Innovation in brick manufacturing has significantly transformed the construction landscape worldwide. Modern advancements in brick production techniques, such as the utilization of recycled materials or the development of high-performance brick varieties, have revolutionised traditional brick construction. By incorporating recycled materials like plastic or industrial byproducts, innovative brick manufacturing processes contribute to sustainability efforts by reducing waste and conserving natural resources. Additionally, specialized bricks engineered for enhanced thermal insulation, durability, and structural strength offer improved performance compared to conventional bricks, ensuring the longevity and resilience of constructed buildings.
In regard to growing innovation in brick manufacturing Canada-based PLAEX Building Systems Inc., has created lego-like recycled plastic bricks. Named “Plaex-crete,” these lightweight, durable, and eco-friendly bricks are poised to transform the construction industry. These bricks have undergone testing against bulldozers.
The Genesis of PLAEX-crete:
Plastic waste has long been a global environmental concern, with landfills brimming with non-biodegradable materials. PLAEX-crete emerges as a beacon of hope, utilizing recycled plastic sourced primarily from farm and agricultural waste. The innovative process involves extruding plastic into a cement-like paste, forming the bulk of the final product. Additional components, including colourants and UV inhibitors, contribute to the brick’s durability and aesthetic appeal.
By diverting plastic and aggregate waste from landfills, it mitigates environmental degradation and reduces carbon footprints. Unlike traditional construction materials, which often entail the extraction of natural resources and high energy consumption, Plaex-crete embraces a circular economy model, preserving finite resources and minimizing waste.
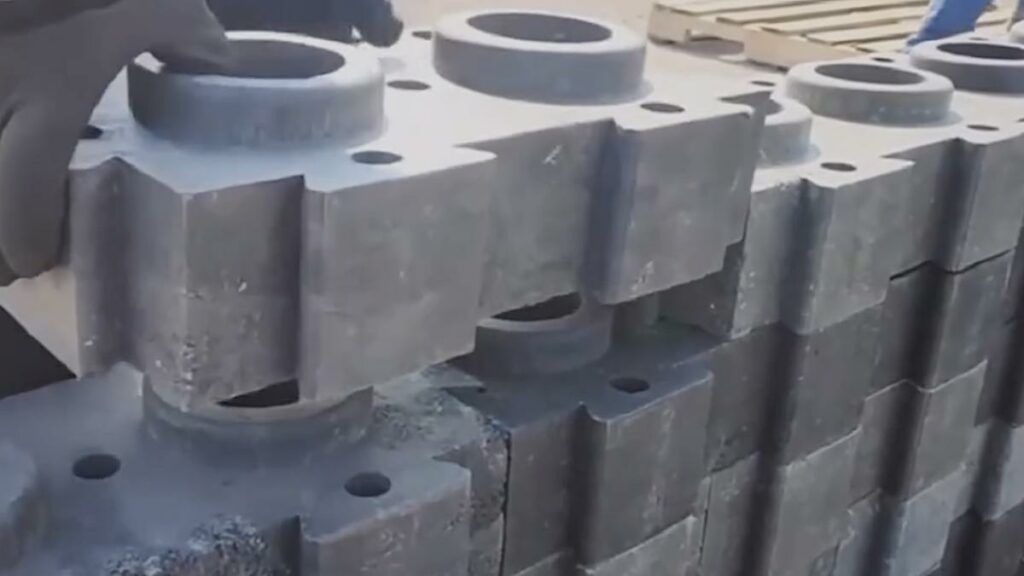
Composition and Manufacturing Process:
Composition:
The composition of Plaex-crete bricks revolves around a blend of recycled plastic and additional components to enhance durability and functionality. The primary ingredient, recycled plastic, constitutes over 90% of the brick’s composition. This recycled plastic is sourced from various partners engaged in extended producer responsibility (EPR) initiatives, emphasizing the utilization of plastic waste that would otherwise end up in landfills or oceans. The plastics used include PETE, LDPE, PP, and HDPE, which are commonly found in agricultural and farm waste streams.
The manufacturing process begins with the collection and sorting of the recycled plastic materials, ensuring quality and consistency. These plastics undergo a meticulous cleaning and shredding process to remove impurities and prepare them for extrusion. Once cleaned and shredded, the plastic materials are fed into an extruder, where they are melted and formed into a paste-like consistency. This paste serves as the base material for the Plaex-crete bricks, providing the bulk of their structure.
In addition to recycled plastic, the composition of Plaex-crete bricks may include supplementary components to enhance performance and durability. These components typically include colorants to achieve desired aesthetics, UV inhibitors to protect against sun damage and fading, and flame retardants to improve fire resistance. The precise formulation and ratio of these additives are carefully calibrated to ensure optimal performance and longevity of the bricks.
