3D printing (sometimes referred to as Additive Manufacturing (AM)) is the computer-controlled sequential layering of materials to create three-dimensional shapes. It is particularly useful for prototyping and for the manufacture of geometrically complex components. It was first developed in the 1980s, but at that time it was a difficult and expensive operation and so had few applications.
It is only since 2000 that it has become relatively straightforward and affordable and so has become viable for a wide range of uses including product design, component and tool manufacture, consumer electronics, plastics, metalworking, aerospace engineering, dental and medical applications, and footwear. The sales of AM machines, or ‘3D printers’ has grown rapidly and since 2005, the home use of 3D printers has become practical. 3D printing systems developed for the construction industry are referred to as ‘construction 3D printers’. A 3D digital model of the item is created, either by computer-aided design (CAD) or using a 3D scanner. The printer then reads the design and lays down successive layers of printing medium (this can be a liquid, powder, or sheet material) which are joined or fused to create the item. The process can be slow, but it enables almost any shape to be created.
Depending on the technique adopted, printing can produce multiple components simultaneously, can use multiple materials and can use multiple colours. Accuracy can be increased by a high-resolution subtractive process that removes material from an oversized printed item. Some techniques include the use of dissolvable materials that support overhanging features during fabrication. Materials such as metal can be expensive to print, and in this case it may be more cost-effective to print a mould, and then to use that to create the item.
Scope of 3d in the construction industry
In the construction industry, 3D printing can be used to create construction components or to ‘print’ entire buildings. Construction is well-suited to 3D printing as much of the information necessary to create an item will exist as a result of the design process, and the industry is already experienced in computer aided manufacturing. The recent emergence of building information modelling (BIM) in particular may facilitate greater use of 3D printing. Construction 3D printing may allow, faster and more accurate construction of complex or bespoke items as well as lowering labour costs and producing less waste. It might also enable construction to be undertaken in harsh or dangerous environments not suitable for a human workforce such as in space.
3d printing itself is not a new technology, harking back to the 1980s. Fabricating a three-dimensional model, or prototype, from a computer-aided design by adding successive layers of material is now standard practice in many industries, ranging from aerospace and architecture to medicine and high-end manufacturing.
McKinsey, the consultancy, estimates the technique could have an annual economic impact worth $550 billion by 2025. Construction, however, is proving a tougher challenge. It is thought that 20 commercial buildings around the world have been built using 3D printing so far, the first being by COBOD International, in the Danish capital Copenhagen, in 2017.
In practice, concrete is squeezed out of a nozzle attached to a computer-programmed robotic arm, either stationary or travelling along rails, in successive strips, layer upon layer, to produce the desired building structure, such as an exterior or interior wall, or component, like an archway or void. Advocates claim the technique offers construction that is faster, cheaper and more environmentally friendly than traditional building methods. They point to accelerated delivery of homes, greater flexibility in design, reduced cost of construction, more efficient use of materials and higher levels of sustainability by reducing waste typical of construction, and even less noise pollution.
Specifically, industry experts identify seamless production of objects from a numerical design and access to a wide range of geometries for the final object, most impossible or very expensive to realise with traditional processing techniques. The commercial appeal to big builders seems irresistible. According to SmarTech Publishing, a market forecaster, by 2027 the 3D-printed construction industry will be worth $40 billion.
Concrete 3D printing in the construction industry helps save time, effort and material compared to traditional construction methods. It’s important to note, though, that 3D printers are not yet capable of creating a fully functional house.
Only the frame and walls of the house are built; other elements, such as windows, electricity, or plumbing, need to be installed separately. But concrete 3D printers can also be used to print bridges, benches, or simply outdoor decorations.
