Manufacturers are focusing on coming out with compaction equipment models that are fuel-efficient and require minimal maintenance. With competition, intensifying suppliers are concentrating on coming out with machines that would ideally suit Indian working conditions. These machine models could be put through more work cycles. Ease of use and improved ergonomics are also design targets for manufacturers, who have long recognized that more comfortable machines can be operated more productively and for longer. Compaction machine technology is going through evolution with the integration of a Tier 3/Stage IIIA engine and oscillatory variant features. Discussed below are different types of soil compaction equipment used across projects in India.
Different models of soil compaction in India
Soil compactors with intelligent compaction technology
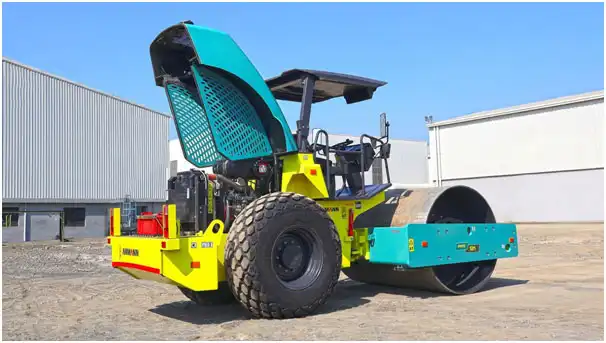
Newer compaction equipment combines existing features with intelligent compaction technology. It has great compaction output while offering improved efficiencies and cost savings as well. These are suitable for compaction of a wide range of soils, from silt to crushed stones. The machine is equipped with an efficient turbocharged, water-cooled engine ensuring non-stop performance with maximum reliability and lower operating cost.
The machine features newly designed cabs that set new standards in operator comfort and visibility. The single-drum rollers also are designed for fast and easy daily maintenance and long life. The powerful and robust 4-cylinder engine and heavy-duty hydrostatic drive of the differential axle ensure great traction and travel performance even under extreme circumstances. The roller is suitable for compaction of a wide range of soils, from silt to crushed stones. The machine is equipped with an efficient turbocharged, water-cooled engine ensuring non-stop performance with maximum reliability and lower operating cost. It provides the necessary flat base which provides the crucial support for construction foundations, pavements, roads and various other construction structures.
Tandem rollers with oscillation system
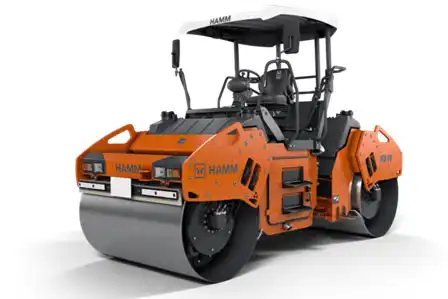
Oscillation systems help to achieve homogeneous compaction and of higher-quality. With oscillation, two unbalanced shafts rotate synchronously. The unbalances are offset by 180°. This causes the drum to carry out a rapidly alternating forward-backward rotary movement, with the result that the compaction energy is directed into the soil tangentially to the front and rear in the form of shear forces. In contrast to a vibrating drum, it acts dynamically on the soil all the time. Because the drum is always in contact with the ground, there is also a constant static load due to the weight of the machine.
Oscillation technology eliminates vertical vibrations and offers high compaction performance while producing a non-damaging oscillation movement. This transfers less stress to the surrounding surface, enabling compaction in more delicate application areas, such as bridges, over pipes and close to residential areas. Additionally, when compacting against a cold joint, the risk of damaging the cold surface is reduced, and the material can be more effectively compressed to seal and protect the surface.
Double-drum rollers with high centrifugal forces and 360-degree visibility
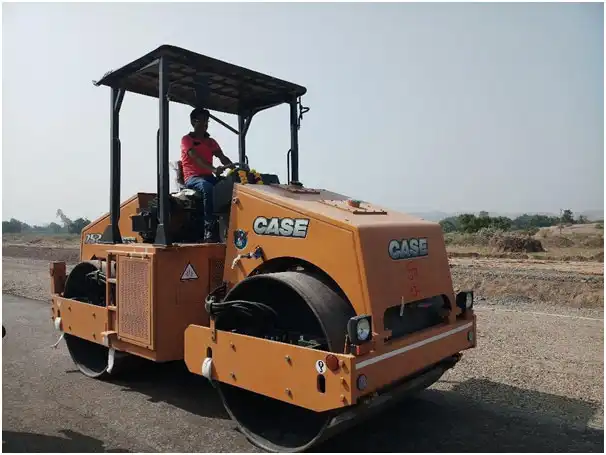
Modern compaction rollers comes with compact design and the weight equally distributed on both drums provide even compaction and easy transportability. The newer models also feature Heavy duty articulation joints to enhance the reliability of the machine in every working condition and terrain and large anti-vibration mounts for effective isolation and long life. The excellent grade-ability maximizes the machine’s versatility. The high steering angle allows the machines to work in very narrow spaces and to increase the compacting accuracy. The superior drum diameter ensures high compaction quality even in case of very irregular surfaces.
