Bridge retrofitting is essential because they undergo structural weaknesses over time due to factors such as increased traffic, exposure to harsh environmental conditions, and changes in safety standards. These weaknesses can compromise the safety and functionality of the bridge, posing risks to both vehicular traffic and surrounding communities. Retrofitting involves implementing upgrades and reinforcements to strengthen the bridge’s structure, address existing deficiencies, and ensure it can safely support current and future loads. By retrofitting bridges, potential safety hazards can be mitigated, extending the lifespan of these critical infrastructure assets.
There are different methods for retrofitting methods, one such method is CFRP reinforcement method. The methods involves the use of carbon fiber fabrics on the surface of the concrete to form a composite that works in coordination with concrete to strengthen the component structure and improve its mechanical performance. Unlike traditional retrofit or reconstruction techniques, carbon wrap goes right over the existing substrate. This minimizes disruption during repair and saves significantly on installation time and costs. A case study is being discussed wherein the CFRP reinforcement method was used to restore the structural strength of the jetty using RELinforce™ range of Carbon Fiber products.
A thorough understanding of the site’s historical background, the problems it faced, and the reasons for opting for a retrofitting method were established. Following this, a bespoke solution tailored to the specific needs of the site was proposed. The entire process of application, from site preparation to the final steps of the retrofitting process, is documented in this case study.
Site Background and Problem Identification
The bridge, constructed approximately five decades ago, serves as the primary link on a highway connecting an essential industrial hub. Over time, the increasing volume of heavily loaded vehicles has led to visible signs of distress on the bridge structure, raising concerns about its safety and durability.
The continuous movement of heavily loaded vehicles has exceeded the bridge’s original design capacity, causing structural degradation and compromising its ability to support current traffic demands. With the bridge being the sole route for transportation in the area, addressing these issues was critical to maintaining uninterrupted connectivity and ensuring public safety.
Proposed Solution
To address the structural challenges while a new bridge is planned and constructed, a solution involving advanced materials and reinforcement techniques was proposed. This approach aimed to strengthen the existing bridge structure, enabling it to withstand heavy vehicular loads and potential seismic events until a permanent solution is implemented.
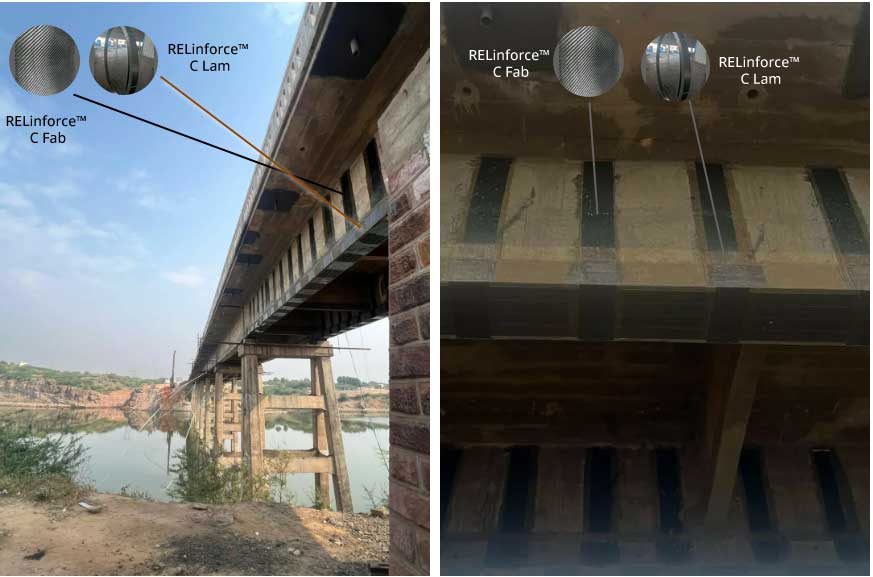
Materials Selection
High Modulus & Intermediate Tensile 5mm thick carbon laminate, RELinforce™ C Lam PU HS was utilized to enhance the load and moment capacity of the girder, enabling it to accommodate heavier vehicular movement as an alternative while awaiting the construction of a new bridge.