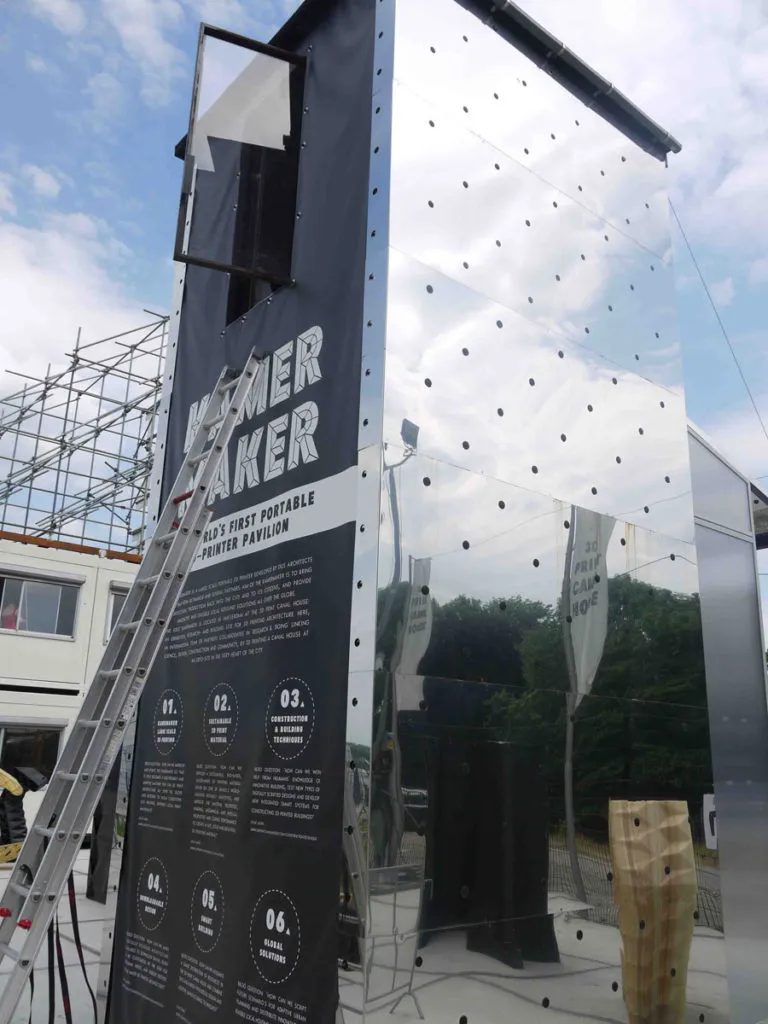
Technology of 3d printing
House 3D printers use extrusion technology. Some construction 3D printers look like super-sized desktop FFF/FDM 3D printers (gantry style), whereas others consist of a rotating mechanical arm.
In both cases, paste-type components such as concrete are used as filament. The material is pushed out of a special nozzle to form layers. To put it (very) simply, paste extrusion is similar using a piping bag to spread frosting on a cake.
The printer creates the foundations and walls of the house or building, layer by layer. The ground is literally the printer’s build plate. Some concrete 3D printers, however, are used to 3D print brick molds. When molded, the bricks are then piled atop each other manually (or with a robotic arm).
Advantages of 3d printing
1. Reduced Injury
One of the biggest benefits that 3D printers have presented to construction workers is a reduction in injuries in the field. Considering that building with concrete is difficult-even dangerous-this is a welcome improvement. Not only do workers have an easier time doing their job, but employers have less worker’s compensation paperwork to wade through due to injuries on the job.
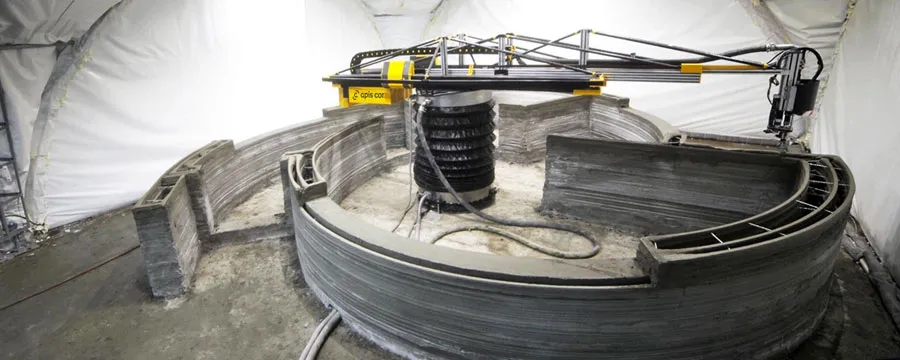
2. Reduced Material CostsConcrete Pour – Pile of Concrete Waste
Another improvement is a considerable reduction of material waste. 3D printers use the exact amount of concrete needed for the wall, floor, or whatever it is that you want to build. Builders and GCs don’t have to order in bulk because they’ll know exactly how much material they need. Not only is this a more sustainable, environmentally friendly way to build, but it also results in reduced costs for the contractor.
