Today’s construction projects just need materials that can handle extreme conditions, carry massive loads, and last for generations. Raw metals by themselves usually can’t meet these requirements.
Heat treatment turns regular construction materials into exceptional building components. Every major structure from skyscrapers to bridges relies on metal heat treatment to ensure they stay strong and durable. Construction companies are turning to professional heat treatment services to improve their material properties, especially when you have steel applications.
Let me show you seven innovative techniques that are reshaping how builders work with metal. These methods are a great way to get superior strength, durability, and performance from construction materials.
Annealing for Improved Workability and Strength
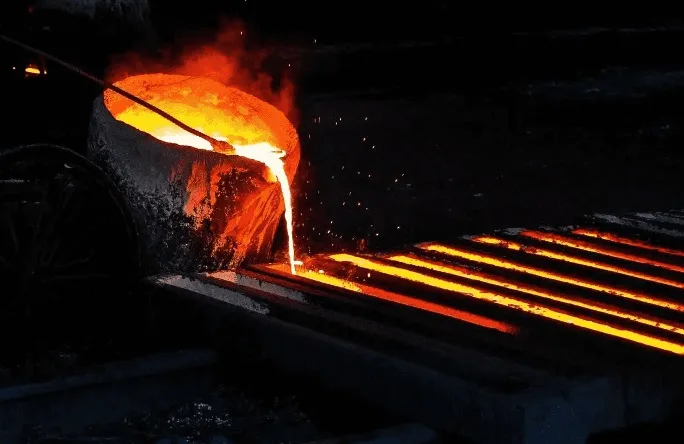
Image Source: Industrial Metal Service
Annealing is a foundational metal heat treatment process that changes construction materials’ physical and chemical properties. This advanced technique heats materials above their recrystallization temperature. The cooling rate is controlled to achieve specific mechanical properties.
The process happens in three distinct stages:
- Recovery – Removes internal stresses and linear defects
- Recrystallization – Forms new strain-free grains
- Grain Growth – Develops refined microstructure
Construction applications benefit from annealing in several vital ways:
- Enhanced Workability: Metal ductility increases, which makes it more pliable during complex forming operations
- Stress Relief: The process eliminates internal stresses from welding, grinding, or machining
- Improved Machinability: Tools last longer and create better surface finishes in the softened state
- Uniform Structure: Better mechanical properties come from grain refinement
Steel construction requires annealing temperatures between 260°C and 760°C, based on specific alloy needs. Careful cooling control is essential, especially with hardenable steels, to avoid unwanted microstructures.
Construction metals each respond differently to annealing:
Carbon Steel: This material is accessible to more people in structural applications. Full annealing helps achieve maximum softness and refined grain structure. Complex fabrication processes in modern construction work better because of this.
Aluminum Alloys: Construction-grade aluminum series (2xxx, 3xxx, 5xxx, 6xxx, 7xxx) become more ductile and formable through annealing. Architectural components and lightweight structural elements benefit from this process.
Stainless Steel: The material’s corrosion resistance improves while its ductility returns after work hardening. This makes it ideal for exposed structural elements in harsh environments.
Normalizing for Uniform Grain Structure
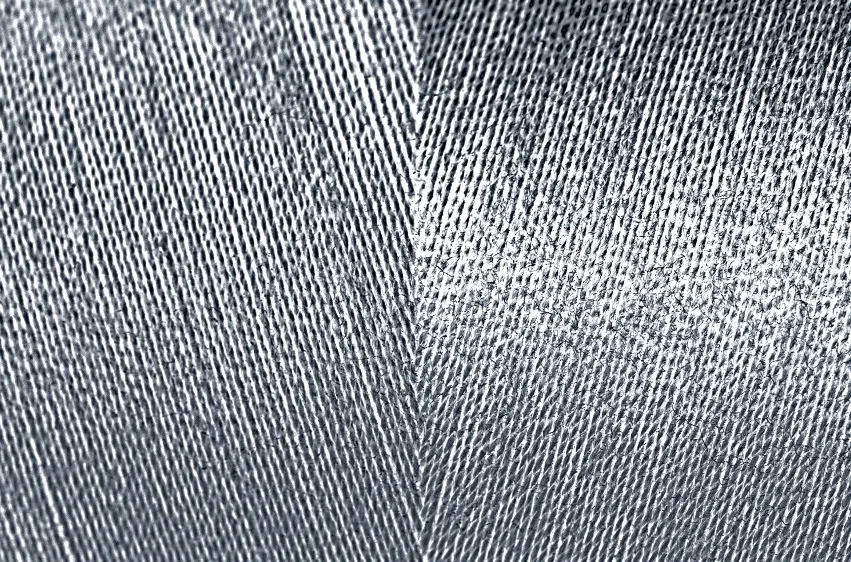
Image Source: Freepik.com
Normalizing is a precise heat treatment technique that creates uniform grain structures in construction metals, especially in steel components. This process refines microstructures and boosts mechanical properties through controlled heating and cooling cycles.