Pneumatic Tyre Roller for Medium and Large job sites
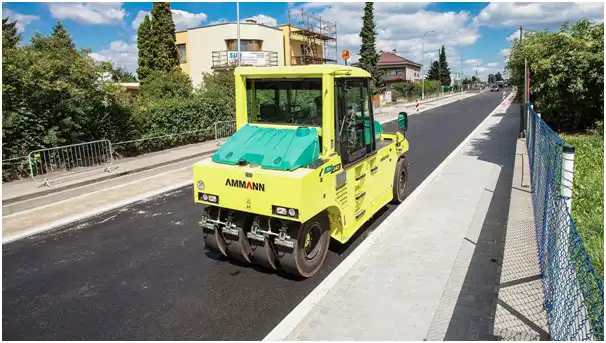
Pneumatic rollers have become more popular with stiffer mixes since they can help you achieve compaction density. These types of rollers consist of tyres that provide better static penetration into the materials. The weight of the machines and air pressure of the tires can be adjusted to meet the specific pressure desired on a particular job.
The adoption of the Pneumatic Roller particularly in the construction of roads is very necessary to avoid timely road damages, potholes, road breakage as a result of poor construction of the roads. The latest models come with a ballasting range of 9 tonnes to 24 tonnes with an Air-on-run system, which the operator uses to adjust tyre pressure without ever leaving the cab. Traction Control boosts productivity on tough terrain. The proven hydrodynamic propulsion system ensures efficiency.
Tandem Vibratory Rollers with lower fuel consumption
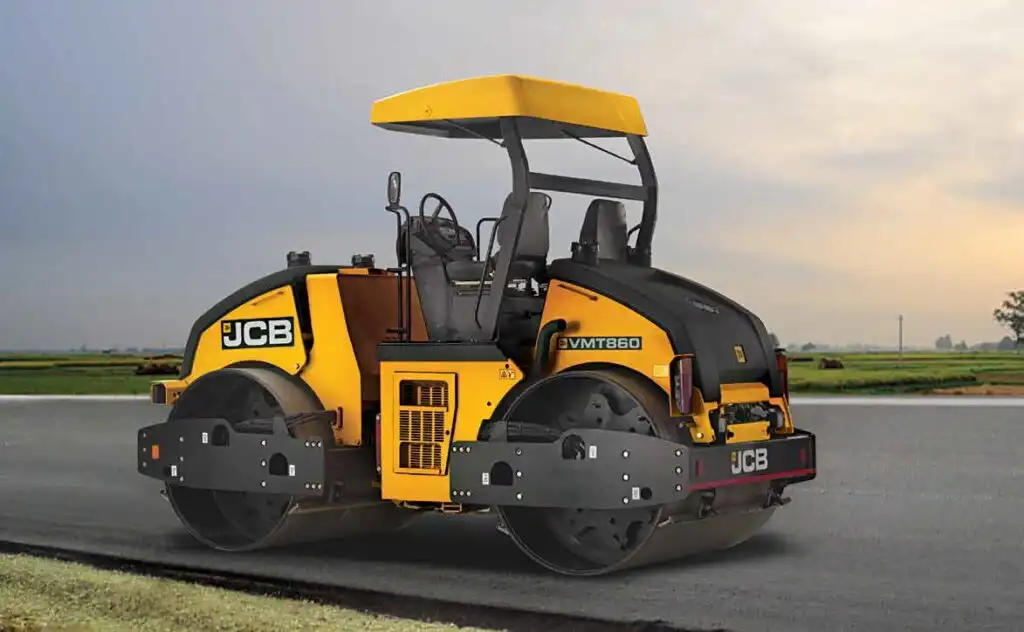
Tandem vibratory rollers are used primarily to compact paving materials, such as asphalt mixes and roller-compacted concrete. The modern tandem roller is powered by the ecoMAX engine, which also makes it highly fuel-efficient, providing the lowest fuel consumption in its class. Further, its maintenance-free vibration system and articulation joint, makes it a highly efficient vibratory compactor. The tandem roller also offers around 10%* higher productivity with the help of exclusive features like the unique drum offset provision. The machinery also has better serviceability due to its maintenance-free vibration system and articulation joint.
Tandem vibratory rollers are used primarily to compact paving materials, such as asphalt mixes and roller-compacted concrete. Modern machines feature two steel drums that vibrate via an internal, eccentric mechanism, which often can be adjusted to vary the frequency and amplitude of the vibratory action. Some tandem vibratory rollers are also equipped with satellite-navigation and proprietary software systems, continually report the degree of compaction and can map the job site’s compaction values for future reference.
Conclusion
The biggest challenge of Indian construction especially tough terrains provides resistance and is always hard work for operators. Therefore the machines have to be stringent enough to address the rough terrains. Soil compactors are being manufactured now which can efficiently compact varying soils and aggregates in applications such as highways, utilities, water retention structures, as well as in the preparation of commercial and industrial sites.
Image source – ammann.com, casece.com, writgen-group.com, jcb.com,