires the panel to be placed in “the dry” and attached to the concrete. The locations of the attachments must be coated with mastic to seal the penetrations in the panel.

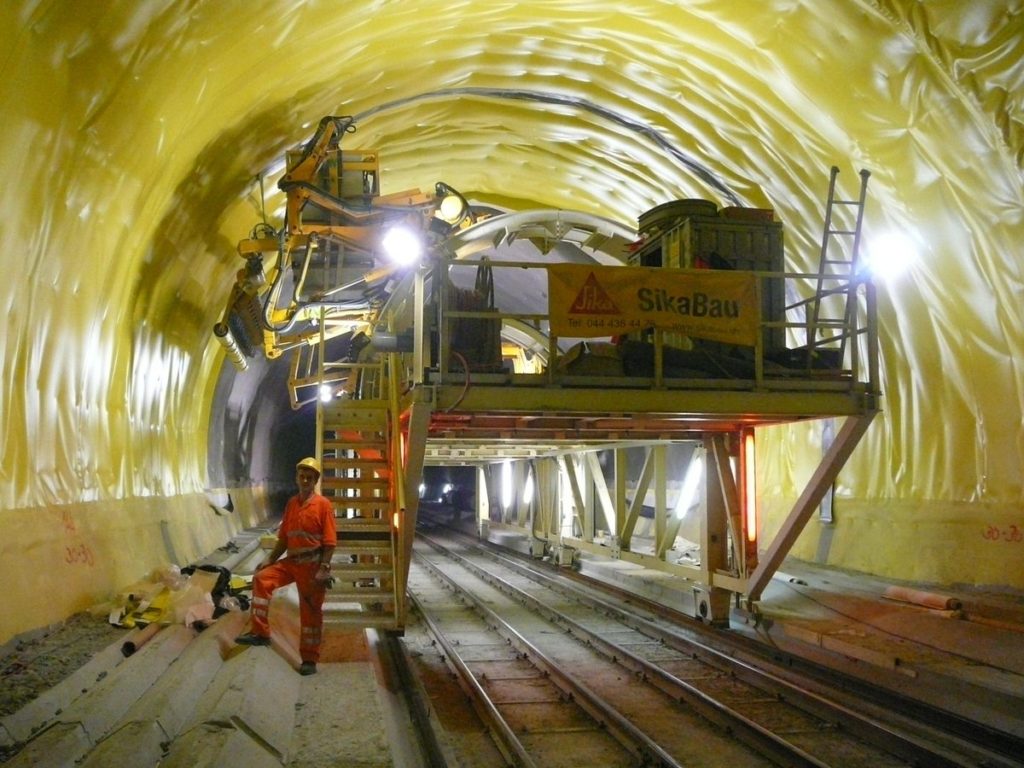
Membrane waterproofing system
Membrane waterproofing systems are applied to either vertical or horizontal surfaces. Membrane systems consist of a membrane, a protection course, a drainage medium, and a layer of filter fabric. When the concrete surface does not have a uniform texture certain membrane materials will 3 require a parging layer which is used to fill in pinholes or voids. This parging layer ensures that the membrane has a uniform surface for complete bonding.
Sheet Membranes waterproofing system
Sheet membrane systems are available in Rubber, Neoprene, high-density polyurethane, (HDPE) and combinations of rubber and HDPE. They are provided as rolls usually approximately 2-3 meters in width and are self-adhered. During application, the roll is laid out flipped over and the backing removed. The sheet is placed onto the concrete with the adhesive in contact with the concrete and pressed into place. The sheets can be applied either as a blindside waterproofing against sheet piling or a temporary support system or can be applied after partial cure of the concrete. The blind side does not require a protection board; however, normal installation requires the use of a protection board.


The epoxy Liner waterproofing system
Epoxy liner systems were first developed for use on bridge decks under railroad ballast. They are two-component systems and generally are produced in two formulations: one for horizontal surface and one for vertical surfaces. The difference is that the vertical material is non-sag to better adhere to the vertical surfaces. The formulations are not interchangeable due to the requirement to have non-sag for vertical surfaces to develop the required thickness. Typical installation of epoxy systems is performed by spraying the epoxy.