3. Quicker Construction
This is where concrete 3D printers truly set themselves apart from traditional construction methods. Where a project may sometimes take weeks–or months-to complete, 3D printers can often finish a project in a matter of hours or days. An entire house was once constructed in 24 hours! This allows contractors to move onto other projects sooner…and with more orders filled, more money is brought in for the contractor.
4. New Markets
Using a 3D printer also allows construction companies to work in markets that might have otherwise been inaccessible to them before. And for new construction companies, having a 3D printer on hand could set them apart from companies that have been around for a few decades and are resistant to change.
Similarly, traditional and established construction companies could utilize 3D printers to make sure they remain relevant in the market. Essentially, 3D printers can be used as a means to enter a new market but also to give an already established company a competitive edge.
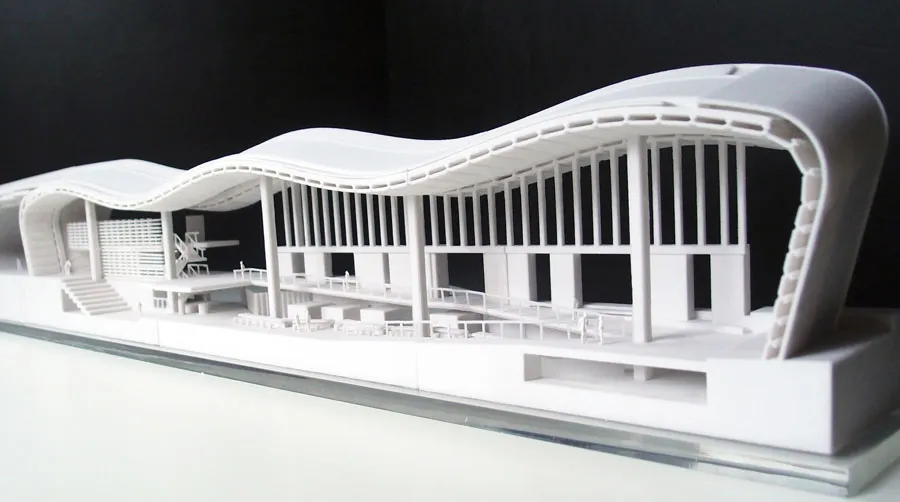
5. Cheaper Construction
Overall, the use of 3D printers costs less than traditional construction techniques and processes. With the reduction of injuries, time, and material cost, companies will see a dramatic increase in their profits. And while some workers will probably have to be let go, others will remain, since someone still needs to be able to put all of the pieces together. By learning the technology, workers have a chance to maintain their job security as well. They’ll earn more, as will the company as a whole.
6. Improved Form
3D printers are renowned for their ability to create seemingly odd and atypical design structures. Now construction companies can utilize that to offer their clients unique buildings designed entirely for them. This can open up their portfolio to certain individuals who may not want the standard rectangular options. Essentially, being able to create unique architectural designs for a client makes the construction company more desirable to certain clients.
7. Better Durability
While testing concrete during the early stages of construction will continue to be necessary, 3D printers have been found to contribute to the durability of the structural elements. This is due in part to how the materials are made and the manner in which they are assembled. More durable buildings mean fewer repairs need to be made, so construction companies can focus their efforts elsewhere to drive profit. For clients, too, their preferences certainly rest with a building that will last longer.
Benefits of house 3D printing
- Eco-friendly: 3D printed houses can be built with organic, eco-friendly materials. Moreover, some house 3D printers use solar energy and generate low CO2 emissions.
- Affordable: house 3D printers can build affordable housing, being of great aid for people in poverty-stricken regions or after natural disasters.
- Scalable: construction 3D printing reduces certain building costs. For example, the cost for 1 square meter of wall using traditional construction methods is approximately $75, whereas with the Apis Cor house 3D printer it is only $27.
- Efficient: since the materials are 3D printed on demand, the machines produce less waste. Also, construction 3D printers can finish a home’s foundations in less than a few days, while traditional construction methods take several weeks or even months.
- Design flexibility: with a 3D construction printer, it’s possible to easily create curved walls and unique facades. (Good thing it’s possible to 3D print furniture to match the curves!)
Effects of 3d printing for the construction industry
Often as automation and mechanization rise, prices drop. 3D printing is an affordable way to create housing for the impoverished in need of adequate shelter. Wealth Daily suggests that with the advent of 3D printing, “The use of lumber in the home’s framework would be spared.” This is a great advancement for green construction firms and a frightening development for the lumber industry.