Manufacturing Process:
The manufacturing process of Plaex-crete bricks involves a series of steps, from material preparation to final product assembly. Once the recycled plastic materials have been processed and prepared, they are mixed with the additional components in a controlled environment to achieve the desired consistency and properties. This mixture is then fed into a molding machine, where it is shaped into individual brick units.
The molding process may vary depending on the specific design and dimensions of the bricks. Some bricks may be molded using traditional injection molding techniques, while others may utilize compression molding or other specialized methods. The molds used in the process are carefully designed to ensure precision and uniformity in the final product.
After molding, the bricks undergo a curing or setting process to solidify their structure and enhance strength. This may involve exposure to heat, pressure, or chemical treatments to promote bonding and cohesion within the material. Once cured, the bricks are inspected for quality control purposes, ensuring compliance with specifications and standards.
The final Plaex-crete bricks are ready for packaging and distribution to construction sites or retail outlets. Their lightweight and interlocking design make them easy to transport and assemble, offering a sustainable alternative to traditional construction materials. Overall, the composition and manufacturing process of Plaex-crete bricks exemplify the innovative utilization of recycled plastic waste to create durable, eco-friendly building solutions.

Plaex-crete Advantages:
Plaex-crete bricks position them as a sustainable and innovative solution for modern construction challenges. From their durability and lightweight nature to their eco-friendliness and ease of assembly, these bricks offer a promising alternative to traditional building materials, paving the way for a greener and more resilient built environment.
1. Durability: Despite being constructed primarily from recycled plastic, the bricks exhibit exceptional durability, surpassing traditional concrete in many aspects. They are resistant to common issues such as water absorption, decomposition, splitting, and cracking, ensuring long-term structural integrity even in harsh environmental conditions.
2. Lightweight: Significantly lighter than traditional bricks of comparable size, making them easier to handle and transport. This characteristic reduces labour requirements during construction and facilitates rapid assembly, contributing to overall project efficiency.
3. Eco-Friendly: By utilising recycled plastic waste as the primary raw material, these bricks help mitigate the environmental impact of plastic pollution while reducing reliance on conventional construction materials. Additionally, the bricks are fully recyclable, contributing to a circular economy model.
4. Interlocking Design: Features a unique interlocking design that simplifies the construction process. Without the need for mortar or cutting, the bricks can be seamlessly assembled, facilitating faster and more cost-effective building projects. The interlocking mechanism also ensures tight joints, creating structures that are both watertight and airtight.
5. Versatility: Their lightweight nature and interlocking system make them suitable for various residential, commercial, and industrial projects. Whether used for storage, walls, landscaping, or other applications.
6. Reduced Carbon Footprint: Contribute to reducing carbon emissions associated with conventional construction materials. The manufacturing process of these bricks also requires less energy compared to traditional concrete production, further lowering their carbon footprint.
7. Tested Strength: Undergoes rigorous testing to ensure their strength and durability. Tests, such as the bulldozer test demonstrate the bricks’ ability to withstand significant impact and pressure without deformation or collapse.
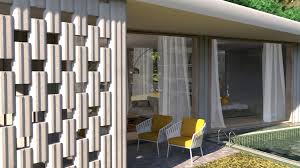
Applications and Future Prospects:
Plaex-crete bricks offer a versatile solution for various construction applications, ranging from landscape walls to wall construction and circular angling. Their lightweight nature, coupled with the interlocking system, makes them ideal for rapid and cost-effective construction, with the potential to revolutionize both residential and commercial building projects. The company envisions a future where automation further streamlines the construction process, with fleets of robots assembling and modifying buildings efficiently. By diverting significant quantities of plastic and aggregate waste from landfills,s.
Challenges and Regulatory Considerations:
While the potential of Plaex-crete bricks is immense, certain challenges and regulatory considerations must be addressed for widespread adoption. Currently, the bricks are not approved for house construction, with the company actively seeking permits to expand their usage. Regulatory compliance, including adherence to building codes and standards, is crucial to ensuring the safety and reliability of structures built using Plaex-crete. Additionally, continued research and development are necessary to enhance the bricks’ performance, address any durability concerns, and optimize the manufacturing process for scalability and efficiency.
Conclusion:
The development of bulldozer-resistant Lego bricks from recycled plastic waste represents a paradigm shift in construction methodology, combining sustainability, durability, and ease of use. PLAEX Building Systems Inc.’s innovative approach not only tackles the pressing issue of plastic waste but also offers a viable alternative to traditional construction materials. As the industry embraces eco-friendly solutions, Plaex-crete stands at the forefront of a sustainable construction revolution, paving the way for a greener, more resilient built environment.
References- interestingengineering.com,yahoo.com