Metal needs heating to about 30-50°C above its upper critical temperature (Ac3 or Acm). This temperature control will give a complete transformation of the material’s microstructure. Air cooling then creates a refined, uniform grain pattern that boosts the metal’s performance.
Construction applications benefit in several ways:
- Improved structural uniformity with consistent grain size
- Better mechanical stability
- Better response to subsequent processing
- Reduced internal stresses from manufacturing
- Superior strength-to-weight ratio
Normalized structures show finer and more uniform pearlitic characteristics than untreated metal. These refined properties work better for construction components that face varying loads and environmental conditions.
Carbon steel applications typically need heating to 55°C above the critical point. This exact temperature ensures complete austenite transformation and creates a more refined, uniform pearlitic structure. Cooling rates strongly influence the amount of pearlite formed and the spacing of pearlite lamellae.
Grain refinement helps foundry operations by breaking up large columnar grain structures. Construction materials need this transformation because smaller, uniform grains improve structural integrity. The Hall-Petch relationship shows that material hardness increases as grain size decreases.
Induction Heat Treating for Precision and Efficiency
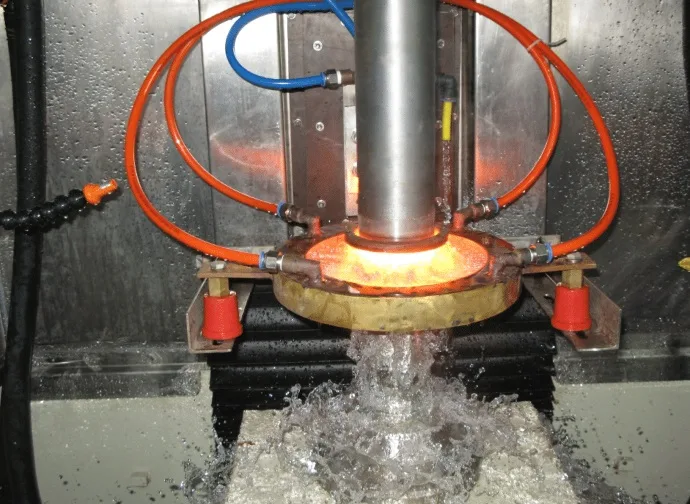
Image Source: Electroheat Induction
Induction heat treating has revolutionized metal heat treatment technology. It uses electromagnetic fields to create precise, controlled heating in specific areas of metal components. The process uses induction coils that heat conductive materials to temperatures above 2000°F in under a second.
This method stands out because it turns 90% of used energy into useful heat. Traditional batch furnaces only achieve 45% efficiency. These improvements make it valuable in modern construction.
The most important advantages in construction include:
- Precise temperature control for consistent results
- Reduced part distortion and warpage
- Minimal surface oxidation
- Lower environmental impact
- Boosted production efficiency
Modern equipment comes with advanced monitoring systems that give immediate feedback. This helps control the heating process precisely. The result is consistent, high-quality parts that meet strict construction industry standards.
The environmental benefits go beyond saving energy. The process needs no traditional fossil fuels, which means clean, pollution-free operation. This lines up with current environmental regulations and eco-friendly construction practices.
Case Hardening for Surface Durability
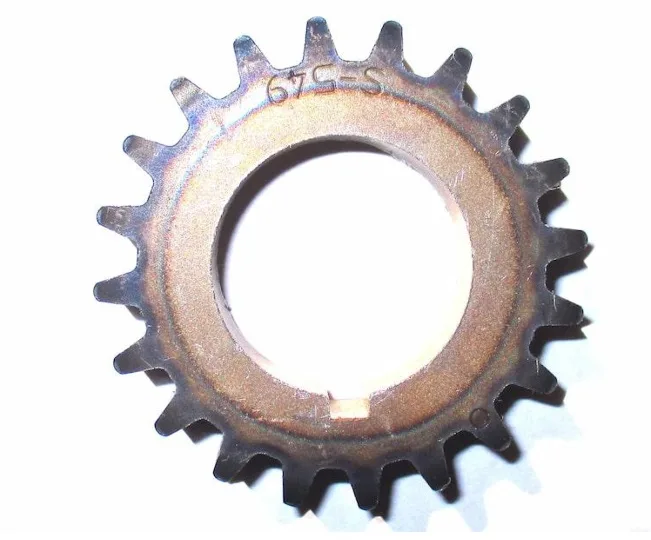
Image Source: Fractory
Construction companies just need durable components, which makes case hardening a vital metal heat treatment technique. This specialized process creates components with unique properties. A hardened exterior surface protects a softer, more flexible core.
