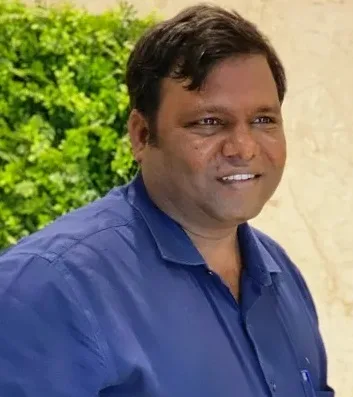
The demand for precast technology in construction has been steadily increasing due to its advantages, such as rapid construction, cost-effectiveness, and durability. It is widely utilized in various applications, including resilience, commercial buildings, bridges, tunnels, and highways. However, large-scale precast projects come with significant challenges related to resource planning.
Ensuring a consistent supply of high-quality raw materials is the first important step. Any disruption in the supply chain can bring production to a standstill. Next, managing a skilled workforce proficient in precast techniques can be a challenge, especially when scaling up for large projects. To meet tight schedules, meticulous logistics planning is essential, encompassing the coordination of fabrication, transportation, and installation of massive precast elements. Often, limited space on construction sites requires efficient on-site storage solutions. To ensure top-notch results, maintaining rigorous quality control standards throughout the process is vital. To overcome these challenges, comprehensive resource planning and close collaboration among all stakeholders are key for the successful execution of large-scale precast projects.
For company owners, real estate developers, and engineers, understanding the nuances of this precast construction is important. This article delves into the core aspects of precast construction, highlighting its significance and the challenges that must be overcome for its successful implementation.
The article analyses different aspects that includes;
- Adopting Precast Technology for Large Scale Project
- Concepts and importance of design of project
- Leadership of Project
- Designing of Project Execution
- Finishing of building and Testing of external joints
- Constraints for Precast Technology for Large Scale Projects
1. Adopting Precast Technology for Large Scale Project
Precast technology has a rich history in our country, with its inception dating back to 1910 in ports, followed by its application in high-rise buildings in 1969 and warehouses in 1994, among other instances.
When considering the adoption and compatibility of precast technology for any construction project, it’s essential to acknowledge its suitability for high-rise buildings. Precast structures offer excellent diaphragm strength and stability compared to conventional cast-in-situ (CIS) construction methods.
There are primarily three types of precast construction systems used:
1. Framed Structures (Columns, Beams, and Slabs): A framed structure is a traditional construction method that involves a combination of vertical columns, horizontal beams, and flat slabs. Columns are the vertical load-bearing elements that support the weight of the building and transfer it to the foundation. Beams are horizontal members that connect columns, providing stability and distributing loads evenly. Slabs are the flat, horizontal surfaces used for floors and ceilings within the building. Framed structures are widely used in various construction projects and offer flexibility in design and construction.
2. Large Panel Prefabricated Structures: Large panel prefabricated structures are a modern construction approach that utilises pre-made, sizeable panels or modules manufactured in a controlled factory environment. These panels often include pre-constructed walls, floors, and sometimes roofs. The prefabricated panels are then transported to the construction site and assembled, significantly reducing construction time and costs.
3. Volumetric Precast Structures: Volumetric precast structures take prefabrication to a more advanced level by creating entire three-dimensional modules off-site. These volumetric units can include complete rooms or sections of a building and are produced in a factory with precise quality control. Once manufactured, these units are transported to the construction site and assembled to create the entire structure.
Applications and savings of precast construction systems:
Framed Structure (Columns, Beams, and Slabs): This type of structure is ideal for applications such as car parking facilities, commercial towers, stadiums, and regular structures where developers prefer the efficiency of CIS construction. Choosing a precast in such cases can result in significant time savings of approximately 20-25% for the project.
Large Panel Prefabricated Structures and Volumetric Precast Structures: These versatile structures are suitable for various building types, including public and residential buildings. By opting for these precast systems, construction projects can potentially achieve cost savings ranging from 25% to 40% or even more, depending on available resources.
2 Concepts and importance of design of project
The design of a project plays a major role in determining its success. Project failures can often be attributed to various factors. For instance, in our country, there are experts in Precast design, but they face challenges in adapting building designs to align with evolving Indian standards and technological advancements.
