What is Carbonation in Concrete?
Carbonation in concrete refers to the process where carbon dioxide (CO2) from the air reacts with calcium hydroxide in the concrete to form calcium carbonate. This reaction gradually reduces the pH of the concrete, which can lead to corrosion of embedded steel reinforcement over time, potentially compromising the structural integrity of the concrete. It’s an important consideration in the design and maintenance of concrete buildings and structures, particularly in urban areas or near industrial sites.
Where does it occur?
- Buildings
- Bridges
- Highways and roads
- Tunnels and Dams
- Marine structures
- Parking structures
- Industrial facilities
- Water treatment facilities etc.
Why does it occur?
- Exposure to carbon dioxide (CO2) in the atmosphere
- Permeability allowing CO2 penetration
- Moisture aiding carbonation
- Insufficient concrete cover over reinforcement bars
- Reduction of alkalinity in concrete
- Presence of cracks or voids facilitating CO2 access
- Environmental factors like temperature and humidity
- Concrete mix design and composition
- Quality of curing and protection during construction
- Exposure to aggressive environments
- Presence of reinforcing steel
- Structural damage or deterioration
- Longterm exposure to high CO2 levels
- Presence of contaminants in the atmosphere (e.g., sulfur dioxide)
- Airflow patterns affecting CO2 distribution around the concrete structure
Types of Carbonation in Concrete
1. Surface Carbonation: Surface carbonation initiates at the outermost layer of concrete, where carbon dioxide from the atmosphere reacts with calcium hydroxide in the presence of moisture, forming calcium carbonate. This process typically occurs within the first few millimetres of the concrete surface. While surface carbonation can create a protective layer that reduces the porosity of concrete, enhancing its resistance to certain forms of deterioration, it also poses risks. If the carbonated layer is not wellbonded to the underlying concrete, it may lead to reduced adhesion and cohesion, making the surface vulnerable to cracking, spalling, and weathering over time.
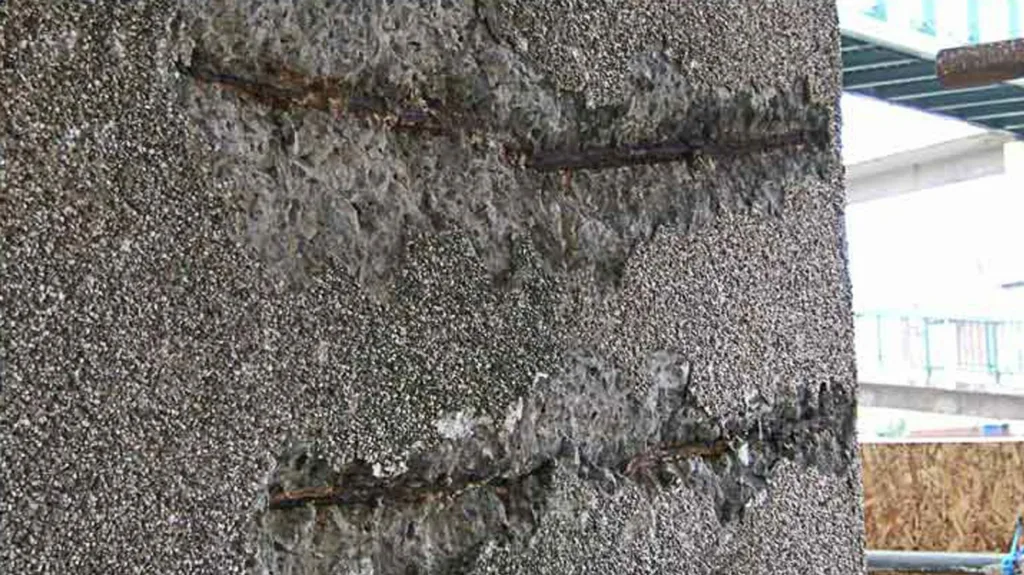
2. Depth Carbonation: Depth carbonation involves the gradual penetration of carbon dioxide into the concrete matrix, leading to a decrease in pH and alkalinity throughout the depth of the concrete. This process occurs over an extended period, affecting the inner layers of the concrete beyond the surface. As carbonation progresses deeper into the concrete, it can compromise the integrity of the cement paste matrix, leading to a reduction in strength and durability. Depth carbonation also increases the risk of corrosion of embedded reinforcement steel by disrupting the passivation layer and facilitating the ingress of chlorides and other corrosive agents.
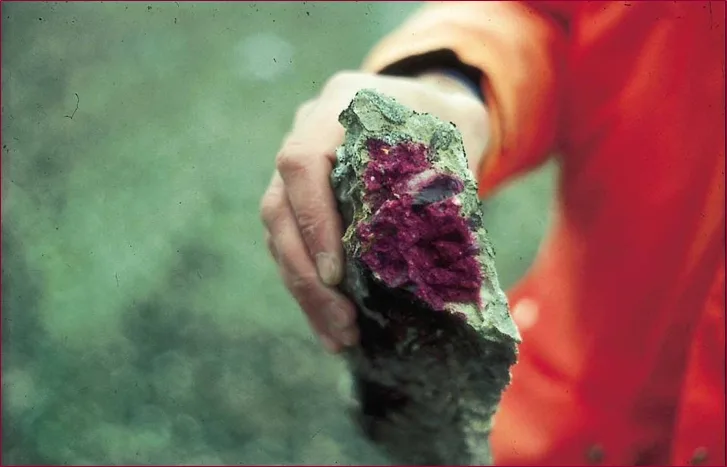
3. Pore Solution Carbonation: Pore solution carbonation occurs when carbon dioxide dissolves in the pore solution present within the concrete. This dissolved carbon dioxide reacts with calcium hydroxide and calcium silicate hydrate phases, leading to the formation of calcium carbonate and a decrease in pH. Pore solution carbonation accelerates the deterioration of concrete by weakening the cement paste matrix, reducing its ability to resist chemical attack and mechanical stress. It also promotes the corrosion of embedded reinforcement steel and compromises the longterm durability and service life of the concrete structure.