An important part of every project plan is the design. With 3D printing, companies will be able to quickly and inexpensively create models to have a visual representation of the project as well as help pinpoint problem areas and avoid delays.
With 3D printing, construction professionals and their customers can communicate more clearly and efficiently. Even a customer with no architectural background can better express their needs and ensure that everyone is on the same page. Much of a client’s expectations come from an idea, and 3D printing makes it simple to materialize that idea beyond the dated method of pencil and paper.
Despite the incredible potential, many construction professionals remain wary of the affect 3D printing could have on their business. Increased automation and mechanization have been detrimental to fidgety labor markets in the past.
3D printing presents promising opportunities for the construction industry to become both greener and more cost-effective, often by considerable margins. As 3D printing research continues to develop, it will be exciting to see the benefits the technology will have on the many facets of the construction industry.
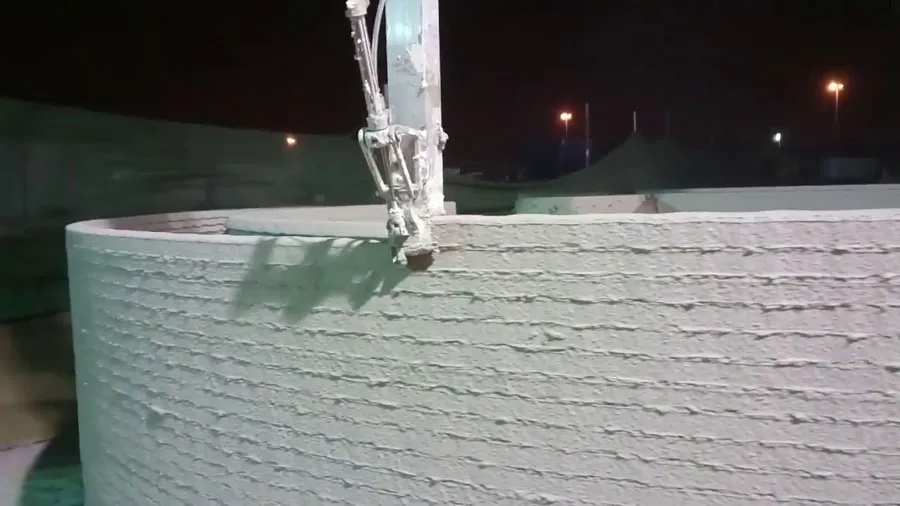
Innovation technologies in 3d printing
Robotic Arm Extruders
The Contour Crafting method involves the building material being deposited to create a large-scale 3D model with a smooth surface finish. Rails are installed around the building ground that will act as a structure to direct the robotic arm. It moves back and forth to extrude the concrete, layer-by-layer. Trowels placed on the side and above the nozzle to flatten the extruded layers and ensure the model’s strength.
In this process, conventional concrete cannot be used as it would need to harden before you could continue the process. If it was 3D printed it therefore wouldn’t be able to support its own weight. Therefore, concrete is used with quick setting properties.
Contour Crafting (company with the same name as the method) are very discreet about their progress. Chinese construction company WinSun Decoration Engineering Co describes it as able to “steal the show” however. These machines are huge (32m long, 10m wide and 6.6m tall). This enables them to 3D print full structures and assemble them on the spot. This is done through mixing concrete and glass fibres on-site and then printing. This feat made builders and construction workers aware of additive manufacturing.
Sand layers linked together
Italian architect Enrico Dini first made waves as the ‘ man who 3D prints houses.’ More recently, he demonstrated an interesting 3D printing process using his ‘D-Shape’ 3D printer. This machine relies on the binding of powder which makes it possible to solidify a layer of material with a binder. Layers of sand are deposited according to the desired thickness before a print head pours droplets (the binder) to harden the sand. This 4 x 4 metre machine can create large structures of up to 6 cubic metres in size.