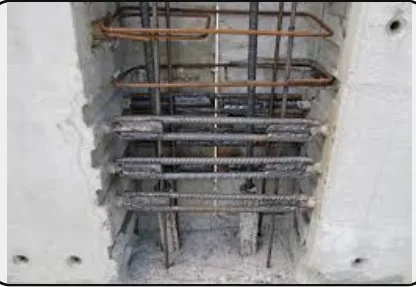

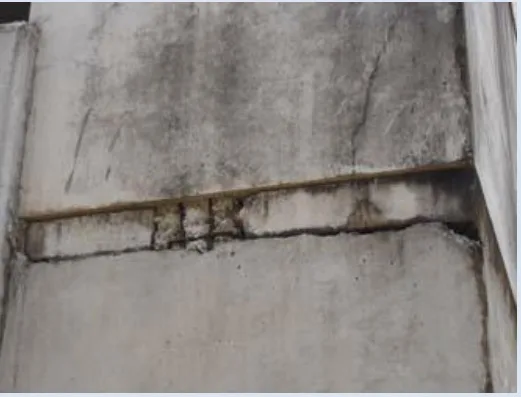
Importance of 3D Modelling of building
The significance of 3D modelling for buildings cannot be overstated. In the current industry landscape, major projects encounter difficulties in analysing designs, primarily due to many teams lacking familiarity with Precast design concepts. An instance of this issue is when a prominent real estate player had to abandon the precast concept because the developer’s structural team could not reach a consensus on the optimal design.
3D modelling serves as an invaluable planning tool for onsite execution teams, enabling them to gain insight into the design in advance, plan the execution, and address concerns or request modifications. Unfortunately, this tool often goes unused, resulting in challenges on major projects.
Design of Joints


Furthermore, the design of joints holds great importance. Well-designed joints can expedite the project schedule and improve waterproofing, thereby ensuring profitability.
3.Leadership of Project
Leadership in a project is typically divided into two key roles: the Investor and the Technical Lead. The Investor, who drives the project, must place a strong emphasis on system and process implementation. They should be unwavering in their commitment to approved processes and be proactive in understanding the technology involved. Investors also play a crucial role in determining the specifications of the precast production facility and ensuring that the equipment requirements align with the project’s scope of work.
Finding a qualified Technical Lead for Large Scale Precast Projects can be challenging, but there are talented individuals capable of delivering world-class projects. The Technical Lead’s responsibilities encompass negotiating structural designs with designers, designing the production facility, establishing an effective procurement and contracts team, planning the production process, and organising logistics and erection processes. They are also accountable for achieving project goals related to safety, quality, and project execution speed.
4. Designing of Project Execution
Execution of Plumbing in project
When it comes to construction, plumbing processes have remained largely traditional. Here are some proposed improvements for the industry:
- Consider a frame system that can be fabricated on the ground and installed as needed.
- Pressure test the fabricated plumbing frame to ensure its integrity.
- Explore options for casting plumbing in a factory during element casting or after wall erection.
- Keep in mind that casting plumbing is typically feasible on tables and not recommended in battery molds.
- Pay attention to the positioning of vertical stacks, especially in balconies, in case waterproofing is done before pipe installation.
Addressing Erection Tolerances:
One of the significant challenges during erection is achieving the right screed level, considering that produced elements have their own tolerances. Here’s how to handle it:
Case 1: If the screed is casted higher than required (more than +8 mm), carefully adjust the wall dimension and floor level by grinding and removing the excess concrete.
Case 2: In the rare case of the screed being casted lower than required (between -5 mm to -8 mm), roughen the surface and use non-shrink grout to bring it to the correct level before proceeding with erection. This avoids the need for placing elements on shims, which can be unsafe.
Factors impacting the size of Element for the project
Several factors impact the size of structural elements for a project, including:
- Logistical feasibility: Ensure that the size of panels is suitable for transport and handling.
- Available logistical resources: Consider the use of low bed trailers, flat beds, A-frames, H-frames, etc.
- Architectural feasibility: Ensure that the design aligns with the project’s architectural requirements.
- Balance of structural and non-structural elements: Determine a feasible ratio that justifies crane costs, especially for heavy precast elements.
- Crane type and system: Select the appropriate crane type and system, considering the project’s needs.
- Crane bracket for high-rise projects: Ensure safe connections for cranes used in tall buildings.
- Element pick-up points: The placement of pick-up points during erection impacts the overall design.
- Wind flow analysis: Account for the impact of wind on the design.
Advanced Logistical Planning:
For efficient logistical planning, especially in densely populated areas, consider the following:
- Project location: Give special consideration to dense urban areas.
- Cassette stacking system: Implement systems that allow multiple elements to be lifted and moved together.
- Use tractors in addition to trailers for improved transportation in congested areas.
Importance of Neoprene Rubber in Erection:
Neoprene rubber plays a crucial role during erection. It helps resist shocks, closes gaps between elements, and prevents water leakages. Unfortunately, over time, neoprene rubber has been omitted from the system, contributing to cracks in the finishing process and water leakage issues.
5. Finishing of building and Testing of external joints
When it comes to finishing and testing building joints, it’s crucial to consider various factors:
- Joint Design: Joints should be designed with a focus on feasibility, practicality, serviceability, fire rating, and appearance. Temporary structures for joint preparation are vital and should be well-designed and placed.
- Welding Cleats and Reinforcement: Be cautious when welding cleats or projecting reinforcement. Ensure that personnel receive training or knowledge-sharing sessions before working on overlapping reinforcement, links, or prestressing.
- Shuttering System: Select an appropriate system of shuttering that is feasible, easy to execute, and stable.