The spray-on waterproofing membrane system
The spray-on waterproofing membrane is a new system in tunnels with single shell linings. The conditions of the application of this system are analyzed in terms of the deformation and surface condition of the first layer of the shotcrete shell, water ingress and water pressure behind the waterproofing membrane. This method can bond to both the primary and secondary linings. This offers maintenance and repair benefits by preventing the movement of water either behind or, should it be breached, in front of the membrane. The application of the membrane is very simple and can be executed by a dry shotcrete machine. For the thin-stream transport of powder to the nozzle, compressed air is needed. The water added in the nozzle should show a minimum of 2 bar static pressure. The product is fed into the hopper of the dry mix machine, blown through the hose to the nozzle, where water is added. The nozzle can be easily handled manually by one man with a helper and an application capacity of more than 50 m2 /h is quite normal.
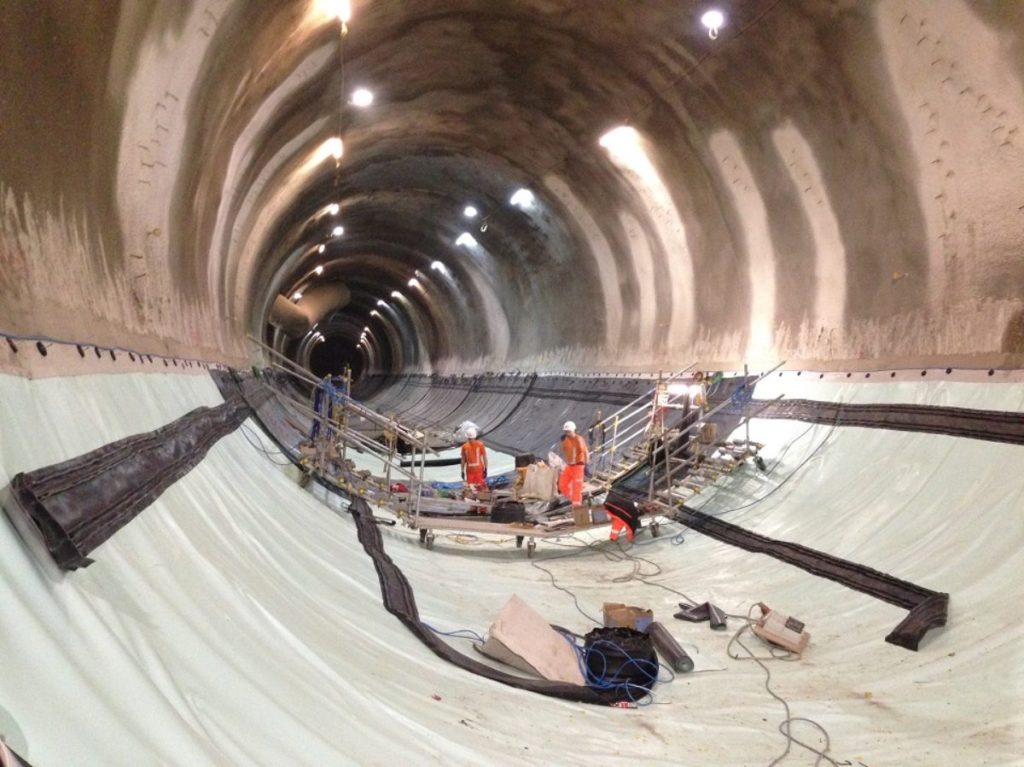
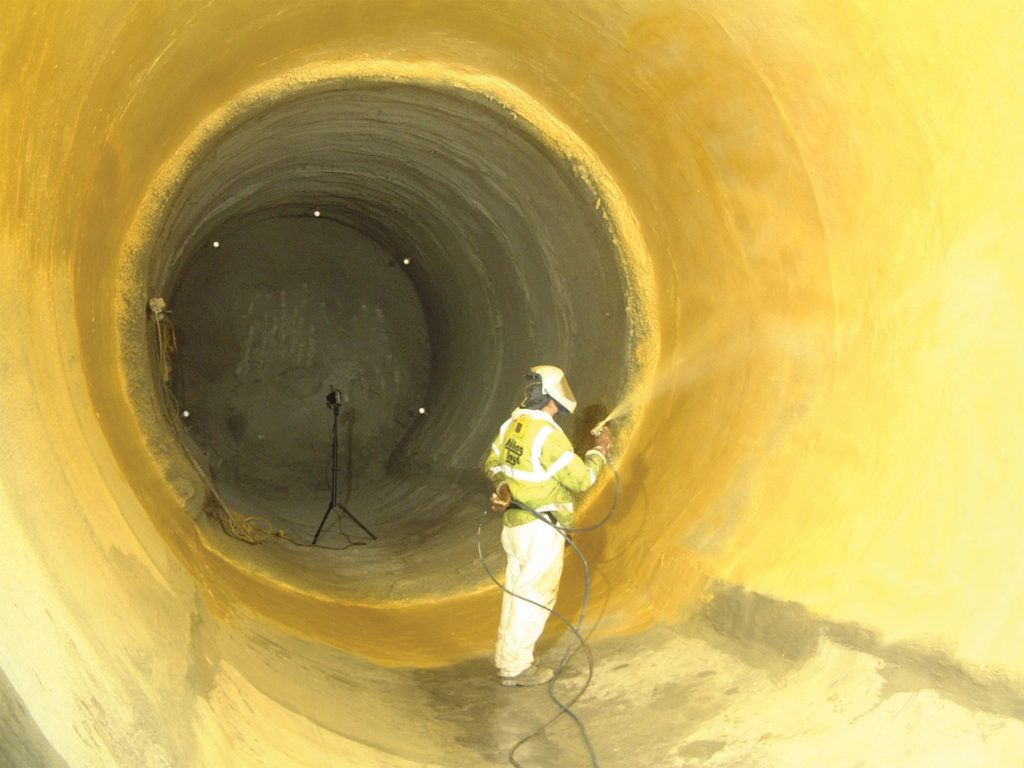
Cementitious Waterproofing System
Cementitious waterproofing systems are a blend of co-polymers and Portland cement. These materials use the copolymers to reduce the pore size of the concrete to prevent the passage of the water molecule through the coating while allowing water vapor to pass. These coatings are generally used on the negative (interior side) of structure in rehabilitation projects where the exterior concrete surface is not accessible. However, it has been used on exterior surfaces of tunnels with success.
