The government’s infrastructure thrust has continued in Budget 2022-23,. There is a sharp increase in the allocations for highways and rural roads including the Gati Shakti Master Plan for multimodal connectivity (which will build 25,000 km of expressways) and five river-linking projects. The capital expenditure for key infrastructure sectors, especially highways, has got a big boost in Budget 2022-23. The total allocation for the highways sector has increased to Rs 1.99 lakh crore from Rs 1.18 lakh crore in FY 2021-22. The quality and fast-track developments play a key role in road construction. The selection of the right road construction equipment becomes pivotal. The road roller is one such important equipment that plays an important role in road construction. They can also be used in areas as diverse as on landfill sites or agricultural projects. The primary use for road rollers is to crush, knead or vibrate loose materials by applying direct pressure. The rolling process is used to compact loosely bound foundation materials, so they remain compacted and do not come loose. There is the availability of different types of road rollers for different construction needs. Each of the road roller models has gone through technological modification and manufactured according to Indian terrain.
Technological advancement of road roller
Articulated Tandem Roller with traction control and speed sensors
The latest models utilise an efficient hydraulic system, traction control and speed sensors. This enables smooth starts and stops that improve mat quality when working on asphalt. The roller features a heavy-duty engine, which is CEV Stage IV compliant. It is manufactured at Ammann India in Ahmedabad. The machine can compact from thin to thick asphalt layers in fewer passes with its high compaction output. A combination of drum dimensions, frequencies and amplitudes provide productivity and flexibility on a variety of job sites. The machine features a powerful, two-stage vibratory system – combined with drum dimensions and multiple amplitudes and frequency settings that provides productivity and flexibility in both soil and asphalt applications. The machine’s unique propulsion system enables smooth starts and stops that improve mat quality when working on asphalt. A powerful, two-stage vibratory system – combined with drum dimensions and multiple amplitudes and frequency settings – provides productivity and flexibility in both soil and asphalt applications. The machine applications include highways and city/municipal roads; PMGSY (urban-rural connectivity); airports; port distribution hubs; industrial developments; roads for power and steel plants; Formula 1 roadways; and smart city developments.

Pneumatic tyred rollers with hydrodynamic propulsion system
Pneumatic rollers have become more popular with stiffer mixes since they can help you achieve compaction density. These types of rollers consist of tyres that provide better static penetration into the materials. The weight of the machines and the air pressure of the tires can be adjusted to meet the specific pressure desired on a particular job.

Single drum roller with with a smart speed control system
The latest range of rollers come with a smart speed control system that not only saves but also produces less noise. The optional ECO STOP enables the engine to shut down automatically after a defined period in idle speed. This also reduces fuel consumption and wear. On these models, manual slip control provides specific adjustments to ground conditions. The rear axles are equipped with a self-locking differential. This translates into forwarding drive, even under the most severe site conditions. The cab has a spacious design with excellent all-around vision. When in use for longer periods, the ergonomic seat position provides fatigue-free driving. The steering wheel is adjustable to suit every operator. The visual lane assistant allows the driver to compact edges or lane to lane with ease. The models also come attached with a drum drive and clamp-on pad foot for compacting more cohesive materials such as clay and silt The optional drum drive system features an additional high torque drive motor mounted on the front drum frame, resulting in excellent gradeability and optimized traction.

Double drum roller with hydraulically adjustable crab steering
The latest rollers come standard with a hydraulically adjustable “crab steering” system that can offset the rear drum up to seven inches. The front drums of the small DV rollers are positioned about two inches off-centre from the back drum, allowing for a tighter turning radius, while both drums have a balanced design and a tapered edge to reduce tearing around curves and during transitions. The standard pressurised water sprinkler system with 6 nozzles per drum provides longer operating hours in every condition due to optimised water usage and consistent water flow regardless of the slope of the jobsite. The ergonomically designed sliding operator’s seat allows the driver to have a perfect view on the drum edge in every working condition.
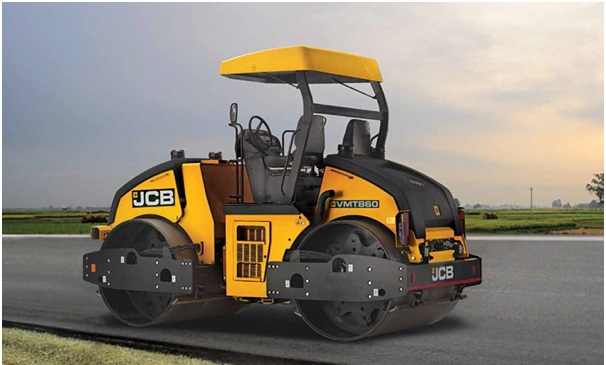
Tandem roller with articulated joint
Latest models feature articulation joints, it ensures good directional stability, high stability in curves and a high level of driving comfort As the connector between the front and rear frame, the three-point articulation ensures optimum steering characteristics, driving comfort and safety while driving on difficult terrain. Moreover, the 3-point articulation ensures uniform weight distribution over the front and rear sections, even at full steering lock. This results in very smooth asphalt surfaces, because asphalt movement and lateral deformations are prevented from the outset. Customers can order their roller with or without lane offset, and can add numerous options. This includes Temperature Meter for continuous measurement of the asphalt temperature at the roller, as well as ICS systems for comprehensive compaction inspection. The edge pressing and cutting device is also available in many different diameters and pressure angles. It is best suited for applications such as highway road shoulders, retaining the walls of flyovers, footpaths, trenches, service roads, industrial and residential columns, rural roads.

Vibratory roller with frequency amplitude adjustment
Modern machines feature two steel drums that vibrate via an internal, eccentric mechanism, which often can be adjusted to vary the frequency and amplitude of the vibratory action. The latest models come with proprietary software systems, continually report the degree of compaction and can map the job site’s compaction values for future reference. Latest models are used to compact loose soil or asphalt and are primarily used for roads and highway construction. These machines also find application for ground compaction/stabilisation at construction sites. Nowadays companies manufacture 10 tons to 12 tons soil compactors and 3.5 tons and 9 tons tandem compactors with advanced features. used to compact loose soil or asphalt and are primarily used for roads and highway construction. These machines also find application for ground compaction/stabilisation at construction sites.

Mini tandem roller with ergonomically located controls
Latest models designed to fulfil the ever-increasing demand for road compaction in the country. This entry-level road construction machine is the best compaction machine which requires zero maintenance, while serving multiple applications. Best suited for applications such as highway road shoulders, retaining the walls of flyovers, footpaths, trenches, service roads, industrial & residential columns, and rural roads. It can be used for both earth and asphalt compaction with surprising ease. • Due to superior design of drums on the curves, the compaction happens without leaving a mark. This is helpful in carrying out compaction on curved stretches. The models provide utmost comfort to the operator with its ergonomically located controls, minimising physical effort and maximising efficiency.

Conclusion
Modern road rollers come with compact design, with articulated manoeuvrability that requires lesser turning radius. Safe and ease of maintenance of these machines are enabled by higher drain out and replacement intervals of the drum oil, engine oil and filters. Choosing the right type of roller for your construction project is important, as the wrong one can result in poor workmanship, pockets of air that’ll sink the structure or uneven spaces that can be dangerous. You’re also going to have to figure out the type of soil that’s going to be compacted.
Image Source: ammann.com, casece.com, wirtgen-group.com, bomag.com, jcb.com, escortsgroup.com, larsentoubro.com, catmachine.co.in