Precast concrete components are made using steel moulds due to several repetitions, generally above 500. Usually, precast components are cast on steel moulds. However, if the quantum of the precast elements to be produced is very less, it will not be economical to make steel moulds for such elements. Therefore plywood formwork may be used to produce such precast elements.
One can create any kind of mould based on the precast element designed. The mould designer uses steel plates ranging from 4 to mm, C-channels ranging from 50 to 200 mm, Angles ranging from 50 to 150 mm and flat bar thickness from 100 mm to 30 mm. Usually, the supporting steels such as angles/ channels/ flats used depend upon the plate thickness chosen based on the span of the mould designed. Hydraulic jacks for prestressing or tilting the table mould used range from 2 tons to 50 tons capacity. The common types of precast concrete molds are discussed below.
Types of precast concrete moulds
Column moulds
Columns are moulded horizontally, only in rare cases such as round columns, vertical moulds are used. Column mould consists basically of a formwork base with a fixed centre platform and movable side platforms. Sections of the mould with different lengths can be operated individually or hydraulically through coupling plates across the entire length. Using an optional sliding plate, which is connected to the side platform by means of a pulling mechanism, demoulding is made considerably easier. In this case, the finished concrete element together with the floor mould rests on the sliding plate and is separated from the centre mould surface before lifting out. Column moulds are also available with an additional mould unit for the production of the foundation footings. A pre-stressing unit can also be integrated for the production of prestressed concrete elements as well as a heating register. To compact the concrete, vibrators are attached to the steel side formworks or side frame grids.
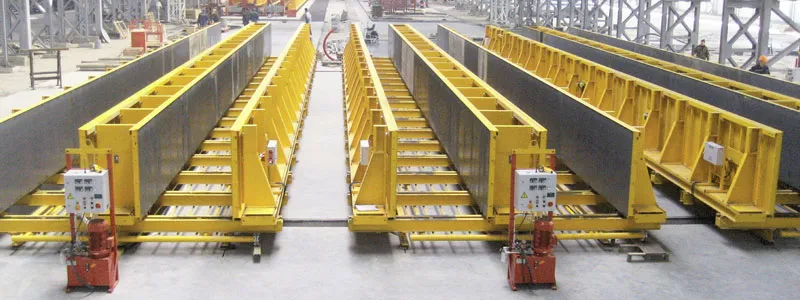
Beam moulds
Beam moulds are generally fabricated as system moulds, where one can cast more elements at a time. Beam moulds are manufactured following dimensions and tolerances stated in the related standards. There are two types either heavy duty plastic or steel. The beam moulds are made of Two part and clamp attached base plate steel molds are designed to be durable, resistant and easy to clean. These moulds are flexible, where you can adjust the height easily by raising the base of the mould and by changing the base you can have a different width of the beam.

Wall moulds
There are different types of wall mould being used in the industry widely. Each of them are explained below.
Battery mould – It is aset of moulds, where you can make a number of wall panels as the moulds are arranged adjacent to each other and all such moulds are braced. Battery moulds for precast concrete elements offer maximum productivity in minimum space. The battery moulds have been designed for vertical concreting of individual concrete panels and floor elements in various sizes and thicknesses. The system consists of several vertical chambers and can therefore produce various elements simultaneously.
Vertical Battery mould – The vertical battery mould allows manufacturing concrete panels with the desired dimensions and with a specific finish on both sides of the precast concrete panels. The vertical battery mould is a machine specially designed for high productivity of precast concrete panels in a small space. An additional benefit of this production system is that the precast panels are already extracted for its stockpiling and transportation in the final position which they will be installed on site. These moulds are designed to produce special wall panels such as walls with chajja, lift walls or any other special walls for architectural requirements.
Tilting mould – This mould is used to cast the wall panels in the horizontal position and then tilting the entire mould upto 90 degree. The panels are then handled, tacked and transported to site in vertical position. The tilting of the mould is done using the hydraulic jacks. In this mould we will get mould finish only one side of the wall and the other side manual troweled finish and hence requires a skilled mason to complete the finishing works.
Flat/table mould – These kinds of moulds are used commonly for making slabs and wall panels as the cost of these moulds were much lesser comparatively. A common bed shall be prepared and the side form shall bde custom made as per requirement. Here the wall panels are cast flat on the bed. It is then handled and transported in the horizontal position of the site. During the erection of the wall panel it is tilted using the cranes and put in position.
Slab moulds
Slab moulds can be classified into prestressed hollow core slab moulds, prestressed plank moulds and non-prestressed slab moulds.
Prestressed hollow core slab moulds – Hollow core slabs are prestressed slabs where the tendons are used. Therefore prestressing the tendons arrangement has to be made using proper mono or multi stressing hydraulic jacks. These slabs are cast on 1.2 m wide flat beds which are generally 80 to 120 m long. These slabs are produced using the extruders which have the side forms and the pipe for creating the hollowness in the slab.
Prestressed plank moulds – These planks are otherwise called prestressed solid slabs. These planks are usually 1.2/2.4m wide and it is a flatbed with side profiles. These flat beds are 80/100/120 m long. Prestressing the tendons, arrangement has to be made using the hydraulic jacks. The thickness of these moulds are usually 75/ 110/ 150 mm and the end plates prepared will match the thickness of the slabs with the slots for the strand patterns.
Non-prestressed slab moulds – These slab moulds are fabricated to produce customised individual slabs with varying sizes.
Staircase moulds
Staircase moulds are fabricated in an upside position. The landing slab shall be integrated with the flight of the stair or as a separate slab. These staircase elements produced are tilted after producing or at the site prior to installation time. It is recommended to use standard tread and riser dimensions. As and when these dimensions change another mould has to be fabricated to produce the same.
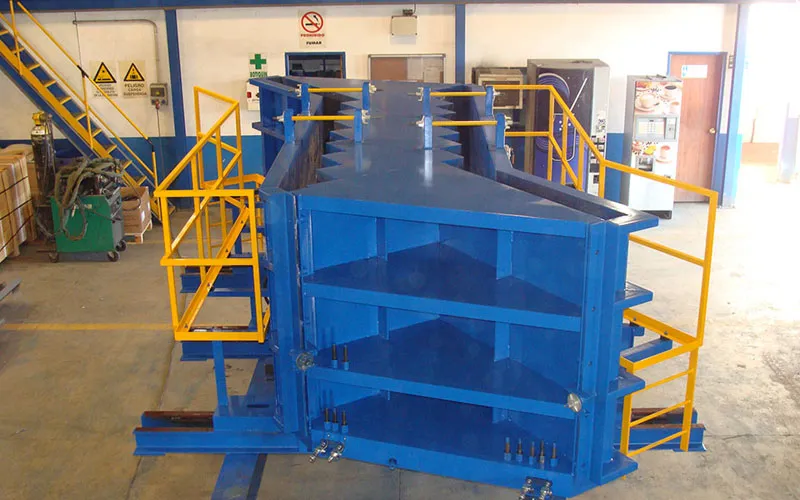
Customised moulds
Once can produce any kind of mould depending upon the requirement of the concrete products by the clients. Some of these moulds are- culvert mould, storm water drain mould, lintel beam with sunshades, tunnel moulds etc.
Conclusion
Whilst dimensional variations are inevitable, precast concrete products can be manufactured to comparatively fine permissible deviation. Tolerances shall be specific for the flatness of mould base, level of mould base, dimensions, fastener hanger positions, squareness of edge, position of openings and side mould profiles.
Image Source: vollert.de, nox-crete.com, weckenmann.com, bianchicasseforme.it, indiaprecast.com, m-konstruktor.com, moldtechsl.es, bft-international.com,