Hybrid waterproofing system
Hybrid below-grade water-proofing membranes combine active polymer barrier technology with conventional passive-bonded product technology in an effort to counter failure trends. By incorporating multiple barrier materials in a single waterproofing membrane, the new active polymer hybrid membranes compensate for the shortcomings of traditional materials in relation to workmanship and dependence on perfect installation to prevent failure. By recognizing modes of failure in traditional membranes, new active products are being engineered to prevent failure by combining different material layers that increase the failure modes that must occur at a specific location for water ingress to occur.


Conclusion
Waterproofing is critical in deep tunnel applications because the stakes are so high. Maintenance or repair work typically would cause a serious interruption in service, so the job has to be done right. A failed waterproofing job, though, is not only inconvenient but dangerous. The long service life of tunnel constructions requires the durability of all components. A major part in this context plays the waterproofing layer and various components, especially those which are supposed to blend together, like PVC disks, Waterbars, Flanges etc. The designers, owners and project managers should select the complete system judiciously and understand in detail the functioning of each component. These measures along with the expertise of the manufacturer selection are critical for tunnel waterproofing.
Image Source: normet.com, twitter.com, worldhighways.com, soprema.co.uk, extruflex.com, WR Meadows, Tunbnel Talk.com, Soprema Uk, sika
Comments are closed.