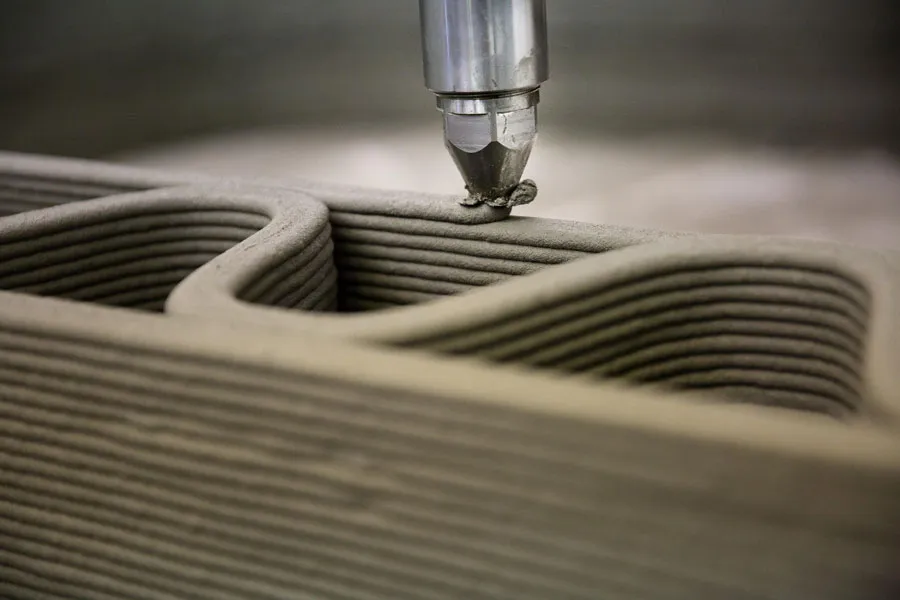
Metal for solid structures
Dutch company MX3D have developed a unique construction method called WAAM (Wire Arc Additive Manufacturing), which enables you to 3D print metal structures with a 6-axis robot that drops 2 kilos of material per hour.
This robot was the result of collaboration with Air Liquide and ArcelorMittal and is equipped with a welder and a nozzle to weld, layer-by-layer, metal rods. This process is also compatible with other metal alloys such as stainless steel, bronze, aluminium and Inconel. The machine can be likened to a sort of giant soldering iron. The team commented that “we combined an industrial robot with a welding machine to turn it into a 3D printer that works with our own software.”
Innovative projects of 3d printing system
Pittsburgh’s Neighborhood 91 Developing Connected 3D Printing Ecosystem
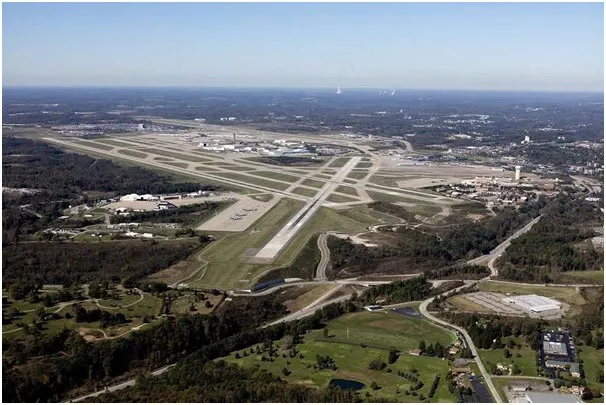
The neighborhood will feature all sorts of production technologies and the latest amenities for tenants of the area. These include a wide range of materials, tools, post-processing devices, testing and analysis capabilities along with storage. It also provides direct access to the airport, making supply lines far cheaper for all the companies involved.
Neighborhood 91 is looking to be a massive undertaking that would not be possible without the aid of the University of Pittsburgh and argon gas supplier Arencibia. The latter is poised to be the anchor tenant for the whole project down at Pittsburgh International Airport. It is going to be the first development of the 195-acre Pittsburgh Airport Innovation Campus and will be adjacent to the terminal and runway.
The Neighborhood campus concept will contain all the elements of the additive manufacturing supply chain in one concentrated place, including an onsite communal supply of powder. By sharing the costs on these materials and services, companies can save a lot. Officials also estimate that manufacturing lead times may shrink by 80 percent. Tenants will also save their clients and themselves a lot of time and money due to on-demand printing.
Another advantage is that thanks to companies like Arencibia, a lot of the crucial gases needed for AM will be easy to procure. This includes argon, helium, and other noble gases, which are essential elements for metal printing.