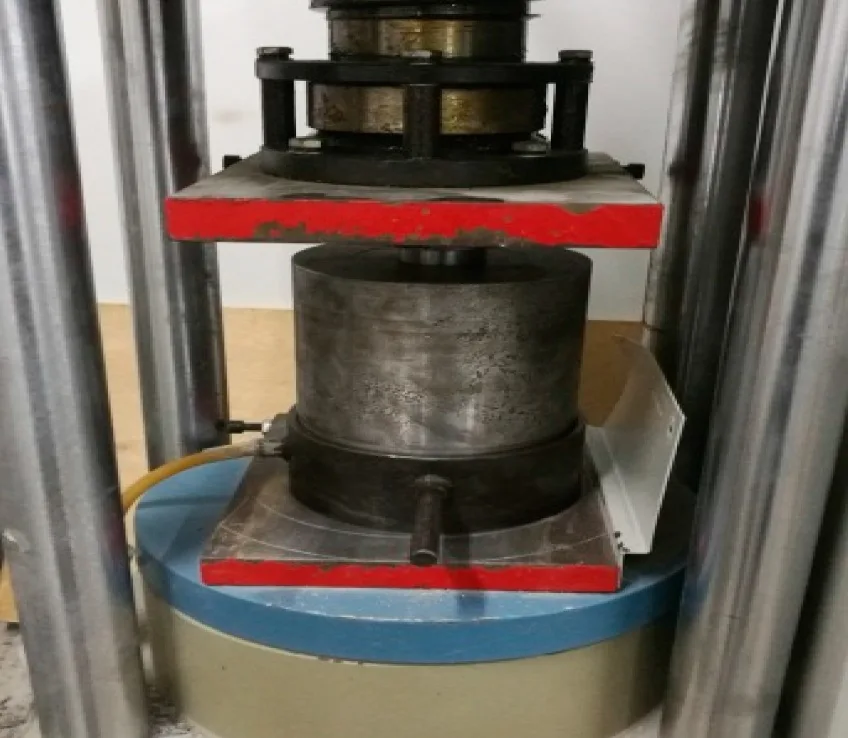
How to avoid Carbonation in Concrete?
Here are few measures that can be used to prevent carbonation in concrete
- Use low carbon cement mixes
- Seal the surface with protective coating
- Ensure proper curing
- Avoid exposure to carbon dioxide sources
- Maintain pH levels
- Incorporate supplementary cementitious materials (SCMs) like fly ash or slag
- Implement cathodic protection systems for reinforced concrete
- Use corrosionresistant reinforcement materials
- Provide adequate ventilation to prevent moisture buildup
- Control humidity levels in indoor environments near concrete surfaces
- Apply anticarbonation paints or coatings specifically designed for concrete surfaces
- Install physical barriers to shield concrete from carbon dioxide exposure
- Use dense mixes with low permeability
Mitigating Carbonation in Concrete with various repair methods
Discussed below are different methods to repair concrete buildings and structures once carbonation has occurred.
1. Surface Coatings: Application of anticarbonation coatings or paints designed to protect the concrete surface and prevent further carbon dioxide ingress.
2. Electrochemical Repair: Cathodic protection systems can be installed to mitigate carbonation induced corrosion of reinforcement bars by applying a low voltage electrical current.
3. Alkali Treatment: Applying alkali solutions to neutralize carbonation and restore the concrete’s alkalinity, thereby halting further carbonation.
4. Concrete Overlay: Adding a new layer of concrete over the affected area to cover the carbonated layer and restore structural integrity.
5. Patch Repair: Removal of carbonated concrete and filling the void with repair mortars or epoxy based materials to restore strength and durability.
6. Crack Injection: Injecting epoxy resins or polyurethane grouts into cracks caused by carbonation to seal and stabilize the concrete.
7. Microbial Induced Calcium Carbonate Precipitation (MICP): Biological treatment using bacteria to induce calcium carbonate precipitation, effectively sealing cracks and reducing permeability.
8. Carbon Fiber Reinforcement: Installing carbon fiber reinforcement to strengthen and stabilize the affected concrete areas, providing additional support against further carbonation induced deterioration.
Conclusion
Carbonation in concrete poses significant challenges to its durability and longevity. Understanding the mechanisms and factors influencing carbonation is crucial for designing structures with adequate protection and maintenance strategies. Addressing carbonation requires a holistic approach, incorporating proper material selection, construction practices, and ongoing monitoring and maintenance to ensure the structural integrity and sustainability of concrete buildings and structures in the long term.
Image Credit: concrete.org, mdpi.com