Concrete roads are made using a concrete mix of portland cement, coarse aggregate, sand, and water. The most important advantage of a Concrete Road is its service life due to exceptional durability. They are considerably less prone to wear and tear defects like rutting, cracking, stripping loss of texture, and potholes that can occur with flexible pavement surfaces. This low maintenance requirement is one of the principal advantages of concrete pavements. There are well-designed concrete pavements that have required little or no maintenance. Less maintenance also means fewer traffic delays, a huge advantage on some of our already congested highways.
Requirements for concrete road pavements
An ideal pavement should meet the following requirements:
- Right thickness to distribute the wheel load stresses to a safe value on the sub-grade soil
- Durable to withstand all types of stresses imposed upon it
- Adequate coefficient of friction to prevent skidding of vehicles,
- Smooth surface to provide comfort to road users
- Impervious surface, so that sub-grade soil is well protected
- Long design life with low maintenance cost
- The thickness should be adequate to transmit the applied loads and distribute them onto a larger area of the soil below
- Hard-wearing surface so as to resist the abrasion caused by vehicle tyres
Types of concrete roads pavements
Jointed Plain Concrete Pavement (JPCP) – Jointed plain concrete pavement uses contraction joints to control cracking and does not use any reinforcing steel. Transverse joint spacing is selected such that temperature and moisture stresses do not produce intermediate cracking between joints.
Jointed Reinforced Concrete Pavement (JRCP) – Jointed reinforced concrete pavements (JRCP) contain steel mesh reinforcement (sometimes called distributed steel). In JRCP, designers intentionally increase the joint spacing and include reinforcing steel to hold together mid-panel cracks.
Continuously Reinforced Concrete Pavement (CRCP) – Continuously reinforced concrete pavement (CRCP) contains continuous, longitudinal steel reinforcement without transverse joints, except where required for end-of-day header joints, at bridge approaches, and at transitions to other pavement structures. Continuous reinforcement is a strategy for managing the transverse cracking that occurs in all new concrete pavements. In new concrete pavements, volumetric changes caused by cement hydration, thermal effects, and external drying are restrained by the pavement base layer and longitudinal reinforcement causing tensile stresses to develop in the concrete.

Methods of construction of concrete road
The concrete roads can either be constructed in a single course or two courses. In single course pavement, or two courses. In single course pavement, the entire depth of concrete is composed of homogeneous material. The concrete is laid in two courses or layers of equal or different depths with different concrete compositions with three different types of methods.
Alternate Bay Method: taken up in alternate bays; the bays left in the first instance are done after the concrete already laid gets hardened adequately-one week in the case of ordinary Portland cement and two to three days for rapid hardening cement.
Continuous Method: the bays of one lane are laid continuously; however, construction joints are provided at the end of the day’s work.
Expansion joint and strip method: the road is divided into longitudinal strips and transverse bays using timber formwork. The joints are then suitably filled up with fillers like asphalt and finished so as to provide for the expansion of the concrete slab.

Structural components of concrete roads
The concrete roads consist of the following components :
Surface Course
It is the topmost layer; its function is to provide a smooth, strong, abrasion-resistant and reasonably impervious course. Since it is directly in contact with the vehicle tyres, it has to resist the imposed wheel loads and transmit them safely to the layer below. The material may be granular, bituminous or cement concrete depending upon the nature of the construction. For flexible pavements, the bituminous surface is the wearing course whereas in rigid pavement the concrete surface act as the base course cum wearing course.
Base course
It is below the surface course and its function is to distribute the stresses transmitted through the surface course evenly onto the layers below. Invariably, it consists of granular or bituminous material, and acts as a structural part of the pavement. The base course is the most important layer of a road structure which transfers the stresses developed due to traffic impacts through the wearing course. The base course layer provides the required foundation stiffness and structural strength.
Sub-Base Course
It is just below the base course and provides additional help to the courses above it in distributing the loads. It also helps in preventing soil grains of the subgrade from intruding into the base course above, and counteracts frost action, if any. It may consist of stabilised soil or soil aggregate mixes, which facilitate drainage of free water from the pavement. It comes between the base course and subgrade. The material used for this layer shall satisfy the specifications in terms of gradation, strength, and plastic characteristics. This layer is necessary if the subgrade is of poor quality.
Subgrade
It is the compacted natural soil immediately below the pavement layers; this acts as a foundation for the highway. The top surface of the subgrade is called the formation level. Based on the alignment and the nature of the terrain, a roadway may be constructed over an embankment or a cutting, or at or nearly at the natural ground level. The formation of level, therefore, has to be properly decided to suit these conditions. It serves as the foundation and acts as a uniform support to pavements. Subgrades bear the entire load of the payments along with the service load of traffic
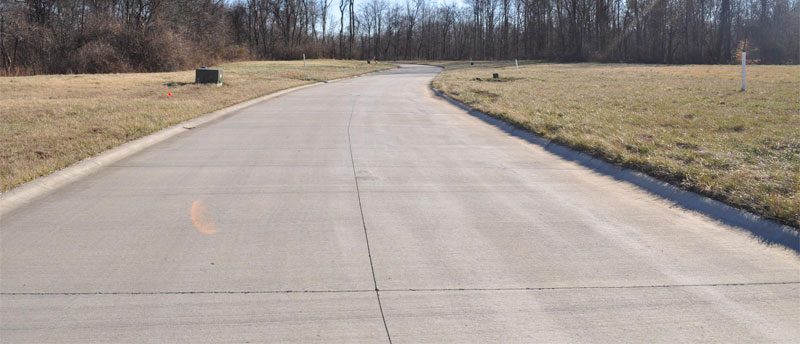
The construction of concrete road involves the following steps;
- Preparation of Subgrade- shaped, and leveled. After cleaning, it is prepared to the required grade and profile.
- Placing the forms- Forms are properly braced and fixed to the ground using stakes. The forms are oiled before placing concrete in them.
- Watering the Prepared Subgrade- forms are fixed, the prepared surface to receive concrete is made moist. It must be sprinkled with as much quantity of water as it can absorb.
- Batching of Materials- the proportions of ingredients for the concrete mix, the fine and coarse aggregates are properly proportioned
- Transporting and laying the concrete mix- the concrete is transported to the site. The mixed concrete is deposited rapidly on the sub-grade in a layer of thickness.
- Compaction- done with a heavy screed or tamper fitted with suitable handles. Concrete is also compacted using a power-driven finishing machine, vibrating hand screed and slabs screed vibrator.
- Floating- done to provide an even surface free from corrugations.
- Belting- done just before the concrete becomes hard
- Brooming – drawing brushes at right angles to the centerline of the road from edge to edge
- Edging- the edges of the slab are carefully finished with an edging tool before the concrete is finally set.
- Joint filling- properly with a suitable sealing compound
- Curing- checking the loss of water from the concrete slab, and keeping the fresh concrete slab moist during a hardening period
- Opening of traffic- opening after attaining required strength
Conclusion
Concrete is capable of withstanding heavy loads, such as heavy vehicles, with less deformation. It serves for years without major repairs. Several factors affect concrete pavement performance, such as traffic, soil, environmental, economic and stress distribution factors. Go for an experienced pavement engineer to meticulously manage the operation efficiency desired from highway pavement.