Dubai Unveils World’s Largest On-Site 3D Printed Building
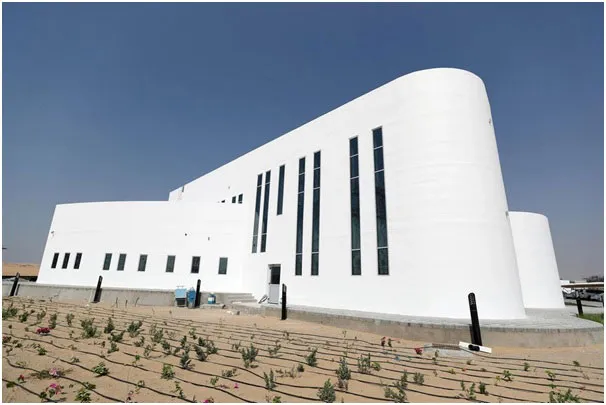
Dubai has just unveiled a major milestone in construction printing technologies. The region’s new building in Warsan now holds the Guinness record for largest on-site 3D printed construction. The two-storey building also meets all the stringent building standards and has undergone a year of testing.
The project was in development with the help of Apis Cor and the University of Nantes, who also researched the technology and special materials. The building was 3D printed from mineral-infused fluids that solidify into concrete, forming the structure on-site without any extra assembly works. Standing at 9.5 metres tall with a total area of 640 square metres, the construction process used only local components.
Officials said construction costs for a building this size would be cut from about Dh2.5 million to less than Dh1m. The process used about half the usual number of construction workers, needing only 15, and generated about 60% less waste. There were also some major time savings in using the 3D printer. The walls took just two days to build, while the rest of the house took a further four months.
3D Printed Prefab Home With Off-the-grid Capabilities
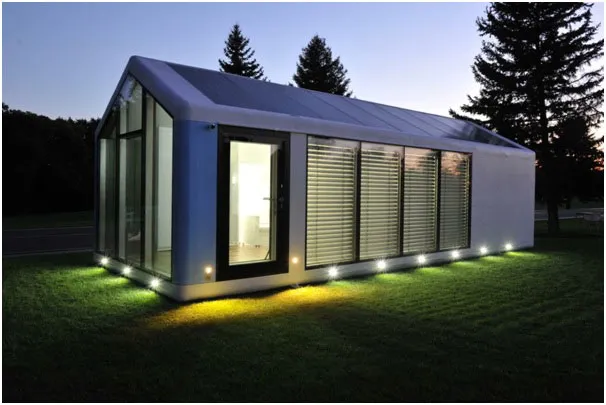
Reno, Nevada-based tech startup Haus.me is looking to change the face of sustainable housing with their new construction project. The houses they offer combine autonomous and off-the-grid capabilities with a build time of mere weeks. They also add in the ability for the house to act autonomously in catering to the customer’s wants with a Smart HomeOS system.
Combining 3D printing, connected smart home technology and “SpaceX worthy” construction principles, Haus.me offers 3 different home models. All of these homes are different in size, including the mOne off-the-grid studio house with a kitchen and bathroom. The other models, mTwo and mFour are less sustainable but still have some options like solar energy and AI-controls.
Haus.me’s homes are offering a bold business model, claiming that they can complete construction of the whole house in just weeks and deliver it the next day. The payments for the basic mOne amount to $1,163 per month for the 400 ft home. The company can also fit the basic version with all the off-the-grid options in case the customer would want them.
GENESIS Eco Screen: Biodiversity Habitat
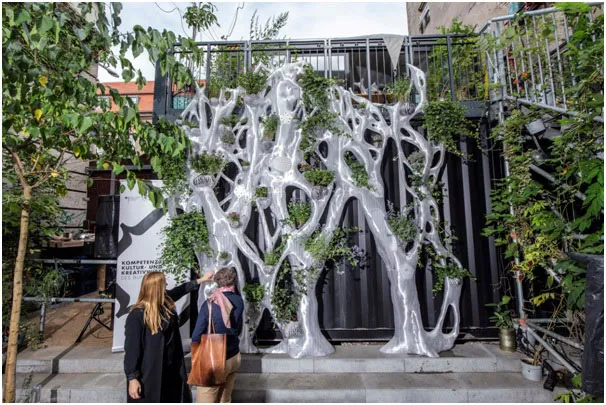
BigRep’s innovation lab NOWLAB unveiled a new sustainable structure that displays the possibilities of biodiversity in urban settings. The GENESIS Eco Screen consists of filament derived from 100% recycled PET and incorporates plants, insect habitats and embedded channels for water flow and drainage altogether. It utilizes complex designs, merging natural habitats with 3D printed architecture.
The GENESIS Eco Screen was the brainchild of Lindsay Lawson, an Applications Specialist at NOWLAB. The team behind the structure wanted to demonstrate the environmental opportunities presented by additive manufacturing technology using circular economy solutions fusing recycled components and natural materials. It represents a model for minimizing waste emissions and energy usage, while building on natural harmony with plants and insects.