Additionally, U-wrap was applied using 530 GSM Carbon Fabric, RELinforce™ C Fab 530, to maximize the shear capacity of the girder, particularly crucial given the bridge’s location in an earthquake-prone zone. This comprehensive approach aimed to fortify the girder against increased stresses, ensuring its continued functionality until a permanent solution could be implemented.
Advantages of Using RELinforce™ products in the Bridge Retrofitting Project:
- Provided superior strength and durability, enhancing the structural integrity of the bridge.
- High modulus and intermediate tensile properties ensured it could withstand heavy loads and stresses.
- Provided additional reinforcement, particularly in shear capacity as the bridge was located in an earthquake-prone zone.
- Contributed to extending the lifespan of the bridge by reducing the need for frequent maintenance and repair.
- Provided lightweight solution, facilitating easier handling and installation during the retrofitting process.
- The corrosion resistance of carbon-based materials ensured protection against environmental degradation, further enhancing longevity.
Application process
- The surface of the bridge’s girder was thoroughly cleaned and inspected for any contaminants or debris that could affect adhesion.
- A primer was applied to the cleaned surface to promote adhesion between the existing structure and the reinforcing materials.
- The RELinforce™ C Lam PU HS carbon laminate was carefully applied to the girder, following precise measurements and strategic placement to enhance its load and moment capacities.
- The RELinforce™ C Fab 530 carbon fabric was strategically placed on the girder to reinforce its shear strength, ensuring comprehensive reinforcement.
- Pressure was applied to consolidate the laminate and fabric onto the girder, ensuring proper bonding and structural integration.
- The applied materials were allowed to cure and bond with the girder, typically under controlled temperature and humidity conditions.
- After curing, the reinforced girder underwent thorough inspection to ensure proper application and adherence to specifications.