Case hardening in construction involves heating metal components and enriching their surface with carbon or nitrogen. This thermo-chemical process creates a wear-resistant outer layer that keeps the core’s beneficial properties. Components subjected to constant friction and impact, like gears and load-bearing elements, benefit most from this technique.
Case hardening offers several advantages in construction:
- Boosted surface durability with wear resistance up to 60 HRC
- Improved fatigue strength and crack resistance
- Superior shock absorption capability
- Minimal dimensional changes during treatment
- Extended component lifespan
Professional metal heat treatment services use various case hardening methods based on specific construction needs. Steel components can achieve case depths of 4-5 mm with carbon case hardening. This precision will give optimal performance in demanding construction environments.
Components facing challenging operational conditions gain substantial benefits. Case-hardened parts work better in applications with constant exposure to abrasive materials or shock loads. Structural connections, heavy machinery components, and high-stress architectural elements perform exceptionally well after this treatment.
Budget-friendly manufacturing becomes possible as companies can use lower-cost, lower-alloy materials for the core without compromising performance.
Quenching and Tempering for Strength and Toughness
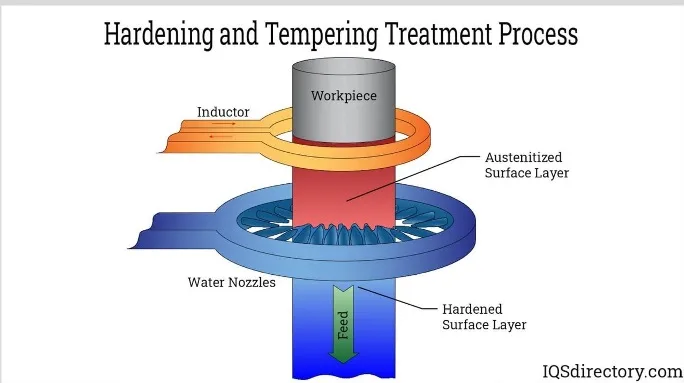
Image Source: IQS Directory
Quenching and tempering stands out as one of the most versatile metal heat treatment techniques. It creates the perfect balance between strength and toughness in construction materials. This two-stage process turns ordinary steel into high-performance components through careful temperature control and cooling methods.
Steel needs heating to temperatures between 815°C and 900°C when the quenching process begins. The heating phase must keep stable temperatures because any variations could lead to metal distortion.
The tempering phase is vital to get the best material properties. It usually happens at temperatures between 400°F and 1,105°F. This careful reheating reduces brittleness while keeping important hardness characteristics. Temperatures might reach up to 1,300°F when additional ductility is needed.
The combined process gives several benefits to construction applications:
- Better wear resistance and abrasion protection
- Improved weldability and ductility
- Superior toughness without losing too much hardness
- Better resistance to mechanical stresses
Quenched and tempered steel shows exceptional versatility in modern construction. It works especially well when components face extreme demands, such as:
- Mining and quarrying equipment
- Heavy construction machinery
- Earthmoving components
- High-stress structural elements
Recent advances in heat treatment steel processing have shown something remarkable. Short-time, rapid tempering can improve impact toughness by over 43% at a strength level of 1.7 GPa. This breakthrough gives construction professionals materials with unprecedented combinations of strength and toughness.
Carburizing for Enhanced Surface Hardness
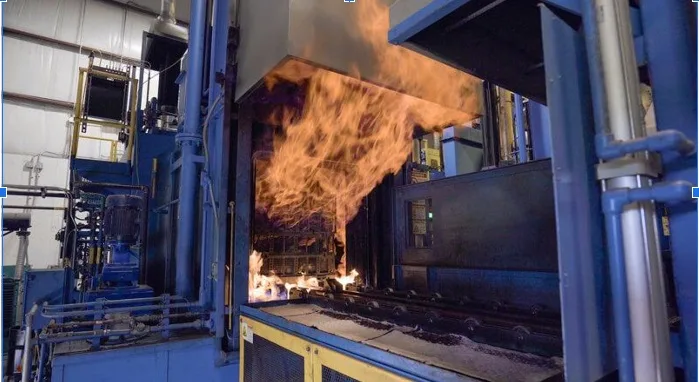
Image Source: Peters’ Heat Treating, Inc.