Singapore HDB Uses a Concrete 3D Printer for Construction & Landscape Furniture
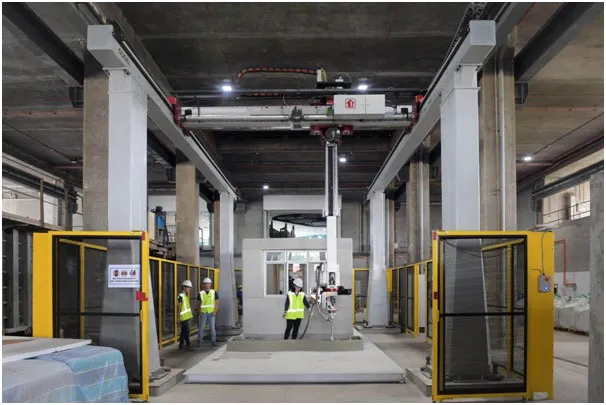
Singapore’s Housing Development Board (HDB) has greenlit the use of concrete 3D printing in the development of architectural components and various items like benches and pavilions. The board is considering such methods for eventual use in their Tengah and Bidadari estates. The project also employs the use of the largest 3D-printer in South-east Asia, costing $900,000 for purchase and installation.
Extensive testing in 3D concrete printing is underway at Singapore’s HDB Centre of Building Research at Woodlands. The agency has installed a concrete AM machine capable of creating components up to 9m long by 3.5m wide by 3.8m tall. Previously, they successfully printed a room measuring 3.6m by 3m by 2.75m in 13 hours back in August.
By employing the technology, they were able to build a room in about 6 days. This included, not just the printing, but also the manual insertion of steel reinforcement bars into the structure and fitting in windows and a door. In contrast, their previous workflow took more than two months to build a similar room using precast production. Fabricating the precast mold alone can require two months, and even more if design time is included. On top of this, molds would deteriorate over time and extensive use. With 3D printing, there is no mold to worry about.
S-Squared Inc. Prints 500-Square ft. House Within 12 Hours
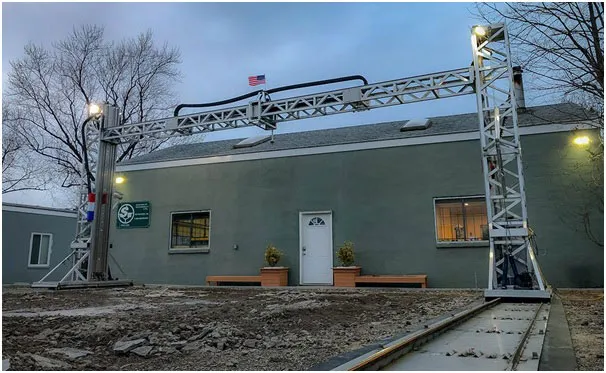
With the recent advancements in construction printing, we’re seeing major speed improvements, especially for residential construction technologies. From WASP building a house in roughly 10 days to Be-More-3D creating the basic structure of a home within a day. Now, New York-based S-Squared is touting the ability to build a 500 square-ft house in under 12 hours. Not only does this display remarkable build-speed, the project has also built the largest 3D printed house yet.
The company originally introduced their Autonomous Robotic Construction System (ARCS) in December 2018. They say it’s capable of reducing costs by as much as 70% compared to traditional construction methods and have demonstrated that it can complete homes in mere hours. Moreover, the company is also pushing it s an eco-friendly solution to the housing crisis.
S-Squared 4D Commercial is a subdivision of S-Squared 3D Printers Inc. that successfully developed a state-of-the-art eco-friendly concrete printer. The technology can build homes at the exact specifications that users input and produce all kinds of houses. Despite displaying a feat of residential construction, the company also has wider ambitions, setting their sites on “roads and bridges, and everything in between“.
Conclusion
New companies are developing 3D printers, coming up with innovative solutions to change the construction industry. There are already families moving into 3D printed houses, and soon we will be able to deliver homes to rural parts of our planet. This is a truly revolutionary time for the construction industry and such huge development wouldn’t be possible without Additive Manufacturing technologies.
Info and image – Raconteur.net, aniwaa.com, giatecscientific.com, thebalancesmb.com, 3dnatives.com, 3dprinting.com, Uk construction online