- Grouting: Develop a proper system for grouting and provide training to all personnel involved. Carefully select the grout material, mix it correctly, and place it accurately.
- Curing: Pay attention to curing, even for joints, as it is essential for the sustainability of structures. Overlooked joints can lead to long-term issues.
- Shuttering Material Removal: Take special care when removing shuttering material and temporary structures to avoid any damage to joints and ensure safety.
Testing of Joints and Floors:
Different types of testing are required for adherence to quality construction.
Water tightness test for joints:
- Method Statement: Ensure the concrete surfaces are dry and free from rain. For vertical joints, select test locations at least 1 meter apart, starting from the bottom. Test the intersection of vertical and horizontal joints.
- Water Jet Test: Use a water jet with a flow of 600 liters per hour at a velocity of 0.6m/sec. Hold the nozzle 1.2 meters from the concrete face, with a 60-degree angle cone of water, and maintain the jet for 2 hours.
- Examination: Check the back surface for any signs of leakage or dampness. Note the location if dampness is observed and take photographs.
- Acceptance Criteria: There should be no signs of leakage or dampness on the back surface of concrete.
Perform load tests for slabs and balconies according to project specifications.
Building Finishing:
When it comes to structural finishing, it’s essential to avoid common mistakes. Notably, avoid doing all floors together, as it can lead to unsafe conditions and poor workmanship.
- Grinding: Proper tools and trained manpower are important for the finishing process. Focus on specific areas like dowel tubes, grout couplers, and joint corners between walls, walls to slabs, and doors.
- Rebar Removal: Ensure that rebar used for supports is correctly removed. Avoid the common practice of using gas cutting, as it leads to rusting and water leakages. Instead, chip the area near the bar for at least 20 mm from the surface, create a recess, and then cut using an appropriate tool. Fill the recess with approved high-strength material.
- Honeycomb Treatment: Carefully address exposed honeycomb in joints with the guidance of quality experts on the project.
- Grout Cleanup: Be cautious when removing spill-over grout on the external or internal parts of the building. It’s preferable to remove it immediately to prevent visible stains behind the paint.
6. Constraints for Precast Technology for Large Projects
It’s important to address various constraints and challenges in the precast construction industry for large projects. Here’s a revised and more structured version of the provided information:
Constraints for Precast Technology in Large Projects:
1. Resource Planning:
- Precise resource planning is essential for large-scale projects.
- Ensure the project’s vision and goals align with resource allocation.
- Scrapping a facility due to misaligned sales expectations or high staffing costs can be avoided with careful planning.
2. Vendor Development:
- Support small businesses, but not at the expense of project requirements.
- Balance cost savings with technical quality.
- Prioritize the use of precast technology to save costs.
3. Research and Development:
- Emphasize the need for ongoing research and development.
- Stay updated with evolving technology to remain competitive.
4. Supporting Production Facilities:
- Consider investing in small joinery factories and production of accessories (doors, windows, kerb stones) to meet project demands.
5. Contract Management:
- Address issues related to contract management.
- Ensure contracts are well-structured to prevent project failures.
Challenges for Precast Industry in Today’s Real Estate Industry
1. Limited Scope in Design:
- Precast technology is often associated with affordable housing or government projects.
- Architects may have restrictions on design freedom, hindering the adoption of precast methods.
2. Knowledge and Awareness:
- Shortage of knowledgeable structural designers in the country.
- Limited awareness of the versatility of precast technology for architectural features and aesthetics.
3. Special Monumental Structures:
- Hesitance to accept precast contracts for special or monumental structures.
Taking the Precast Industry to the Next Level in India:
1. Statutory Body:
- Establish a statutory body to aid developers and architects in understanding precast technology.
- Offer services like project feasibility analysis, structural design support, and project management consultancy.
2. Hybrid Structures:
- Promote the use of hybrid structures, starting with non-load bearing walls.
- Encourage the integration of precast elements into various construction projects.
Conclusion
The article covers vital aspects of implementing large-scale precast projects, emphasizing the importance of proper design, leadership, and execution planning. It underscores the need for choosing the right precast construction system for various project types and highlights the significance of robust resource planning, vendor development, and research and development. Additionally, it addresses the constraints and challenges faced by the precast industry in the context of India’s real estate sector. To elevate the precast industry to the next level, there is a call for a statutory body to guide developers and architects, promote hybrid structures, and encourage the utilization of precast technology.
About the Author
Mir Mohammed Ali Khan, the Senior Vice-President of Suraksha Smart City, is a third-generation civil engineer hailing from Hyderabad. He holds PMP certification and boasts extensive expertise in precast technology. With a rich career spanning two decades, he has collaborated with prominent construction companies in both the Middle East and India. His profound knowledge encompasses precast factory setup, equipment selection, project-specific design conceptualization, and the adept management of large-scale projects. Currently, he is associated with Conceptual Advisory Services, where he is actively involved in the development of one of the largest projects in the MMR region.