Carbon surface boosting through carburizing has become the life-blood of metal heat treatment. This advanced process gives unprecedented control over material properties. The technique diffuses carbon into steel’s surface layer at temperatures between 850°C and 950°C and creates a wear-resistant exterior while keeping a tough core.
The process delivers impressive improvements in material properties and achieves surface hardness levels between 62-64 HRC. Engineers can precisely control case depths from 0.010″ to 0.200″ based on specific application needs.
Construction components gain several key benefits:
- Increased mechanical strength and toughness
- Superior wear and corrosion resistance
- Improved fatigue strength
- Better ductility with stress relief
Careful control of carbon diffusion changes low-carbon steels into high-performance materials. Carbon content in the surface layer can reach up to 1.2% during treatment, which creates a reliable exterior that withstands severe operational conditions.
Modern metal heat treatment facilities use advanced monitoring systems to maintain exact temperature control. The metal heats up to austenization temperature first, then undergoes carbon diffusion and controlled cooling.
Gas carburizing has emerged as the preferred method in construction applications because of its precise control and economical benefits. The technique uses carefully regulated atmospheres with gasses like methane or carbon monoxide to develop consistent case depth across large components.
Base material composition plays a crucial role in carburizing’s success with construction materials. Low-carbon and alloy steels with original carbon content between 0.05% to 0.30% show excellent response to the treatment. This makes it perfect to boost properties of commonly used construction steels.
Stress Relieving for Reducing Residual Stresses
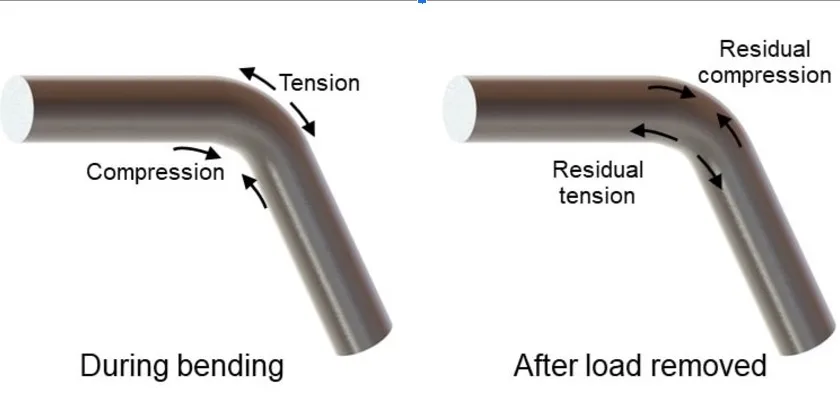
Image Source: imetllc.com
Residual stresses in construction materials create big challenges. Stress relieving has become a vital metal heat treatment process. This technique tackles internal stresses that build up during manufacturing, welding, and forming operations.
Professional metal heat treatment services use both thermal and mechanical methods to relieve stress. Thermal treatments have become popular because they redistribute residual stresses without creating new ones. The process heats components to temperatures below their critical range and keeps them there for a set time. A controlled cooling procedure follows.
Construction applications benefit in several ways:
- No dimensional changes during manufacturing
- Lower component failure risks
- Boosted upstream process efficiency
- Better structural stability
Precise temperature control determines how well stress relieving works. Steel components that need tight tolerances usually heat up to 2,050°F. This careful heating redistributes stress perfectly while protecting material properties. The cooling phase matters just as much – slower rates work better to avoid new stresses.
Oil- and gas-related structures just need stress relieving to maintain weld integrity. The process follows strict temperature schedules and soaking times, usually one to two hours. This precision prevents microstructural changes that might cause failures.
Metal heat treatment services often combine stress relieving with other treatments. Temperatures should go above 600°C before processes like nitrocarburizing. This combination relieves stress and prepares surfaces for later treatments, which helps components perform better in tough construction environments.
The process works great at addressing residual stresses from various manufacturing operations:
- Forming and straightening
- Rolling operations
- Rough machining
- Welding procedures
- Flame cutting
Conclusion
Today’s construction projects demand materials that can handle extreme conditions, carry massive loads, and last for generations. Raw metals by themselves usually can’t meet these requirements. Heat treatment turns regular construction materials into exceptional building components.
As construction demands continue to evolve, these innovative heat treatment techniques will remain essential tools for creating stronger, more resilient structures that stand the test of time.