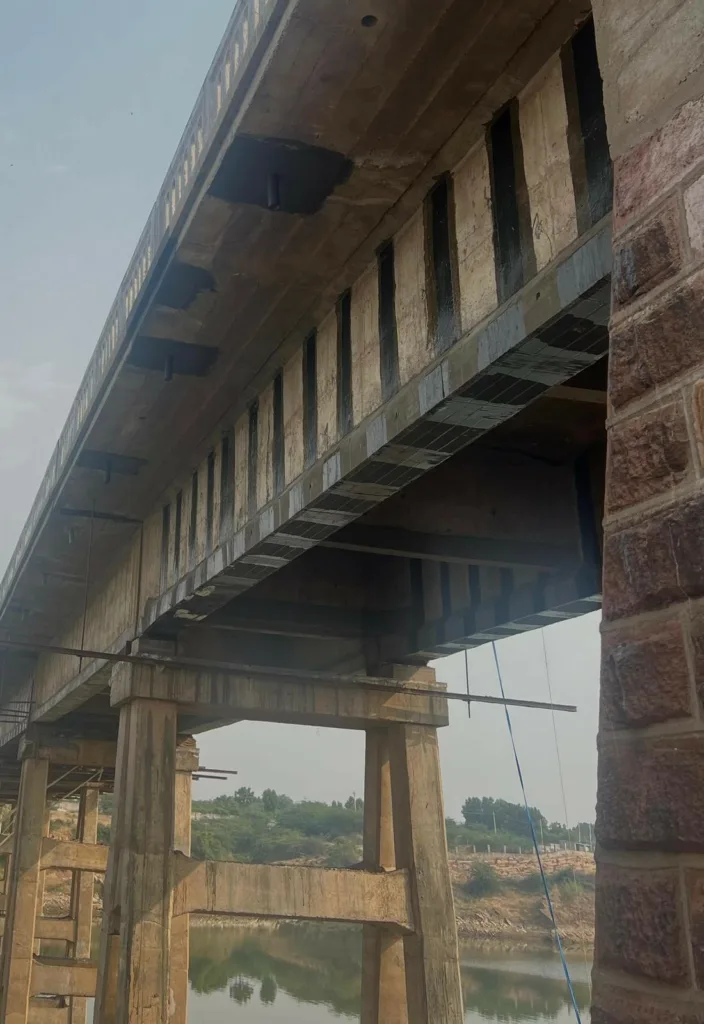
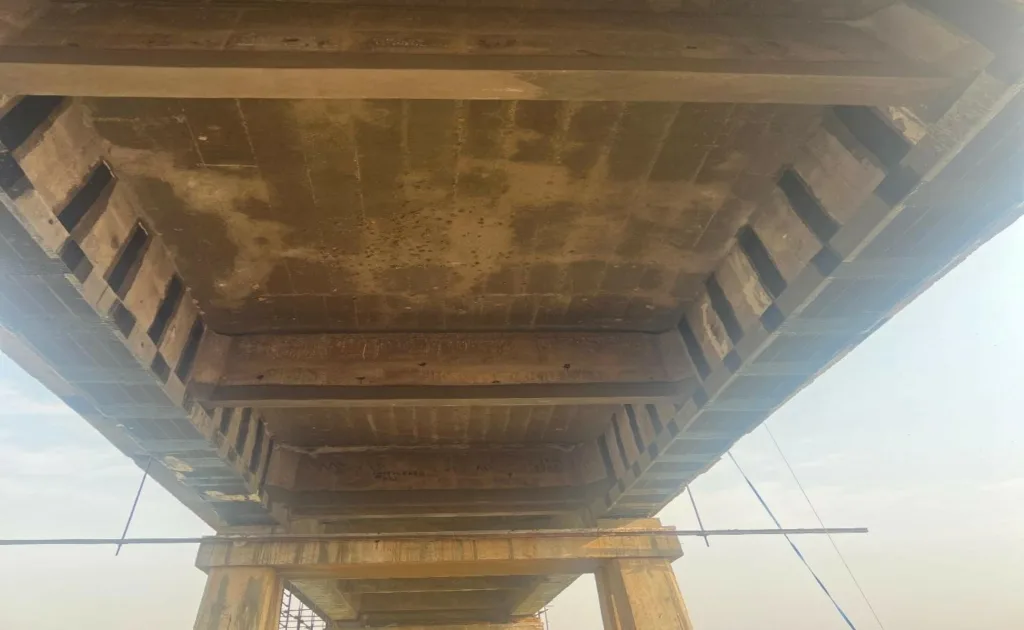
Bridge girder retrofitting with Relinforce™ products
Outcome Evaluation:
Following the application of reinforcement materials, a thorough assessment is conducted to evaluate the bridge’s performance under simulated loading conditions. During a 60MT load test, only minimal deflection (2-3mm) is observed at the centre of the span, demonstrating the effectiveness of the reinforcement measures in enhancing the bridge’s structural integrity and load-bearing capacity.
Final Report:
Through the strategic application of advanced materials and reinforcement techniques, the bridge’s structural deficiencies are successfully addressed, allowing for the continued safe passage of heavy vehicular traffic. This temporary solution provides a crucial interim measure to ensure uninterrupted connectivity for the industrial hub while plans for a new bridge are executed, highlighting the importance of proactive infrastructure management in safeguarding critical transportation networks.
About RELinforce™ Composite solution
RELinforce™ range of Carbon wrap & Glass Fiber-reinforced polymer products are manufactured and supplied under Reliance India’s Composites Solution Division. Reliance Industries Limited is India’s largest private and one of the most profitable private sector companies and the first Indian Fortune 500 company.
RELinforce™ product range is used for structural strengthening & protection of the structural members using guidelines that conform to international standards. These products just don’t repair degraded structures, but it makes the structures stronger even against harmful effects of seismic forces or further corrosion. There is a wide range of products combined with outstanding combinations of properties, such as low weight, immunity to corrosion, excellent mechanical strength and stiffness to tackle the issues on hand with ease.
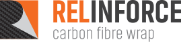
Reliance Industries Limited
Vadodara Composites Division, Vadodara – Halol Expressway, Vill – Asoj, Taluka – Waghodia, Vadodara, Gujarat 391510
Phone:+91-95104-03668
Email: Petchem.Relinforce@ril.com